A Guide to Bearing and Drive Components in Rotary Kiln Design
Learn about the critical elements in rotary kiln design, including drive assembly and trunnion rollers. Contact Kiln Technology Company Company for more information.
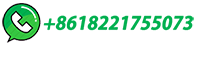
Rotary kiln process: An overview of physical mechanisms, …
The rotary kiln is a slightly inclined steel cylinder that rests on supports (bearing rollers) with an interior lining; it is equipped with a rotating motor that induces a turning motion. ... In 1898, Hurry and Seaman improved the design of rotary kilns; they added a cooler to facilitate grinding and improved the quality of the clinker [5 ...
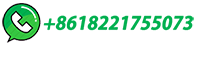
Rotary Kiln Design: Thermal Analysis Part 2
As a high-temperature device, the analysis of a material's thermal properties is the foundation of rotary kiln design. Factors such as a material's specific heat, thermal conductivity, heat transfer properties, and more, will all influence how that material will behave in the kiln, and ultimately, how the kiln will need to be designed to ...
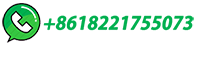
Download our FREE Rotary Kiln Handbook
This handbook gives an overview of the rotary kiln design process, chemical & thermal analysis as well a basic background on rotary kilns & much more.
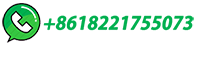
The FEECO Rotary Kiln Handbook
THE ROTARY KILN HANDBOOK FEECO International was founded in 1951 as an engineering and equipment manufacturer. We quickly became known as the material experts, able to solve all sorts of material processing and handling problems,
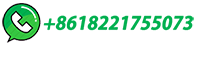
Cement Kilns: Design features of rotary kilns
Despite the challenges of their size and their high temperature, the best examples of rotary kiln rotate on their rollers almost frictionlessly, the power supplied by the drive being …
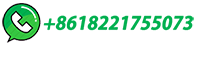
Development of an up-scalable rotary kiln design for the …
A rotary kiln design for a tyre particles mass flow of 20 kg/h, which is representative for experimental or small industrial kilns and therefore can be built at moderate costs, is developed fulfilling these requirements. This design is then successively scaled up by two orders of magnitude to a maximum tyre particle mass flow of 2000 kg/h ...
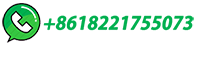
Rotary kiln incinerator
Design and manufacturing of medical, industrial and hazardous rotary kiln incinerators for thermal waste to energy conversion
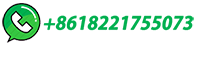
Rotary Kiln – IspatGuru
Rotary kiln sizing and design. Every material is different in terms of how it behaves in the kiln and at what temperatures different reactions are going to occur. When designing a process around a rotary kiln, as well as in the design of the kiln itself, the material is required to undergo thorough chemical and thermal analyses.
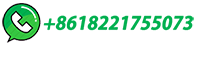
Design of an indirect heat rotary kiln gasifier
Additionally, rotary kiln design and construction is relatively simple and the pertinent technology is established and reliable with industrial applications in the cement and metallurgical industry. However, it has to be mentioned that the current commercial status of rotary kiln technology could offer only an atmospheric indirect heat ...
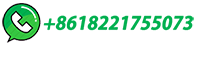
Indirect-fired Rotary Kiln Design – Alpha Thermal Process
Typical Gas-fired Indirect Rotary Kiln Electrically-heated Indirect Rotary Kiln (Harper International, Buffalo, NY) In the forefront of the indirect-fired kiln offering is Harper International, a reliable AlphaThermal collaborator.
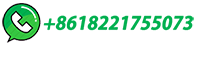
Rotary kiln process: An overview of physical …
Figure 2: Geometric considerations of the rotary kiln design [11] The angle of repose is an intrinsic characteristic of a given material; it depends principally on: particle size, rotational speed of the kiln (Figure 2), and surface condition of the kiln wall.
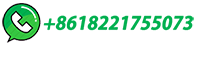
Using rotary kilns for high-temperature bulk solids processing
The rotary kiln is the preferred device for producing catalyst substrates, impregnating carriers with the catalyst component and recovering spent catalysts for reuse. ... The flexible design and processing capabilities of rotary kilns has made them a key tool in modern industry. As technologies advance and industries look for ways to implement ...
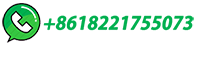
Finch Manufacturing & Technology
Finch Manufacturing & Technology crafts steel components of all sizes for the Rotary Processing industry including Rotary Dryer, Rotary Kiln, Rotary Parts, Thrust Roller, and many other industrial processes. Finch is an ISO 9001:2015 certified company.
