Mineral dressing (= Orebeneficiation)
Mineral dressing (= Orebeneficiation) The first process most ores undergo after they leave the mine is mineral dressing (processing), also called ore preparation, milling, and ore dressing or ore beneficiation. Ore dressing is a process of mechanically separating the grains of ore minerals from the gangue minerals, to produce a concentrate ...
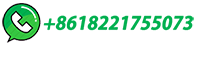
Gold Extraction Methods From Three Types of Ore
The methods of extracting gold from quartz vein ore, sulfide ore, polymetallic gold-bearing ore, gravity separation, flotation, and cyanidation can all …
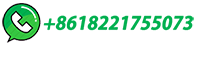
The Importance Of Two Treatment Methods When Tin Ore …
Pretreatment and tailings reprocessing when tin ore flotation is essential to optimize the efficiency and effectiveness of the flotation process.
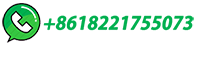
Fluorite Ore Flotation Methods & Influencing Factors
Fluorite is a non-metallic raw material with strategic significance, mainly used in the three major industries of metallurgy, chemical industry and building materials, followed by light industry, optics, sculpture and national defense industry. In production practice, the beneficiation methods of fluorite ore mainly include hand separation, …
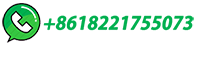
Copper Ore Processing Plants, Flow And Equipment
Copper industrial minerals include: natural copper, chalcopyrite, chalcocite, tetrahedrite, azurite, malachite, etc. Chalcopyrite (a compound of copper, sulfur, and iron) is mined mainly, followed by chalcocite and bornite. If copper ore wants to be fully utilized, it must be processed by flotation. Flotation separation is an important copper ore …
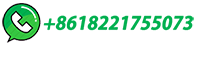
Iron Ore Processing
Due to differences in ore properties, different processes and equipment are used in iron ore dressing, but most iron ore processing processes need to go through the following stages. The large iron ore is fed into the jaw crusher by the vibrating feeder through the silo for preliminary crushing. After reaching a certain particle size, it enters ...
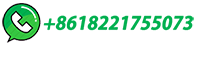
Silver Ore Flotation Process, Equipment
Silver-bearing ores are mainly divided into gold-silver ores and lead-zinc-copper-associated silver ores.Their silver production accounts for more than 99% of the total output. Taking the independent silver mine mainly producing silver as an example, its beneficiation method usually adopts silver ore flotation process.
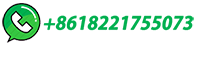
Sulfide Ore Processing
This sulfide rock ore processing plant suitable for separating sulfide rock gold, copper, silver, zinc, lead, fluorite ore, etc.. Usually can reach about 85-90% depending on material conditions. We support custom sulfide ore processing plant and equipment to max your mineral recovery rate.
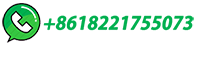
Research on Beneficiation and Reprocessing of Gold Tailings
It can be seen from the above process application and analysis that the ore samples existing in the tailings of gold beneficiation are processed by the spiral chute, and the combination of the two technologies of strong magnetic and shaking table technology can effectively obtain the content of iron and sulfur.
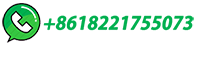
How to Process Gold Ore? 4 Gold Processing Steps
The gold processing line mainly includes four steps: crushing and screening, grinding and classification, separation and tailings processing.
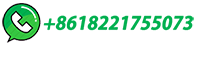
Ore
Ore is a deposit in Earth's crust of one or more valuable minerals. The most valuable ore deposits contain metals crucial to industry and trade, like copper, gold, and iron.
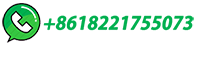
Three Methods To Antimony Ore Beneficiation And Processing
Three methods to beneficiation antimony ore: hand separation, gravity separation, flotation separation, JXSC custom antimony ore flotation plant.
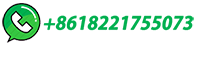
Iron Ore Processing
Due to differences in ore properties, different processes and equipment are used in iron ore dressing, but most iron ore processing processes need to go through the following …
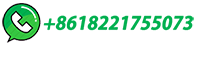
Four Points To Improve Tin Ore Flotation …
Note that these four points include pH value, particle-bubble interaction, metal ions and flotation reagents to help you improve the recovery rate of tin ore flotation.
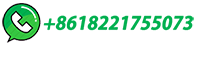
Molybdenum Ore Beneficiation Process Technology
Common molybdenum ores mainly include single molybdenite, molybdenum-containing polymetallic ore and high oxidation rate molybdenum ore.Different molybdenum ore types have different grades and properties, which also determines their beneficiation methods are also different.
