Advancing Iron Ore Beneficiation: Exploring Cutting-Edge
The evolution of iron ore beneficiation process technology underscores the industry's commitment to innovation and sustainability, driving continuous improvement in ore processing efficiency and ...
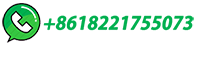
US20210025028A1
the prior art related to the beneficiation of uranium ores has either involved the use of methods such as flotation, magnetic separation, radiometric sorting or the rejection of coarse size fractions in order to produce a higher uranium grade feed stock for leaching. None of the prior art has described a process to produce a higher uranium grade feed stock for leaching which …
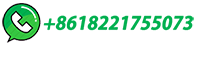
Uranium, vanadium pilot plant takes shape for Toro
On the back of a strong scoping study last year, Perth-based company Toro Energy has commissioned a pilot processing plant design and added vanadium to its Wiluna uranium project in Western Australia's …
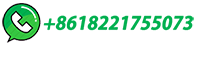
PILOT PLANT FOR WILUNA URANIUM PROJECT …
Design phase for the pilot plant commissioned by Toro continues on-track. Pilot plant will test the improved beneficiation and hydrometallurgical circuit developed by Toro over recent years from bench scale research at a closer to production scale and as single streams. Pilot plant willtest potential ore from the three uranium -vanadium ...
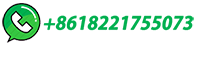
Tumas open pit Uranium Project, Namibia, South Africa
Tumas Uranium Ore Processing . The Tumas processing plant is designed to treat 4.15 Mt/y of carbonate ore containing carnotite (K 2 (UO 2) 2 (VO 4) 2.3H 2 O) as the uranium-bearing mineral from an open pit mine to produce 3.6 Mlb/y uranium yellow cake (U 3 O 8) product and 1.18 Mlb/y vanadium (VOSO 4) by-product over a 30-year mine life.
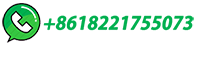
Process development to recover rare earth metals from monazite …
The details of RE sources, their processing and applications have been made by different authors and are evident from the papers ... The material is then transported as slurry through a pipeline to the beneficiation plant. ... Based on these results, uranium was purified from the leach solutions by extraction with Aliquat-336 diluted in ...
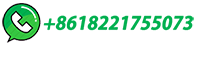
Iron ore beneficiation | Commodities | Mineral …
Extending beyond traditional spiral plants our designs for fine iron ore beneficiation incorporate gravity and magnetic beneficiation equipment with capacities ranging from 5 to 7,000 tonnes per hour. Plants include integrated …
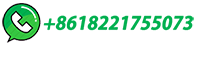
Recycling of Chrome-Containing Waste from a Mining and Processing Plant …
DOMBP's tailings mineral resources, which have been accumulated since 1938, amount to 2.2 million tons as of 1 January 2018. In total, there are 2.2 million tons at 27.65% Cr 2 O 3, which is 0.6 million tons in terms of chromium oxide [].The technological scheme of chrome ore processing at DOMBP includes standard operations of gravity concentration: crushing …
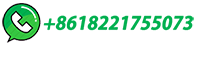
ALTA MetBytes
A physical beneficiation process developed by Marenica Energy, Australia (patent pending), for upgrading low ... Paladin believe that the technology represents a new paradigm for uranium processing plants. For example, the nano-filtration step could be moved upstream of IX as in the case of Langer, where potentially it would be a ...
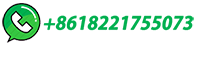
Beneficiation process for enhancing uranium mineral processing
The invention relates to a beneficiation process for uranium ores comprising clay and carbonate minerals, the process comprising: performing a hydrocyclone step to obtain a hydrocyclone underflow fraction substantially comprising the uranium component; treating the hydrocyclone underflow fraction to effect a separation of carbonate and uranium minerals; and recovering …
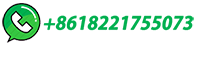
4 Uranium Mining, Processing, and Reclamation | Uranium …
Ore Pretreatment or Beneficiation. ... Once the pregnant solution is returned to the surface, the uranium is recovered in much the same way as in any other uranium processing plant. The ISR method requires that the ore deposit rock structure be permeable (commonly sandstone) and have an underlying impermeable confining layer (such as a clay ...
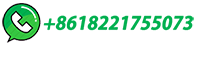
Uranium extraction: the key process J drivers
Column SX has found a ready application to uranium in view of the rapid extraction kinetics. With the renewed interest in uranium processing, efforts are being redirected towards further …
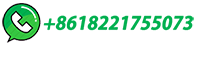
World leader in fine iron ore beneficiation
cost effective fine iron ore beneficiation for the highly variable low‑grade ore. Innovative plant design Extending beyond traditional spiral plants our designs for fine iron ore beneficiation incorporate gravity and magnetic beneficiation equipment with capacities ranging from 5 to 7,000 tonnes per hour. Plants include integrated feed ...
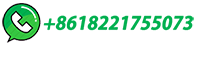
Life Cycle Assessment in mineral processing – a review of
3.1.1 Group 1 – mining and beneficiation as a single stage. Most of the studies considered beneficiation altogether with the mining operation. For example, Awuah-Offei and Adekpedjou carried out a review scrutinising the very first LCAs applied to the mining sector.This work is focused on the extraction stage, and it mentions the beneficiation stage only when it …
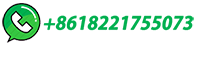
11.21 Phosphate Rock Processing
11.21 Phosphate Rock Processing 11.21.1 Process Description1-5 The separation of phosphate rock from impurities and nonphosphate materials for use in fertilizer manufacture consists of beneficiation, drying or calcining at some operations, and grinding. The Standard Industrial Classification (SIC) code for phosphate rock processing is 1475. The ...
