Crushing Plant Design and Layout Considerations
The largest primary gyratory crushers cost US $2 million or more, while overall crushing plant costs can be as high as $18 million. It's necessary therefore to estimate crusher installation costs based on equipment costs plus the following direct costs, including construction contractor indirects: • Earthworks • Mechanical
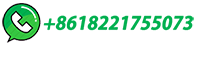
Types of Crushers: What You Need to Know
In 1881, Philetus W. Gates received a U.S. patent for his device featuring the basic ideas of today's gyratory crushers. In 1883 Mr. Blake challenged Mr. Gates to crush 9 cubic yards of stone in a contest to see which crusher would finish the job faster. The Gates crusher completed the task 40 minutes sooner! ... Impactor and hammer mill ...
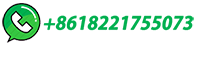
Crushing Plant Flowsheet & Design-Layout
Before the advent of the cone crusher the usual practice was to make a 2-in. product in two steps consisting of a primary breaker of the jaw or gyratory type followed …
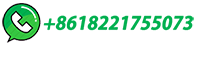
Heavy duty, maintenance-friendly Gyratory Crusher
The Gyratory Crusher "NT" incorporates all of the TC's heavy-duty design features (Heavy Cast-Steel Shell Sections, Forged Main Shaft and Countershaft, Robust Gearing, Generous Lubrication, Long-Life Bronze Components) and focuses on coupling these historical characteristics with updated maintenance-friendly features.
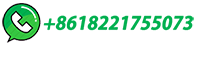
Construction Working and Maintenance of Crushers for …
Gyratory Crushers Gyratory crusher is generally used as a primary crusher. The crusher is popular due to its high throughput capacity and the large sized opening. The crusher is well …
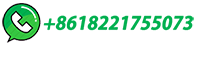
operation of a jaw crusher with a neat diagram
. Contribute to sbmboy/en development by creating an account on GitHub.
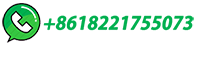
Gyratory Crusher | SpringerLink
Gyratory Crusher. Gyratory crusher is a crushing equipment that uses the gyratory motion of the crushing cone in the conical cavity inside the shell to extrude, bend, …
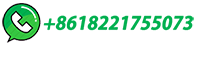
How Does a Jaw Crusher Work
If you are a rock, sand, gravel, or mineral processing industry veteran or an avid reader of our blog, you know that there are several different types and styles of crushing equipment.The exact crushers you need—jaw, cone, impact, or gyratory—will depend on your site, the product you're making, and how much you need to produce.
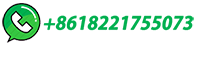
TECHNICAL NOTES 5 CRUSHERS
be accepted into the crusher is approximately 80% of the gape. Jaw crushers are operated to produce a size reduction ratio between 4:1 and 9:1. Gyratory crushers can produce size reduction ratios over a somewhat larger range of 3:1 to 10:1. The primary operating variable available on a crusher is the set and on jaw and gyratory the open-side ...
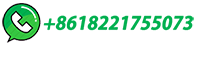
gyratory crusher diagram | Mining & Quarry Plant
Diagram of jaw crusher. Diagram of horizontal shaft impactor crusher. … gyratory, roller or impactor-type crushers depending on the characteristics of the rock.
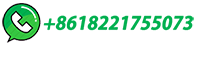
Gyratory Crusher
A gyratory crusher is an ore processing machine that crushes the ore between an eccentrically mounted cone and a crushing throat, that is fixed. In mining, the most important criteria for …
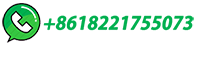
Industrial Solutions Gyratory crushers
The design of our gyratory crushers and jaw gyratory crushers is based on over one hundred years of experience gained by thyssenkrupp in the manufacture of these machines. Changing mining and processing techniques demand, besides new materials and design methods, continuous development of the products.
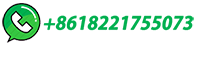
Types of Crushers Explained: Everything You Need …
Gyratory crushers are valued for their high capacity, continuous operation, and ability to process feeds up to 1500 mm in diameter. Unlike jaw crushers, gyratory crushers generally have higher reduction ratios. …
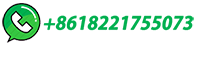
Gyratory VS Jaw Crushers: Advantages
The jaw crusher will handle sticky,'or dirty feed better than the gyratory, there being no diaphragm below the crushing chamber on which such material can pack. Routine maintenance and repair jobs are generally more …
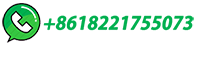
neat digram of gyratory crusher customer case
neat digram of gyratory crusher customer case T11:07:01+00:00 Who we are > Products > Cases > Solutions > Contact Us > Solutions. Copper ore beneficiation plant; Iron Ore Beneficiation Plant; Iron ore powder beneficiation production sand crusher plant; Basalt Crushing Plant in South Africa;
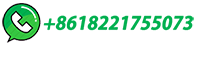
Construction Working and Maintenance of Crushers for …
Gyratory Crushers Gyratory crusher is generally used as a primary crusher. The crusher is popular due to its high throughput capacity and the large sized opening. The crusher is well suited for handling direct feed from haul/dump trucks. The gyratory crusher is mainly used in rock that is abrasive and/or has high compressive strength.
