sbm mobile crushing process of copper.md
Find and fix vulnerabilities Codespaces. Instant dev environments
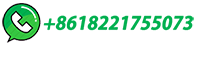
Rotary Crushers
A rotary Crusher is a term often used for Roll Crusher are compression type crushers, and were once widely used in mining. They have, within the last 10 or so years, fallen into dis-favor …
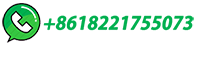
How to Process Copper Ore: Beneficiation Methods and Equipment
Before the beneficiation of copper ores, crushing and grinding are required. The bulk ores are crushed to about 12cm by a jaw crusher or a cone crusher. Then the crushed materials are sent to the grinding equipment, and the final particle size of the copper ore is reduced to 0.15-0.2mm.
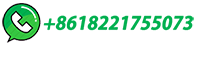
The efficiency of copper ore comminution: A
The theoretical minimum work needed to crush the rock is first calculated by comparing the difference in surface energy between the incoming ore and the outgoing …
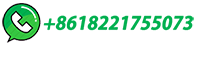
Copper Mineral Properties, Uses and Occurrence
Optical Properties. Copper has some interesting optical properties that have made it useful in a variety of applications. Here are a few of its optical properties: Color: Copper has a distinctive reddish-orange color when in its pure state, but it can also appear brown or gray depending on its surface finish and the presence of other elements or compounds.
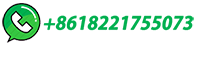
Superior™ MKIII Series primary gyratory crushers
Get the maximum potential out of your size reduction process to achieve improved crushing performance and lower cost per ton. By using our unique simulation software, our Chamber Optimization experts can design an optimized crushing chamber that matches the exact conditions under which you operate. Learn more about our Chamber Optimization Program
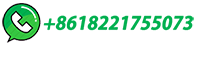
Extraction Of Copper | Mining, Concentration, Smelting
Copper Smelting means that the concentrated ore is heated strongly with silicon dioxide (silica), calcium carbonate (CaCO 3) and air in a furnace. The major steps in the extraction of copper are. Copper in Chalcopyrite is reduced to copper sulphide. Just like in Blast Furnaces, calcium carbonate is added as a flux to create the slag.
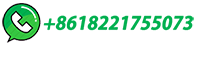
Environmental, economic and technological factors affecting …
1. Introduction. There is continual projected growth in the global copper industry, wherein the U.S. Geological Survey (USGS) indicated that around 20.0 million tonnes of copper were produced worldwide in 2020 [1], which agreed with the projections made by Cochilco [2].Of this, 80% comes from the pyrometallurgical processing of copper sulphide ores which are …
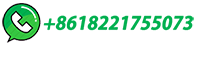
Gyratory Crusher (Gyratory Crushers Explained)
Typically, the initial crushing stage is completed using either gyratory crushers or jaw crushers. It is often the case that there will be only one crusher installed, and this will be referred to as the 'Primary Crusher'. Cone crushers are typically used for 2 nd, 3 rd & 4 th stage crushing steps (although not always).
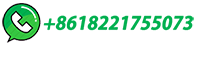
Copper Mining and Processing: Processing Copper Ores
Copper processing is a complicated process that begins with mining of the ore (less than 1% copper) and ends with sheets of 99.99% pure copper called cathodes, which will ultimately be made into products for everyday use.The most common types of ore, copper oxide and copper sulfide, undergo two different processes, hydrometallurgy and pyrometallurgy, respectively, …
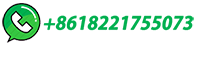
Health Effects of Excess Copper
This chapter focuses on the health effects associated with acute and chronic exposure to excess copper. Information on those effects comes from human case-reports and population-based studies. The emphasis is placed on acute exposure effects on the gastrointestinal (GI) system. Effects on other target organs, such as the liver, in subjects following high-dose chronic …
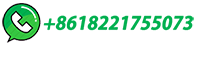
Optical rotatory dispersion spectra of bis- and mono(.alpha
DOI: 10.1021/JA00990A057 Corpus ID: 101181410; Optical rotatory dispersion spectra of bis- and mono(.alpha.-substituted glycinato)copper(II) complexes @article{Wellman1967OpticalRD, title={Optical rotatory dispersion spectra of bis- and mono(.alpha.-substituted glycinato)copper(II) complexes}, author={Keith M. Wellman and Thomas G. Mecca and William S. Mungall and …
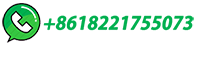
Copper Ore Processing Methods
Since metallic copper is malleable, it cannot be broken and pulverized as can the more friable minerals, and after first picking out the larger lumps or nuggets of copper by hand, crushing is done by steam stamps; pebble mills instead of ball mills are employed for grinding because of the abrasive qualities of the gangue.
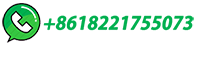
(PDF) Copper heap leaching: Process, principles …
Most copper minerals are amenable to leaching under atmospheric conditions. A critical exception is chalcopyrite (CuFeS2), which does not dissolve under percolation leach conditions. Several ...
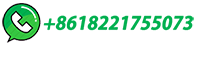
Copper Production in Zambia in Five Easy Steps. How it is …
The large pieces of ore are collected by haul trucks and taken to a mill, a large rotating device which makes the pieces smaller through crushing and grinding. There are two types of copper ore (sulphide ore and oxide ore), and each is treated differently in order to liberate the copper inside. Step 3. Sulphide ore – treatment process
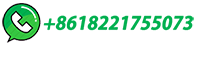
From Ore to Finished Product
Copper - From Beginning to End. Copper is a major metal and an essential element used by man. It is found in ore deposits around the world. It is also the oldest metal known to man and was first discovered and used about 10,000 years ago. And as alloyed in bronze (copper-tin alloy) about 3000 BC, was the first engineering material known to man.
