Development of a model estimating energy consumption values of primary
Most of the costs in open pit quarry operations occur in crushing and grinding processes. Therefore, the management of crushing–grinding processes is very important. Many researchers investigated the effects of pile size distribution and specific charge values occurring as a result of blasting on crusher energy consumptions and provided some cost reductions in …
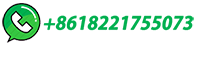
Crushing Products Size and Shape -What to Expect
The group of curves on the right is charted from screen analyses of the products of crushers receiving screened feed. They are useful in predicting the character of output from secondary and tertiary crushers, and are of great value in the preparation of plant flowsheets, and in calculating vibrating screen capacities.
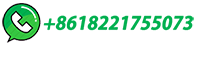
Downstream Crushing Options for Secondary, Tertiary …
Primary crushers can handle large feed lump sizes and typically include Jaw Crushers and Gyratory Crushers, but Impact Crushers may also be used as primary crushers if the material is easily crushed and not abrasive. ... whether for final product sizing or in preparation for final product sizing in the tertiary or quaternary stages.
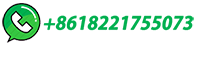
What Crusher Should You Choose for Primary Crushing?
The most common types of primary crushers: Gyratory crusher. Jaw crusher. Hammer crusher. 1. Gyratory crusher. Gyratory crushers are designed for medium to high …
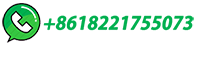
Crushing and Screening Handbook
the crusher and scalp out fi nes. Primary gyratory crushers – ideally suited to all high-capacity primary hard rock crushing applications. Jaw crushers – we have more installed jaw crushers …
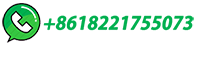
Primary and Secondary Crushing: Understanding …
The primary crusher receives the materials directly from the mine or quarry, and its size reduction ratio ranges from 3:1 to 7:1. The primary crusher can be a jaw crusher, gyratory crusher, or impact crusher, depending on the …
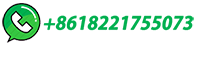
Primary Coal Crushers Grow to Meet Demand
Primary crushers reduce a wide range of large Run of Mine (RoM) coal to either a marketable product or a range that can be more easily handled by the preparation plant. More recently, as large mines try to crush RoM coal to a saleable product, the industry has seen the size of primary crushers grow. Moreover, crusher manufacturers are making ...
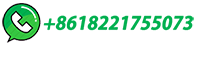
Construction Working and Maintenance of Crushers …
As the term "primary" implies, primary crushers are used in the first stage of any size reduction cycle. Generally gyratory crushers, jaw crushers, high speed double roll crushers, low speed sizers, impactors and hammer mills are used as primary crushers. In the secondary and subsequent stages, the material is further reduced and refined for ...
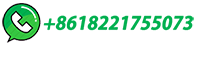
OPP: Ore Preparation Plants Explained | Oil Sands Magazine
The Ore Preparation Plant (OPP) is the first step within any Bitumen Production facility where mined oil sands is loosely crushed and mixed with hot/warm water to form a slurry that can be pumped to the main processing plant. ... The crushers/sizers break up clumps of oil sands into loose sand and crush any oversize material, such as ice or ...
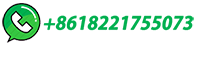
Primary Crushing: A Comprehensive Guide
Gyratory crushers, with their rotating mantle and conical-shaped opening, elevate the efficiency and capacity thresholds of primary crushing. Designed to handle input sizes from 500mm up to 2000mm, these powerful …
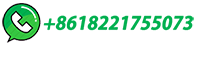
The Complete Guide to Primary Crushing, Secondary …
Primary, secondary, and tertiary crushing are three stages in the comminution process that break down large rocks into smaller pieces of varying sizes. Each stage uses different types of crushers and has distinct advantages and disadvantages. This article provides a comprehensive guide …
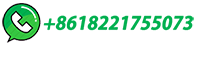
Compression mining crushers | Primary crushers | FL
Compression mining crushers for your mining aggregate/cement needs field By using high intensity compressive forces, your materials can be broken down into much smaller particles. However, the process is incredibly wear intensive, and can easily take its toll on your equipment and your operation.
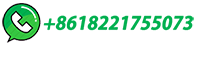
Primary Crusher Selection & Design
How you select your primary crusher will be based on factors like moisture content, maximum rock lump size, material density SG, abrasion index, degradability and it being prone to dusting or not. The crusher capacities given by manufacturers are typically in tons of 2,000 lbs. and are based on crushing limestone weighing loose about 2,700 lbs. per yard3 and …
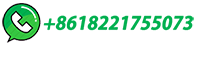
Crushing and Screening Handbook
Primary gyratory crushers – ideally suited to all high-capacity primary hard rock crushing applications. Jaw crushers – we have more installed jaw crushers than anyone in the world. The lead-ing choice due to their high reduction ratio and heavy duty design. Cone crushers – capacities available to suit all
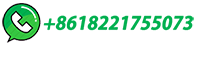
Industrial Solutions Jaw crushers
primary crushers to crush blasted rockpile, which may have edge lengths of over 2,000 mm depending on the blasting method, in preparation for finish crushing or conveying. For these tasks thyssenkrupp Industrial Solutions has in its range two types of jaw crusher, which differ in the kinematics of the swing jaw: single-toggle jaw crushers
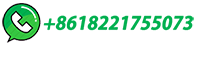
Crusher
Roll crushers are generally not used as primary crushers for hard ores. Even for softer ores, like chalcocite and chalcopyrite they have been used as secondary crushers. ... Small-sized jaw crushers (refer to Fig. 7.32) are installed in laboratories for the preparation of representative samples for chemical analysis. Figure 13.10. Medium-sized ...
