Production Process | CEMEX Philippines
The crushed raw materials are then delivered by belt-conveyor to our production facilities, where we manufacture cement through a closely controlled chemical process. In this process the limestone and clay are first pre-homogenized, a process that consists of combining different types of limestone and clay.
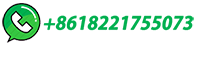
Cement Manufacturing Process
Production of cement completes after passing of raw materials from the following six phases. These are; Raw material extraction/ Quarry. Grinding, …
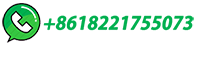
Cement
The three processes of manufacture are known as the wet, dry, and semidry processes and are so termed when the raw materials are ground wet and fed to the kiln as a slurry, …
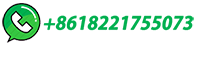
Cement Manufacturing Process- Wet and Dry Processes
Cement is a crucial building material used in construction. The Cement manufacturing process involves the extraction and preparation of raw materials, such as Limestone, clay, shale, iron ore, and Gypsum.
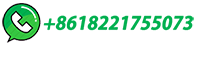
Construction of cement plants under an EPC contract
Typically, cement plants are built in close proximity to raw material extraction sites, which helps to minimize transportation costs. Cement production includes the following stages: • Extraction of raw materials and their delivery to the plant. • Crushing and grinding of raw materials to the required degree.
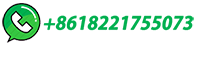
Projecting future carbon emissions from cement production …
In Group 2 countries, the largest cement producer, China, started most large-scale construction of cement plants around the year 2000 and experienced rapid growth in production from around that time.
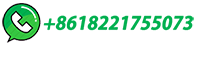
Global database of cement production assets and upstream …
The cement industry plays a crucial role in the global economy as it is used in the production of various infrastructure and construction projects.
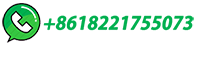
China's provincial process CO2 emissions from cement production …
Carbon dioxide (CO2) emissions from China's cement production process have increased rapidly in recent decades, comprising the second-largest source of CO2 emissions in the country, next only to ...
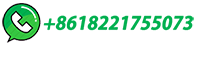
Process technology for efficient and sustainable cement production
The technology of cement production will without doubt be developed further in future years, as it has in the past. The challenges which remain for the cement industry are: to reduce production costs, and to keep a strong focus on quality, performance and cement's impact on concrete durability.
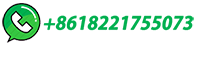
Cement Industry in Sri Lanka
2 CEMENT MANUFACTURING PROCESS A cement production plant consists of three major processes such as quarry and raw material preparation, clinker production and cement grinding and distribution [2]. During raw material preparation first, limestone and other raw materials are extracted using drilling and blasting techniques. ...
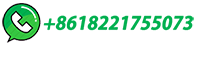
Cement Plant: The Manufacturing Process 4 5
Limestone (CaCO3) is taken from a quarry The cement is then packed and distributed to 3. consumers The crushed limestone and aggregates such as sand, clay and ironstone are …
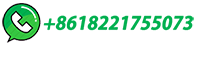
New approach suggests path to emissions-free cement
A new process developed at MIT could eliminate the greenhouse-gas emissions associated with the production of cement, the world's most widely used building material and a major source of such emissions.
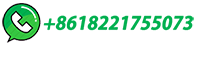
The Cement Manufacturing Process
Cement manufacturing is a complex process that begins with mining and then grinding raw materials that include limestone and clay, to a fine powder, called raw …
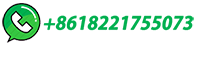
Manufacturing process
The cement manufacturing process starts from the mining of raw materials that are used in cement manufacturing, mainly limestone and clays. A limestone quarry is inside the plant area and a clays quarry is as far from the plant area as 25 km.
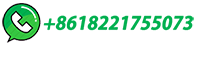
PPC Cement Manufacturing Process
AGICO Cement is a Chinese company that specialized in manufacturing and exporting cement production lines and cement equipment, providing turnkey projects that cover project design, equipment installation, equipment commissioning, equipment maintenance, and spare parts supply.
