Cement Plant: The Manufacturing Process 4 5
Cement Plant: The Manufacturing Process. 4 The kiln feed is blasted in a 5 The clinker is mixed cement kiln at a temperature with additives, such of 1450oC, causing clinkering as gypsum, and then. 2 The limestone is to occur (small balls of up to ground in a cement …
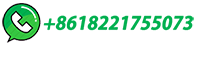
Cement Manufacturing Process
CEMENT MANUFACTURING PROCESS PHASES. Production of cement completes after passing of raw materials from the following six phases. These are; Raw …
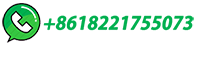
Key factors in setting up a cement plant
Shalini Chauhan Negi, Pankaj Sood and Deven Parti of Holtec Consulting explain the process of setting up a greenfield integrated cement plant, which is generally coined as an integrated unit (IU) in common industry parlance. All other types of cement manufacturing plants are essentially a subset of an IU itself. Cement industry is a part […]
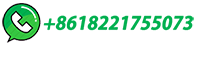
How Cement is Made
While each cement plant may differ in layout, equipment, and appearance, the general process of manufacturing portland cement is the same: crushed limestone and sand are mixed with ground clay, shale, iron ore, fly ash and alternative raw materials.
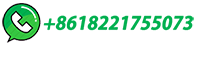
Cement Manufacturing—Technology, Practice, and …
A cement manufacturing process is well suited for co-processing of wastes from different sources. Wastes need to be converted into alternative fuels and raw materials (AFRs) through the pre-processing operation and then utilized to substitute fossil fuels and raw materials used in the cement process.
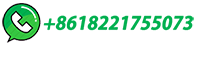
IELTS Diagram: Model Answer Band Score 9
They both have the same techniques, the same layout, the same language, the same linking devices – everything is the same. IELTS Diagram Model Answer. The diagram below shows the stages and equipment used in the cement-making process, and how cement is used to produce concrete for building purposes.
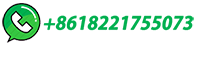
Cement Production Process | Cement Manufacturing Process | AGICO CEMENT
How much do you know about cement production process? A full cement production process includes the cement crushing process, raw mill process, clinker process, and cement grinding process, cement …
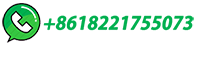
Cement Manufacturing Process
With proper layout, all storages for raw materials can be operated as blending storages with varying efficiency. ... Development of the continuous silo concept started with the introduction of raw material preblending systems in the cement process out of the need to reduce power consumption for cement raw meal homogenization. The increasing ...
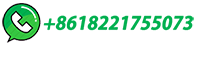
How Cement is Made
The cement manufacturing process is a complex one involving several steps. Each step in the process plays an important role in the overall quality of the finished product. In this article, we will describe how cement is made with …
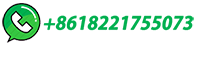
Schematic layout of a typical cement plant.
Download scientific diagram | Schematic layout of a typical cement plant. from publication: Energetic assessment of a precalcining rotary kiln in a cement plant using process simulator and neural ...
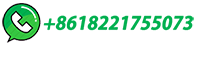
How Cement is Made
Concrete is made by mixing cement with aggregate (sand, gravel, and water), which forms a paste that hardens over time. Cement is necessary to give the concrete its …
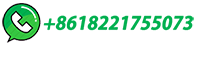
Kiln Process Outline
Kiln Process 2 Course Content 1. Raw material design and chemistry 1.1. Introduction 1.1.1.Chemical requirements for Portland Cement 1.1.2.Cement types
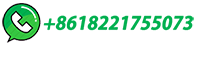
How To Lay a Foundation (2024 Guide)
Step 1: Establish the Layout. Carefully review the construction plans or blueprint for your project. Once the site is level and properly prepared, do a physical walkthrough of the foundation footprint. ... Use a concrete vibrator during the pouring process. Step 2: Smooth and Level. Use a screed board to smooth the surface as it …
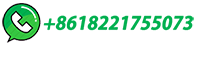
READY MIXED CONCRETE PROCESS
1. READY MEXED CONCRETE PROCESS RMC. Ready mixed concrete process (R.M.C.) is the fresh concrete mix, which is produced by weigh-batching ready mix concrete manufacturing plant. under complete quality control and delivered duly mixed to the site of placement by truck-mounted agitators or dumpers.