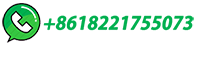
Life Cycle Assessment in mineral processing – a review of
3.1.1 Group 1 – mining and beneficiation as a single stage. Most of the studies considered beneficiation altogether with the mining operation. For example, Awuah-Offei and …
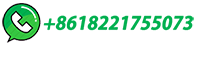
A review of the beneficiation of copper-cobalt-bearing …
Processing of the Kipushi Cu–Zn sulphide ore started in 1935. Initially, the plant treated about 20,000 tonnes of ore per month using a single flotation circuit with conventional reagents such as xanthates and pine oil. Over the period 1937 to 1940, the concentrator was extended to allow the differential flotation of Cu–Zn.
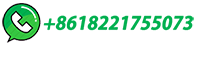
Radioactive beneficiation process for uranium ore
Radioactive beneficiation: Radioactive beneficiation is a coarse-grained ore beneficiation method, in which the raw ore is crushed and graded, and directly enters the radioactive beneficiation equipment for sorting. Some large tailings can be discarded in advance. Process features: low cost and simple equipment.
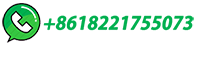
Mineral Beneficiation and Processing of Coal | SpringerLink
The modern-day coal processing plants can be categorized into four different circuits, depending upon the size of the coal particles to be treated: (a) coarse coal processing circuit treating particles coarser than 10 mm, (b) small coal circuit for washing particles in the size range of 1-10 mm, (c) fine coal circuit for cleaning particles in ...
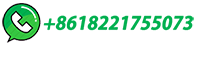
MANUAL FOR URANIUM ORE PROCESSING
FOR URANIUM ORE PROCESSING INTERNATIONAL ATOMIC ENERGY AGENCY VIENNA, 1990 ... Physical beneficiation 105 10.1.1. Gravity concentration 106. 10.1.2. Flotation 107 …
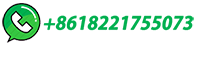
mobile plant for uranium ore processing in south africa 2
Nuclear fuel cycle' Extractin gg uranium from its ores. in South Africa. Until the early 1950s uranium ore came almost ... The interior of the ore-processing plant of l'Ecarpiere in the Vendee region of France.
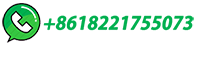
A review of cassiterite beneficiation fundamentals and plant practices
However, many plants consider flotation of tin using specific collectors because of the advantages like higher tin selectivity and recovery (Foo et al., 1983). 5. Gravity concentration. Gravity concentration is an age-old method used in the mineral processing plants for the separation of heavy and light mineral particles.
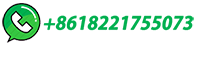
Technical Resource Document: Extraction and …
beneath and in the vicinity of inactive uranium processing sites by uranium tailings (60 Federal Register 2854, January 11, 1995). These regulations have been included in Appendix C of this document. The use of the terms "extraction," "beneficiation," and "mineral processing" in the Profile section of this document is not intended to classify ...
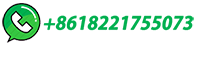
Coal beneficiation: theory and practice
Although the theoretical knowledge of coal beneficiation is available aplenty in coal preparation books; it is essential that mineral processing engineers also possess basic knowledge regarding selection of process equipment, key operational factors, problems encountered in plant operations, and their troubleshooting strategies.
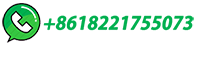
Dry beneficiation of iron ore
In the beneficiation plant, high-pressure grinding rolls (HPGR) with downstream dry screening and dry magnetic separation are used as tertiary crushers to obtain a concentrate with 67 % iron content. In 2013, CITIC Pacific Mining had put into operation a first line from a total of six for the production of a magnetite iron ore concentrate in ...
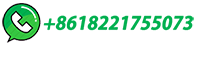
ALTA MetBytes
A physical beneficiation process developed by Marenica Energy, Australia (patent pending), for upgrading low ... Paladin believe that the technology represents a new paradigm for uranium …
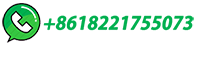
Phosphate Beneficiation
Depending upon which company designed the plant, some existing Florida plants will size the slurry leaving the cyclone underflow into various tight size fractions before further processing. This is done to enhance efficiency in the next operation, but some plants skip sizing and just send the cyclone underflow on to the next treatment.
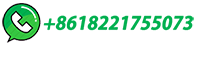
Existing and New Processes for Beneficiation of Indian …
Cliff's Tilden plant in Cleveland, USA, is the only iron ore beneficiation plant, where selective flocculation technique, using degraded starch as the flocculant, has been applied to produce pellet grade concentrate from a feed containing around 32% Fe . The plant has a capacity of processing 10 million tons and is in operation since 1975.
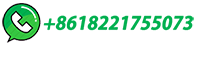
Review of processing and future demand of uranium ores
In this paper, processing of uranium ores is discussed, namely, beneficiation by radiometric sorting, gravity and magnetic separation methods, flotation and leaching.
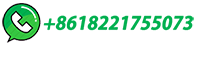
Iron ore beneficiation: an overview
The quality of Indian iron ore resources is generally good with high iron content and high percentage of lumpy ore. More than 85% of the hematite ore reserves are of medium- to high-grade (+62% Fe) and are directly used in blast furnace and in direct-reduced iron (DRI) plants in the form of sized lump ore, agglomerated sinter, and agglomerated pellets (Iron and …
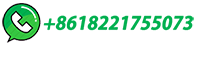