How to best maintain the right crusher settings : Pit & Quarry
Why is selecting and maintaining the proper jaw crusher closed-side setting (CSS) so important to crushing efficiency? Jarrod Adcock, crushing product manager at Superior Industries, explains. "The right jaw crusher closed-side setting directly affects the flow of the rest of the crushing circuits, allowing the primary jaw to produce material …
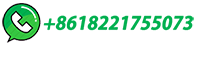
What Are the Differences Between The 7 Types of Crushers?
7 Types of rock crushers have different advantages in many aspects like crushing ability, suitable material, lifespan, etc. Once you know what are the differences, you know to choose an optimal crusher.
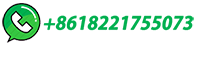
® C130™ jaw crusher
® C130™ jaw crusher is commonly used as a primary crusher, preparing material feed for the secondary crusher. However, even though it is traditionally seen at the first stage of the crushing process, this crusher also performs well in other roles, depending on the processed material and application.
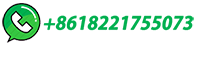
Primary Crushing: A Comprehensive Guide
Getting a good start on primary crushing is critical for all that follows. It can help you save money while also improving the finished product. People in charge can really affect the final product's look. They do this by choosing the right type of first crusher. This could be a jaw crusher, gyratory crusher, or impact crusher.
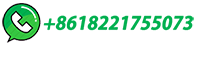
Jaw Crusher Explained
Gyratory Crusher; Jaw Crusher; Cone Crusher; Crusher Types (jaw, cone, gyratory) Typically, the initial crushing stage is completed using either gyratory crushers or jaw crushers. It is often the case that there will be only one crusher installed, and this will be referred to as the 'primary crusher'.
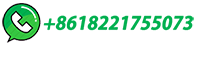
McLanahan | Jaw Crushers
Jaw Crushers. Jaw Crushers are a compression-type machine that crush material between a moving piece of steel and a stationary piece of steel. They are used for primary and sometimes secondary size reduction.
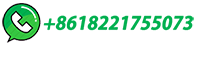
The Ultimate Guide to Jaw Crushing Machines: …
Discover everything you need to know about jaw crushing machines, from the various types such as single and double toggle, hydraulic and portable models, to their working principles, advantages, …
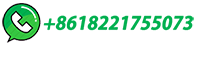
Primary Crusher Selection & Design
Dependability and long service life are landmarks of good primary crusher design of up to 30 yrs. The selection of the primary crusher must consider best-in …
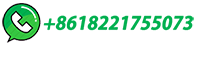
3. Select the crusher settings for a primary jaw | Chegg
Question: 3. Select the crusher settings for a primary jaw crusher and a secondary roll crusher to produce 150 tons per hour (136 t/h) of aggregate meeting the following specifica- tions.
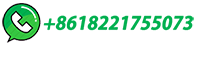
Selecting the right type of crushing equipment
Primary crushing – The duty of the primary crusher is, above all, to make it possible to transport material on a conveyor belt. In most aggregate crushing plants, primary crushing is carried out in a jaw crusher, although a …
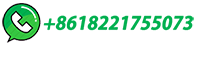
® C Series™ jaw crushers
® C Series™ jaw crushers are used as primary crushers in aggregates production, mining operations and recycling applications.
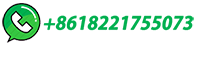
Jaw Crusher: What Is It & How Does It Work?
Learn how a jaw crusher works, what types of jaw crushers are available, and how to use them effectively for your construction projects.
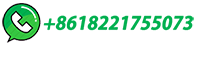
The Ultimate Guide to Rock Crushers | Mellott
Jaw crushers are ideal for primary crushing. Cone Crushers Cone crushers are quite different from jaw crushers. They use a rotating cone within a bowl to crush rock into smaller pieces. ... Considerations for Choosing a Crusher. When choosing a crusher, several factors come into play. First, consider the hardness and size of the …
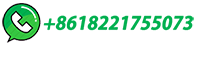
Solved Select the crusher settings for a primary jaw crusher
Select the crusher settings for a primary jaw crusher and a secondary roll crusher to produce 150 tons/h (136 t/h) of aggregate meeting the following specifications. Indi- cate the output in tons per hour (t/h) and in percentage for each of the specified size ranges.
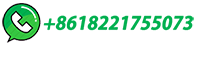
Crushers
All crusher types with 100+ years of experience. Our crushers are fit for aggregates production, construction material recycling and mining operations.
