Jaw Crusher: What Is It & How Does It Work?
But many people don't know that jaw crushers come in all shapes and sizes, from small tabletop models to massive industrial machines. So what exactly is a jaw crusher, and how does it work? What Is A Jaw Crusher, And How Does It Work? A jaw crusher is a machine that breaks down large rocks into smaller pieces of rock, gravel, or dust.
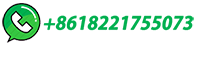
Efficient Jaw Crusher for Coal Analysis
Efficient coal processing with jaw crusher. Advanced technology for precise crushing and material preparation. Explore now!
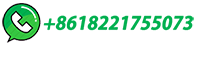
Understanding the Different Types of Crushers | Agg-Net
The discharge conveyor and hopper under the crusher should be wider than the discharge width of the crusher. Sufficient tension must be placed on the toggle plate to ensure proper alignment. Feeding for efficiency. Jaw crushers are routinely choke fed to maximize production capacity and ensure that particles are uniformly broken.
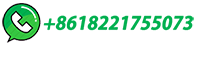
McLanahan | Best Practices for Feeding Jaw Crushers
1. In line feeding. Jaw Crushers should only be fed in line with some type of Feeder or scalping screen. This means the discharge end of the feeding machine should …
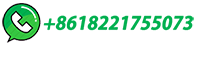
The Complete Guide to Primary Crushing, Secondary …
Learn everything you need to know about primary crushing, secondary crushing, and tertiary crushing in this comprehensive guide. Discover the types of crushers used in each stage, their working principles, and the advantages and disadvantages of each process. Get answers to frequently asked questions and improve your understanding of …
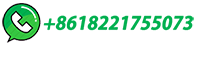
Cone Crusher Diagram: Simplified Guide
Understand cone crusher diagram basics with our comprehensive blog post. Learn about the structure and operation of cone crusher models.
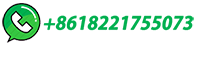
How Does a Jaw Crusher Work? A Simple Guide
A jaw crusher is a robust, essential and rugged crusher used primarily in mining and construction for the initial crushing of large rocks and ore. Positioned at the start of the crushing process, it uses compressive force between two jaw plates to break down large materials into smaller, manageable pieces.
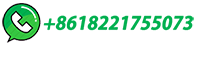
en/166/broken particle size of the crusher.md at main · …
Contribute to lbsid/en development by creating an account on GitHub.
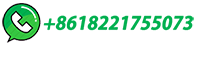
Tips to maximize crushing efficiency : Pit & Quarry
Jaw crushers are routinely choke fed, as this maximizes production capacity and ensures particles are uniformly broken. This promotes stone-on-stone crushing, breaking up flaky or slabby particles. If you seek fewer fines, trickle feeding material into the jaw crusher could achieve this.
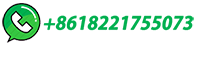
The flowchart of crushing process with one-stage and three …
Particles larger than the OSS of the crusher ''report'' to breakage and will undoubtedly be broken, while particles in between the CSS and open side set (OSS) report to breakage …
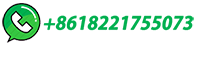
AA04
attrition and chipping of the larger and harder bauxite particles takes place. Eventual breakage of ... and broken rods removed. More recently these mill options have ... achieved by a combination of steps that may include jaw crusher, sizer, rolls and hammer crushers. Open circuit and closed-circuit crushing circuits are operated, as well as ...
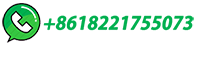
How To Choose Cement Crusher? | Jaw Crusher, Cone Crusher
The cement crusher is used to grind limestone or other materials into required particles. Common cement crushers include jaw crusher, cone crusher, impact crusher, and hammer crusher. In recent years, mobile crusher is popular in the cement plant. The cement crushing process. The raw material can be broken by extrusion, …
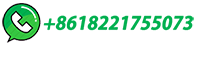
Influence of jaw crusher parameters on the quality of
A parameter study using a jaw crusher is designed to investigate the influence of feed gradation, feed rate, crusher setting and crusher speed on the crusher operation and the quality of the produced aggregates.
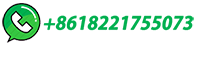
(PDF) Influence of jaw crusher parameters on the quality of …
A parameter study using a jaw crusher is designed to investigate the influence of feed gradation, feed rate, crusher setting and crusher speed on the crusher operation and the quality of the ...
