Introduction to Jaw Crushers: Understanding the Basics
Introduction: In the world of material processing and mining, Jaw Crushers stand as stalwart machines, pivotal in breaking down large rocks into more manageable sizes.
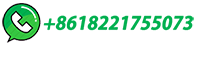
The Ultimate Guide to Stone Crusher Plant Design
Discover the best practices for designing a successful stone crusher plant, including factors to consider, equipment selection and configuration, environmental management, and safety and maintenance priorities. Learn how to optimize crushing operations and minimize environmental impact for efficient and effective production.
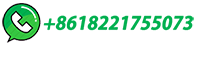
Application guide ® C Series™ jaw crusher …
C SeriesTM jaw crusher basic concepts r. Feed material is crushed between fixed and movable jaw dies. Large particles are rushed in a single layer, referred to as single-layer …
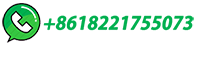
Construction Working and Maintenance of Crushers …
There are four basic ways to reduce size of a material: by impact, by compression, by shear or by attrition. Most crushers employ a combination of all these crushing methods. ... For example, jaw crushers using this method of compression are suitable for reducing extremely hard and abrasive rock. As a mechanical reduction method, compression ...
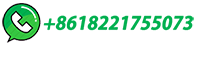
JAW CRUSHER SERIES
Our jaw crushers are of the single-toggle type and feature a deep, symmetrical crushing chamber, a large feed opening for its size, and an ideal nip angle that ofers smooth …
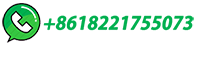
® C Series™ jaw parts
3 Contents C Series™ jaw crusher basic concepts 4 How to operate a C Series™ jaw crusher 6 C Series™ jaw crusher wear parts 8 One- or two-piece jaws 10
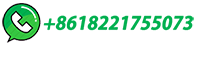
What Are Jaw Crushers and How Do They Work? | Oreflow
There are several other jaw crushers like bulldog jaw crushers and force feed jaw crushers. But for reference, we'll focus on the two most widely-used jaw crushers in the mining industry. Down below we'll discuss how these pieces of equipment operate and what makes them different from each other.
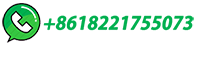
McLanahan | Jaw Crushers
McLanahan's Universal Jaw Crusher produces more spec material at a lower cost per ton and ensures continuous crushing action with less abrasive wear.
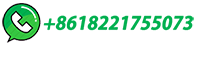
Below the surface: Setting up an underground primary jaw crusher
Jaw crushers are the most common solution in underground applications when the throughput is below 1000 tonnes per hour, depending somewhat on the scalping solutions. Above 1000 tph, primary gyratory crushers are an option. After the throughput reaches 2000 tph, jaw crushers are very rare, with the exception of a parallel plant layout.
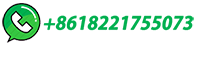
Understanding Jaw Crusher Parts and Their Functions
Learn about the different components of a jaw crusher and their respective functions. This article covers everything you need to know about jaw crusher parts, from the movable jaw to the flywheel.
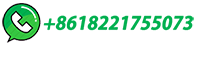
In- depth – Components of a Jaw Crusher | PROPEL …
A jaw crusher consists of Crusher Body Pitman Jaw plate Rear end frame Eccentric shaft The jaw crusher is one of the most admired and most sought after equipment from the house of Propel Industries. For the benefit of newcomers in the industry, here is an explainer of the various components of the Jaw crusher.
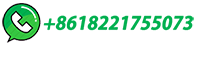
A Detailed Overview of Cone Crushers and What You Need …
In this Cone Crusher article we want to educate you about what to consider when purchasing a cone crusher. It also will inform and educate you if you are a current owner or operator of a Cone Crusher. If you have a good base of knowledge about cone crushers you can skip through the article by choosing the topics below.
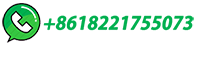
Jaw Crusher: What Is It & How Does It Work?
Learn how a jaw crusher works, what types of jaw crushers are available, and how to use them effectively for your construction projects.
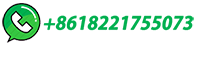
Cone Crusher Diagram: Simplified Guide
Understand cone crusher diagram basics with our comprehensive blog post. Learn about the structure and operation of cone crusher models.
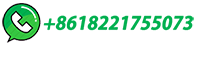
The Complete Guide to Primary Crushing, Secondary …
Learn everything you need to know about primary crushing, secondary crushing, and tertiary crushing in this comprehensive guide. Discover the types of crushers used in each stage, their working principles, and the advantages and disadvantages of each process. Get answers to frequently asked questions and improve your understanding of …
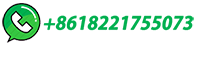
Jaw Crusher: Range, Working Principle, Application
Jaw crushers are used as primary crushers, or the first step in the process of reducing rock. They crush primarily by using compression. The rock is dropped between two rigid pieces of metal, one of which then moves inwards towards the rock, and the rock is crushed because it has a lower breaking point than the opposing metal piece.
