Recovery of Iron Ore Fines and Ultrafines from Tailings …
In addition, these secondary deposits have already been mined and processed, meaning that the recovery of high-grade product requires low capital and operating costs.The most widely used process for the recovery of these valuable fine and ultra-fine hematite iron particles is the wet high-intensity magnetic separation technique, originally ...
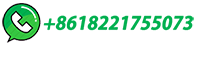
Optimal Recovery of Iron Values from a Low Grade Iron Ore using
A low grade iron ore containing 51.6% Fe, 17.6% SiO2, 4.3% Al2O3, and 3.8% LOI was subjected to reduction roasting followed by low intensity magnetic separation studies. The phase transformation of hematite into magnetite and fayalite due to reduction roasting was investigated using reflected microscope and X-ray diffraction (XRD) techniques. The effects of …
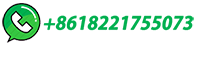
Influence of process parameters of dry high intensity magnetic
Also, there are some machine variables which play a vital role in concentrating mineral fines. Further, magnetic separation studies of low grade iron ore was carried out by using IRMS and found that a product of maximum of 51.2% Fe can be separated from the low grade ore assaying 35.9% Fe (Tripathy et al., 2014).
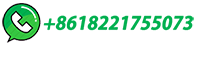
Magnetic Separators
The evolution of high strength permanent rare-earth magnets has led to the development of high-intensity separators that operate virtually energy free. The use of rare-earth magnetic separators for beneficiation of industrial minerals has become the industry standard with literally hundreds of separators placed in recent years.
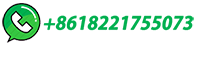
Dry High-Intensity Magnetic Separation In Mineral …
ABSTRACT. High intensity dry magnetic separators are in use for various applications in the mineral as well as coal processing industries. Evaluation of the …
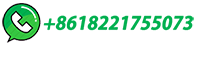
Processing of Ferruginous Chromite Ore by Dry High-Intensity Magnetic …
ABSTRACT Mineral and morphological characteristics of chromite ore strongly affect the separation efficiency while upgrading the low-grade deposits. Usually, chromite ore enrichment is carried out by using gravity separation due to high-concentration criterion between chromite and other minerals. However, chromite ore from Sukinda region, India, is a …
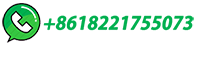
Low-Intensity Magnetic Separation: Principal Stages of a Separator …
Comparative analysis of the mineral phase properties of the magnetic separation feed and its magnetic product has confirmed that wet drum magnetic separators currently used for wet treatment of ...
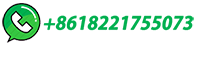
Wet low intensity magnetic separators
Tank design CC and CR CC – Concurrent The concurrent style of magnetic separator features: The counter-rotation style of magnetic separator features: • Feed box with serrated overflow for even distribution of the feed slurry • …
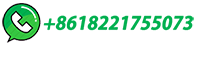
Beneficiation of Low-Grade Hematite Iron Ore …
Present investigation includes the magnetizing roasting of low-grade iron ore fines followed by grinding and beneficiation using magnetic separation. The hematite iron ore used in the investigation contains 53.17% …
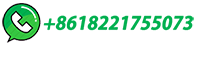
Processing a rare earth mineral deposit using gravity and magnetic
In the context of RE mineral beneficiation, magnetic separation is typically used for two purposes: low intensity magnetic separation is used to remove ferromagnetic gangue minerals such as iron oxides and high intensity magnetic separation is used to separate monazite and xenotime from other heavy minerals (Gupta and Krishnamurthy, 1992).
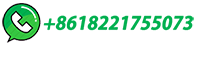
Influence of matrix type on WHIMS performance in the magnetic
Liu et al. (2014) found that the optimum conditions for upgrading their iron ore was a primary grind at 60% passing 75 µm and 1.5 T followed by a secondary grind of the coarse concentrate at 71% passing 44 µm and a magnetic field strength of 1.0 T. A WHIMS RK/CSQ-50 × 70 magnetic separator was used to upgrade their ore from a Fe content of 38% to a final …
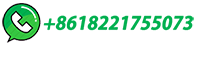
Physical Concentration of Heavy Minerals: A Brief Review on Low …
These magnetic separators were adopted in order to beneficiate HMs in various parts of the separating/processing system or circuit. For instance, dry low-intensity and wet high-intensity magnetic separators can be employed in order to beneficiate ilmenite from HM concentrates, such as Zr-containing minerals, when adopting magnetic concentration.
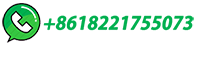
Separation of Iron and Rare Earths from Low‐Intensity …
based on low-intensity magnetic separation incorporated with high-intensity magnetic separation-flotation.[3] This approach focuses on the production of iron ore, with rare earth …
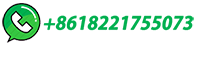
Processing of Lean Iron Ores by Dry High Intensity Magnetic …
Abstract. Dry high intensity magnetic separation (DHIMS) is investigated to process a lean hematite ore. It was found that the feed particle size and the drum rotation …
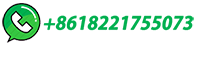
Physical separation of iron ore: magnetic separation
This experiment using a simple process low intensity magnetic separation-high gradient magnetic separation, for the ultimate index for comprehensive grade of iron concentrate is 58.41%, at a total ...
