Tin Metallurgy | SpringerLink
Tin ore has very low grade (tin content 0.005–1.7%), so it needs to experience mineral processing to generate the concentrate with tin content 40–70%. Gravity separation is the main process for tin ore mineral processing. There are other physical processes such as flotation and leaching.
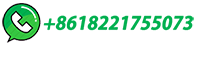
An integrated process for the recovery of tungsten and tin …
An integrated process comprising of physical beneficiation and chemical extraction was developed for a wolframite-scheelitecassiterite ore from Kyrgyzstan, yielding 80% and 90% recovery of ...
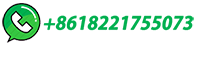
ANALYSIS AND PROPOSED CHANGES OF TIN ORE …
Tbk. Currently tin ore processing system in KIP produces high grade tin ore (±70% Sn). By applying high grade tin ore processing system in KIP, recovery of tin ore is low and associated minerals of tin contained in concentrates secondary jig will be wasted.
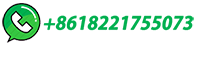
Tin Recovery
Tin recovery processes are diverse, and depend on the product from which tin is being recovered and the desired end product. In the past, tin recovery from waste has been overlooked due to the metal making up a very small proportion of consumer waste. ... in Belgium. The new plant will process copper anode sludge using a hydrometallurgical ...
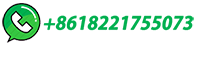
Tin Ore Mining Process
Flowchart Explanation. The raw ore is fed into the trommel screen for washing a few little clays and can separate the gravel or stone which needs to crush&grind to get the inside tin, the separated gravel can transfer to the next jaw crusher by the belt conveyor. After the jaw crusher, goes to a cone crusher for second crushing.The output from the cone crusher goes to a …
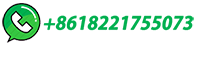
20TPH Alluvial & Rock Tin Ore Process Plant In Zimbabwe
JXSC has equipped a complete 20TPH Tin Ore Processing Plant for Zimbabwean customers with a recovery rate of 95%. Skip to content. JXSC Machinery. Email Us [email protected] +86- . Tel or WhatsApp Chat . Home; ... JXSC has developed a complete set of tin ore process plant equipment lines based on customer needs. The following is the ...
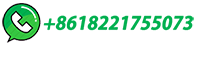
Recovery of strategically important critical minerals from …
The total global reserve of Co is estimated to be around 7.1 million tons, of which the DRC holds the largest reserve of 3.6 million tons [55].Australia has the second largest reserve of Co, but it only produced 4971 tons in 2020 [55].The global production of Co was 140 kt in 2020 and the DRC produced highest 68% of Co [3].Co is primarily produced as a by-product of …
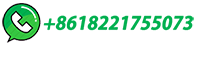
(PDF) Extraction and Separation of Tin from Tin-Bearing …
The proven global tin reserves were reported to be approximately 4.7 million tons (Mts) in 2016, and among these resources, only approximately 2.2 Mts can be recovered economically.
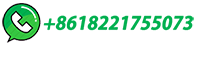
Prospects for Return of Valuable Components Lost in …
Despite a satisfactory supply of explored mineral reserves, the non-ferrous metal mineral resource base faces problems. The percentage of metals in ore concentration tailings (average and maximum values) are as follows: tin — 35% and 58%; tungsten — 30% and 50%; zinc — 26% and 47%; lead — 23% and 39%; molybdenum — 19% and 53%; copper — 13% …
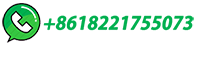
Tin Ore Processing Plant
Tin (Cassiterite) ore processing refers to the process of extracting tin from ore. Gravity separation, magnetic separation and flotation are mainly used to grade tin concentrate and remove other impurities. In order to achieve high efficient, low …
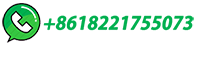
Novel Process for Tin Recovery from Waste Print Circuit …
World tin ore reserves have been exhausted gradually during the past two decades. The exploitation of primary tin ores (mostly lean-grade ores of tin) was insufficient ... Novel Process for Tin Recovery from Waste Print Circuit Boards … 17. Fig. 2. G. θ T –T diagram and saturated vapor pressure diagram of WPCBs during the oxidation
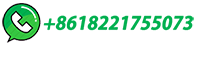
Tin Ore Extraction
The flowsheet below Explains the Extraction of Tin Ore as shown by a study adapted to the concentration of a lode tin deposit.Cassiterite (SnO2) is very friable and special considerations to crushing and grinding of …
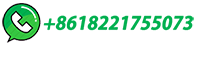
What are the commonly used tin processing methods?
Tin ore is traditionally beneficiated mainly through gravity means, especially for placer tin ore, and jig machines are generally used for preliminary enrichment. Sometimes in order to improve the recovery rate of fine-grained tin ore, a shaking table is also used.
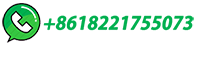
Tin (Sn) Ore | Minerals, Occurrence, Formation, Deposits
Tin ore is a type of mineral ore that contains tin, a soft, malleable, silvery-white metal. Tin is commonly used in various applications, including as a coating for other metals to prevent corrosion, in the production of solders, as a component in electronics, and in the manufacturing of tin cans. Tin ore is typically found in rocks and minerals, often in association …
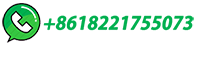
Tin Ore Extraction
The flowsheet below Explains the Extraction of Tin Ore as shown by a study adapted to the concentration of a lode tin deposit.Cassiterite (SnO2) is very friable and special considerations to crushing and grinding of the ore are necessary to avoid an excessive production of fines. The Mineral Jig is an important feature of this flowsheet to recover the coarse free tin …
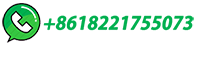
Tin Ore Beneficiation Methods And Some Practice
United beneficiation processing for tin ore. There are one of our customer use all those three beneficiation method on their tin ore processing flow. ... and the flotation of sulfide ore adopts the priority mixing and flotation separation process, and the recovery rates of tin, lead, antimony and zinc are 78.11% and 85.59% respectively., 82.63 ...