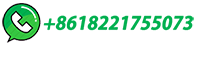
Crusher
The cone crusher (Fig. 13.12) is very similar to the gyratory type, except that it has a much shorter spindle with a larger-diameter crushing surface relative to its vertical dimension. The spindle is not suspended as in the gyratory crusher. The eccentric motion of the inner crushing cone is similar to that of the gyratory crusher.
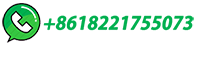
Superior™ MKIII 60-89 primary gyratory crusher
Superior™ MKIII 60-89 primary gyratory crusher fits a wide range of feed opening ranges, and provides great benefits no matter the need. Excellent performance. Thanks to upgraded components, the Superior™ MKIII 60-89 primary gyratory crusher has increased speed and more crushing power.
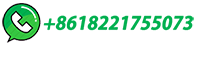
AMIT 135: Lesson 5 Crushing – Mining Mill Operator Training
Diagram of a gyratory crusher [image: 135-5-16)] Gyratory Crushing Action. Designs of the breaking faces vary with manufacturer. As a result, the product size distribution varies. When the feed drops into the crusher, the mantle squeezes the rock against the concave surface.
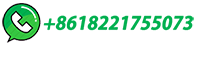
Gyratory Crushers CG800i
CG830i Gyratory crusher : 380 (419) 1,525 (60") 2,700-6,000 (2,980 - 6,610) CG850i Gyratory crushers: 500 (550) 1,549 (61) 3,800-8,250 (4,180 - 9,075) The knowledge hub Over the last 150 years, we've learned a thing or two about crushing and screening. As innovators and experts in the field, we have a deep understanding of technical and ...
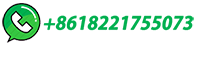
Jaw Gyratory Crusher Pro | FL
Our gyratory crushers are typically driven directly via a disc-pack coupling with a floating shaft and a safety coupling. The disc-pack coupling compensates for geometric misalignments between the motor shaft and the countershaft, while the safety coupling protects the crusher motor from overload when uncrushable tramp material enters the ...
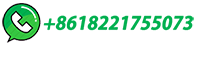
Unveiling the Advantages and Applications of …
Gyratory cone crushers have been in use for over a century, with the first models dating back to the late 1800s. They were initially designed to handle larger feed sizes and higher capacities than jaw crushers, which were …
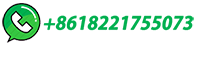
Primary Gyratory Crusher High Performance GY Series
opening. Gyratory crushers can be used for primary or secondary crushing. The crushing action is caused by the closing of the gap between the mantle line (movable) mounted on the central …
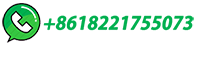
TECHNICAL NOTES 5 CRUSHERS
Figure 5.1 Schematic diagram of a crusher showingg the open- and closed-side settings. 5.1 Jaw and Gyratory Crushers. Jaw and gyratory crushers are used mostly for primary …
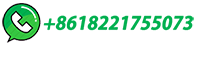
2. GYRATORY CRUSHERS
GYRATORY CRUSHERS The original patent for the gyratory crusher was granted to Phile- tus W. Gates in 1881. This fint crusher was used by the Buffalo Cement Co. At the time these early gyratory crushers were developed all mining and quarrying, either underground or open pit, was done by hand; tonnages generally were small and product ...
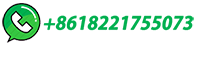
Gyratory Crushers | Mellott
Gyratory crushers are generally more robust than cone crushers and are well equipped to handle larger feed sizes. Gyratory crushers can be divided into two categories: cone and impact gyratory crushers. Cone gyratory crushers are the most common type and are used to crush medium to hard materials. They work by forcing the material to fall ...
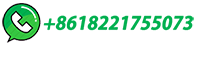
Types of Crushers: What You Need to Know | Machinery …
In 1881, Philetus W. Gates received a U.S. patent for his device featuring the basic ideas of today's gyratory crushers. In 1883 Mr. Blake challenged Mr. Gates to crush 9 cubic yards of stone in a contest to see which crusher would finish the job faster. The Gates crusher completed the task 40 minutes sooner! ... Impactor and hammer mill diagrams
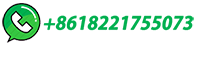
Working Principle of Crushers
Working Principle of Crushers. On left is a showing of the "standard gyratory with straight concaves" is a section through any vertical, radial plane in the crushing chamber of one of the intermediate sizes of the crusher. In order to understand the crushing action in such a chamber it is helpful to consider the process as though each step took place in an orderly, and …
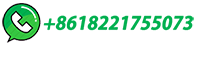
Types of Crushers: What You Need to Know
Gyratory crushers. Run of mine material is transferred into a gyratory crusher's upper-level hopper. The walls of the gyratory crusher's hopper are lined with "V-shaped" pieces, the mantle and the concave, like a jaw crusher but shaped …
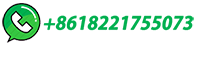
What Are the Differences Between The 7 Types of Crushers?
For gyratory crusher, the outer circle represents the stationary bowl covered by the concave and the inner circle represents the main shaft covered by the mantle. The main shaft rests in the eccentric bushing at the base of the crusher. As the eccentric rotates, the base of the main shaft moves in a circular path around the crusher centerline. ...
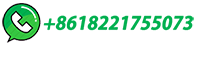