Ironmaking 101 – From Ore to Iron with Blast …
Iron is mainly extracted from hematite (Fe 2 O 3) and magnetite ores. Natural or direct shipping iron ores contain between 50-70% iron and …
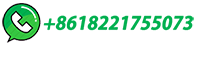
Solving iron ore quality issues for low-carbon steel | IEEFA
BHP – one of the key suppliers of blast furnace-grade iron ore and metallurgical coal to the steel industry – has stated: "There is simply not enough high-quality iron ore suitable for efficient DRI/EAF production to meet the global steel demand." BHP considers that most of the world's steel will still be produced via the blast ...
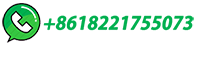
Hopewell Furnace: A Pennsylvania Iron-making Plantation (Teaching …
The splash and creak of the turning water wheel and the swishing roar of the furnace "blast" never stopped. By day, black charcoal dust swirled from the furnace and blanketed the whole village; by night, only a flickering red glow lit the sky. ... hot enough to convert iron ore into iron. In front of the furnace was the cast arch where the ...
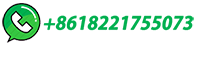
Iron ore pellets for blast furnace
What is iron ore pellet. Iron ore pellets are made by adding a small amount of additives to the fine ore powder (-200 mesh, that is, the ore powder with a particle size of less than 0.074mm accounts for more than 80%, and the specific surface area is more than 1500cm2/g), adding water to the pelletizer, relying on capillary force and mechanical force of …
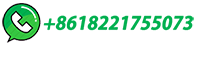
Electric arc furnaces: the technology poised to make British
The purpose of the blast furnace is to separate iron ore extracted from the ground into its component parts: iron and oxygen. A form of carbon, normally coal, combines with the oxygen in the iron ...
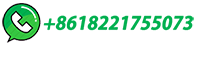
Blast Furnace/Strategies
The method is relatively simple to execute. An inventory consists of a coal bag; goldsmith gauntlets and ice gloves (one pair equipped); 26 gold ore; and 26 mithril, adamantite, or runite ore. Each time a full inventory of gold ore (26) is added to the Blast Furnace, the player will also transport and deposit 26 coal with the coal bag.
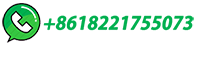
Ironmaking 101 – From Ore to Iron with Smelting and Direct Iron …
Figure 1: Steelmaking byproducts for blast furnace (BF), basic oxygen furnace (BOF) and electric arc furnace (EAF) processes. Source: World Steel Association (worldsteel) The first step in the production of steel or cast iron alloys is the reduction of iron ore—which contains iron oxide and gangue or mineral impurities—to unrefined, reduced iron form.
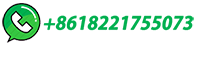
Modeling of iron ore reactions in blast furnace | Request …
The ironmaking blast furnace (BF) is an efficient chemical reactor for producing liquid iron from solid iron ore, where the solids of coke and iron ore are charged in alternative layers and ...
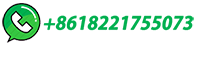
Lesson Explainer: Extracting Iron | Nagwa
Iron metal is usually extracted from a hematite ore, which contains an iron(III) oxide (F e O 2 3) compound.The ore must be treated before it can be placed in a blast furnace, because blast furnaces are usually optimized to burn small …
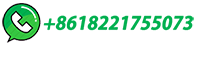
Chemistry of the Ironmaking by Blast Furnace Process
The iron-bearing components in the charge to the furnace are the simple oxides of iron, Fe2O3, and Fe3O4. The natural ore normally are hematite (Fe2O3) or magnetite (Fe3O4). Pellets are principally Fe2O3. Iron ore sinter can range in composition from Fe2O3 and Fe3O4 to fused mixtures containing magnetite, fayalite, 2FeO.SiO2, and di-calcium ...
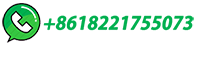
Ironmaking Blast Furnace | SpringerLink
where P is the daily output of ironmaking blast furnace (ton/day and night), ν is the bosh gas volume (m 3 /ton), and χ is the bosh gas volume index, generally 58–66 m/min.. The size ratio of each part of the inner shape of the ironmaking blast furnace is D/d = 1.1–1.2, d 1 /D = 0.62, d 1 /d = 8.7, the shaft angle is 80–81°, and the bosh angle is 74–75°.
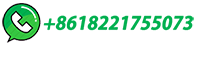
Making iron & steel
Before iron ore can be used, oxygen must be removed from it. Known as 'reducing', this can be done either in the blast furnace, where hot air is injected into a continuous feed of coke, sinter and lime, or by the direct reduced iron (DRI) process. The result from both is liquid iron, which is then transported to the basic oxygen furnace. The blast furnace process also produces two ...
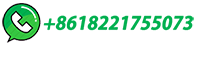
Extraction of Iron from Hematite | CIE IGCSE Chemistry …
Extraction of Iron | Metallurgy | Blast Furnace and …
The purpose of a Blast Furnace is to reduce the concentrated ore chemically to its liquid metal state. A blast furnace is a gigantic, steel stack lined with …
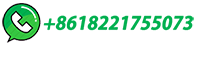
DRI production | International Iron Metallics Association
Direct reduction of iron is the removal of oxygen from iron ore or other iron bearing materials in the solid state, i.e. without melting, as in the blast furnace. The reducing agents are carbon monoxide and hydrogen, coming from reformed natural gas, syngas or coal. Iron ore is used mostly in pellet and/or lumpy form.
