CHAPTER-7 GRAVITY CONCENTRATION OF IRON ORE
CHAPTER-7 GRAVITY CONCENTRATION OF IRON ORE R. K. Rath and R. Singh INTRODUCTION Gravity concentration process is the oldest beneficiation method known to mankind.
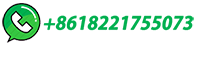
A new method for gravity separation: Vibrating table gravity
In this work, a novel process consisting of calcining-slaking followed by gravity separation for the enrichment of niobium (Nb) and titanium (Ti) from carbonatite pyrochlore ore was proposed, validated and compared with …
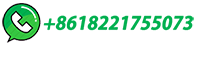
ADVANCES IN MAGNETIC SEPARATION OF ORES
I compares iron analyses of several crude and bene- ficiated ceramic raw materials that undergo dry magnetic separation. Dry Magnetic Separation of Iron Ore: There are many inherent advantages in processes that utilize dry magnetic separation to beneficiate iron ore. Wet concentration of magnetite ore, in comparison, re-
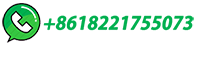
Gravity separation of ultra-fine iron ore in the REFLUX
The iron ore feed had a head grade of 35 wt-% Fe T. At a low feed solids mass flux of 1.5 t m −2 h −1, the REFLUX™ Classifier produced high-grade products at a high recovery. Overall a grade of 66.1 wt-% Fe T with Fe recovery of 80 wt-% could be achieved in a single-stage separation. Within ...
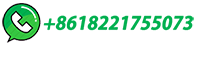
Iron processing | Definition, History, Steps, Uses, & Facts
Iron Ore Processing: From Extraction to Manufacturing
WEBIron ore processing is a crucial step in the production of steel, one of the most essential materials in modern society. Iron ore, a naturally occurring mineral …
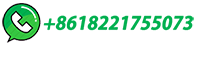
A critical review on metallurgical recovery of iron from iron …
The chemical and physical properties of iron ore tailings are comprehensively examined in this review, and various beneficiation and metallurgical recovery techniques …
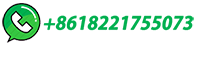
Dry beneficiation of iron ore
Falling prices for iron ore with lower quality than 60 % Fe have led increasingly to the design of iron ore beneficiation lines. General problems of water scarcity and risks with tailings dams have led to the focus shifting to dry beneficiation technologies.
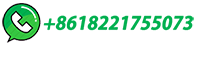
Separating Mixtures | Methods & Examples
The iron in the ore sticks to the magnetic roller while the impurities fall off. Manual Separation The separation of some heterogeneous mixtures can be accomplished by manual separation methods.
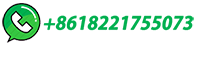
Magnetic Separation | SpringerLink
Magnetic separation is widely used. All materials with magnetism in the magnetic field can be treated by magnetic separation, which is the main method to treat iron ore.
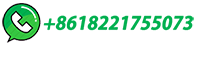
Why Is Iron Ore Valuable? Behind the Scenes of Production …
Learn about the extraction and production process of crude iron ore, along with which countries mine and store the most. See what experts say.
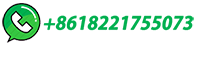
Electrostatic Separation Equipment | Mineral Technologies
Used for the separation of titaniferous mineral sands, hard rock ilmenite and rutile, cassiterite, chromite, tantalite, wolframite and iron ore. Access our electrostatic separator equipment datasheets here.
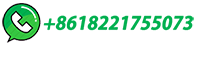
1 Froth Flotation – Fundamental Principles
Froth flotation is a highly versatile method for physically separating particles based on ... removing silicate minerals from iron ores; separating phosphate minerals from ... the ore is not weighed and only assays will be available. However, it is possible to express the ...
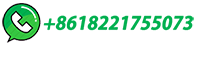
sbm/sbm products from iron ore seperation.md at master
You can not select more than 25 topics Topics must start with a letter or number, can include dashes ('-') and can be up to 35 characters long.
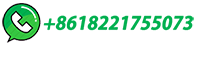
Iron Ore Flotation Process: The Journey from Ore to …
The iron ore flotation process, as an important part of modern mining, is an important means to effectively separate iron ore from raw ore…
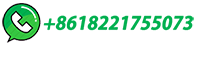
A critical review on metallurgical recovery of iron from iron ore
Iron ore tailings (IOTs) are by-products generated during the beneficiation process of iron mining, encompassing stages such as gravity separation, magnetic separation, and flotation. ... This process is advantageous for separating iron from complex solutions with multiple metal ions due to the specificity of the extractants used. …
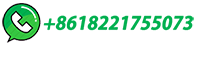
Iron processing
The partially reduced ore is then smelted in the second unit, and liquid iron is produced. Smelting-reduction technology enables a wide range of coals to be used for iron …
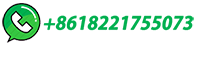
A systematic review of sustainable gold extraction from …
In general terms, ore sorting is the process, based on analysed characteristics determined by on-line sensors, of separating bulk feed material into two or more products (Cutmore et al., 1997; Von Ketelhodt, 2009).
