Crushing Plant: Surge Bins VS Stockpiles
There is no reason why this same expedient cannot be applied in a quarry operation; following the primary, or secondary, crushing stage. Aside from the production insurance it affords, such a stockpile is an excellent point from which to regulate the feed to the reduction crushing stages and screens, by means of one or more mechanical feeders.
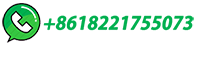
What is the definition of crushing in mining?
What is the purpose of secondary crushing in the production of lime? What is the minimum possible crushing size of limestone after it has been crushed in a crusher? What is the role of crushing in ...
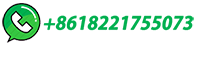
Production
Crushing and washing. The trucks tip the limestone into a large primary crusher which usually relies on either impact or compression to break the rock.
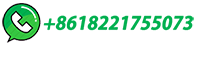
Downstream Crushing Options for Secondary, Tertiary …
This is where downstream crushing with secondary, tertiary and quaternary stages comes in. Secondary Crushing. Secondary crushing (or intermediate crushing) accepts the material from the primary crushing stage and reduces it even further, whether for final product sizing or in preparation for final product sizing in the tertiary or …
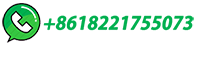
What is the purpose of secondary crushing in the production …
The purpose of secondary crushing in the production of lime is to reduce the size of the material before grinding. It can also be used to reduce the size of the material for...
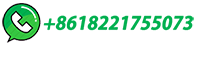
Secondary Crushing 101: Everything You Need to Know
Discover the basics of secondary crushing and what you should know. Explore more on our blog for insightful information.
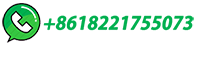
How Lime is Made
Limestone enters a primary crusher to break the rock. Depending on the size of the feedstone required, limestone may go through a secondary or tertiary crusher to further …
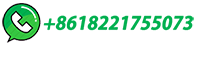
Crushing in Mineral Processing
The picture above shows an example of how the crushing plant can be divided into primary, secondary, and tertiary stages. The aggregate produced in a primary crusher is classified using a screen into a 0-20 mm …
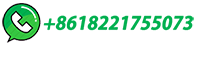
Primary and Secondary Crushing: Understanding the Basics …
Secondary crushing is the second stage of crushing that takes place after the primary crushing. The secondary crusher is the equipment that reduces the size of …
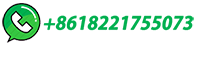
Primary Crusher vs. Secondary Crusher: Understanding Their …
Overall, both primary and secondary crushers play an important role in the crushing process and are essential components in the mining and construction industry. Understanding their differences and when to use each type is crucial for achieving the desired product size and shape.
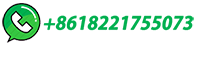
LIME SLAKING 101
Lime is used in a wide variety of industrial processes: from pH control to water and flue gas treatment, pulp and paper manufacturing to the production of some metals (to name just a few). In many of these applications, hydrated lime, or calcium hydroxide (Ca(OH) 2), is used. This is produced by adding water to quicklime (calcium oxide, CaO).
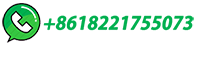
GitHub
{"payload":{"allShortcutsEnabled":false,"fileTree":{"":{"items":[{"name":"1701743034.jpg","path":"1701743034.jpg","contentType":"file"},{"name":"1701743035.jpg","path ...
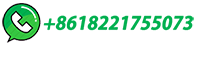
CRUSHING SCREENING
AND CONCRETE PRODUCTION INDUSTRY Meka was founded in 1987 in Ankara, Turkey, by a well-educated, visionary and ... Reliable primary, secondary and tertiary crushing groups that have been designed and manufactured with precise engineering and first-class workmanship.
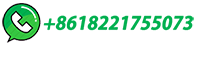
Primary Crusher vs. Secondary Crusher: Understanding Their …
In the aggregate industry, primary crushers are used to break down larger rocks and stones into smaller particles, while secondary crushers are used to further …
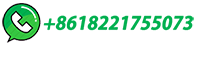
Limestone Crushing Process
The typical limestone crushing process is Primary Crushing -> Secondary Crushing -> Screening -> Conveying -> Storage. Skip to content ... The hydrated lime is prepared into lime slurry, lime paste, etc., as coating materials and brick adhesives. ... Limestone is a key ingredient in cement production and is also used in various industrial ...
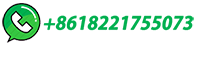
Limestone Crusher: What Is It & How Does It Work?
