Types of Crushers Explained: Everything You Need to Know
The decision of a jaw crusher or a gyratory crusher is based on, for instance, the required output size, production capacity, and the available budget. ... Hardness: The hardness of a material determines the crushing force needed and the type of crusher that is suitable. Crushing of the harder materials may require the use of the …
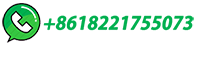
DEM simulation and optimization of crushing chamber shape of gyratory
The working process of the gyratory crusher is used as a specific analytical target in this paper, and the performances of the gyratory crusher, including productivity, mass percentage of effective particles, and crushing …
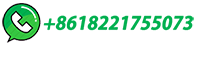
Crusher Close Side Settings
The actual minimum safe closed side setting of a crusher will vary somewhat, for any given crushing machine, depending upon the character of the material, the amount of fines in the feed, and whether the crusher is being operated under choke-feed or regulated feed conditions. It is possible, when all conditions are favourable, to …
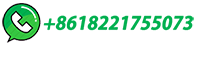
AMIT 135: Lesson 5 Crushing – Mining Mill Operator Training
Crushing occurs between two moving plates that are arranged to form an acute angle to apply a compressive force that results in tensile failure; Typically preferred for feed rates of 900 tph or less. ... Diagram of a gyratory crusher [image: 135-5-16)] Gyratory Crushing Action. Designs of the breaking faces vary with manufacturer. As a result ...
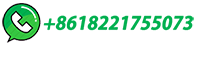
Mathematical Modeling and Multi-Criteria Optimization of …
Mathematical modeling and optimization of the design parameters of the working chamber and the executive body (roll) of a single-roll gyratory shaft crusher, designed for crushing strong rocks ...
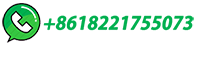
Mathematical Modeling and Multi-Criteria Optimization of …
Mathematical modeling and optimization of the design parameters of the working chamber and the executive body (roll) of a single-roll gyratory shaft crusher, designed for crushing strong rocks, was performed in this paper.
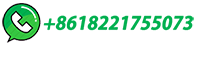
Types of Crushers: Choosing the Right One for Each Stage
Gyratory Crusher. Gyratory crushers use the oscillating motion of the crushing cone to compress and crush hard ores and large materials, making them particularly suitable for high-hardness and abrasive materials. They produce smaller particle sizes and can generate fine needle-like particles, but can only handle dry to slightly wet …
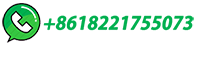
Primary Crushing | AllMinings
Gyratory Crusher: This equipment employs a gyrating motion, where a conical head revolves within an outer concave bowl. This motion compresses the material against the concave, producing finer output. ... "Relentless Crushing Force" encapsulates the dynamic and robust nature of the primary crushing operation, highlighting its critical …
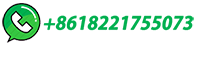
Superior™ MKIII 42-65 primary gyratory crusher
Superior™ MKIII 42-65 primary gyratory crusher brings high capacity and lower footprint to your mineral processing circuit's primary crushing. Read more here.
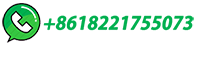
Primary Crusher vs. Secondary Crusher: …
The primary crusher is usually a jaw crusher or a gyratory crusher, which operates by compressing the material between two surfaces. The jaw crusher works by moving the material between a …
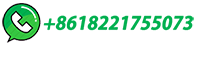
Mining crushers SuperiorTM MKIII Primary Gyratory
Superior™ Primary Gyratory MKIII Range Perfect mix of experience and innovation 100+ years of proven experience, latest advancements in metallurgy and thousands of crusher installations around the world combine to create a Primary Gyratory crusher with the best performance, highest capacity and highest reliability.
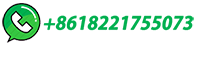
CG820 Primary Gyratory Crusher For Safe Crushing …
CG820i crusher offer excellent reliability and safer & faster maintenance – up to 30% faster than competing crushers. A robustly designed one-piece main shaft and reinforced shells are made for tough use.
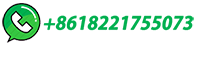
Types of Crushers: What You Need to Know
The hammers are attached to a disk and swing with centrifugal force against the casing. Material is fed into the top and crushed the falls through the hole at the bottom. ... The main features of a Gyratory Crusher include a tall crushing chamber lined with replaceable manganese wear plates, a main shaft with head and mantle, and a spider to ...
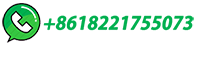
Gyratory Crusher
The majority of gyratory crushers are used as primaries, i.e. they receive the initial feed from the mine or quarry. The same type of crusher with chamber modifications is used as a secondary crusher, particularly when following a large primary crusher. The fine-reduction gyratory crusher can also be used for tertiary crushing.
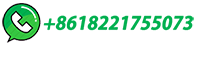
Simulation and optimization of gyratory crusher
Therefore, the working process of the gyratory crusher is taken as the specific analysis object, in this paper, the gyratory crusher performances, including the productivity, crushing force distribution, and particle size distribution, are explored by the DEM simulation.