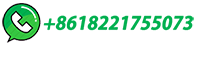
Iron processing | Definition, History, Steps, Uses, & Facts
The blast furnace appeared in Europe in the 15th century when it was realized that cast iron could be used to make one-piece guns with good pressure-retaining properties, but whether its introduction was due to Chinese influence or was an independent development is unknown. At first, the differences between a blast furnace and a Stückofen were slight.
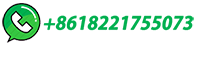
Iron Ore Reactions and Phenomena in a Blast …
Dear Colleagues, Blast furnaces (BF) are still the dominant process for making iron in the world. Blast furnaces are charged with iron ores in the form of pellets, sinter and/or lump ore and metallurgical coke in …
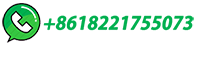
The Blast Furnace: 800 Years of Technology Improvement
The modern world uses shocking amounts of steel. The input requirements for 16th century blast furnaces were large. Though fuel consumption had fallen to roughly the level of the bloomery furnace (initially it used much more fuel than a bloomery), producing a ton of pig iron still required roughly 4.5-5 tons of charcoal, and 5.5-7 tons of iron ore.
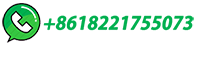
Blast furnace process
In the blast furnace, the iron ore reacts with the carbon contained in the coke to form grey or white pig iron. Combustion process. The iron in the processed ores must be dissolved out by chemical processes. This requires …
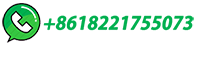
Iron Production
Iron Production. The production of iron from its ore involves an oxidation-reduction reaction carried out in a blast furnace. Iron ore is usually a mixture of iron and vast quantities of …
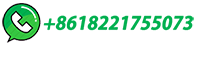
Nassawango Iron Furnace — Furnace Town Historic Site
Nassawango Iron Furnace National Historic Landmark. As you walk up the ramp to the top of the furnace, look at the carts near the ramp base. Imagine them filled with charcoal, bog iron ore and shells, and then pulled up to the top of the ramp. Look in the mirror at the top of the furnace and imagine interior temperatures of 3000 degrees Fahrenheit.
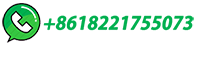
Pig iron
Blast furnace economics are such that larger units have lower unit production costs, hence there has been a trend to bigger and bigger furnaces. Modern blast furnaces produce more than 10,000 tonnes per day. For general information …
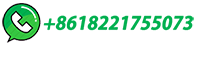
iron and steel
IRON AND STEEL. This page looks at the use of the Blast Furnace in the extraction of iron from iron ore, and the conversion of the raw iron from the furnace into various kinds of steel. The common ores of iron are both iron …
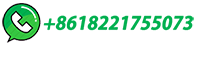
Blast Furnace Process
The term blast furnace comes from the blast of hot air that is blown into the lower part of the furnace at between 1400º to 2100ºF. Molten iron is produced in a blast furnace by the following steps: 1. Charge (solid iron ore, coke, and limestone) is constantly dumped into …
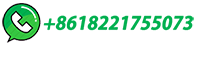
Iron Heritage Trail
The 1731 discovery of superb limonite and goethite iron ore at Salisbury's Ore Hill led to the iron forges of the 1700's and the larger blast furnaces of the 1800's. Ore at Lime Rock, Furnace Village (Lakeville), and East Canaan. …
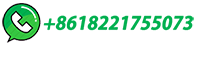
How we make steel
Making iron. In Scunthorpe we have four blast furnaces named after four English queens – Mary, Bess, Anne and Victoria. Coke, iron ore, sinter and limestone are fed – or charged – into the top of the furnaces. A hot air blast of temperatures around 1,000°C is injected at the bottom of the furnace through nozzles called tuyeres.
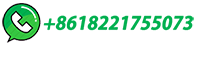
How to make a Blast Furnace in Minecraft
To make a blast furnace, place 5 iron ingot, 1 furnace and 3 smooth stone in the 3x3 crafting grid. When making a blast furnace, it is important that the iron ingot, furnace and smooth stone are placed in the exact pattern as the image …
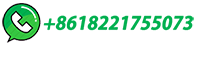
What is steel and how is steel made?
Most steel in Europe is produced via two basic routes: The Blast Furnace-Basic Oxygen Furnace (BF-BOF) route and the Electric Arc Furnace route (EAF). Blast furnaces produce iron from iron ore. In a second step a basic oxygen converter turns iron, with some additions of scrap, into steel. Electric Arc Furnaces produce steel mostly from scrap ...
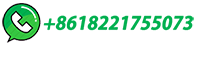
Steel Production
The blast furnace is the first step in producing steel from iron oxides. The first blast furnaces appeared in the 14th century and produced one ton per day. Even though equipment is improved and higher production rates can be achieved, the processes inside the blast furnace remain the same. The blast furnace uses coke, iron ore and limestone to ...
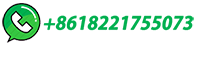
Iron processing
Iron processing - Smelting, Refining, Alloying: The primary objective of iron making is to release iron from chemical combination with oxygen, and, since the blast furnace is much the most efficient process, it receives the most attention here. Alternative methods known as direct reduction are used in over a score of countries, but less than 5 percent of iron is made this way.
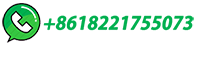
Can electric furnaces be used for steel production from ore?
In a traditional blast furnace, you use carbon not only as something to burn to get heat, but also as a chemical reactant. Simplifying the chemical process involved 1, ... So, while it's obviously possible to get the iron ore hot with an electric furnace, you still need to add something to absorb the oxygen being released from the iron ore ...
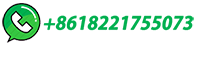