A limestone crusher is essentially a heavily built machine designed to reduce large rocks and stones, such as limestone, into much smaller pieces. Its uses vary from residential …
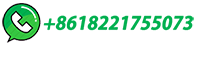
Limestone crushing and grinding production line
After limestone is mined from limestone rock, it is crushed to form limestone particles, namely stone and sand. Or further grinding to form limestone powder, which is widely used in building materials, highways, metallurgy, chemical …
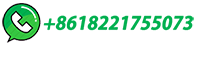
What Machines Do Stone Crushing Plants Need? | Fote …
A stone crushing plant is a special site where mined stones are processed into different sizes using one or various stone crushing machines (primary, secondary, and tertiary). However, the operation of a stone crushing plant is understandably complex.
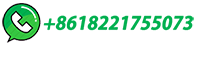
Perfecting the Performance of Secondary Crushers | E & MJ
E&MJ asks eight industry experts how best to optimize the operation and throughput of secondary crushing circuits. By Carly Leonida, European Editor. The role of the secondary crushing circuit, like every other stage in mineral processing flowsheets, is to prepare the feed material for the next stage of the process.
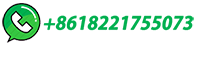
Screening 101
It indicates just what is available for recovery by screening through and over certain openings in a commercial production screening operation and also shows the reduction obtained by passage through crusher or grinding mill. ... Type and setting of primary crusher and secondary crusher? ... By "closed circuit" crushing or grinding it is ...
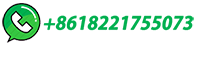
Calcium Carbonate Manufacturing Process and Equipment …
Machines Used for Processing Calcium Carbonate. Heavy machinery is primarily used during the dry processing phase, when calcium carbonate manufacturing processes focus on reduction through milling, crushing, and screening, whereas air classification is generally used in later reduction phases.
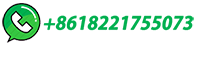
(PDF) Comminution a Heart of Mineral Processing
Mineral liberation as the main purpose of comminution in ore beneficiation is not applied in the design of comminution machines or even often neglected in designing comminution circuits.
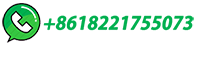
11.19.2 Crushed Stone Processing and Pulverized …
The stone that is too large to pass through the top deck of the scalping screen is processed in the secondary crusher. Cone crushers are commonly used for secondary crushing …
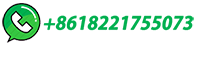
Roll Crushers | Williams Crusher
Both single and double-roll crushers operate most efficiently with dry, friable materials. However, the successful use of single-roll machines to reduce moist clays has occurred. Double crushers are successful for both primary and secondary crushing when minimizing fines. Single Roll Crushers. These machines reduce via impact, shear, and ...
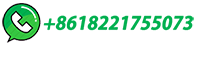
Rock Crushing Equipment | Rock Crushers | Kemper …
As the first stage in a crushing circuit following extraction from a mine site, (or in the case of recycled asphalt production, delivery to the RAP processing plant via truck transport), primary crushing reduces material to a size and shape that can be handled by the secondary crusher.
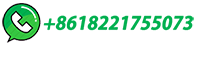
The Complete Guide to Primary Crushing, Secondary …
The purpose of secondary crushing is to produce a smaller, more uniform product size that can be fed into the tertiary crushers. This helps to optimize the …
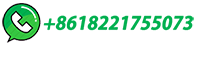
Perfecting the Performance of Secondary Crushers
In most applications, the secondary crusher has a primary target of maximizing the reduction ratio and reducing the top size and F80 for the downstream equipment. …
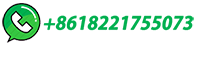
Limestone crushing technology and equipment
Recommended machines for crushing limestone. Depending on the purpose and the fineness of the output, the choice of limestone crusher will also be different. ... In the limestone crushing production line, the coarse crushing equipment can crush the large pieces of limestone mined into stones of 125-400mm in size. ... the …
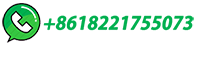
Do's & Don'ts Of Limestone Rock Crushing | Mellott
Limestone crushing is an essential part of the mining and construction industry. Cone crusher parts are used for this purpose, and they come in various sizes and configurations to match different applications. However, every operator should be aware of certain do's and don'ts when using cone crushers before making any adjustments or …
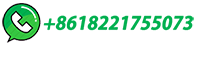
Stone Crusher Plant Design: Best Practices for Efficient Crushing
Discover the best practices for designing a successful stone crusher plant, including factors to consider, equipment selection and configuration, environmental management, and safety and maintenance priorities. Learn how to optimize crushing operations and minimize environmental impact for efficient and effective production.
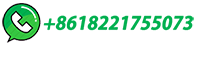