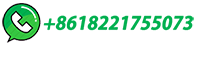
Wet High Intensity Magnetic Separation | Bunting
The electromagnetic laboratory-scale Wet High Intensity Magnetic Separator (WHIMS) removes fine magnetics and para-magnetics from mineral slurries. ... Wedge wire, with a high surface area, for applications such as iron ore processing where a large volume of magnetics are being removed; Expanded metal matrix, with sharp points that generate ...
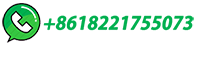
Separation of Iron and Rare Earths from Low‐Intensity …
based on low-intensity magnetic separation incorporated with high-intensity magnetic separation-flotation.[3] This approach focuses on the production of iron ore, with rare earth recovery being an auxiliary part.[4] Currently, the utilization rate of rare earth resources is less than 20 %.[5–7] Consequently, a large
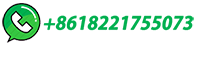
Magnetic separation equipment | Reading range | Mineral …
The Reading Rare Earth Magnetic Drum (RED) uses a unique 5 pole magnetic element to generate a field intensity in excess of 0.7 Tesla on the drum skin. The magnetic element design affords the maximum field gradient and the 5 poles enables additional cleaning of the magnetic stream. This gives a very selective separation at high throughputs compared to alternative …
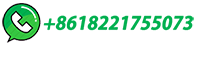
Magnetic Separation
Integrated mechanical separation for municipal solid waste. Zhou Tao, ... Eugene Atta Nyankson, in Resource Recovery Technology for Municipal and Rural Solid Waste, 2023. 6.3.3 Magnetic separation. The magnetic separation of solid waste is a method of separating ferromagnetic substances using the magnetic field generated by the magnetic separation equipment.
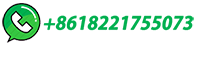
Dry High-Intensity Magnetic Separation In Mineral Industry—A Review …
ABSTRACT. High intensity dry magnetic separators are in use for various applications in the mineral as well as coal processing industries. Evaluation of the performance of these separators treating different minerals has become an active research topic.
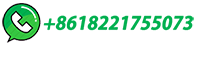
Chapter 2 Magnetic Separation
32 2 Magnetic Separation Fig. 2.2 Classification of magnetic separators from different perspectives [14]. Re-drawn figure Dry low-intensity magnetic separators (DLIMS) are generally employed to: – upgrade iron ores containing relatively large particles and strongly magnetic minerals – separate iron pieces from steel mill slags and blast ...
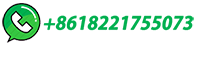
Dynamic behavior and separation prediction of magnetic ore …
1. Introduction. The past decades have witnessed tremendous progress made in the magnetic separation technology that have significantly decreased the industrial grade of mined iron ore (Liu et al., 2020, Zeng et al., 2019).However, the extensive energy consumption and high capital costs required in utilization of low-grade iron ore still render it economic …
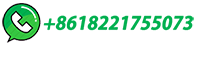
The Use of Flotation and High-Intensity Magnetic Separation …
According to the XRD data, the ore contains minerals of 38.2% quartz, 35.5% albite, 25% microcline and 1.3% mica. The dry high-intensity magnetic separator model MIH (13) 111-5 is depicted in It was used to remove titanium and iron from the feldspar concentrate product produced under the optimum flotation conditions that was mentioned previously.
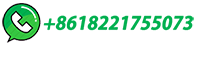
Separations | Free Full-Text | Application of Magnetic Separation
Magnetic separation technology is a physical separation method that uses the differences in magnetism between matter to separate them from each other by different motion behaviors in a non-uniform magnetic field. It is highly efficient, green, and environmentally friendly, with little change in the physical and chemical properties of raw materials. Magnetic …
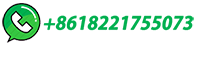
Intensity Magnetic Separator
As shown in Figure 13.2, minerals with ferromagnetic properties have high susceptibility at low applied field strengths and can therefore be concentrated in low intensity (<~0.3 T) magnetic …
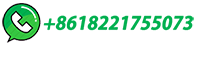
Recovery of Iron Ore Fines and Ultrafines from Tailings …
Most of the existing iron ore beneficiation plants in Australia utilise one or more of the following processes: • classification • gravity separation • low-intensity magnetic separation (LIMS). The most common equipment used in size classification …
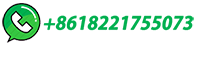
For dry and wet processing Low Intensity Magnetic …
the revolving magnet drum with an internal stationary magnet array. The Low intensity magnetic separators are available in several types for vast number of duties and could be seen a. split …
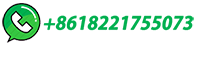
Developments in the physical separation of iron ore: Magnetic …
The SLon is used to continuously beneficiate fine, weakly magnetic minerals of sizes from −1.3 mm down to about 10 µm, and is claimed to have the advantages of a large beneficiation ratio, high ...
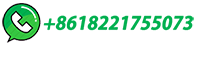
SPECIAL IRON ORE PROCESSING ISSUE Beneficiation of a …
tory low- and high- intensity magnetic separators and a slimes shaking table, respectively. Factors affecting these separation methods are discussed, including process mineralogy on …
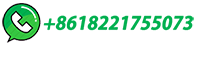
Magnetic Separators
The Davis tube or Davis tube tester is a laboratory machine designed to separate a small sample of pulverized magnetic iron ore into magnetic and non-magnetic fractions. ... a wide variety of materials which do not respond well to traditional methods of processing on low intensity dry drum separators or high intensity induced magnetic roll ...
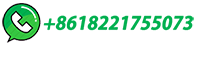