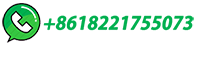
The Processing of Copper Ore Beneficiation
In the development and utilization of copper resources, the grading operation of the copper ore beneficiation plant is also an important production link in the separation of copper ore. As the difficulty of copper mining and sorting increases, the requirements for screening efficiency and classification efficiency are getting higher and higher. …
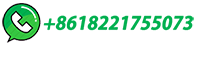
How to Remove Harmful Materials on Ore Handling Stage
Ore entering the mill from the mine (run-of-mine ore) normally contains a small proportion of material that is potentially harmful to the mill equipment and processes. For example, In the crushing stage, large pieces of iron and steel broken off from mine machinery can jam in the crushers and even cause damage to the crusher machines.
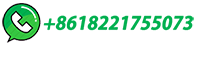
Tungsten Ore Processing Plant
Among them, the raw ore is 150mm, with a grade of 2-5%, and the tungsten ore processing equipment provided by JXSC can reach more than 65%. The following are the main processes and equipment: (1). Crushing & grinding: The jaw crusher initially crushes the mining ore and the hammer crusher for fine crushing. After the crushing to reasonable ...
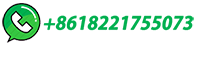
Treatment And Utilization Of Gold Mine Tailings
The gold mining process involves crushing the ore into sand and dust to liberate and recover the gold. What's leftover is called tailings. Ballarat Gold Mine uses its robust management and monitoring processes to make sure its produced gold tailings comply with all license conditions and permits necessary for the safe storage of tailings.
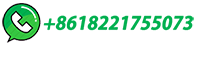
Difference Of Metallurgical And Chemical Grade Fluorite Ore
The beneficiation methods of fluorite ore are mainly gravity beneficiation, flotation and hand selection. ... The equipment used in flotation of fluorite ore mainly includes crushers, ... The process flow design and mining equipment configuration of the fluorite ore dressing plant need to be designed according to the actual situation.
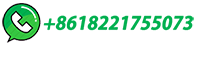
Three gravity separation methods of gold ore dressing
The ore feeding granularity range of the shaking table gold dressing is generally 3mm-0.019mm, the gold dressing is stable and reliable, the ore belt distribution is clearly visible, the rich ore ratio is higher than other ore dressing methods, easy to manage, and the ore required can be separated at one time. 3. Gold selection by Spiral chute
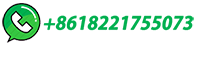
Iron Ore Beneficiation Plant
Iron ore beneficiation process including ilmenite, magnetite, limonite etc ore processing plants and equipment as per customer's needs.
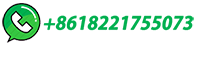
gold and gold ore iron ore dressing corp
Contribute to lbsid/en development by creating an account on GitHub.
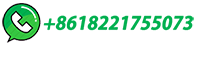
Gold Processing Plant, Equipment
Crushing & grinding: The content of gold in the ore is extremely low. To extract gold, gold ore processing equipment crushes and grinds the ore and adopts ore dressing methods …
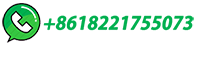
Iron ore washing process and equipment | LZZG
The commonly used method of ore dressing in iron ore washing plants is gravity separation. ... including sawtooth jigs, side-acting jigs, and sine wave jigs. For the selection of placer gold, after long-term practice summary, the trapezoidal jig machine has outstanding advantages in the selection of placer gold, because the entire working ...
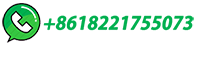
Three Types Of Vanadium Ore Beneficiation Methods
The beneficiation of this kind of ore generally uses weak magnetic separation to separate the vanadium iron concentrate, and then uses the combined method of gravity separation, strong magnetic separation, flotation and electric separation. Recovery of ilmenite from tailings and pyrite by flotation.
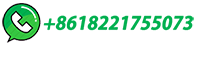
Microsoft PowerPoint
Ore dressing is a process of mechanically separating the grains of ore minerals from the gangue minerals, to produce a concentrate (enriched portion) containing most of the ore …
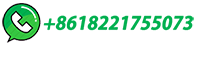
Three Refractory Molybdenum Ore Types And Beneficiation Methods
The beneficiation methods of the three refractory molybdenum ores are mainly flotation, leaching and other combined processes.
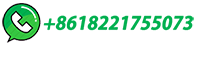
The six main steps of iron ore processing
Learn about the key stages in iron ore processing, including crushing, screening, and beneficiation techniques for optimal resource utilization.
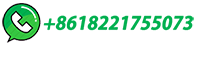
Fluorite Flotation Process, Equipment
The main component of fluorite (fluorspar) is CaF2, fluorite ore process mainly includes gravity separation and flotation.. The type of fluorite ore, the embedded particle size, and the ore properties are different. We support customizing the fluorite processing plant and equipment according to the situation and ore properties.
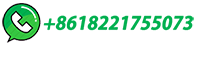