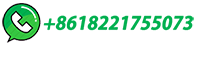
McLanahan | Crushers vs. Breakers: A Complete Guide for …
Jaws and Gyratories are more often used as primary crushers, while Cone Crushers, known for providing a good product shape, are often used for downstream crushing to refine the product size. Roll Crushers, Impactors and Hammermills can be used in the primary and/or the subsequent crushing stages. What is a breaker?
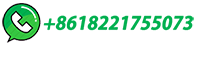
Lab Jaw Crusher
Typical applications will include general primary crushing of initial bulk or field samples in analytical and metallurgical laboratories, sampling stations, and pilot plants. Qingdao Decent Group Laboratory Jaw Crushers are robust, rugged, and durable single toggle crushers. The crusher frame adopts strong steel and cast iron structure.
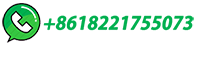
McLanahan | Roll Crushers
Single Roll Crushers are typically used as primary crushers that provide a crushing ratio of up to 6:1. They crush materials such as ROM coal, mine refuse, shale, slate, gypsum, bauxite, salt, ... Quad Roll Crushers are ideal for producers, including those with preparation plants, who want to accomplish two stages of reduction in one pass. They ...
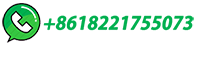
Primary Crusher Optimisation for Improved Comminution
The primary can produce these sizes at a rate of 150 to 12 000 mtph depending on the feed characteristics of the ore, the crusher setting, crusher size and the connected power to the crusher. The family of primary crushers typically used in the mining industry include the: • Gyratory. • Double toggle jaw. • Single toggle jaw.
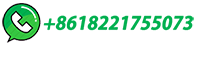
Primary Crusher vs. Secondary Crusher: …
A primary crusher is a machine that breaks down large rocks and stones into smaller particles for further processing. It is the first stage in the crushing process and is essential in the mining and construction industry. The …
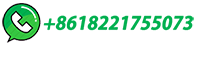
Jaw crushers for primary size reduction
Jaw crushers for primary size reduction RETSCH Product Navigator Milling Jaw Crushers – BB 51 – BB 100 – BB 200 – BB 300 Rotor Mills Cutting Mills Mortar Grinders Disc Mills ... ideal for sample preparation in laboratories and industrial plants. The throughput and final fineness depend on the type of instrument, the gap
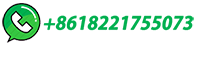
Primary Crusher vs. Secondary Crusher: …
While primary crushers are responsible for breaking down larger rocks and stones into smaller particles, secondary crushers are used to further refine these particles into the desired size and shape. The primary crusher is …
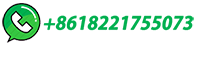
CG820 Primary Gyratory Crusher For Safe Crushing …
Stationary gyratory crushers. CG820i Capacity (by hour) 1,500 - 4,000 mtph (1,650 - 4,400 stph) Feed opening 1,372.0 mm (54.0 in.) Motor power 525 kw (700 hp) CG820i crusher is built to be robust, reliable and efficient. Connected to SAM by , they revolutionize availability and optimize uptime by giving you actionable insights ...
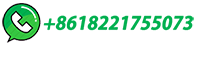
Crushers & Sizers | manufactor | thyssenkrupp
For instance, this principle was applied to the preparation of food or the crafting of tools. From muscle power to the thyssenkrupp Gyratory Crusher Pro ... Gyratory Crushers are commonly used in primary crushing applications and are able to process large rocks for mining ore, overburden or hard rock. ...
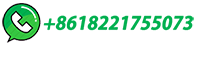
Types of Crushers Explained: Everything You Need to Know
Primary crushers are built to process large and abrasive feed materials. They can handle feed sizes of up to 1500 mm, but it depends on the type and size of the crusher. Jaw crushers and gyratory crushers are the two most common kinds of primary crushers. These crushers apply compressive forces to the material, but they can be different in ...
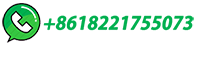
Aggregate Crushers, for Rock, Ore & Minerals
Morse crushers are heavy-duty and designed for high throughput and oversize feed, and available in models with 3, 5, or 10hp motors. Portable Crushers is a new line of Hammermill and Jaw Crushers that offer rugged construction, portability, and versatility of use. All can be equipped with gasoline or electric power.
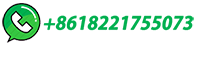
The Ultimate Guide to Primary Jaw Crushers: What They Are …
The capacity of a primary jaw crusher depends on the machine's size and the material being crushed. Typical capacities range from a few hundred tons per hour to more than 10,000 tons per hour. Types of Primary Jaw Crushers. There are two main types of primary jaw crushers: single toggle and double toggle.
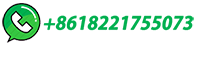
Different Types of Crushing Equipment for Lab Applications
Primary crushers are commonly used in mining and quarrying operations. Secondary Crusher. As the name suggests, secondary crushers follow the primary crushers and are used to further reduce the size of the material. ... Our Orbis range consists of dual-action fine crushers designed by experts with decades of experience in sample preparation ...
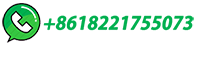
SIZE REDUCTION BY CRUSHING METHODS By
5 5.2 Gyratory crusher : A gyratory crusher is similar in basic concept to a jaw crusher, consisting of a concave surface and a conical head; both surfaces are typically lined with manganese steel ...
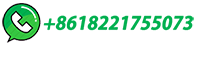