An operational model for a spiral classifier
The processing of heavy minerals and coal is often carried out using spiral classifiers. Processing of iron ore to separate coarse iron oxides such as hematite from light gangue mineral, such as quartz, is carried out in circuits with several hundreds of rougher, cleaner and re-cleaner spirals (Bazin et al., 2014). The development of spiral ...
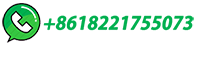
NEW DEVELOPMENTS IN SPIRALS AND SPIRAL PLANT …
Keywords: mineral processing, gravity separation, spiral, innovations, separation effi ciency, metallurgical performance. ... (most commonly in the treatment of iron ore). The design parameters of spiral separators can be classi …
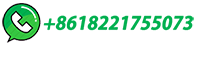
Modeling and optimization of spiral concentrator for separation …
Particle separation in the spiral concentrator was simulated by discrete element methodology for the iron ore fines [21]. Performance of spiral concentration operation at different operating variables was analyzed for the feldspar-mica separation [28]. But it can be observed that, limited literature is available on recovery of ultrafine ...
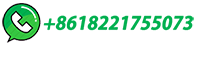
Spiral conditions for the recovery of ultra-fine …
Spiral separators for the recovery of ultra-fine particles have a unique profile, pitch and features to ensure it performs efficiently. The flow on the spiral trough must be controlled to minimise turbulence that will entrain fine particles in the outer section of the trough. Keywords: Ultra-fine particles, spiral, design, recovery 1. Introduction
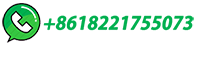
Beneficiation of Iron Ores – IspatGuru
Fig 1 Typical flow-sheet of ore beneficiation plant. Several methods / techniques such as washing, jigging, magnetic separation, gravity separation, and flotation etc. are used to improve the Fe content of the iron ore and to reduce its gangue content.
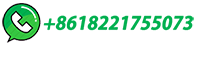
Revisiting spiral concentration as applied to iron Ore …
The application of concentrate spirals during the iron ore processing started in the sixties decade in a specular hematite concentration in Canada. ... Modelling particle separation in a spiral ...
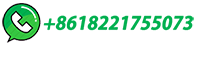
Evaluating separation efficiencies of Multotec's new …
The SC25 spiral has shown better Cr2O3 separation efficiencies than the SC21 model and with higher SiO2 rejection at saleable grades, thus providing an additional revenue …
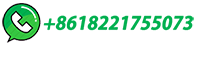
Spiral separation for optimised recovery
Because of this large density difference, spiral technology is ideal for separating the chromite bearing ore from the surrounding waste, so that a high grade product can be delivered into the ferrochrome industry," Menzi Xulu explains. The spiral can also easily produce other product grades like chemical and foundry grade sands.
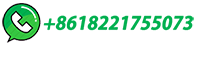
Spiral Classifier
Introduction: Spiral classifiers are the main equipment for the classification operation of the mineral processing plant. It is mainly used for ore classification, separation, screening, desliming, and dewatering in sand-washing operations. The spiral centrifugal classifier has the advantages of strong continuous operation, large processing capacity, low energy …
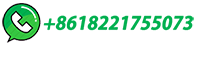
How do spiral concentrators work?
For the separation of fine heavy minerals, Multotec's ranges of mineral spiral concentrators greatly facilitate the processing of 1.5 o;mm to 0.1 mm particles. They're ideal for iron ore, chrome, mineral sands and high-density ores.
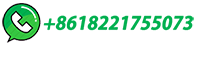
Modeling and optimization of spiral concentrator for separation …
In the present study, effects of several operating parameters on the separation efficiency of mica from feldspar by spiral concentrator were investigated. For this purpose, an albite ore containing … Expand
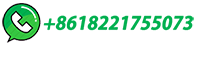
Improving Mineral Processing Efficiency With Spiral Chutes
Spiral chute, also known as a spiral separator, is commonly used in iron ore, ilmenite, chromite, pyrite, zircon, rutile, monazite, tungsten ore, chrome, tin ore, niobium ore, and other non-ferrous metals, rare metals and non-ferrous metals, and metal ore separation.In particular, the effect of placer mining on seashores, riversides, sandy …
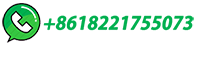
Axial or turn-by-turn particle recovery in a spiral concentrator
Results show that knowing the mineral size distributions in the spiral feed is necessary to forecast spiral performance. Further, in the case of iron ore processing, the separation process is practically complete after four turns, with wash water affecting the process rate of recovery.
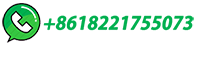
Observation of Iron Ore Beneficiation within a Spiral …
One such example is the iron ore sector, which involves separating large amounts of valuable iron minerals from gangue minerals. Plants processing those minerals treat many millions tons of ore every year, and most of the refinement and separation techniques used rely on bulk ore properties (density, size, magnetism) and wet processing.
