A Review of Flotation Physical Froth Flow Modifiers
Over the past few decades, the need to process more minerals while lowering capital costs has led to an increase in the size of flotation cells, e.g., 0.03 m3 to 1000 m3. However, this increase has created new challenges in the operation and design of industrial flotation cells, particularly in terms of froth removal, because the distance the froth must …
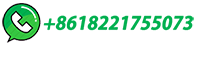
A critical review on natural surfactants and their potential for
The transition of the mineral processing sectors, which depend mainly on various petroleum-origin chemicals, to the green industry based on the production of greener materials and the reduction of carbon footprints, is mandatory due to the growing concerns regarding the extensive environmental impact of the mining industry. In this context, biological ore …
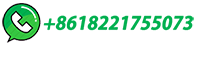
Coal Flotation
Wet Cleaning Process by Major Unit Operations. Dilip Kumar, Deepak Kumar, in Sustainable Management of Coal Preparation, 2018. 5.4.2 Flotation Reagents. In coal flotation, only collectors and frothers are generally used as chemical reagents.The collector enhances the hydrophobic property of coal. Kerosene or No 2 fuel oil are usually used as collectors, while …
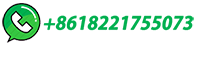
Flotation of Copper ORE from SOSSEGO Mine Utilizing
Flotation of Copper ORE from SOSSEGO Mine Utilizing Palm Oil as Collector Auxiliary 780 Collector auxiliaries (PO and DO) were emulsified in oil/water solution at 6000mg·L-1 by mechanical shaking ...
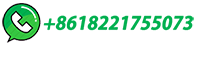
How to maximize ore and grade recovery through flotation
The key to avoid recovery losses is to ensure that you install the right flotation solution in your process. Attributes such as innovative tank design, efficient air and level control, proven drive systems with safe and easy maintenance have helped mining companies in achieving higher ore and grade recovery in the flotation cell, while also optimizing energy …
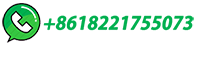
Flotation
The FLOTATION PROCESS is one of the commonest methods of extracting the valuable minerals from certain classes of ores, and it is generally more efficient as regards the recovery of the minerals than any other process applicable to the treatment of similar types of ores. The metallic contents of the minerals are recovered from the concentrates in a …
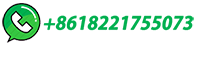
Flotation collectors
flotation collectors. Case description One of our customers wanted to address a reduction in the quality of the ore feeding their flotation plant and the resulting lower recovery rates. In …
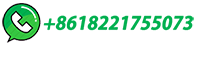
Flotation of Iron Ores: A Review
This paper reviews the industrial practices and fundamental research surrounding iron ore flotation. The advantages and disadvantages of direct flotation, cationic reverse flotation, and anionic reverse flotation are reviewed. A novel stepped flotation technique is discussed for the treatment of carbonate-rich iron ores.
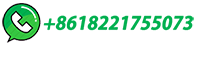
Technological assessments on recent developments in fine …
Imhoflot™ cells have great success in coal, potash, magnesite and many other base metal applications like copper, molybdenum, zinc and reverse iron ore flotation using H-cell, V-cell and G-cell types, which have been described in detail elsewhere (Imhof et al., 2004, Mohanty et al., 2005, Imhof et al., xxxx, Imhof et al., xxxx, Imhof et al ...
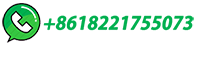
Froth Flotation
flotation circuit which are unique to each ore. Reagents Frothers Collectors Depressants Activators General frother information When mineral-bubble agglomerates reach the surface of a flotation cell, the bubbles can break and the collected mineral fall back into the slurry. To prevent this loss, a frother is added to produce a froth
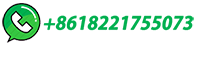
Mine/Mill Piping, Tank, Dust Collection Prefabrication
We also installed 18,000 feet of aboveground HDPE piping and equipment including tanks, silos, copper and nickel thickening tanks, pumps, compressors, flotation cells, concentrator building dust collector and ductwork. Work also included the secondary crushing dust collector and dust collection ductwork.
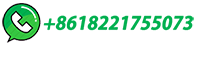
Technological assessments on recent developments in fine …
An advantage of this type of cell compared to traditional mechanical cells is the intensive collection efficiency of particles in the downcomer and ... -Pino, S., 2005. The …
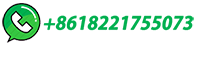
Enhancing Fines Recovery by Hybrid Flotation Column and Mixed Collectors
The froth flotation technique can be considered one of the most efficient methods for the separation of minerals. Prior to utilizing any physicochemical separation method, the size of the mined ore must be decreased to facilitate the release of the valuable materials. This practice, along with the increased exploitation of ores that carry fine mineral particles caused …
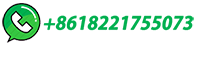
Flotation Guidebook
Useful Flotation Calculations 39 10.1 Two Product Formula for Plant Recovery 40 10.2 Two Product Formula for Recovery by Weight and Assay 40 10.3 % Solids 41 10.4 Mass of Solids …
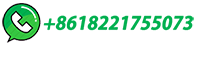
Froth Flotation Process
The Froth Flotation Process is about taking advantage of the natural hydrophobicity of liberated (well ground) minerals/metals and making/playing on making them hydrophobic (water-repel) individually to carefully separate them from one another and the slurry they are in. For this purpose we use chemicals/reagents: Frothers (MIBC) is what allows the …
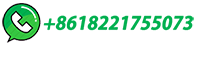
Flotation technologies
processing flowsheets. The Outotec Concorde Cell technology helps flotation circuits overcome these challenges and achieve improved efficiency in fine and ultra-fine particle recovery. Concorde Cell™ is an ideal flotation solution due to: • Superior recovery: faster kinetics, improved fine and ultra-fine particle recovery, optimized froth
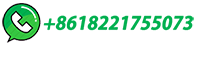
(PDF) Froth flotation process and its application
The paper is about the froth flotation process and its application. It is a metallurgical process for the extraction of metals in a pure state from their ores: especially for sulfide ores.
