PROCESS BRIEF
Sintering process is developed mainly to utilize under size of lump ore called iron ore fines; which otherwise, could not be charged directly in blast furnace. In order to conserve these, otherwise waste material, they are compacted together and made into lumps by a process known as sintering.Sintering is defined as the agglomeration of the ...
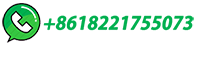
Iron Ore Sintering Process & Equipment in Steel …
Sinter is the primary feed material for making iron in a blast furnace. According to the U.S. Environmental Protection Agency, the sintering process converts fine-sized raw materials, including iron ore, coke breeze, limestone, mill scale, and flue dust, into an agglomerated product, sinter, of suitable size for charging into the blast furnace.
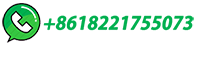
SAFETY GUIDELINES FOR IRON & STEEL SECTOR …
Sintering process is developed mainly to utilize under size of lump ore called iron ore fines; which otherwise, could not be charged directly in blast furnace. In order to conserve these, otherwise waste material, they are compacted together and made into lumps by a process known as sintering. Sintering is defined as
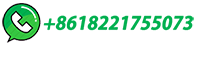
Basics of Iron Ore Sintering
In iron making process, sintering of iron ore fines is an integral step to utilize not only the ore fines but also to introduce a part of flux (limestone and dolomite) …
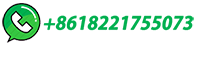
New Measurement Techniques Describing the Sinter Process
Steel making using the integrated blast furnace (BF) process route is still the dominant steel production method covering 70% of worldwide steel production and iron ore sintering is one of the most important iron sources within this process, which represent 70–80% of charged iron-bearing materials into modern BF [].Inside this route, sinter …
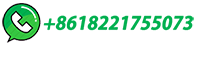
Reduction of Iron Ore Pellets, Sinter, and Lump Ore under …
A blast furnace (BF) is the dominant process for making iron in the world. The BF is charged with metallurgical coke and iron burden materials including iron ore pellets, sinter, and lump ore. Whil...
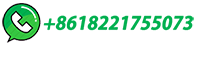
Mineralogical Aspects of Reducing Lump Iron Ore, Pellets, and Sinter …
Iron ore, pellets, and sinter were reduced with hydrogen at 800 °C to understand the degree of reduction and the mineralogical aspects. The weight loss of goethite and limonite iron ore was noticed to be lower than that of magnetite and hematite varieties. ... Recent trends in this field are hydrogen injection into the blast furnace, …
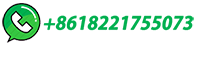
Sintering: A Step Between Mining Iron Ore and …
According to the U.S. Environmental Protection Agency, the sintering process converts fine-sized raw materials, including iron ore, coke breeze, limestone, mill scale, and flue dust, into an agglomerated …
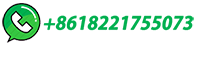
The Sintering Process of Iron Ore Fines – IspatGuru
The process of sintering is basically a pre-treatment process step during iron making for the production of the charge material called sinter for the blast furnace from iron ore fines and also from metallurgical wastes (collected dusts, sludge and mill scale etc.).
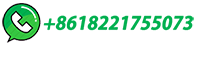
Recent advances in iron ore sintering
Sintering is the most economic and widely used agglomeration process to prepare iron ore fines for blast furnace use. Owing to the depleting reserves of traditional …
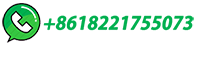
Iron ore sintering
Like other sintering processes, iron ore sintering converts iron ore fines of often −8 mm in size into larger agglomerates, namely sinter, between 5 and 50 mm in particle size, which possess the physical and metallurgical characteristics as well as gas permeability required for efficient blast furnace operation.
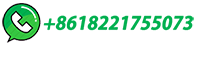
Sintering and Briquetting Synergy in Blast Furnace Smelting
The article describes the concept of partially replacing the sinter in a blast furnace charge with extrusion briquettes to form the basis for sintering and briquetting synergy.
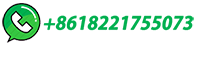
Iron processing
Iron processing - Ores, Smelting, Refining: Iron ores occur in igneous, metamorphic (transformed), or sedimentary rocks in a variety of geologic environments. Most are sedimentary, but many have been changed by weathering, and so their precise origin is difficult to determine. The most widely distributed iron-bearing minerals are oxides, and …
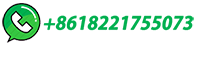
Ironmaking 101 – From Ore to Iron with Blast Furnaces
Iron is made by reacting iron ore (iron oxide and impurities), coke (a reductant) and limestone (CaCO 3) in a blast furnace. Iron ores with lower iron content …
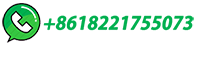
How we make steel
Coke, iron ore, sinter and limestone are fed – or charged – into the top of the furnaces. A hot air blast of temperatures around 1,000°C is injected at the bottom of the furnace through nozzles called tuyeres.
