Jaw Crusher: What Is It & How Does It Work?
A jaw crusher is a machine that breaks down large rocks into smaller pieces of rock, gravel, or dust. It does this by placing two jaw plates perpendicular to each other and squeezing the rock between them until it is broken into small pieces. …
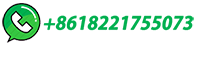
Site Safety and Safer Aggregate Crushing …
Crusher safety starts with the person feeding the plant. This person needs to be trained on crusher best practices specific to the machine they are working with. An operator may have years of experience of operating …
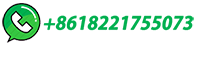
(PDF) An experimental investigation on rock crushability using jaw …
This study covers the investigation of rock crushability using laboratory-scale cone and jaw crushers for five types of hardrocks. For this purpose, physico-mechanical properties of the ...
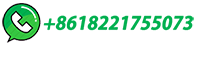
Assessing the energy efficiency of a jaw crusher
For a selected optimised case an attempt was made to simulate the jaw crusher using a commercial software for discrete element modelling (DEM), after first simulating single particle breakage using this software. ... The recommended procedure to avoid this situation is a momentary suspension of the contact forces between particles (i.e ...
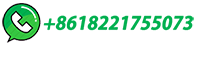
Optimisation of the swinging jaw design for a single toggle jaw crusher …
The plate dimensions of the un-optimised jaw crusher were modelled using ANSYS Design Modeller 2021, as shown in Fig. 3.The load and boundary conditions for the static structural analysis were as shown in Fig. 4.Design of Experiments (DoE) was then conducted where the minimum and maximum values of the target parameters were matched in possible …
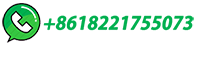
MC 110i EVO2 | Mobile jaw crushers | Kleemann
The jaw crusher MOBICAT MC 110 EVO2 is used for the precrushing of almost all natural rock and in recycling. Compact dimensions, efficient prescreening, simple operation via SPECTIVE as well as impressive production output characterize the efficient key player. ... SPECTIVE guides the operator step by step through the starting procedure. The ...
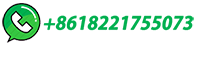
Jaw Crusher Explained
Size Reduction) A crusher is a machine designed to reduce the size of large rocks to smaller rocks, gravel, sand, or rock dust; this is essential for efficient transport of the product via conveyors etc. Crushing is the first of many stages …
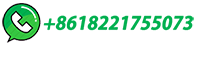
Safe Job Procedures For Crusher Operations
jaw crusher and cone crusher worksafe procedures jaw ... jaw crusher safe work operation ... safe work procedure using hand grinder_Sand Making Plant. PE series Jaw Crusher PEW Series Jaw Crusher HP series Cone ... Safety Tips for Crusher Operator Mining Metallurgy.
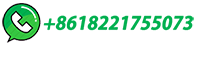
EXPERIMENT:- Jaw Crusher
PROCEDURE: • Start the jaw crusher and find the power consumption under no load condition with the help of energy meter and a stop watch. • Prepare the sample you want to crush in the jaw crusher. • Feed the above sample of coal to a jaw crusher …
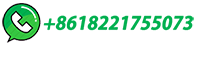
How to Properly Install and Use Jaw Crusher |
The operation and use procedures of jaw crusher 1.Preparation before starting. Before the jaw crusher is started, the equipment must be thoroughly inspected, for example, …
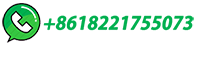
Crusher Shutdown Sequence & Procedure
Normal Crusher Shutdown Sequence & Procedure Shut down the apron feeder. Wait until all equipment is free of material. Shut down the jaw crusher. Stop conveyor #3, associated interlocks will shut down the rest of the equipment. Shut down the cone crusher and lube system. De-energize the electromagnet. (Swing the magnet clear of the conveyor ...
AMIT 129: Lesson 12 Crusher and Mill Operation Safety
Recently an overseas operator with more than 4 years experience was killed when a heavy jaw crusher liner plate dislodged as he was attempting to secure it. This type of accident calls attention to the need to have safe maintenance procedures for all tasks. Maintenance procedures must take account of manufacturer's instructions and safety ...
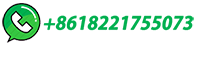
® C Series™ jaw crushers Proven reliability and …
® C Series™ jaw crushers have proven to be reliable and productive in thousands of mining, quarrying, recycling and industrial applications with up to 11,000 jaw crusher installations since 1975. Developed to crush the hardest ores and rocks, jaw crushers also perform outstandingly with less demanding materials.
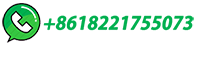
Jaw Crusher
The size of a jaw crusher is usually described by the gape and the width, expressed as gape × width. The common crusher types, sizes and their performance are summarised in Table 4.1. Currently, the dimensions of the largest Blake-type jaw crusher in use are 1600 mm × 2514 mm with motor ratings of 250–300 kW.
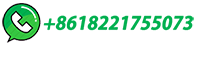
August 26, 2020 Fatality
OVERVIEW. On August 26, 2020, at 12:30 p.m., Bobbie D. Skillett died when the right side hopper extension of the jaw crusher fell on him. He was a 52-year-old Crusher Foreman with more than 23 years of mining experience, including approximately four weeks of experience with Chilton Logging Inc. Skillett was preparing the jaw crusher for transport by removing both …
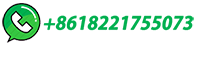
5 Common Questions about Jaw Crushers Answered
The space at the bottom of the V-aligned jaw plates is the output gap that dictates the size of the crushed product from the jaw crusher. The rock remains in the jaws until it is small enough to ...
