Various Types Of Iron Ore Beneficiation Processes
There are several different types of iron ore, each with its own unique characteristics and chemical composition. The iron ore beneficiation process aims to …
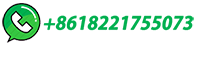
Mineral processing | Metallurgy, Crushing & Grinding
mineral processing, art of treating crude ores and mineral products in order to separate the valuable minerals from the waste rock, or gangue. It is the first process that most ores …
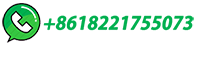
Applied Sciences | Free Full-Text | A Method of Ore Blending …
Ore blending is an essential part of daily work in the concentrator. Qualified ore dressing products can make the ore dressing more smoothly. The existing ore blending modeling usually only considers the quality of ore blending products and ignores the effect of ore blending on ore dressing. This research proposes an ore blending …
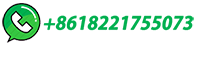
Flotation of Iron Ores: A Review
A tremendous amount of research has been done on refining the flotation process for iron ore and designing the reagents which go into it. This paper reviews the industrial practices and fundamental...
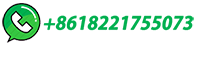
Galvanishing of iron sheets is done by
Ore dressing for iron is done by. A froth floatation method. B magnetic separation. C hand picking. D all of the above. Submit. The process of zinc plating on iron sheet is known as . View Solution. The process of …
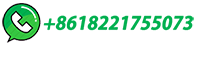
Concentration of iron ore is done by
Since, the nature of iron ores is magnetic, thus its concentration is done by magnetic separation method.
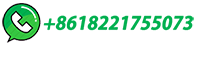
(PDF) GRAVITY SEPARATION IN ORE DRESSING
Gravity dressing is done by means of wat er and air. ... Many large jig circuits are still operated in the co al, cassiterite, tungsten, gold, bary tes, and iron-ore . industries.
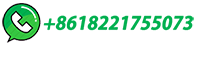
How is ore-dressing of iron done?
In magnetic separators, ferromagnetic materials are separated from non-magnetic materials using the effect of magnetism. The iron ores siderite and hematite may theoretically be processed using this method as well since they become weakly magnetic when heated.
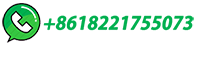
machinery
The decline of importing iron ore has provided great chance for the development of iron ore industry in China. Meanwhile, the traditional coal mining is facing pressure due to the market demand and increasing imported coal. ... The process flow of ore dressing need to be simple and of high efficiency and the equipments of the flow need to be ...
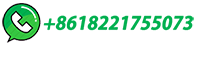
Ore
Ore is a deposit in Earth's crust of one or more valuable minerals. The most valuable ore deposits contain metals crucial to industry and trade, like copper, gold, and iron.
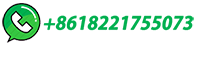
Ore Dressing Methods
Ore-dressing methods fall naturally into two general subdivisions— (1) concentration methods and (2) direct-recovery methods (amalgamation and leaching or …
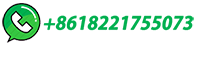
Ore dressing for iron is done by:
In the field of extractive metallurgy, mineral processing, also known as ore dressing, is the process of separating commercially valuable minerals from their ores. Ore dressing for iron is done by magnetic separation.
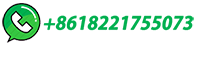
The six main steps of iron ore processing
Learn about the steps involved in iron ore processing, from crushing and grinding to separation. Contact Multotec experts for guidance on iron processing.
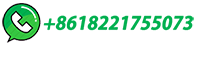
Ore dressing for iron is done by
Ore dressing for iron is done by A. froth floatation method B. magnetic separation C. hand picking D. all of the above
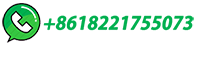
Physiochemical separation of iron ore
The iron ore industry commenced with direct shipping and smelting of iron ores. These ores were fully oxidized, consisting of high-grade hematite containing negligible sulfur and phosphorus and very low levels of other impurities. As these ores became depleted the iron ore industry had to change to accommodate lower grades and less …
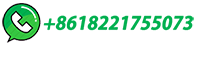
Flotation | Mineral Processing, Separation & Beneficiation
Flotation, in mineral processing, method used to separate and concentrate ores by altering their surfaces to a hydrophobic or hydrophilic condition—that is, the surfaces are either repelled or attracted by water. The flotation process was developed on a commercial scale early in the 20th century to
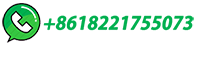
Ore dressing for iron is done by:
Solution For Ore dressing for iron is done by: Ask your question, on a video call with tutor
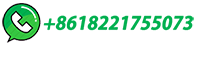
Four Kinds of Hematite Ore Dressing Processes, Which One …
The mineral form is dominated by iron oxide. According to its composition, hematite ore can be divided into four varieties, including ilmenite, aluminum hematite, magnesium hematite and hydrohematite.