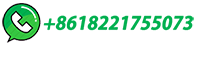
Iron ore sintering
Sintering is the most economic and widely used agglomeration process to prepare iron ore fines for blast furnace use. Compared with pellets, production of sinter …
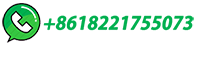
Iron Ore Sintering | SpringerLink
Iron ore sintering is the iron ore powder agglomeration process that changes fine iron ore powder into the lumpy iron-bearing raw material used for blast furnace ironmaking. High-temperature process and addition of alkaline flux will improve metallurgical performance of iron-bearing raw material.
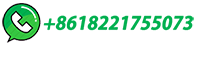
Effect of FeO concentration in sinter iron ore on …
cessing changes ore into fine ore, which cannot be directly used as a raw material for blast furnaces, but it can be used as raw material for pellets or sintered iron ore, hereinafter re-ferred to as sinter. Sinter accounts for approximately 73% of iron ore charged in blast furnaces in Japan [6], and it is cru-
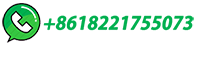
Basics of Iron Ore Sintering | SpringerLink
In iron making process, sintering of iron ore fines is an integral step to utilize not only the ore fines but also to introduce a part of flux (limestone and dolomite) along with the sinter in blast furnace burden. In this way, the productivity of the furnace...
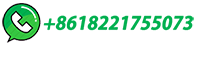
Iron Ore Sinter
Sintering is the most economic and widely used agglomeration process to prepare iron ore fines for blast furnace use. Compared with pellets, production of sinter is cheaper, …
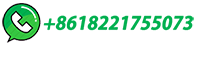
Iron Ore Sintering: Process: Mineral Processing and …
Sintering is a thermal agglomeration process that is applied to a mixture of iron ore fines, recycled ironmaking products, fluxes, slag-forming agents, and solid fuel (coke). The purpose of the sintering process is manufacturing a product with the suitable characteristics (thermal, mechanical, physical and chemical) to be fed to the blast furnace.
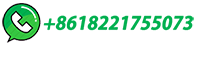
Investigating the Effect of the Iron Ore Pellet Addition on …
The efficient operation of a blast furnace requires burden materials with high softening temperatures and a narrow softening–melting range. This leads to the formation of a thinner cohesive zone in the lower part of the furnace, which improves permeability. In this study, softening–melting tests were conducted on pellets with different levels of …
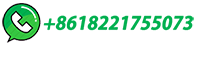
Chemical composition of sinter and iron ore | Download Table
Download Table | Chemical composition of sinter and iron ore from publication: Assessment of blast furnace behaviour through softening–melting test | Blast furnace operation is a complex ...
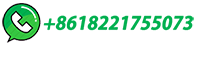
Iron Ore Pelletizing Process: An Overview | IntechOpen
The main used reduction reactors are the blast furnace (BF) and direct reduction reactors (DR). In the blast furnace, iron is reduced and melted and the most common product is liquid iron called hot metal. ... The high temperature phase is divided into three steps: pre-heating, firing, and after-firing. ... Fahidy T. Solid state sintering in ...
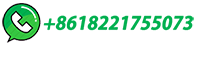
Enhancement of Iron Ore Sinter Reducibility through Coke Oven …
Request PDF | Enhancement of Iron Ore Sinter Reducibility through Coke Oven Gas Injection into the Modern Blast Furnace | Energy network within the integrated steel works should be used more ...
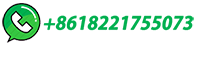
Sintering and Briquetting Synergy in Blast Furnace Smelting
The article describes the concept of partially replacing the sinter in a blast furnace charge with extrusion briquettes to form the basis for sintering and briquetting synergy. The comparability criteria for sinter and extrusion briquette (brex) properties and production parameters were analyzed along with a substantiation of the fundamental …
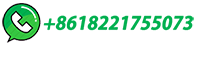
Application of deep learning in iron ore sintering process: a …
In the wake of the era of big data, the techniques of deep learning have become an essential research direction in the machine learning field and are beginning to be applied in the steel industry. The sintering process is an extremely complex industrial scene. As the main process of the blast furnace ironmaking industry, it has great …
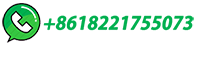
(PDF) Impact of Sinter Basicity and Alumina on Softening …
The chemical composition of iron ore fines, particularly alumina, sinter basicity and sinter MgO together with the thermal conditions that sinter blends are subjected to play an important role in ...
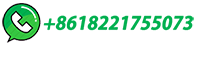
Improved iron-ore sinter for blast furnaces | Steel in Translation
Technology has been developed for the production of fluxed local sinter and pellets with residual carbon for blast-furnace use. The new products have better metallurgical characteristics than existing materials.
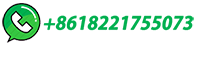
Steel Manufacturing | Sintering Process | Blast Furnace Process
Blast Furnace Process. These raw materials like sinter or iron ore and coke meet each other at the blast furnace, where they are fed into the top of the furnace and some limestone. A hot air blast from which the furnace gets its name is injected through nozzles called tuyeres in the furnace's base. This blast raises the temperature in the ...
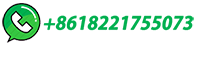