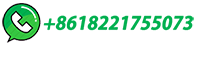
The Complete Guide to Primary Crushing, Secondary …
Learn everything you need to know about primary crushing, secondary crushing, and tertiary crushing in this comprehensive guide. Discover the types of crushers used in each stage, their working principles, and the advantages and disadvantages of each process. Get answers to frequently asked questions and improve your understanding of the comminution …
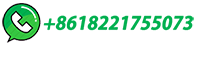
How Does a Jaw Crusher Work | Jaw Crusher | Kemper Equipment
A fixed jaw, mounted in a V-shaped alignment, is the stationary breaking surface, while a movable, "swing" jaw exerts force on the feed material by pushing it against the stationary plate. The space at the bottom of the "V"-aligned jaw plates is the output gap that dictates the size of the crushed product from the jaw crusher.
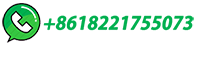
MINERAL PROCESSING LABORATORY MANUAL
To crush the of coal in a Primary Jaw Crusher (Blake Jaw Crusher), and determination of average product size by the use sieve shaker. MATERIALS / APPARATUS REQUIRED: 1. Coal 2. Different sieve screens of ASTM size. 3. Black jaw crusher 4. Weight balance 5. Ro-Tap sieve shaker THEORY: Blake Jaw Crusher: It has its moving jaw pivoted at the top ...
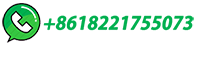
How Does a Jaw Crusher Work? A Simple Guide
A jaw crusher operates by the movement of a movable jaw in relation to a fixed one to crush large rocks into smaller pieces. It does this by using a spinning shaft that makes the movable jaw move back and forth. When the movable jaw goes towards the fixed jaw, it squishes the stuff in between and breaks it into smaller bits. ...
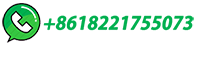
Jaw crusher maintenance | Pit & Quarry : Pit & Quarry
To prevent crusher damage, downtime and difficult maintenance procedures, the hydraulic overload relief system opens the crusher when internal forces become too high, protecting the unit against costly component failure. After relief, the system automatically returns the crusher to the previous setting for continued crushing.
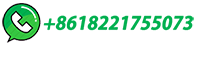
The Ultimate Guide to Jaw Crushing Machines: …
One of the main advantages of using a jaw crusher is that it can handle a wide range of materials. Jaw crushers are able to crush rocks, ores, and other materials of varying hardness, making them a versatile option for many …
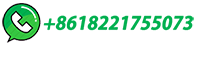
STANDARD OPERATING PROCEDURES Jaw Crusher
ry damage).Pre-Operational Safety ChecksLocate and ensure you are familiar. with all machine operations and controls.Ensure that the wall-mounted dust collection system. is turned on before starting the crusher.Position the dust collect. on intake near the output of the crusher.De …
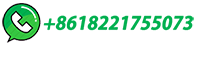
Understanding Jaw Crusher Parts and Their Functions
Introduction: Jaw crushers are powerful machines that are widely used in the mining, quarrying, and recycling industries. These machines are designed to crush large rocks and ores into smaller pieces for further processing. A jaw crusher consists of a fixed jaw and a movable jaw, with the latter being driven by an eccentric shaft that moves the jaw up and down.
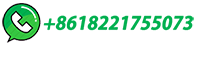
What Are Jaw Crushers and How Do They Work? | Oreflow
The size of a jaw crusher is measured by the top opening of the crushing chamber. For example, a 48" x 42" jaw crusher measures 48" from one crushing jaw to another and is 42" across the width of the two crushers. The primary applications for using jaw crushers are: Crushing different kinds of ore; Reducing building rubble to pieces
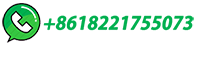
SOPs For Using Cement Crusher | Crusher Mills, Cone Crusher, Jaw …
» How to use Jaw crusher … » minerals extracted using the slurry pump » cement kiln burner manufacturer … Standing Operating Procedures–Reconstitution. 1.
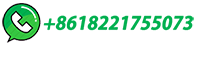
An evaluation of the procedure and results of laboratory …
With worn jaw ends (indicated by a in Tables 1, 2 and 4) the crusher had a wider setting (22 mm compared to 17 mm). At laboratory 3, crushing stages 1 and 2 were performed with separate laboratory crushers. The primary crusher can crush larger fragments of rock and the fragment size of the feed has an effect on the reduction ratio.
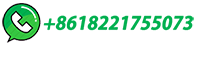
STANDARD OPERATING PROCEDURE NO. 8 SAMPLE …
4. If applicable, homogenize fine-grained material and split out 50 grams using cone and quarter method to be used for DI leach. 5. Crush rock samples using large jaw crusher (if necessary), then use small jaw crusher until particles are pea sized. 6. Homogenize. 7. Crush pea-size sample in tungsten carbide disc grinder (hockey puck) to approx. 100
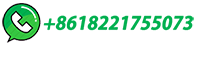
Crushing and Screening Handbook
the crusher and scalp out fi nes. Primary gyratory crushers – ideally suited to all high-capacity primary hard rock crushing applications. Jaw crushers – we have more installed jaw crushers than anyone in the world. The lead-ing choice due to their high reduction ratio and heavy duty design. Cone crushers – capacities available to suit all
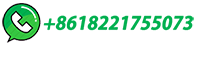
Jaw Crusher: Range, Working Principle, Application
Jaw crushers are used as primary crushers, or the first step in the process of reducing rock. They crush primarily by using compression. The rock is dropped between two rigid pieces of metal, one of which then moves inwards towards the rock, and the rock is crushed because it has a lower breaking point than the opposing metal piece.
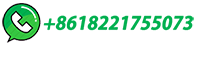