From Ore to Alloy: Navigating Ironmaking in Modern Steel …
In this process, iron ore, coke (a form of carbon), and limestone are fed into the furnace, where intense heat and chemical reactions extract molten iron. Innovations in blast furnace technology, including hot blast systems, oxygen enrichment, and refractory materials, have significantly improved productivity and environmental performance. ...
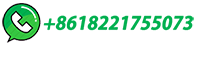
Full article: Iron ore processing
Iron ore processing. This special issue of Mineral Processing and Extractive Metallurgy presents a selection of the best metallurgy papers delivered at the very successful …
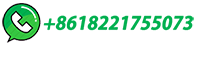
23.3: Metallurgy of Iron and Steel
Originally, the iron was collected in pools called pigs, which is the origin of the name pig iron. Figure (PageIndex{1}): A Blast Furnace for Converting Iron Oxides to Iron Metal. (a) The furnace is charged with alternating layers of iron ore (largely Fe 2 O 3) and a mixture of coke (C) and limestone (CaCO 3). Blasting hot air into the ...
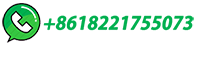
Sintering: A Step Between Mining Iron Ore and Steelmaking
World resources are estimated to be greater than 800 billion tons of crude ore containing more than 230 billion tons of iron. The only source of primary iron is iron ore, but before all that iron ore can be turned into steel, it must go through the sintering process. Sinter is the primary feed material for making iron and steel in a blast furnace.
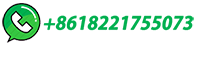
From Ore to Iron with Smelting and Direct Iron …
Smelting Reduction. Figure 2: The smelt reduction vessel (SRV) is the core technology component of the Hismelt process. Source: RioTinto …
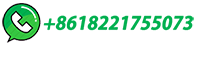
Iron Ore – Minecraft Wiki
Iron ore is a mineral block found underground. It is a source of raw iron, which can be smelted into iron ingots. Deepslate iron ore is a variant of iron ore that can generate in deepslate and tuff blobs. Iron ore itself can be obtained by …
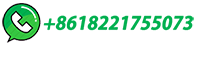
Iron Ore: Mineralogy, Processing and Environmental …
Iron Ore: Mineralogy, Processing and Environmental Sustainability, Second Edition covers all aspects surrounding the second most important commodity behind oil. As an essential input for the production of crude steel, iron ore feeds the world's largest trillion-dollar-a-year metal market and is the backbone of the global infrastructure. The book explores new ore …
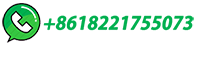
Iron processing
Iron processing - Smelting, Refining, Alloying: The primary objective of iron making is to release iron from chemical combination with oxygen, and, since the blast furnace is much the most efficient process, it receives the most attention here. Alternative methods known as direct reduction are used in over a score of countries, but less than 5 percent of iron is made this way.
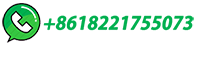
Mining separation and sorting equipment for processes in the mining
Since our founding, STEINERT has been a pioneer in mechanical mining separation and processing, e.g. ore sorting equipment. As a leading global manufacturer of advanced sorting and magnet-based systems, we are continually developing new high-tech solutions to meet the challenges of our customers: when it is necessary to protect equipment from ...
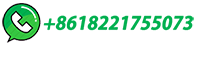
Iron Ore production in the Pilbara
Activities involved in finding, mining and processing iron ore at our Pilbara operations have been simplified in the following diagram. Rio Tinto operates 11 iron ore mines in the Pilbara and the specific sequence of activities varies from mine to mine. Excellence in planning, scheduling and quality control are fundamental to the process.
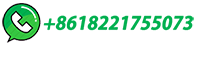
The six main steps of iron ore processing
Iron Ore Processing: From Extraction to …
Iron ore processing is a crucial step in the production of steel, one of the most essential materials in modern society. Iron ore, a naturally occurring mineral composed primarily of iron oxides, is mined and processed …
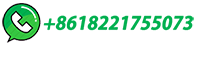
Direct reduced iron process
The reduction gases only dissolve oxygen from the iron ores. This causes the iron ores to crack on the surface. The appearance resembles a porous sponge, which is why the deoxidized and thus strongly ferrous iron ore is also called sponge iron. Sponge iron is a highly ferrous ore from the direct reduced iron process!
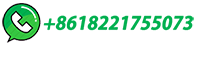
Iron ore beneficiation | Commodities | Mineral Technologies
The world's largest producers rely on Mineral Technologies for iron ore processing solutions. DOWNLOAD. From Canada's Labrador Trough region, across India, Brazil and Africa, to Australia's iron rich Pilbara, our teams deliver unrivalled expertise in fine iron ore beneficiation. ... Our latest iron ore equipment range. HC33 (High Capacity ...
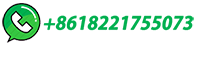
Iron Ore
Our expertise extends to conveying, stockpiling and stacking; loading and unloading; shiploading; and sampling systems. Add in our advanced knowledge of iron-ore processing, ore behavior, and modeling design tools, and our clients get the most efficient and value-engineered bulk-materials handling solutions. Ore slurry, tailings, and water ...