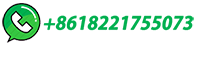
Crusher
The primary gyratory crusher offers high capacity thanks to its generously dimensioned circular discharge opening (which provides a much larger area than that of the jaw crusher) and the continuous operation principle (while the reciprocating motion of the jaw crusher produces a batch crushing action). The gyratory crusher has capacities ...
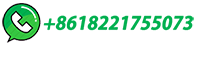
What Are the Differences Between The 7 Types of Crushers?
Jaw rock crusher VS gyratory crusher Different crushing principles Jaw crusher is a compression type of crushing machine. The flywheel works together with eccentric shaft and toggle plate provides a motion which pushing moveable jaw plate towards stationary jaw dies, and during the process, a compressive force squeezes raw …
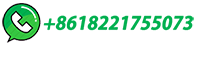
DEM simulation and optimization of crushing chamber shape of gyratory
It can be seen that the working process of the gyratory crusher mainly includes the feeding process, the breaking process when ore particles fill the crushing chamber, and the discharging process. The initial productivity, mass percentage of effective particles, and crushing force of the gyratory crusher can be obtained.
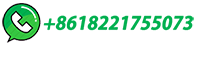
Torque Analysis of a Gyratory Crusher with the Discrete …
In this paper, a 60-110 gyratory crusher of 1500 kW nominal power operating in a Chilean copper mine is modeled and simulated by using the discrete …
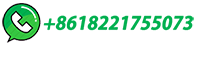
Gyratory Crusher | Hazemag North America
A gyratory crusher is one of the main types of primary crushers in a mine or ore processing plant. Gyratory crushers are designated in size either by the gape and mantle diameter or by the size of the receiving opening. Gyratory crushers can be used for primary or secondary crushing.
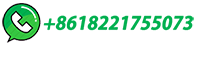
The Ultimate Guide to Rock Crushers | Mellott
These machines work by applying force to break rocks. They are essential in industries like mining and construction. ... Impact crushers are versatile, used for primary and secondary crushing. Gyratory Crushers ... Gyratory crushers are ideal for hard and abrasive rocks. Selecting the Right Rock Crusher Choosing the right rock crusher is ...
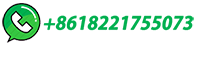
Simulation and optimization of crushing chamber of gyratory crusher …
At present, there are relatively little researches on the chamber shape of the gyratory crusher, mainly focusing on cone crusher. Compared with the gyratory crusher, this type of crusher has a relatively small crushing force and compression ratio, and their changes are small.
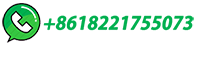
Gyratory Crushers | Mellott
Gyratory crushers can be divided into two categories: cone and impact gyratory crushers. Cone gyratory crushers are the most common type and are used to crush medium to hard materials. They work by forcing the material to fall between two cone-shaped crushing surfaces, which effortlessly reduces the size of the material.
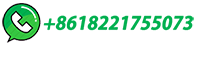
Simulation and optimization of gyratory crusher
To study and optimize the gyratory crusher performance, taking the process of crushing iron ore by the gyratory crusher as the specific analysis object in this paper.
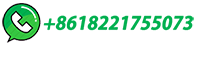
CG810 Primary Gyratory Crusher For Maximum …
Well-designed crushing chambers built from strong materials make a fulcrum point that ensures a constant eccentric throw, guaranteeing up to 90% of feed opening.
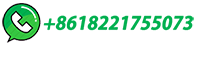
Application guide SUPERIOR® primary gyratory crusher …
Operating a gyratory crusher within its design parameters reaps huge benefits for the end-user, most notably, maximum crusher online availability, lowest possible ... angle, power draw, crushing force and capacity requirements. The required product output size is achieved with the design of the lower tier concaves together with
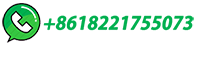
Gyratory Crusher | SpringerLink
Gyratory crusher is a crushing equipment that uses the gyratory motion of the crushing cone in the conical cavity inside the shell to extrude, bend, and impact …
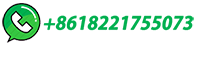
Ore Crushing | SpringerLink
The maximum crushing ratio of coarse crushing is about three. The main force in the coarse crushing of ore is crushing. Typical coarse crushing equipment includes jaw crusher, gyratory crusher, and roller-tooth crusher. Ore medium crushing is a process of crushing ore blocks with a feeding particle size of 125–400 mm to 50–100 …
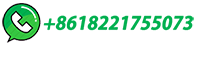
Simulation and optimization of gyratory crusher
The crushing force is an important performance index of the gyratory crusher, which is related to the geometric parameters of the crushing chamber and the …
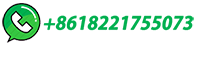
Jaw Crusher
The primary gyratory crusher offers high capacity thanks to its generously dimensioned circular discharge opening (which provides a much larger area than that of the jaw crusher) and the continuous operation principle (while the reciprocating motion of the jaw crusher produces a batch crushing action). The gyratory crusher has capacities ...
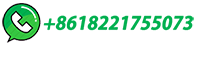