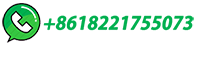
Application of response surface methodology for modeling …
Application of response surface methodology for modeling and optimization of spiral separator for processing of iron ore slime. ... was employed to understand the performance behavior of fine mineral spiral separator for separation of pre-concentrated iron ore ... it can be found that the flow pattern of gas–liquid mixture …
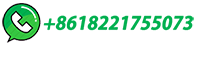
Observation of iron ore beneficiation within a spiral …
One such example is the iron ore sector, which involves separating large amounts of valuable iron minerals from gangue minerals. Plants processing these minerals treat many millions tons of ore every year, and most of the refinement and separation techniques used rely on bulk ore properties (density, size, magnetism) and wet processing.
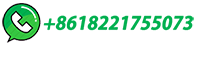
Iron Ore Processing: From Extraction to Manufacturing
Gravity Separation: Gravity separation exploits the difference in density between the iron-bearing minerals and the gangue minerals. Techniques such as spiral concentrators, shaking tables, and centrifugal separators are used to separate the heavier iron-rich particles from the lighter gangue minerals. ... Before iron ore can be used in …
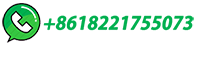
Humphreys Spiral Concentrator
Humphreys Spiral Concentration of Iron Ore. The installation in 1948 of a Humphreys spiral concentrator section at the Hill-Trumbull plant of The Cleveland-Cliffs Iron Co. is the latest commercial method on the Mesabi Range being used for the recovery of fine iron ore.
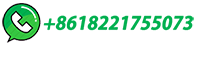
Gravity Spiral Concentrator Working Principle
The Humphreys Spiral Concentrator is a simple, efficient gravity concentrator which effects a separation between minerals of the proper size range that …
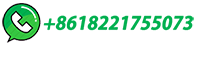
How to Improve the Separation Efficiency of Spiral Chute?
Here we're going to teach you how to effectively improve the spiral chute dressing efficiency from 3 aspects:. The structure index and performance of spiral chute. Feed ore characteristics. Process parameters in spiral chute operation
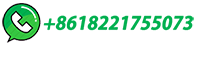
Performance Evaluation of Spiral Separator for Coal …
Spiral separator is considered to be the most effective gravity separator, capable of processing a wide range of minerals such as coal, iron, chromite, gold, zircon and other heavy minerals ores. Combined action of …
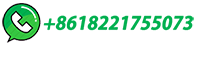
New heavy mineral spiral for recovery of …
New heavy mineral spiral for recovery of ultrafine chromite . Spiral concentrators are gravity separation units which are cost and energy efficient. They are widely used to treat various minerals such as coal, …
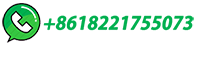
Size recovery curves of minerals in industrial spirals for …
Spirals are gravity concentrators used for the concentration of coal, iron oxide ore and heavy minerals. As in any gravity concentrators the separation of minerals in a spiral is based on particle size and specific gravity.
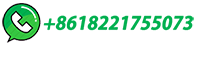
World leader in fine iron ore beneficiation
Extending beyond traditional spiral plants our designs for fine iron ore beneficiation incorporate gravity and magnetic beneficiation equipment with capacities ranging from 5 to ... latest HC33 gravity separation spiral technology, coupled with coarse and fine jig technology. Arrium engaged our expertise for
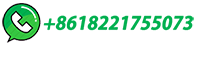
Mining Spiralling in control
Spiral separation technology has steadily developed over the past 60 years and is now routinely used in industrial minerals, base metal and coal operations …
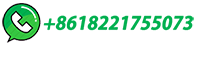
Evaluating separation efficiencies of Multotec's new …
contribute to the effectiveness of separation on a spiral. The effectiveness of separation is also dependent ... kimberlite-bearing ilmenite ore showed that the SC25 spiral achieved 20 % more ilmenite recovery than ... the spiral was run until steady-state conditions were reached before taking the relative density (RD)
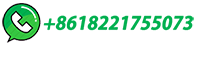
Axial or turn-by-turn particle recovery in a spiral concentrator
Results show that knowing the mineral size distributions in the spiral feed is necessary to forecast spiral performance. Further, in the case of iron ore processing, …
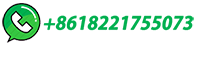
How to efficiently process iron ore spiral chute gravity separation
How to efficiently process iron ore spiral chute gravity separation? 💕💕💕 The finer the particle size of the sorted iron ore, the smaller the diameter of the spiral chute should be selected, and the hourly processing capacity will be correspondingly smaller.
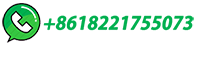
Application of response surface methodology for modeling …
In the present investigation, three factors three level Box–Behnken design of experiments coupled with response surface methodology (RSM) was employed to understand the performance behavior of fine mineral spiral separator for separation of pre-concentrated iron ore slime. Pre concentration of iron ore slime was done using …
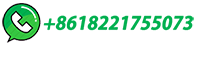
A Beneficiation Study on a Low Grade Iron Ore by …
Abstract—In this paper, a sample from Tange-zagh iron mine was characterized by gravity and magnetic sep-aration methods. The mineralogical studies showed that hematite and goethite are the main iron-bearing minerals with insignificant amounts of FeO. The results indicated that spiral separation yields higher separa-tion efficiency than others.
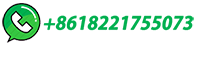