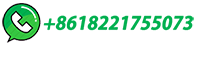
Full article: Iron ore processing
This special issue of Mineral Processing and Extractive Metallurgy presents a selection of the best metallurgy papers delivered at the very successful international 'Iron Ore 2015' conference held at the Perth Convention and Exhibition Centre, Australia, on 10–12 July 2015. This was the seventh in the series of biennial conferences featuring recent …
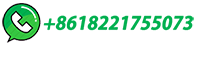
Iron Ore Processing, General | SpringerLink
Iron ore handling, which may account for 20–50% of the total delivered cost of raw materials, covers the processes of transportation, storage, feeding, and washing of the ore en route to or during its various stages of treatment in the mill.. Since the physical state of iron ores in situ may range from friable, or even sandy materials, to monolithic deposits with hardness of …
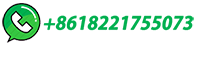
Iron Ore Sintering: Process: Mineral Processing and …
Sintering is a thermal agglomeration process that is applied to a mixture of iron ore fines, recycled ironmaking products, fluxes, slag-forming agents, and solid fuel (coke). The purpose of the sintering process is manufacturing a product with the suitable characteristics (thermal, mechanical, physical and chemical) to be fed to the blast furnace.
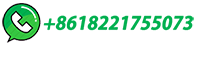
Iron Ore Processing | Home
Narvik is situated at the Ofotfjord, north of the Arctic Circle, and has an average annual temperature of around 4° C. Thanks to these temperatures, which are influenced by the Gulf Stream, the fjord remains free of ice almost all year round.This is where the processing plant of Scandinavia's biggest iron ore producer is located, with a facility for direct loading of iron ore …
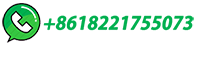
Iron Ore Processing
Iron Ore Dressing. The iron ore dressing process is aimed at the processing of iron ore materials, which is divided into crushing and screening, grinding and classification, separation, and dehydration.Crushing and screening refers to the crushing and screening of iron ore to ensure that the particle size of crushed ore can provide ore that meets the requirements of …
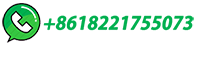
Wet High Intensity Magnetic Separators | Multotec
Our engineers and metallurgists will help you process minerals faster and more efficiently. Full range of process equipment to optimise your mineral processing plant. Large stockholdings & fast delivery of equipment and spares to support your plant . 24-hour field services, technical and maintenance support. Metallurgical & engineering support
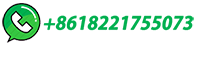
Iron Ore Beneficiation Plant Equipment For …
Jig machine: processing 30 (2)~0.5mm coarse iron ore; Shaking table: separating 2~0.037mm fine iron ore particles; Spiral chute: processing 0.1-0.37mm iron ore with low mud content. 4. Iron ore dewatering …
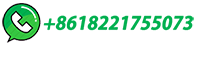
How to process iron ore
Iron ore is an iron-rich ore used primarily in steel manufacturing and infrastructure construction. It has a high iron content and a variety of mineral forms and is a key raw material for the steel industry and is also used to make machinery, electronic equipment and other products.
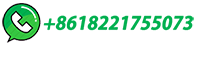
From Ore to Alloy: Navigating Ironmaking in …
Conclusion. Ironmaking remains a cornerstone of modern steel production, blending centuries-old techniques with cutting-edge innovations. From ore processing to alloy design, the journey of iron through blast furnaces, direct …
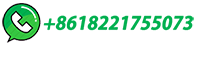
Top 6 Steps Of Iron Ore Processing
Visit our Australian Mining Product and Services to see what our professionals are equipped with to help you in your processing iron ore journey or what other services we can offer. Alternatively, call us on 1300 241 620 to …
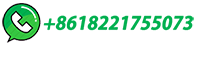
Iron processing
Iron processing - Ores, Smelting, Refining: Iron ores occur in igneous, metamorphic (transformed), or sedimentary rocks in a variety of geologic environments. Most are sedimentary, but many have been changed by weathering, and so their precise origin is difficult to determine. The most widely distributed iron-bearing minerals are oxides, and iron ores consist mainly of …
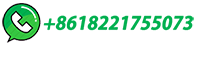
Copper Ore Processing And Equipment
Copper ore processing equipment is an excellent and efficient piece of equipment that can improve the value of copper ore. The equipment includes a jaw crusher, ball mill, classifier, magnetic separator, flotation machine, thickener, and dryer. It comprises leading equipment such as a feeder, hoist, and conveyor to form a complete beneficiation production …
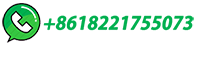
Iron Ore Processing Equipment
A Brazilian iron ore producer has purchased six modular Niagara XL-Class banana vibrating screens for its iron ore processing plant. The 12- by 32-foot, exciter-driven vibrating screens were specifically designed to process 900 …
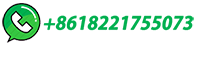
Beneficiation of Iron Ores – IspatGuru
Fig 3 Types of processing ores. The wet processing (Fig 4) is normally practiced for low / medium grade (60 % Fe to 63 % Fe) hematite iron ore. The wet process consists of multi-stage crushing followed by different stages of washing in the form of scrubbing and / or screening, and classification etc., but the advantage is only partial removal of adhered alumina …
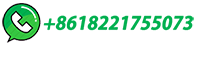
Iron Ore Processing Equipment
Our heavy-duty iron ore balling drums are relied on by some of the industry's top producers to process iron ore fines into pellets for the steelmaking process. The use of a disc pelletizer is a popular alternative approach to pelletizing iron ore fines, as this offers more control over pellet size and produces a more refined pellet product.
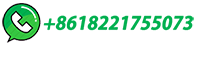
Advancing Iron Ore Beneficiation: Exploring Cutting-Edge
The evolution of iron ore beneficiation process technology underscores the industry's commitment to innovation and sustainability, driving continuous improvement in ore processing efficiency and ...
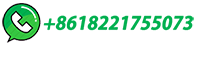