Mining Technologies Eccentric roll crushers ERC
Consequently, the crushing gap between the roll and the jaw in the crusher housing changes constantly and the feed material which has not been screened out is continuously crushed between the roll and the jaw as it falls by gravitation until the product exits the crushing chamber at the bottom.
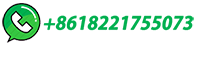
Roll Crushers
Progress in Roll-Crushing. BY C. Q. Payne, New York, N. Y. On the right, a Roll Crushers is shown in a sectional elevation of the A-C single-roll crusher while here below is a cutaway view of the machine, with hopper and part of the near side frame removed to show the crushing chamber. The moving elements of the machine consist of the roll, with its supporting shaft and …
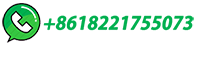
Crusher Reduction Ratio
I have mentioned the fact that, as the % of voids in the crushing chamber decreases, the production of fines by attrition increases. This is like saying that, as the Crusher Reduction Ratio in any given crusher is increased, the % of fines in the product will increase, even though the discharge setting remains unchanged. Both of these statements ...
Difference between Double and Single Toggle …
That said, Double Toggle Jaw Crushers have been hugely successful in the past. They offer a better operational economy as compared to Single Toggle Jaw Crushers. The jaw plate consumption is less by almost 4 …
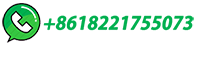
The Advantages and Applications of Double Roll Crushers in …
This article explores the benefits and uses of double roll crushers in the mining industry. It provides an in-depth analysis of the components, operating principles, and various applications of double roll crushers. Additionally, it compares the advantages and limitations of double roll crushers with other types of crushers commonly used in mining operations.
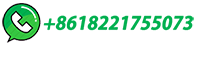
J50 Jaw Crusher
With 1270mm (50") x 735mm (29") single toggle jaw (the widest jaw in its class), the J50 places International at the fore of portable crushing machinery. J50 Jaw Crusher Maximum productivity is delivered through the enhancements to the jaw box including heavier flywheels and optimization for all crushing applications.
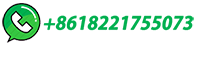
Mechanical Operations Questions and Answers – Crushing …
Explanation: The capacity of a roll crusher is 3 to 300 T/hr and the roll speed ranges from 50 to 300 revolution per minute. Sanfoundry Global Education & Learning Series – Mechanical Operations. To practice all areas of Mechanical Operations, here is complete set of 1000+ Multiple Choice Questions and Answers .
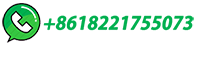
Design, Fabrication and Testing of a Double Roll Crusher
by the secondary crusher. Examples of crushers include jaw crusher, gyratory crusher and roll crusher. A double roll crusher consists of two rolls. Crushing takes place between two cylindrical rolls with each rotating about a concentric horizontal shaft in opposite directions. This is the most common of all roll crushers.
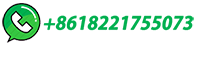
Crushing Products Size and Shape -What to …
I have made a number of general remarks regarding the character of product delivered by crushers of various types, and under different conditions of operation. Generalities are of value only if we have some standard to which …
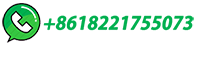
Factors to Consider When Selecting the Proper Roll Crusher …
Some materials are considered too hard for Roll Crushers and may need to be tackled by a Jaw, ... which allows the larger feed sizes to be readily grabbed in the large throat opening between the top (primary) roll and crushing plate. If the feed-to-product-size can be accomplished with 4:1 and 4:1 ratios then a Quad Roll crusher can be ...
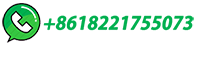
How Does a Jaw Crusher Work? A Simple Guide
The choice between a single or double toggle jaw crusher depends on the nature of the task, the size of the feed material, and the required size reduction. For large, heavy-duty operations, a double-toggle jaw crusher is often the go-to. ... In jaw crushers, the crushing force is generated by the movement of the movable jaw plate towards the ...
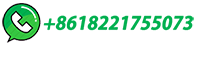
6 Types of Coal Crusher: Which Is Best for Crushing My Coal?
1. Jaw crusher The jaw crushers are popular primary crushers for coal. They are often used in mines and quarries where large amounts of coal are mined. The working principle of the jaw crusher is to use compression force to compress coal between a fixed jaw and a movable jaw for coarse crushing.
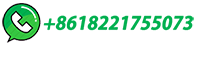
Gyratory VS Jaw Crushers: Advantages
For crushing extremely hard, tough materials extra strength can be built into the jaw crusher at less extra expense than in the gyratory. So-called "standard" designs, i.e., unreinforced, are usually more rugged than the …
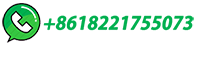
Fine Crushing Plant With Roll Crushers
Double Toothed Roll Crusher Introduction. The double toothed roll crusher is equipped with two toothed rolls. The toothed roll surface is divided into large (small) wolf teeth, special teeth for coke cutting, ring teeth, straight teeth, large plate teeth, etc. it is suitable for medium or coarse crushing occasions where the particle size of finished products requires 10 …
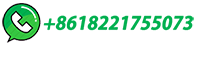
Understanding the Difference Between Blake Jaw Crusher …
Differences Between Blake Jaw Crusher and Dodge Jaw Crusher. Construction. The main difference between these two crushers lies in the construction of their crushing chamber. Blake Jaw Crushers have a single swing jaw while Dodge Jaw Crushers have double swing jaws. Crushing Action. Blake Jaw Crushers have a fixed jaw and a moving jaw that ...
