Ring formation in kilns | PPT
12. Porosity of the brick may help to reduce ring formation but at the cost of heat loss. It can be reduced but it cannot be avoided. Closed pores Porosity of the kiln brick Open pores Silica infiltrated surface or vitrified surface on brick can avoid infiltration of low melting,low Viscous components .This avoids destruction of refracories but spurrite rings cannot be …
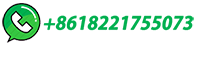
What are the reasons behind formation of Kiln build-ups
This phenomenon occurs especially in the burning zone inlet, where the liquid phase is just starting to form, at approximately 1250°C. Due to the rotation of the kiln, the material freezes with each kiln rotation and deposit of clinker particles having less than 1 mm diameter may reach a large thickness.
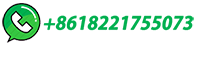
Kiln Tips for Beginners
Why is it important to always have a kiln wash coating on kiln shelves? The main purpose of putting kiln wash on a shelf is to keep any glaze drips from sticking to the shelf. So, if your glazes don't run and drip, you don't …
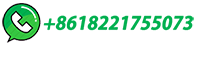
New Kiln Inlet Gas Analysis Technology
This paper outlines a new patented gas analysis design for the kiln inlet of a cement plant. The paper will explain why gas sampling is facing more process challenges, particularly from the increased use of alternative fuels in the industry. The paper will describe a how a new patented technology makes it possible to increase the cleaning power of a kiln …
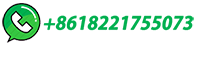
Reactions in the cement kiln
The decomposition products react with lime to form intermediate compounds which in turn form other compounds as clinkering proceeds. Water evaporation In wet-process kilns, and their derivatives, water must first be driven off. In a wet-process kiln, calcining takes place after the water has been driven off, about a third of the way down the kiln.
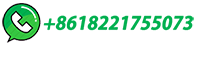
Clinker formation process in a modern plant rotary kiln.
The impact of coating layers on the clinker production process within a rotary kiln burning both coal and Refuse Derived Fuel (RDF) was investigated in one study [7], showing that a thin coating ...
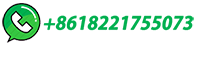
Snowman Formation and Prevention
Another phenomenon in the cooler is the formation of a "Snowman". A Snowman (SM) is a type of build up formed in the static inlet. In general a snowman is caused by [9]: fine and sticky clinker fall of coating from the kiln. A …
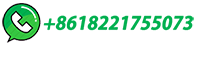
Why does the kiln's breaker keep tripping? | Hot Kilns
There is NEVER a problem with the kiln when the breaker just trips after being on for a while, and when you reset it the kiln can come back on. Does the breaker not let you reset it at all, even when the kiln is completely off?
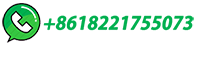
(PDF) REFRACTORIES SELECTION FOR CEMENT …
coating formed. Key Words . Cement Kiln, Kiln I n let, K iln Cooler, Tertiary Air . Duct. Coating, Build – up. Abrasion Resistant, ... The kiln inlet, smoke chamber an d lower riser .
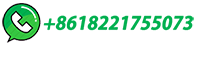
Coating formation in Kiln Inlet
Re: Coating formation in Kiln Inlet. Hi. Coating at kiln inlet ia mainly due to the volatiles like Chlorides, alkalies ( Na2O and K2O) and SO3. To minimise the coating formation, the alkali sulfate ratio should be around 1.1 so that these volatiles will come out as alkali sulfate along with the clinker so that the recirculation inside the kiln circuit will be less.
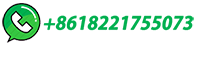
Chapter 4 Cement Manufacturing and Process Control
ciner is 10–25%, and the calcination at the kiln inlet is 50–70%. The advantage of this system is low coating tendency in kiln inlet and riser duct. The coating in burn-ing zone is stable, and it is less sensitive to chloride and sulfur. The kiln dimension is …
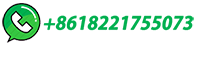
kiln inlet coating
kiln inlet coating. 1) whats are the reasons of kiln inlet coating. 2) why plysious kiln have differnt dia. 3)polysius kiln have no grith gear and having electromechanic roller …
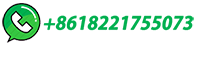
Microwave Kiln Basics and FAQs
The basic steps of fusing glass in a microwave kiln. 1. Prepare your glass separator: Put a fresh coat of kiln wash on the working platform and let it dry (or put it in the microwave for 1 minute uncovered for a quicker dry), or put a piece of fiber paper down.; 2. Prepare your turntable: Put three kiln bricks down in a tripod arrangement in the center of your …
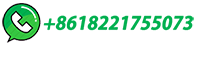
7 Most Common Problem in Pyro Processing For Kiln and Cooler …
This document discusses 7 common problems that can occur in pyroprocessing kilns and coolers: cyclone blockage, kiln inlet blockage, large clinker ball formation, kiln coating, feed rushes and dusty kilns, cooler snowman formation, and red rivers in clinker coolers. It then provides more details on the main reasons for each problem and potential solutions.
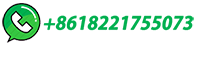
Rush in Kiln & heavy coating in KIln inlet
Re: Rush in Kiln & heavy coating in KIln inlet. Dear Wahid, As you are mentioning heavy coating at inet. This seems to be the main cause of kiln rush. You can take help from QC regarding slight increase in SR and same time increase AM to break the rings at inlet till problem finishes. You can adjust flame of main burner.