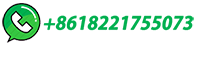
Magnetic Separation and Iron Ore Beneficiation …
Magnetic separation methods are used to take the advantage of the difference in the magnetic properties for separating iron ore from the non-magnetic associated gangue materials. Magnetic separation …
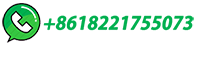
Magnetic separation for recovering iron resources from acid …
Recovering iron from acid-leaching tailings of laterite nickel ore by mineral phase transformation. • Reduce the inventory of hazardous waste while recycling iron resources.
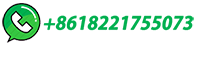
Magnetic Separation: Principles, Devices, and Applications
With the increasing decline in ore quality and the increasing demand for high-quality raw materials, such magnetic separation technologies with higher separation performance are inevitably required by industry, and they include the scaling-up of current magnetic separators to meet the demand for larger-scale and lower-cost exploitation of …
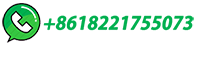
Iron Extraction and Purification / Steel | ChemKey
Iron Extraction and Purification / Steel This page looks at the use of the blast furnace in the extraction of iron from iron ore, and the conversion of the raw iron from the furnace …
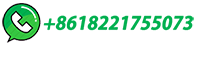
Magnetic Fluid Separation | SpringerLink
It can be used for the separation of nonferrous and precious metal ore (tin, lead, and gold ore, etc.), ferrous metal ore (iron, manganese ore, etc.), coal, and nonmetallic ore (diamond, potassium salts, etc.). In rock-mineral identification, magnetic fluid can replace dense liquid to separate mineral particles.
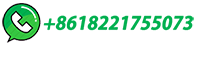
(PDF) Separation and recovery of iron from a low-grade …
In this study, a process of magnetizing roasting followed by low-intensity magnetic separation (MR-LMS), which is used to separate and recover iron from a low-grade carbonate-bearing iron ore ...
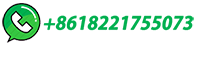
Electric Separation | SpringerLink
The method is also used for the separation of gold and gangue mineral, iron ore, chrome ore, manganese ore, and gangue mineral, quartz, feldspar, graphite, diamond, apatite, asbestos, and gangue mineral among nonmetallic minerals, tantalum niobite, monazite, and zirconite, and the electric separation of fly ash.
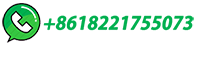
Types of magnetic separators: classification, application
Induction on the separator working surface from 50 to 300 mT. It is used in equipment for recovery of coarse inclusions with ferromagnetic properties in the process of iron separation, as well as for the production of iron ore concentrates during beneficiation of magnetite ores, metal concentrates in processing of ferrous metal slags, scrap metal.
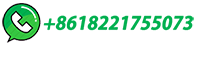
Gravity separation and Ore Beneficiation – IspatGuru
The 'concentration criteria' (CC) gives an idea of the amenability of separation of two ore particles and can be expressed by (Dh-Df)/(Dg-Df) where Dh is the specific gravity of heavier component of the ore, Df is the specific gravity of the fluid medium, and Dg is the specific gravity of the lighter component of the ore.
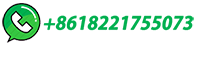
DMS Mining Process, Equipment
DMS(dense medium separation) is an efficient and widely used technique, especially useful for separating valuable minerals with relatively high gangue densities.It is often used in the processing of diamond, coal and various base metal ores.. The mineral DMS process enables the mining industry to increase overall recovery efficiency by concentrating …
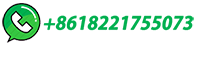
Developments in the physical separation of iron ore: …
This chapter introduces the principle of how low-grade iron ores are upgraded to high-quality iron ore concentrates by magnetic separation. Magnetite is the most magnetic of all the naturally occurring minerals on earth, so low-intensity magnetic separators are used to upgrade magnetite ores.
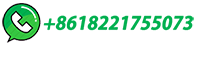
Different types of separation methods for minerals
For best Mineral processing with dry separation equipment, ST Equipment & Technology is a leader in minerals separation industry in Needham.
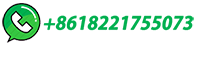
Mineral processing | Metallurgy, Crushing & Grinding
Mineral processing, art of treating crude ores and mineral products in order to separate the valuable minerals from the waste rock, or gangue. It is the first process that most ores undergo after mining in order to provide a more concentrated material for the procedures of extractive metallurgy.
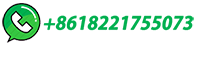