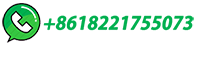
Understanding the mechanism of microcrack-enhanced …
2.2. Crushing. A primary jaw crusher (PE-150 × 250A) was firstly employed to comminute the Zijinshan copper ore. The comminuted copper ore passed through a 20 mm …
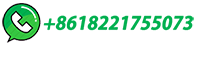
Copper Production: How Is Copper Made?
Sulfide Copper Ores . Virtually all sulfide-type copper ores, including chalcocite (Cu 2 S), chalcopyrite (CuFeS 2) and covellite (CuS), are treated by smelting.After crushing the ore to a fine powder, it is concentrated by froth flotation, which requires mixing the powdered ore with reagents that combine with the copper to make it hydrophobic.
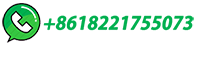
Modern Methods of Pre-Treatment of Plant Material for the …
2.1. Convection Drying. The most common method for plant material preparation is convection drying. Convection drying is one in which a stream of drying agent (dry gas, most often air) flows around the plant material bringing heat and removing moisture (Figure 1).The drying process is a process of simultaneous heat and mass exchange as well as an ongoing phase …
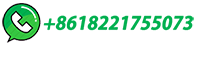
milling champer of rotatory ball mill | Mining & Quarry Plant
XBM's Ball mills that incloud roller mill,ball end mill,ball mill,ball milling,grinding mill,sag mill,hammer mill have … Jaw crusher Ball mills Rotary kiln Brick …
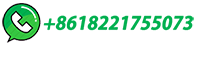
(PDF) Environmental, Economic and Technological Factors Affecting
Chile is the world's leading copper producer (28.3%) and maintains approximately 23.0% of current global reserves. Chile is faced with a significant risk posed by its collection of the most ...
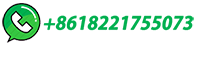
Rotary Scrubber
The trommel scrubbers are mainly applied for washing gold, diamond, and other ore (including manganese, copper, tantalum-niobium-tin, iron ore, silica sand, fluorite, etc.). It is often called gold wash trommel or diamond wash trommel. Main parts: Our JXSC's rotary scrubbers have two main parts: the drum scrubber and the screen. The drum ...
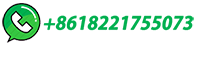
sbm/sbm crushing rolls rotatory coal breakers.md at master …
sbm crushing rolls rotatory coal breakersCrushers thyssenkrupp Industries India Roll Crushers; Hammer Crushers; Impact Crushers; Ring Granulators; Rotary Breakers; Jaw Crushers; Hammer Mills; Gyratory Crushers; Cone Crushers. Glossary of Mining Terms RocksandMinerals Auger — A rotary drill that uses a screw device to penetrate,break,and then ...
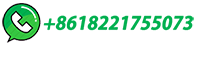
Complete Lecture about Crushers in Cement …
Crushing is comminution in the coarse range, whereas grinding refers to comminution in the fine range. The technique of size reduction was developed chiefly by empirical analysis. ... In this case instead of lime stone, copper ore …
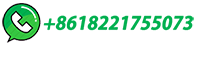
60 Centuries of Copper
This section is based on Sixty Centuries of Copper by B Webster Smith which was published by the UK Copper Development Association in 1965. Sixty Centuries of Copper is intended for the reader who is interested in the general history of copper mining, the development of metal-working processes and the uses of copper through the past six thousand years.
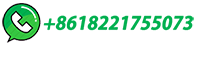
How to Process Copper Ore: Beneficiation …
Before the beneficiation of copper ores, crushing and grinding are required. The bulk ores are crushed to about 12cm by a jaw crusher or a cone crusher. Then the crushed materials are sent to the grinding equipment, and …
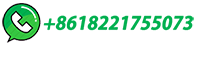
Copper (Cu) Ore | Minerals, Occurrence » Geology Science
Copper (Cu) ore is a naturally occurring mineral deposit that contains copper in varying concentrations. It is an important industrial metal that has been used by human civilizations for thousands of years due to its excellent electrical and thermal conductivity, high ductility, and resistance to corrosion. Copper is widely used in various applications, including …
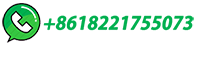
Copper Introduction And Ore Crushing
The processing and production technology of copper ore mainly includes three processes: crushing, grinding, and beneficiation.The modern copper ore crushing method adopts three-stage closed-circuit crushing, …
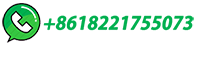
Kinetic Investigation on Leaching of Copper from a Low …
In this study, the reject fraction of the jaw crusher, located in the first part of the crushing circuit, is used as a considerable stock in copper tank-leaching plant. High market …
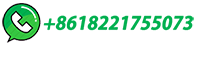
Copper Ore Processing Plants, Flow And Equipment
2. Grinding process. The copper ore processed into granules is screened by a vibrating sieve and sent to a ball mill for grinding and crushing. Here also need to use an auxiliary equipment – classifier. It can classify and …
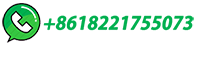