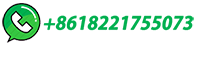
Minerals | Free Full-Text | The Challenges and …
Flotation is a common mineral processing method used to upgrade copper sulfide ores; in this method, copper sulfide mineral particles are concentrated in froth, and associated gangue minerals are separated as …
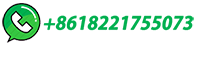
Flotation of Gold and Gold-Bearing Ores
1. Background. The application of flotation on a reasonable scale within the gold-mining industry commenced in the early 1930s following the introduction of water-soluble flotation collectors (specifically xanthates and dithiophosphate collectors) that allowed differential flotation of sulfide minerals (Weinig and Carpenter, 1937, Rabone, 1939, Richards …
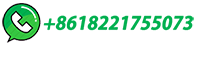
Optimisation of Reagent Addition during Flotation of a …
Page iii froth stabilising gangue, which resulted in reduced recovery of the valuable minerals. Therefore, a careful balance must be maintained in order to maximise nickel recovery.
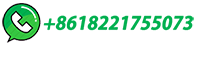
Effects of flotation operational parameters on froth stability …
Introduction. Froth stability plays an important role in determining selectivity and recovery in flotation (Farrokhpay, 2011). It should be noted that froth with very high stability is not desirable because in addition to recovering the particles attached to the bubbles, it creates favourable conditions for entrainment (Zheng, Franzidis, and Johnson, 2006).
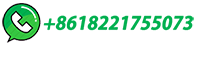
Froth Flotation
Separation of plastic wastes using froth flotation – An overview. Ozan KökkılıçShiva Mohammadi-JamPengbo ChuChristopher MarionYing YangKristian E. Waters, in Advances in Colloid and Interface Science, 2022. 5 Froth flotation. Froth flotation is a physicochemical separation process based on the differences in surface properties of materials. This technique …
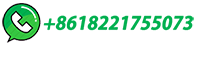
Digital twin of minerals processing operations for an …
The froth flotation process typically involves a series of multiple flotation cells arranged in a sequential manner. This configuration allows for a step-wise separation of valuable minerals from the ore, with each cell playing a specific role in the overall process [].The use of multiple cells in series enhances the efficiency of the flotation process by optimizing the …
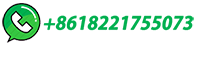
Flotation Plant Units
pplications and orespared to traditional delivery, Flotation Plant Units result in the ea. Compact footprint and minimized elevation. Wide range of flotation equipment from fine to …
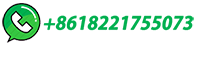
Gold Flotation
REAGENTS FOR SILVER ORE FLOTATION. ... Any good collector may be used for the flotation of gold, but organic collectors of the xanthate type produce a cleaner, higher grade concentrate than coal tar …
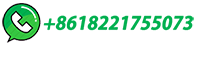
Combined Column and Mechanical Flotation Cell Process …
With higher concentration rates and a simple and efficient flowsheet, the FCSMC has been successfully industrialized for flotation circuits of minerals such as coal and copper ores in China. 21−23 However, there have been relatively few studies on the flotation behavior of columns and cells in gold mineral flotation, particularly concerning the combined column and …
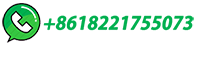
Frothers in flotation: A review of performance and function …
In a flotation cell, the size of air bubbles decreases with increasing the frother concentration. ... Cyclic alcohols are used in copper ore flotation as secondary (supporting) collectors. ... Mixed collector systems in flotation. Int. J. Miner. Process., 51 (1) (1997), pp. 67-79. View PDF View article View in Scopus Google Scholar. Harris and ...
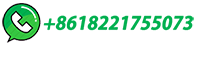
Improving the performance of a low-grade porphyry copper ore flotation …
A large porphyry copper flotation plant has been simulated using a flotation model developed from first principles using the hydrophobic force as a kinetic parameter (Huang et al., 2022, Gupta et al., 2022).The input to the simulation was the size-by-class liberation matrix (m ij) of a flotation feed, which was essential for predicting the size-by-class flotation rate …
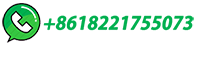
Froth Flotation of Chalcopyrite/Pyrite Ore: A Critical Review
Pyrite in deionized water. Particle size d80 = 38 µm. pH = 7 and 9 fixed with carbonate/bicarbonate and HCl. Gliwice 500 mL flotation cell. Pyrite flotation was induced by xanthate (1.1 × 10 −4 mol/L) and activated by copper cations (2.6 × 10 −4 mol/L).
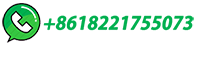
Gold Flotation
GOLD FLOTATION. The flotation process, which is today so extensively used for the concentration of base-metal sulphide ores and is finding increased use in many other fields. In 1932 flotation plants began to be …
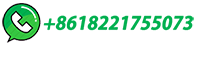