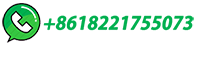
Crushing Plant Design and Layout Considerations
1 Crushing Plant Design and Layout Considerations Ken Boyd, Manager, Material Handling, AMEC Mining & Metals, Vancouver, BC ABSTRACT In mining operations, the layout of crushing plants and ancillary equipment and structures is a
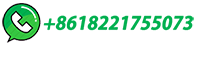
Jaw Crusher Working Principle – StudiousGuy
A jaw crusher mainly works on the principle of reciprocating motion exhibited by the moveable jaw of the jaw crusher. The repeated movement of the jaws results in the development of compression force that further causes the breakdown of the rock or the ore placed between the two jaws into smaller pieces.
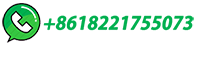
Jaw Crusher Liner Plate Design & Profile Shapes
Straight Jaw Plates: A shows a diagram of a standard type of Blake crusher with regular or straight jaw plates. This type of plate has been the standard from the time of its inception, emulating, in this respect, the straight concaves in the gyratory machine. And it will be noted that the theoretical action in this straight-plate ... ="Jaw Crusher Liner …
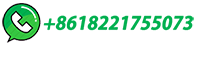
Industrial Solutions Jaw crushers
For these tasks thyssenkrupp Industrial Solutions has in its range two types of jaw crusher, which differ in the kinematics of the swing jaw: single-toggle jaw crushers for a high …
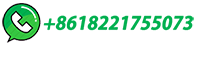
What Is A Jaw Crusher
WHAT ARE THE DIFFERENT TYPES OF JAW CRUSHER? / JAW CRUSHER TYPES. There are two main groups of jaw crushers, categorized according to their jaw movement mechanism. - Single …
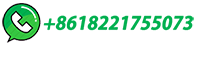
General Electrical Layout Of Crushing & Screening Plant | Crusher …
08-CRUSHER-Crushing Plant Design and Layout Considerations. Crushing plant design should accordingly … or bottom of a crusher plant. Electrical cable tray routing and … in large crushing and screening plants, …
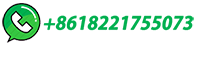
Construction Working and Maintenance of Crushers for …
There are four basic ways to reduce size of a material: by impact, by compression, by shear or by attrition. Most crushers employ a combination of all these crushing methods. ... For example, jaw crushers using this method of compression are suitable for reducing extremely hard and abrasive rock. As a mechanical reduction method, compression ...
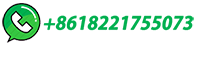
TECHNICAL NOTES 5 CRUSHERS
Schematic diagram of a crusher showingg the open- and closed-side settings. function of size and OSS. Manufacturers publish tables of capacity for their crushers of various …
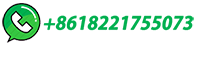
Understanding Types of Jaw Crusher: A Comprehensive …
This smooth operation is exactly why jaw crushers are basic, must-have machines when it comes to mineral processing. To visualize the design, refer to jaw stone crusher: An Easy Guide to Jaw Crusher Diagram.
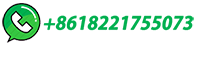
Jaw Crusher PPT RECYLCLE CRUSHING DIAGRAM
Construction Waste Recycling Crushing Plant Diagram,PPT … Construction Waste Recycling Crushing Plant Diagram,PPT, Manufacturers,Sale. … there are generally two crushing equipment, jaw crusher and impact crusher, …
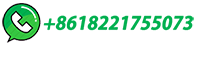
How to Design a Jaw Crusher
The size of a jaw crusher is usually expressed as gape x width. The common crusher types, sizes and their performance is summarized in Table 1.1.Currently, the dimension …
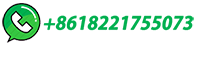
Jaw Crusher Explained
Learn about the Jaw Crusher! How it works, its components, design, advantages, disadvantages and applications.
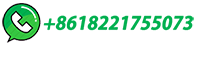
Jaw Crusher Explained
Jaw crushers are sized based upon the dimensions of the top feed inlet ( gape) or the dimensions of the jaws. For example, a 32 x 54 sized jaw crusher will measure 32 …
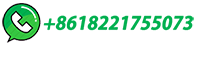
Going underground: Jaws or a primary gyratory?
Above 1,000 tph, primary gyratory crushers begin to look interesting, and after the throughput reaches 2,000 tph, jaw crushers are very rare, with the exception of a parallel plant layout. Capacity is also determined by the feed size and material type introduced to the plant, as well as the required product curve.
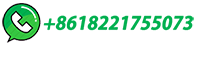