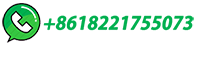
AP-42, CH 11.6: Portland Cement Manufacturing
As shown in the figure, the process can be divided into the following primary components: raw materials acquisition and handling, kiln feed preparation, …
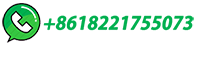
Cement manufacturing: components of a cement plant
This page and the linked pages below summarize the cement manufacturing process from the perspective of the individual components of a cement plant - the kiln, the cement …
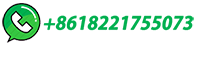
Clinker Production
The kiln is known as the heart of the cement production process. This process makes chemical and physical changes that turn the raw meal into a clinker. Natural gas, petroleum coke and coal are the fuels used for heating the kiln. ... proposed a plant concept to produce hydrogen from waste gasification integrated into a cement production plant ...
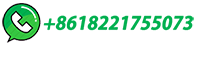
Deep decarbonisation of industry: The cement sector
Fossil fuel combustion to meet heating needs accounts for 35% of cements CO2 emissions. The remaining 65% are due to direct process emissions, which must also be addressed. By 2050, cement production in …
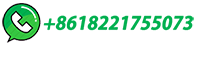
Decarbonisation pathways of the cement production process …
Cement production, responsible for about 8 % of global carbon dioxide (CO 2) emissions [2], has widely been identified as a primary target for progressive decarbonisation efforts. In the conventional cement production process, CO 2 emissions primarily result from the production of clinker, the main component of Portland cement [3].
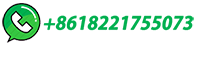
Alternative Fuels in Cement Manufacturing | IntechOpen
In 1995 the world production of cement was about 1420 million tonnes (Cembureau, 1997). Cement production is an energy-intensive process consuming thermal energy of the order of 3.3 GJ/tonne of clinker produced, which accounts for 30 – 40 percent of production costs (Giddings et al., 2000; EC, 2001). Worldwide, coal is the …
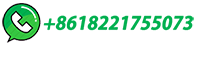
How Cement is Made
The raw cement ingredientsneeded for cement production are limestone (calcium), sand and clay (silicon, aluminum, iron), shale, fly ash, mill scale, and bauxite. The ore rocks are quarried and crushed into smaller pieces of about 6 inches. Secondary crushers or hammer mills then reduce …
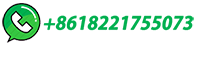
(PDF) Cement Industry in Sri Lanka
A cement production plant consists of three major processes such as quarry and raw material ... the environmental impact of cement production process starting from preproduction stages is ...
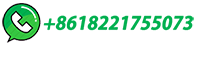
The four major costs associated with cement production
The power requirement of cement plants varies in accordance with the heat treatment process used viz., dry process or wet process. While the wet process requires almost 1,300-1,600 kcal/kg of clinker and 110-115 kwh of power to manufacture 1 tonne of cement, the dry process requires 720-990 kcal/kg of clinker and 95-110 kwh of power.
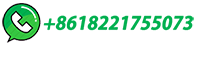
(PDF) Cement Manufacturing
Process Discretion: Wet process, Semi-dry process, Dry process and Finish process. The environmental im pact of the cement production and its variations between different cement plants, using Life ...
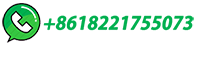
Cement Manufacturing Machine
Cement rotary kiln is the core equipment of cement plant, mainly responsible for clinker calcination, which can be used both in dry process cement production line and wet process cement production line. It is usually placed horizontally and at an angle to the ground, forming a state of one end high and one end low.
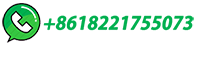
Cement Production: How Cement Is Manufactured | CEMEX …
Take a look at our interactive animation of the cement production process to learn how cement is made by us at CEMEX.
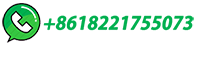
Cement Production Demystified: Step-by-Step Process and …
Explore the intricacies of cement production, from quarry to packaging, and understand the environmental impact. Learn step-by-step processes, energy efficiency strategies, …
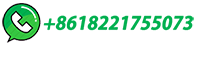
How Cement Is Made | Heidelberg Materials
All over the world, cement is one of the most important building materials. Whether for houses, bridges or tunnels, we cannot imagine our modern world without it. Join us for a short tour to experience how cement is made: starting with the extraction of raw materials and ending with the finished product.
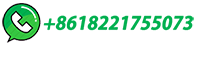
Mastering Process Control Instrumentation in Cement Plants…
Process control solutions for cement plants are designed to provide comprehensive control and monitoring of the entire production process. They integrate the various process control instruments and the operational data into a unified system, providing a holistic view of the plant performance.
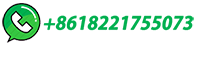