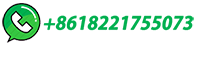
Modeling and simulation of petroleum coke calcination in rotary …
The schematic diagram of the petroleum coke calcination rotary kiln employed in the simulation runs is presented in Fig. 1, and its design specifications are presented in Table 2. The operational parameters of the calcination kiln and the composition of the green coke are presented in Table 3, Table 4, respectively.
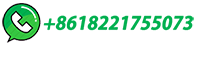
Design and Modeling of Rotary Kiln Technology for …
The design and modeling of rotary kiln technology for pyrolysis processes are critical components of sustainable waste management and renewable energy production. Rotary kilns offer a robust and ...
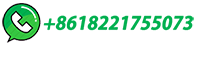
Rotary Kilns
A rotary kiln is a continuous process designed specifically for drying, calcining, processing, or sintering bulk materials.
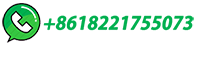
Rotary Kiln
Rotary Kiln - KHD Humboldt Wedag. Can your kiln take the heat? Discover how KHD engineers its rotary kilns for reliable, robust, trouble-free operation - day after day.
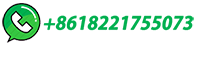
Rotary Dryer Design 101: Flight Design
Proper flight design is a key component in optimizing the efficiency of a rotary dryer, with geometry, pattern, and more influencing overall dryer performance. With decades of drying experience, our team of engineers has a vast knowledge base of materials – experience from which we can often draw to bypass some of the initial testwork other ...
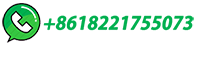
Rotary Dryer Design & Working Principle
Rotary Dryer – Kiln. Of the different types of dryers that there are the most common is the ROTARY DRUM DRYER/Kiln, This type of drier is common not only in the mining industry but you will find them in fertilizer plants, Cement plants, and peat hogs to name but a few.
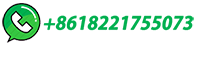
RotarEkiln™
RotarEkiln is an innovative kiln design which uses a more efficient, zero-emission furnace. As the name signifies, RotarEkiln is an electrically powered, indirectly-heated rotary kiln, which doesn't consume fossil fuels.
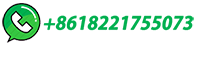
Rotary Kiln Design: Dams
Rotary kilns are integral to modern industrial processing, providing a controlled means of initiating chemical reactions and phase changes. As they are highly flexible and can be used to process hundreds of different materials, optimizing the performance of a rotary kiln around the process and material at hand is an important aspect of kiln design.
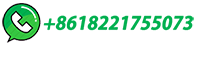
Rotary Kiln Shell Design
Rotary kiln shell has a long development history. Its design technology updates with its developmental needs and the advantages of times.
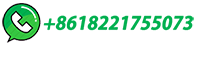
Rotary Kiln Design: Bearing and Drive Components
FEECO's custom rotary kilns are engineered and fabricated to the highest quality for a reliable system that stands the test of time. From choosing the right drive assembly, to …
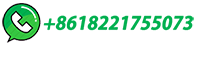
FEECO Rotary Kiln Brochure
testing to scale up the process and design and manufacture a custom rotary kiln for full-scale production. COMPLETE SYSTEM CAPABILITIES In addition to the kiln itself, FEECO can provide a complete system with all necessary support equipment, including: WHO WE WORK WITH Many of the world's most notable companies, across nearly all industries,
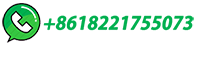
Everything You Need to Know on Rotary Kiln Refractory
Refractory, or the lining utilized on the interior of rotary kilns, is a critical component in ensuring process efficiency and prolonging the life of a rotary kiln.Here, we'll discuss everything you need to know about refractory, including how it works, the different types, and best practices for preventative care.
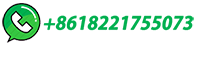
Rotary Kiln
A rotary kiln is a physically large process unit used in cement production where limestone is decomposed into calcium oxide which forms the basis of cement clinker particles …
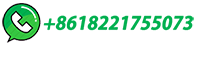
Screw reactors and rotary kilns in biochar production – A …
Screw reactors are the dominant technology in literature. • Rotary kilns offer higher maximum capacities. • External electric heating is the most common energy supply for both technologies.
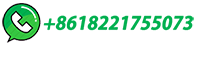
Rotary Kiln Design Important & Formulas.
The Kiln Shell: The shell of the kiln is made of mild steel plate. Mild steel is the only viable material for the purpose, but presents the problem that the maximum temperature of the feed inside ...
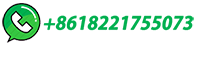
Indirectly heated rotary kiln – for efficient thermal processing
An indirect rotary kiln that keeps sustainability in mind without substituting quality. With a strong demand for the mining industry to adopt a more sustainable method of producing high-quality products, the machinery used must be designed to accommodate this need, while still maintaining a high level of efficiency and productivity.
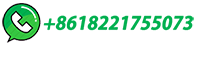