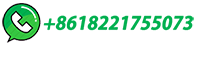
Characterization and Ore Dressing of Bauxite from Brazil
This work intended to characterize and to ore dress crystallized bauxite (CB), amorphous crystallized () and nodular bauxite (MNB) from Pará to make them usable in the Bayer process. The ore dressing was developed by mechanochemical activation with an alkaline reagent in different concentrations and conditioning time.
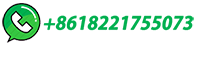
Extraction of Iron from its ores, Iron dressing, Reduction
Extraction of iron or its metallurgy is the process of obtaining this metal in a form where it can be put to practical use, and this process of extraction consists of three …
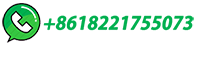
Concentration of Ore | Learn Important Terms and Concepts
In iron ore, the non-magnetic impurities from magnetic iron ore are separated by the magnetic separation process. Leaching is a process which involves the use of chemical substances to dissolve metal ore which has significant use in the concentration process as it is easy to perform and pollution free.
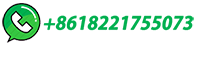
Ore dressing of iron ore is done by
In the field of extractive metallurgy mineral processing also known as ore dressing is the process of separating commercially valuable minerals from their ores Ore dressing of iron ore can be done by Magnetic separation process as iron possesses magnetic properties Magnetic Separation process is based on differences in magnetic properties of ...
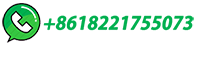
Concentration of Ore Definition, Types and Properties of Ore …
Concentration of Ore - Understand the properties of Ore and its types, Hydraulic Washing, Magnetic Separation, Froth Flotation Method, Leaching and more.
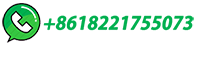
Ore dressing for iron is done by
The correct answer is Ore dressing for iron is done by magnetic separationDuring ore extraction, the iron ore is first prepared by crushing and grinding before being processed. To raise the iron content, the goal of this is to minimise the unwanted high proportion of admixtures to a minimum level. Processes like flotation or magnetic separation are used …
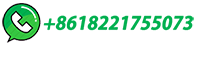
Mineral Processing
Mineral processing, also known as ore dressing, mineral beneficiation, or mineral engineering, is defined as the science and art of separating valuable metallic and nonmetallic minerals from unusable gangues.
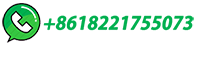
Magnetizing Roasting Mechanism and Effective Ore …
Key words: oolitic hematite ore; ore dressing; magnetizing roasting; mechanism 1 Introduction Oolitic hematite ore is an important existing form of iron ores. From published information, oolitic hema- ... mm ore sample, iron content in tailing was about 23%. Therefore, smaller particle size is more beneficial to the magnetizing roasting of ...
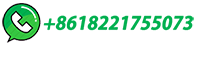
Ore dressing for iron is done by
Step by step video, text & image solution for Ore dressing for iron is done by by Chemistry experts to help you in doubts & scoring excellent marks in Class 12 exams.
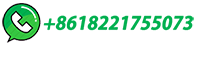
From Ore to Iron with Smelting and Direct Iron Reduction
Ironmaking is a critical step in producing high performance steel because high-quality raw materials reduce the time and energy to purify the iron to steel. On the …
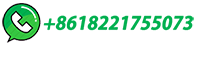
Mineral Processing and Ore Dressing
In this process certain minerals can be separated from a large portion of gangue, or waste material. A preliminary crushing to the necessary fineness is made, in …
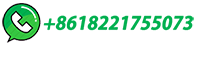
Iron ore beneficiation: an overview
This chapter briefly discusses the current scenario of the iron ore resources in India, iron ore mining methodology, beneficiation technique, and the current operating practices for achieving sustainable growth in the iron and steel industry.
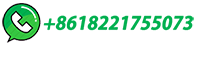