Iron Ore Sintering: Process: Mineral Processing and …
Sintering is a thermal agglomeration process that is applied to a mixture of iron ore fines, recycled ironmaking products, fluxes, slag-forming agents, and solid fuel (coke). The purpose of the sintering process is manufacturing a product with the suitable characteristics (thermal, mechanical, physical and chemical) to be fed to the blast furnace.
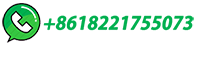
Evaluation of iron ore fines from the viewpoint of their …
The sintering properties of ores are evaluated separately according to each stage in sintering process, which is the heating stage before melt formation, primary melt formation in adhering fines layer of pseudoparticles, and assimilation of nucleus ore particle with calcium ferrite system melts.
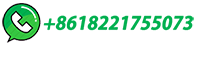
Iron Ore Pelletizing Process: An Overview
The iron ore pelletizing process consists of three main steps: 1. Pelletizing feed preparation and mixing: the raw material (iron ore concentrate, additives ... increase the strength of pellets before heating (green strength); ... be screened by a roller screen, which has increasingly replaced vibrating screen to extract ...
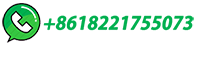
Iron processing | Definition, History, Steps, Uses, & Facts
iron processing, use of a smelting process to turn the ore into a form from which products can be fashioned. Included in this article also is a discussion of the mining of iron and of …
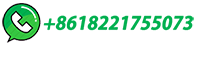
Process simulations in mineralogy-based geometallurgy of iron …
This study focussed on flowsheet simulation for mineralogical-based approach to geometallurgy of iron ores. Process unit models used were selected based on their applicability at particle level for iron ore beneficiation and flowsheet simulation. The feed streams for plant simulation were run-of-mine feed and forecast feed from ore …
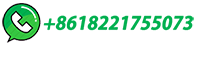
Iron Ore Processing
iron ore reserves [1]. P rocessing of low grade iron ore is inevitable as a r esult of increase in production and consumption of high grade ores . Though Indian iron ore is rich in iron but it contains high alumina, which is not favorable for efficient operation of blast furnace [2]. Indian iron ore mine have been operated by selective mining ...
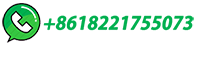
The impact of new technologies on the iron ore screening …
The role of screening, particularly through roller screens, is fundamental to ensuring the production of high-quality iron ore pellets by managing size distributions, …
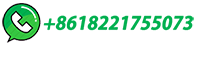
Ironmaking 101 – From Ore to Iron with Blast Furnaces
The first step in the production of steel or cast iron alloys is the reduction of iron ore, which contains iron oxide and gangue or mineral impurities, to unrefined hot metal or pig iron. The blast furnace is currently the key tool for ironmaking.
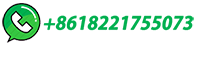
Introduction to Mineral Processing or Beneficiation
Within an ore body, valuable minerals are surrounded by gangue and it is the primary function of mineral processing, to liberate and concentrate those valuable minerals. 1.3 Run-Of-Mine Material and Minerals. Generally, mineral processing begins when an ore is delivered from a mine, to a processing facility.
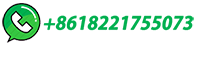
The screening process: a vital component of the crushing …
The whole process philosophy is especially important when managing the crushing circuit, one of the biggest energy consumers in any plant. This is where …
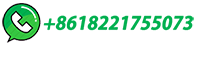
Iron Mining Process
At the processing plant, the taconite is crushed into very small pieces by rock crushing machines. The crushers keep crushing the rock until it is the size of a marble. The rock is mixed with water and ground in rotating mills until it is as fine as powder. Separation The iron ore is separated from the taconite using magnetism.
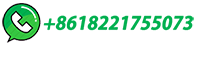
Sintering: A Step Between Mining Iron Ore and …
The only source of primary iron is iron ore, but before all that iron ore can be turned into steel, it must go through the sintering process. Sinter is the primary feed material for making iron and steel in …
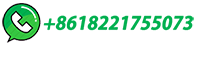
Direct Reduced Iron By-Product Fines (DRI D): A Guide …
iron ore burden is such that the ascending column of g ases interfaces with the maximum surface area of the iron ore - the higher the content of iron ore fines in the feedstock, the lower the permeability of the burden. The iron ore feedstock (pellets and lump ore) is therefore screened to remove fines before being charged to the furnace.
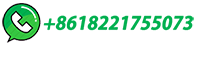
Mining & Mineral Processing
Our unparalleled knowledge and experience in iron ore recovery, has seen many of the world's largest producers rely on us for the design and engineering of mineral processing systems, that deliver them increased efficiencies and higher production.
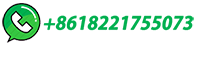
Mobile screening plants in a large-scale operation in India
The red colour usually allows you to spot it from a distance: iron ore. The volcanic rock is mainly used in the manufacture of steel. India has vast reserves of iron ore and is the second biggest steel producer in the world. The mobile screening plants MOBISCREEN EVO from Kleemann are used during the extraction of the important material.