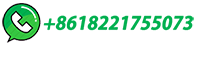
Preparation
Your first firing will create an oxide coating which will take over this function for the life of the element. In order for this coating to form the kiln must reach a temperature of at least 1900 F, which is beyond the upper temperature rating for many glass kilns. For ceramic kilns it is recommended that you do a 04 firing (1945 F) to attain ...
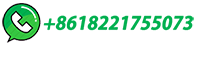
KilnLoq Cement kiln inlet gas
Kiln inlet gas analysis systems deliver essential data. Cement plants need reliable online analysis of the process gasses at the kiln inlet if they are to compete in a tough market. Use the data to optimise your safety, operating costs, production and emissions – and compete with the best in the cement industry. Without kiln inlet gas analysis,
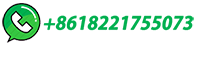
Impact of coating layers in rotary cement kilns: Numerical
Section snippets Determination of the coating profile in the kiln. To obtain a first estimate of the coating layer profile at the inner kiln wall, the coating thickness is initially …
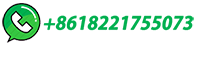
Kiln Inlet / Outlet | dalmachinery
Our graphite seals reduce false air intake and allow enough flexibility to follow the kiln's movements. Rows of graphite blocks held in place by a wire rope system. This, ensures an efficient seal against the outer air casing. The inlet and …
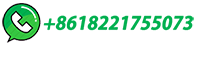
Reliable Kiln Inlet Gas Analysis: Part 1
Using this technique, the kiln inlet gas is kept above acid dewpoint in the sample system and is transferred into the analyser without any further gas conditioning or drying treatment. Benefits of the hot-wet measurement technique. Combustion gases at kiln inlet are mainly composed of O 2 (2 – 4%), CO 2 (12 – 15%), H 2 O (8 – 10%) and N 2.
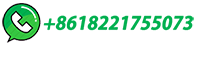
From a mineralogical analytical view to a mechanism …
From Table 1, it can be seen that there is a large variation of oxygen, especially in the kiln inlet. This irregularity determines the chemical reaction in the kiln inlet. The local variability of gases' flux, loaded with alkalis SO 2 and/or CO 2, is certainly responsible for the heterogeneity of the rings' composition. Hence, it is interesting ...
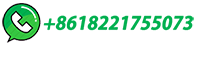
Refractories for the cement industry Kiln
With the exception of the inlet cone and the nose ring, the kiln should always be lined only with brick. Brick heights, which depend on kiln diameter, range from 200 mm and up. On the …
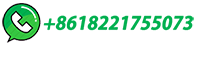
Why does Pottery Explode in The Kiln?
When the water evaporates in the kiln, it is called the 'water smoking stage'. Ideally, the preheat is long enough so that all of the free water has evaporated. I usually preheat my kiln for a couple of hours before the main firing schedule starts. During the preheat, the kiln gradually increases in temperature to just below 212F (100C).
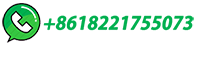
Kiln Coating | FCS Ltd
KC2000 is a Mullite-based refractory coating designed primarily to encapsulate RCF furnace and kiln linings. KC2000 does NOT contain ceramic fibre. When fired above 800°C, KC2000 forms a tough 'egg shell' type finish that: ... Form Clay Based paint; Wet Density: 2000kg/m³ ...
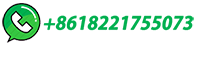
From a mineralogical analytical view to a mechanism …
Abstract. Ring growth in cement rotary kilns is a complex and a dynamic phenomenon, where the agents responsible for their formation cannot be easily controlled. …
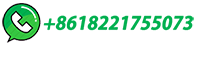
EVERYTHING YOU NEED TO KNOW ABOUT THE CHEMISTRY OF KILN …
Alkali chlorides tend to remain in the internal kiln cycle for a long time and can lead to heavy coating and ring formation in the upper part of the rotary kiln and the lower stages of the preheatcr. Chlorides, even in such small quantities as 0.02% in the kiln feed can become so troublesome on some preheater kilns that they are forced to ...
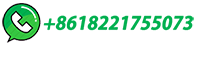
Different Types of Non-Stick Coatings | Explained 2023
It is considered to be a safe and durable non-stick coating option. However, it's not as heat-resistant as Teflon and can be more expensive than other types of non-stick coatings. Comparison of Non-Stick Coatings. Durability: Teflon and ceramic non-stick coatings are less durable than anodized aluminum or stainless steel. Heat Resistance:
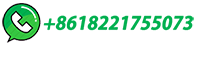
Why Brick Refractory Coating Is Ideal For A Brick Kiln
In many industries, using a kiln is an important part of getting things done. A kiln can be used to harden clay, ceramic, and other materials, so it might be something that your business uses on a daily basis. If you do use a kiln that is made out of brick, you should have it coated with a brick refractory coating if this has not been done yet.
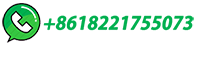
What are the reasons behind formation of Kiln build-ups
The bonding is created by the freezing of the clinker liquid phase. This phenomenon occurs especially in the burning zone inlet, where the liquid phase is just starting to form, at approximately 1250°C. Due to the rotation of the kiln, the material freezes with each kiln …
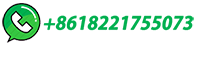