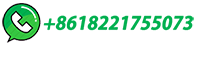
(PDF) Handbook for Desinging Cement Plants
Handbook for Desinging Cement Plants - Deolalkar. Pablo CA. See Full PDF Download PDF. See Full PDF Download PDF. Related Papers. Cement plant operation handbook. jorge pinedo sanchez. Download Free PDF View PDF. Production of Cement. Engr Sajid Chaudhary. Download Free PDF View PDF.
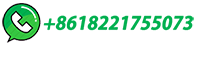
Pyroprocessing and Kiln Operation
Dr SB Hegde, Professor, Jain University, Bangalore, talks about pyroprocessing and the role of preheater, rotary kiln and clinker cooler in the cement manufacturing process. In the concluding part of the two-part series, we will learn more about the various factors aiding pyroprocessing. False Air in Pyro ProcessingIndia is the …
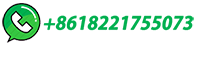
8 Tips For Cement Plant Design | Cement Manufacturing …
We give some tips for cement plant design, including cement site selection, mineral selection, raw material prehomogenizing, grinding station design, calcination …
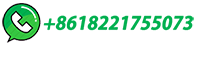
Paving a Patio: How to Lay Pavers for a DIY Patio
Paving a patio with DIY patio pavers lets you build your own outdoor room. Learn how to lay pavers and get patio paving ideas to customize the space.
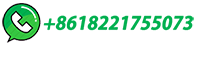
APPLICATION GUIDE
design, layout, use, maintenance, and special applications. The United States consists of many regions, some with unique requirements and regulations; ... The manufacturing process for fiber-cement has virtually remained the same for over 100 years; only the ingredients used have changed over time.
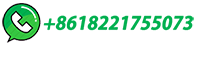
Chapter 4 Cement Manufacturing and Process Control
4.1 Cement Manufacturing: Basic Process and Operation. al operational process of a cement plant in depth. It is necessary to know the conditions prevailing in different …
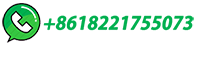
Cement Manufacturing Process
The production of cement is started from quarrying the raw material. The main raw materials are limestone, basalt, sand stone, pumice, gypsum. Site Exploration of …
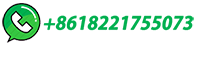
Cement plant design under EPC contract
The modern cement industry uses dozens of types of equipment for clinker production, drying, crushing, grinding, mixing, packaging and other manufacturing processes. A high-quality design is critical for smooth, cost-effective production. The correct layout of a cement plant must provide an optimal balance between all production processes.
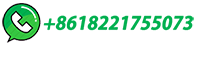
PPC Cement: Meaning, Types, Manufacturing Process, …
Discover the world of PPC cement with our in-depth guide! Learn about the setting time, full form, and types of PPC cement, along with its uses and advantages.
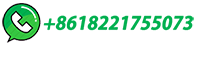
All About Building foundation layout plan and process
By following the proper steps in the foundation layout process, such as site analysis, soil testing, and choosing the right foundation type, the risk of future problems can be minimized. This article has provided an overview of all the key aspects of building foundation layout and process that are crucial for a successful construction project.
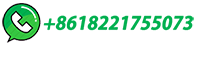
A practical guide to improving cement manufacturing …
The cement production process There are 4 stages of cement production that help maintain consistent raw material quality with minimal chemistry deviation, from quarry to …
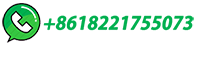
A comprehensive review on Advanced Process Control of cement …
The heating process in the cement kiln requires intense energy to heat the clinker and compensate for the heating loss. Studies illustrate a significant loss of energy (> 50 %) in cement kilns, as shown in Fig. 2 [4].Thus, there is a need for optimal design and efficient operation of the cement kiln to minimise this energy loss.
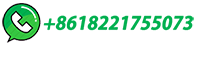
Process location and layout decisions
Site Layout. The process units and buildings need to be arranged in such a way that allows for the most economical flow of materials and people.
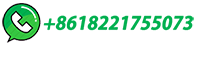
RCC Column Construction Process
RCC column construction process: 1. Column layout work 2. Column reinforcement work 3. Column formwork 4. Pouring concrete
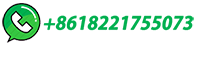
How Cement is Made
Cement is manufactured through a closely controlled chemical combination of calcium, silicon, aluminum, iron and other ingredients. Common materials used to manufacture …
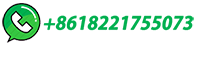
All about the Wet Process of Cement Manufacturing
Cement production in cement plants can be divided into cement wet process and cement dry process. The wet process of cement manufacturing has the characteristics of simple operation, low dust content in production processes.
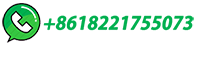