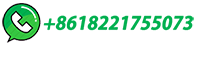
Crushing and Screening Handbook
the crusher and scalp out fi nes. Primary gyratory crushers – ideally suited to all high-capacity primary hard rock crushing applications. Jaw crushers – we have more installed jaw crushers than anyone in the world. The lead-ing choice due to their high reduction ratio and heavy duty design. Cone crushers – capacities available to suit all
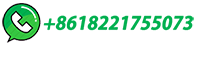
What is a Primary Crusher?
Learn what a primary crusher is and why it is important for your crushing business. Discover the types of primary crushers to increase crushing efficiency.
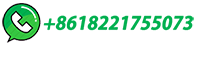
Jaw Crusher
Primary jaw crushers typically operate in open circuit under dry conditions. Depending on the size reduction required, the primary jaw crushers are followed by secondary and tertiary crushing. The last crusher in the line of operation operates in a closed circuit. That is, the crushed product is screened and the oversize is returned to the ...
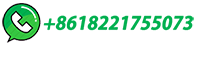
Selecting the Right Crushing Equipment | Agg-Net
The duty of the primary crusher is, above all, to make it possible to transport material on a conveyor belt. In most aggregate crushing plants, primary crushing is carried out in a jaw crusher, although a gyratory primary crusher may be used.
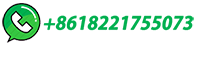
Primary Crushing
The term "primary crusher," by definition, might embrace any type and size of crushing machine. ... Selecting the right type and size of primary crusher is a problem of prime importance in the designing of a crushing plant of any nature and size. Usually this machine is the largest and most expensive single item of equipment in the plant; a ...
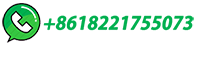
Primary Jaw Crusher – Everything You Need to Know
Learn everything you need to know about primary jaw crushers in this comprehensive guide. Discover how they work, their applications, and where to buy …
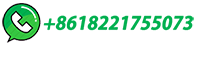
McLanahan | How To Size A Jaw Crusher
If you are considering a Jaw Crusher for your application, here's how to choose the right one. Jaw Crusher sizing and selection Like other types of crushers, Jaw Crushers are sized based on the material to be crushed. This includes: - A description of the material to be processed - Physical characteristics of the material - Maximum feed size
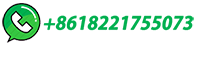
Primary Crusher vs. Secondary Crusher: Understanding Their …
The primary crusher's function is to reduce the size of the rock or stone for easier handling and transportation. The primary crusher is usually a jaw crusher or a …
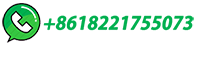
Choosing the right primary crusher for your aggregate …
Here is what a successful process of choosing a primary crusher looks like! Stages include defining crusher purpose, model refinement and installation.
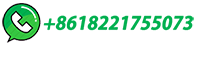
What Crusher Should You Choose for Primary Crushing?
Explore efficient primary crushers, from gyratory crushers to jaw and hammer crushers, and elevate production to new heights.
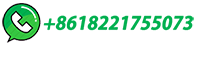
Types of Crushers: Choosing the Right One for Each Stage
Learn about different types of crushers and their applications in primary, secondary, and tertiary crushing stages.
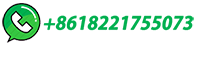
Choosing the Right Jaw Crusher Size and Capacity for …
Maximizing crusher performance and productivity requires selecting the right jaw crusher size and capacity. Learn how to determine the optimal size and capacity for your application, and discover the benefits of choosing the right equipment. Our expert guide provides valuable insights and recommendations for achieving the best possible …
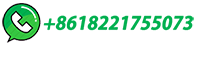
Selecting the Right Crusher for Quarry Operations | Agg-Net
Jaw crushers. Jaw crushers, which use a moveable jaw and a stationary plate designed to form a 'V', crush material using compressive force. These crushers offer an ideal solution for primary crushing applications involving hard, abrasive materials such as granite or recycled concrete.
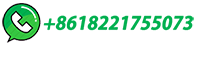
Understanding Types of Jaw Crusher: A Comprehensive …
Blake jaw crushers, also as double toggle jaw crushers, are characterized by the position of the pivot of the swing jaw, which is located at the top of the machine. This design allows for a larger feed size and a higher capacity, making it …
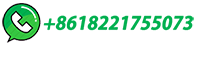
Jaw crushers, Stationary Jaw crusher series
Jaw crushers come with everything you need for plug-and-play primary crushing operations. Each jaw crusher comes with feed hopper, feed hopper interface, drive and subframe with v-belt guard and motor bracket, our unique guarding retraction arrangement and toggle plate stop.
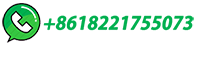