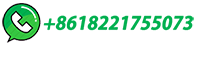
The Ultimate Guide to Jaw Crushers
A jaw crusher is a primary crushing machine used in mining, construction, and demolition recycling industries. It operates by compressing rock between a fixed jaw and a moving jaw, which moves back and forth to create crushing action. ... High Crushing Capacity: Jaw crushers are known for their high production capacity, allowing you to process ...
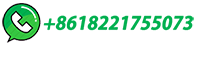
Jaw Crusher Working Principle
The jaw crusher discharge opening is the distance from the valley between corrugations on one jaw to the top of the mating corrugation on the other jaw. The crusher discharge opening governs the size of finished material produced by the crusher. Measuring Discharge Opening: Measure distance at bottom of jaws at the point of the crushing cycle …
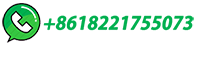
Jaw Crusher
Overview of size reduction of raw materials of the cement industry. Vipin Kant Singh, in The Science and Technology of Cement and Other Hydraulic Binders, 2023. 4.2.1 Jaw crushers. Jaw crushers are used for the primary reduction of hard and abrasive materials used for cement manufacture. Jaw crushers 3 are of either Blake-type or Dodge-type and operate by applying …
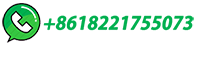
Jaw Crushers
A jaw crusher is a crucial component in mining and ore processing plants, performing the primary crushing of rock and mineral ore to reduce and control the size of materials for further sizing, …
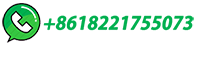
What is the difference between jaw and roll …
The jaw crusher mainly completes the task of crushing ore by periodically pressing the swinging jaw plate against the fixed jaw plate to crush the materials sandwiched in between. The jaw crusher has a simple …
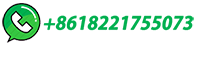
QJ241 Jaw Crusher
QJ241 utilizes a substantial 1,000 x 650mm (40 x 26 in.) jaw, powered by a 168kW (225hp) engine. This means that while the machine is compact, it retains a high level of power and productivity.
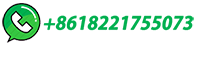
Compare Gyratory Crusher vs Jaw Crusher
Gyratory Crusher & Jaw Crusher Compared. There is another comparison that should be taken into consideration, that is the amount of space that each takes. The Jaw crusher is the smaller of the two and its single feed …
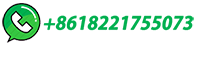
Gyratory VS Jaw Crushers: Advantages & Disadvantages
No discussion of primary crusher selection would be complete without a comparison of the two leading types: the standard gyratory crusher and the Blake jaw crusher. Although their fields of application overlap to a considerable degree (at least in the realm of primary crushing) there is no real conflict between these two machines; one supplements the …
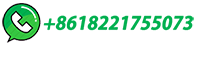
Types of Crushers: Choosing the Right One for Each Stage
Compression crushing: This method applies pressure to the material between two crushing surfaces, effectively squeezing it. It is used in jaw crushers, cone crushers, …
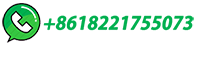
Jaw crushers – Crushing machines
Jaw crusher is a type of crushers that uses mechanical pressure of two jaws (one jaw is fixed and the other is reciprocating) to crush materials.. Jaw crusher is universal machine for crushing various materials. It is used for crushing rocks materials of any strength, slag and some metal materials. This machine can not be used for processing viscoelastic materials, such as wood, …
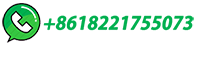
Types of Crushers: What You Need to Know
ARK 2416 jaw crusher in action Gyratory crushers. Run of mine material is transferred into a gyratory crusher's upper-level hopper. The walls of the gyratory crusher's hopper are lined with "V-shaped" pieces, the mantle and the …
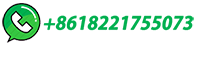
Jaw Crusher VS Cone Crusher | Advantages and …
Jaw crusher adopts the extrusion process between the moving jaw plate and the static jaw plate. Application Field. Cone crusher and jaw crusher are widely used, but the applicability of the two types of crusher is different. Jaw crusher has the most extensive adaptability and can meet the crushing requirements of almost any kind of materials.
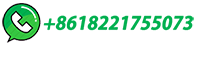
Roll Crushers Jaw Crushers Rotary Crushers Sample …
APPLICATIONS Coal, Gypsum, Limestone, Salt, Coke, Chemicals Sturtevant Inc. 348 Circuit Street Hanover, MA 02339 PHONE: 781-829-6501 FAX: 781-829-6515
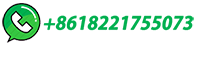
(PDF) An experimental investigation on rock crushability using jaw …
The same was observed for the relationship between TC and both d50 and d80; the correlation coefficients were higher and more reliable for the roll crusher than the jaw crusher.
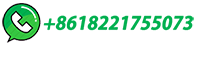
Jaw Crushers
Dodge Jaw Crusher: Similar to the Blake crusher, the Dodge crusher has a movable jaw that moves towards and away from the stationary jaw, and is preferred for crushing softer particles. Universal Jaw Crusher: This type has a "V"-aligned fixed jaw and a movable jaw on an eccentric shaft, creating an elliptical motion.
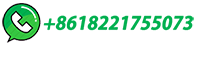