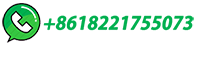
What is a theoretical grade-recovery curve? An example.
The theoretical grade-recovery curve for an ore is a definition of the maximum expected recovery by flotation of a mineral or element at a given grade. This is defined by the surface area liberation of the value minerals and is consequently directly related to the grind size utilised in the process. The theoretical grade-recovery can be readily used to quickly identify …
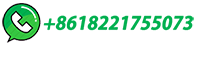
Tin Processing
To participate in the 911Metallurgist Forums, be sure to JOIN & LOGIN; Use Add New Topic to ask a New Question/Discussion about Mineral Processing or Laboratory Work.; OR Select a Topic that Interests you.; Use Add Reply = to Reply/Participate in a Topic/Discussion (most frequent). Using Add Reply allows you to Attach Images or PDF files and provide a more …
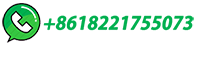
(PDF) Evaluation of Efficiency of Using Mechanized Processing
Rwanda is known to be among the top producers of tin and tantalum, despite having low recovery and grades. This study was carried out to evaluate the efficiency of using mechanized methods to ...
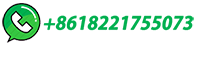
Tin ore processing | Commodities | Mineral …
Recovery of tin bearing minerals from hard rock deposits involves multiple processing stages. Mineral Technologies can aid the processing of historical tin tailings by designing a suitable gravity circuit comprising spirals and wet …
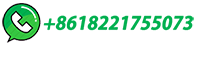
Formation of tin ore deposits: A reassessment
About 85% of all historically mined tin of about 27 million tonnes Sn is from a few tin ore provinces within larger granite belts. These are, in decreasing importance, Southeast Asia (Indonesia ...
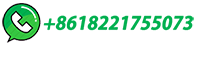
Extraction of Tin From Its Ore
Introduction of extraction of tin from its ore. Rock Tin ore is one of the metals that mankind first discovered. In the early days, our ancestors' innovative extraction of tin from its ore, used tin, copper and lead to produce bronzes.Tin and tin alloys have been widely used in modern national defense, modern industry, advanced science and technology and human life because of the …
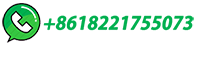
Tin Metallurgy | SpringerLink
Tin ore has very low grade (tin content 0.005–1.7%), so it needs to experience mineral processing to generate the concentrate with tin content 40–70%. Gravity separation …
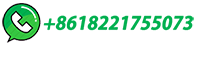
Novel Process for Tin Recovery from Waste Print Circuit
World tin ore reserves have been exhausted gradually during the past two decades. The exploitation of primary tin ores (mostly lean-grade ores of tin) was insufficient for refined tin production. ... B., Li, Q., Zhang, Y. (2024). Novel Process for Tin Recovery from Waste Print Circuit Boards (WPCBs) by Selective Oxidation Roasting Under H 2 O ...
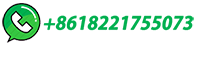
Minerals | Special Issue : Advances in Ore …
The results were compared to the results obtained by artisanal processing techniques. The proposed mechanized techniques were found to increase the efficiency of tin and tantalum recovery from 60.75% to 81.85% and from …
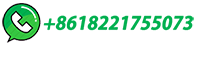
Beneficiation of cassiterite from primary tin ores using …
PDF | Alluvial tin ore deposit of PT. Timah is predicted to be depleted in the next 5 to 10 years. ... A Value-Added Multistage Utilization Process for the Gradient-Recovery of Tin and Iron and ...
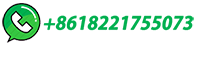
Arsenic Removal from Arsenopyrite-Bearing Iron Ore and Arsenic Recovery
In most cases, arsenic is an unfavorable element in metallurgical processes. The mechanism of arsenic removal was investigated through roasting experiments performed on arsenopyrite-bearing iron ore. Thermodynamic calculation of arsenic recovery was carried out by FactSage 7.0 software (Thermfact/CRCT, Montreal, Canada; GTT-Technologies, Ahern, …
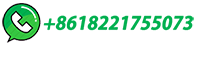
Improving recovery in the processing of hard rock tin ores
491 Improving recovery in the processing of hard rock tin ores S.T. Hall+ and B.A. Wills* + University of Nottingham, Nottingham, England *Camborne School of Mines, Redruth, Cornwall, England ABSTRACT Fines losses in the treatment of hard rock tin ores, such as those found in Cornwall, England, are notoriously high, sometimes accounting for more than 20% of …
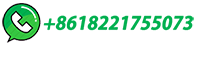
Improving recovery in the processing of hard rock tin ores
491 Improving recovery in the processing of hard rock tin ores S.T. Hall+ and B.A. Wills* + University of Nottingham, Nottingham, England *Camborne School of Mines, Redruth, …
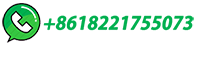