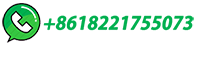
Capacities and performance characteristics of jaw crushers
Introduction. Although jaw crushers are extensively used for a variety of materials, their operational characteristics are not well understood. This lack of understanding makes …
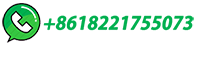
Types of Crushers: What You Need to Know
Often smaller and more expensive than a jaw crusher, gyratory crushers are suitable for larger amounts of materials when a more uniform shape is desired. Parts diagram of a gyratory crusher . Secondary crushing equipment. After materials go though their first round of crushing, they are fed into a secondary crusher to be broken down further.
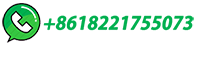
Estimate Jaw Crusher Capacity
The tables also show that for a comparable maximum size of feed and setting, a gyratory crusher has a much greater capacity than a jaw crusher. The gyratory crusher obtains this advantage only at the cost of greater power to drive the crusher.
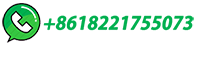
Spherical DEM simulation of particle breakage in an industrial jaw …
Spherical DEM simulation of particle breakage in an industrial jaw crusher. The large red particle in image (a) is broken into a set of smaller daughter particles in image (b).
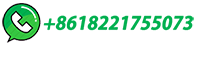
20+ Common Faults of Jaw Crusher with Solutions | M&C
Lining Plate Fracture. Reason: The size of the discharge port is too small, resulting in jamming; There are ironware entering the equipment. Solution: Adjust the discharge port …
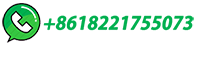
Types of Crushers Explained: Everything You Need to Know
The side setting in crusher like jaw crusher, is the distance between the fixed jaw and the moving jaw at the bottom of the crushing cavity. A side can be set to ensure that the garment size is consistent with the sewn one.
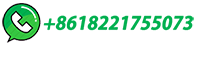
Cone crusher basics in 4 minutes
The CH cone crusher can be calibrated to achieve specific results, maximize productivity and minimize wear, but any calculation will be undermined without a solid understanding of what is going in to the crusher. Sampling is a vital part of the crushing process, to ensure that you know the size distribution of the feed. ...
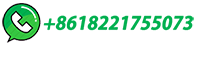
jaw crusher broken line particles after accounting for
jaw crusher broken line particles after accounting for A new methodical approach based on Compton scattering and XRF . the decomposition of lime stone, CaCO3 → CaO …
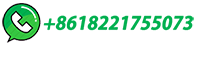
(PDF) Influence of jaw crusher parameters on the quality of …
A parameter study using a jaw crusher is designed to investigate the influence of feed gradation, feed rate, crusher setting and crusher speed on the …
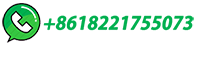
Primary Crusher vs. Secondary Crusher: Understanding Their …
The primary crusher is responsible for breaking down larger rocks and stones into manageable sizes, while the secondary crusher further refines these particles into the desired product. While both types of crushers are used in a variety of real-world applications, understanding their differences and when to use each type is crucial for ...
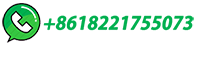
Comparison of sample properties and leaching
Particles from jaw crusher with irregular shape or multi-pointed corners created large unsaturation degree which has a negative impact on the air motion in the heap system ... the micro-crack forms approximately a straight line in the longitudinal direction and has a constant crack width, (d) gold grain size is directly proportional to the ...
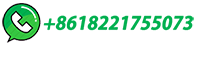
Primary Jaw Crusher – Everything You Need to Know
Learn everything you need to know about primary jaw crushers in this comprehensive guide. Discover how they work, their applications, and where to buy them from reputable sources. Whether you're in the mining or construction industry, this guide will help you make an informed decision when it comes to selecting the right primary jaw …
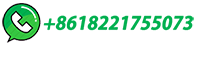
Effects of compression and sliding on the wear and
For compressive crushing, gyratory, jaw and cone crushers are used in the primary, secondary and tertiary stages of crushing, the jaw crusher being designed to …
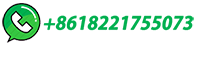
Jaw Crusher: Range, Working Principle, Application
Jaw crushers are used as primary crushers, or the first step in the process of reducing rock. They crush primarily by using compression. The rock is dropped between two rigid pieces of metal, one of which then moves inwards towards the rock, and the rock is crushed because it has a lower breaking point than the opposing metal piece.
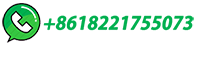
Below the surface: Setting up an underground primary jaw …
Jaw crushers are the most common solution in underground applications when the throughput is below 1000 tonnes per hour, depending somewhat on the …
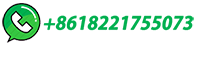
"Computer Aided Design of Jaw crusher"
the reciprocating action, when the swinging jaw moves away from the fixed jaw the broken rock particles slip down and are again caught at the next movement of the pitman and are crushed again to even smaller size.
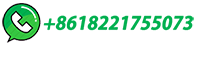