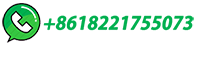
Iron Ore Processing
The coarsely crushed iron ore is screened by a circular vibrating screen and then conveyed by a belt conveyor to a cone crusher for secondary crushing. In order to …
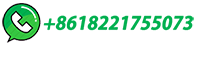
Sieving & Screening Solution for Iron Ore
IRON ORE PROCESSING. Iron is the most abundant metal found on the earth consisting of 5% of the earth's crust. This metal is widely used in our day-to-day life from pin to plane. ... Galaxy Sivtek is helping you to check and screen the powder before packaging. This iron powder is used in many industries. Products made from iron powder need to ...
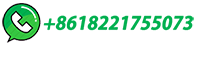
Processing – Karara Mining
To process magnetite the ore needs to be crushed, screened, ground, magnetically separated, filtered and dried. ... The primary grinding plant of four ball mills grinds the ore in slurry into fine particle sizes of <50 µm before further magnetic separation to produce a concentrated magnetite ore stream, with elevated Iron (Fe) grades of ~58% ...
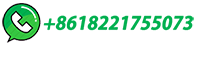
Iron Ore Processing
Resource Recovery and Recycling from Metallurgical Wastes. S. Ramachandra Rao, in Waste Management Series, 2006 9.8 Production of Ceramic Tiles from Iron Ore Tailings. Current practice of washing iron ore before it is processed for extractive metallurgical operation results in three products, coarse ore lumps with sizes in the range 10-80 mm, …
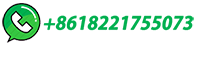
Comminution and classification technologies of iron ore
Additionally, iron ore processing facilities often receive ores from various sources (such as satellite pits) with different qualities. These ores may be treated by different processing routes and/or blended to meet product specifications. Some examples of different iron ore crushing and screening flowsheets are provided below: 8.2.3.1.
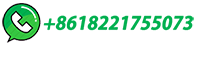
Iron Ore Processing: From Extraction to Manufacturing
Learn about the key stages in iron ore processing, including crushing, screening, and beneficiation techniques for optimal resource utilization.
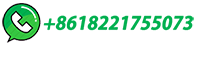
Ore Processing | Multotec
For iron ore extraction, the iron ore processing plant receives ROM where it undergoes crushing and subsequent screening on a grizzly screen. It is then sized and above cut …
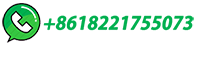
Effects of process parameters on the growth behavior and
This work proposes a novel horizontal high-shear granulator for iron ore granulation before sintering process. The granulation behavior such as growth process and structure of granules were firstly analyzed, followed by the effects of operation conditions such as water content, initial particle size distribution, and the concentrate ratio.
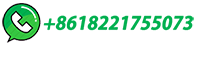
The six main steps of iron ore processing
1. Screening. We recommend that you begin by screening the iron ore to separate fine particles below the crusher's CSS before the crushing stage. A static screen is used to divert the fine particles for crushing. This step prevents overloading the crusher and …
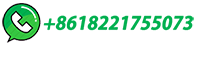
Iron Ore Pelletizing Process: An Overview | IntechOpen
The iron ore production has significantly expanded in recent years, owing to increasing steel demands in developing countries. However, the content of iron in ore deposits has deteriorated and low-grade iron ore has been processed. The fines resulting from the concentration process must be agglomerated for use in iron and steelmaking. …
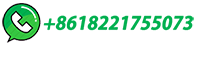
Iron ore beneficiation: an overview
Dry processing of iron ore: In dry processing of iron ore, ROM is generally crushed below 40 mm through three-stage crushing and thus segregated by screening into 10–40 and −10 mm fractions. For softer ore, tumbler index is generally low and hence lump ore is crushed below 10 mm to produce fine product. Yield from the plants has …
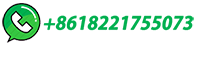
Introduction: Overview of the global iron ore industry
Iron ore is regarded as the second most important commodity behind oil. As an essential input for the production of crude steel, iron ore feeds the world's largest trillion-dollar-a-year metal market and is the backbone of global infrastructure.
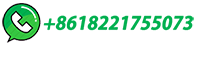
Beneficiation of Iron Ores – IspatGuru
For beneficiation of a particular iron ore, the emphasis is normally to develop a cost-effective flow sheet incorporating necessary crushing, grinding, screening, and beneficiating techniques which are necessary for the upgrading of the iron ore. Processing of iron ore for its beneficiation normally depend on the size and the nature of ...
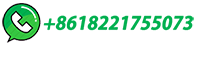
Iron Ore Processing, General
The iron ore processing industry produces usable concentrations of iron-bearing material by removing nonferrous rock (gangue) from low-grade ore. In the United ... Before the blast, the holes are lled with a special mixture of blasting agents. Once prepared, the mine site is cleared of workers and equipment, and the blast is ...
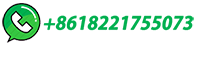
Mineral processing | Metallurgy, Crushing & Grinding
Mineral processing, art of treating crude ores and mineral products in order to separate the valuable minerals from the waste rock, or gangue. It is the first process that most ores undergo after mining in order to provide a more concentrated material for the procedures of extractive metallurgy.
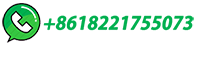