Size recovery curves of minerals in industrial spirals for …
Spiral mineral size recovery curves observed in for iron ore concentrators. ... Thus, the Crago flotation process was evaluated to recover the iron contained in the finest fraction of the Mont-Wright tailings. Since it was patented in 1942, the Crago process with fatty-acid rougher flotation followed by deoiling and amine cleaner flotation has ...
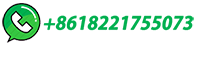
Overview | Labrador Iron Ore
The iron ore deposits in the Labrador City area occur as specular hematite and magnetite, generally in the ratio of 65:35. IOC has mineral reserves and resources of 1.1 billion tonnes and 1.7 billion tonnes, respectively, with an …
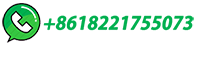
PGM Ore Processing at Impala's UG-2 Concentrator
PGM Ore PrOcessinG at iMPala's UG-2 cOncentratOr in rUstenbUrG, sOUth africa. eUGene nel and JOhan therOn - iMPala PlatinUM ltd.; chris Martin and hans raabe - sGs abstract Impala Platinum Limited is the world's second largest platinum producer, producing more …
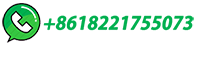
Gold Extraction & Recovery Processes
Process Development Considering the different gold minerals present alone or combined with the host rock, it will be necessary to discharge the unwanted material in order to increase the concentration of gold in an economically manner. This part treats the strategy of beneficiation as a combination of several processes. Joining together these units make …
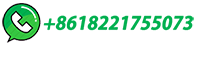
Iron processing
The partially reduced ore is then smelted in the second unit, and liquid iron is produced. Smelting-reduction technology enables a wide range of coals to be used for iron making. Iron …
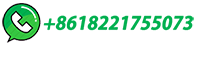
Iron Ore Processing: From Extraction to …
Iron ore processing is a crucial step in the production of steel, one of the most essential materials in modern society. Iron ore, a naturally occurring mineral composed primarily of iron oxides, is mined and processed to extract …
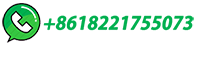
How do spiral concentrators work?
Spiral concentrators are used for a number of mineral processing applications. They're extensively used to process heavy mineral sand deposits, including monazite, zircon, ilmenite and rutile deposits. More recently, spiral …
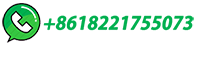
Iron Ore Pelletizing Process: An Overview | IntechOpen
The iron ore production has significantly expanded in recent years, owing to increasing steel demands in developing countries. However, the content of iron in ore deposits has deteriorated and low-grade iron ore has been processed. The fines resulting from the concentration process must be agglomerated for use in iron and steelmaking. This chapter …
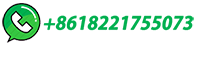
Iron Extraction by Blast Furnace Metallurgy
Iron extraction is an extremely important process as it deals with building a bridge, house et cetera. Iron extraction is one of the main parts of metallurgy. Iron Extraction Procedure. Iron extraction is considered as an extremely lengthy process that starts from concentration and ends through calcination roasting. The process of concentration ...
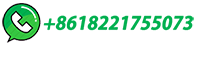
Gravity Spiral Concentrator Working Principle
The Humphreys Spiral Concentrator is a simple, efficient gravity concentrator which effects a separation between minerals of the proper size range that have sufficient difference in their specific gravity. This …
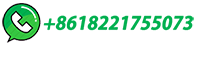
Low grade Iron Ore Beneficiation and the …
Low grade Iron Ore Beneficiation and the Process of Jigging . Iron ore resources are getting consumed at an accelerated rate because of the growth in the production of iron and steel. ... Jigging process is an ore …
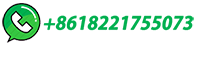
The six main steps of iron ore processing
Mining
Concentrator. In the processing stage, the mined material is transformed into usable raw material. For iron ore this involves crushing the ore and then concentrating it in different …
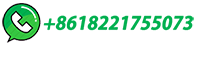
Spiral (Concentrators)
The process proposed by Kasey (1956) included an industrial application involving quenching the roasted ore particles from high temperatures; a process that would likely significantly decrease the energy required for crushing and grinding operations as detailed by Fitzgibbon (1990) in their research into thermally assisted liberation. To the ...
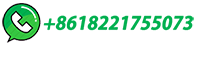
Online Slurry Analysis for Process Control and Monitoring at Iron Ore
This paper presents the art of on-stream particle size and elemental analysis used at iron ore concentrators, followed by the results and experiences from several sites.Online particle size analysis is rather common at medium- to large-sized concentrators. Online X-ray fluorescence (XRF) elemental analysis, however, is only used in some iron ore concentrators, while it is a …
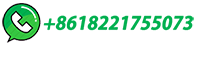
Dense Media Separation (DMS) Plants
Heavy medium vibration chute uses heavy flotation liquid to separate coarse ore (hematite, manganese ore, and other ferrous metals) in the vibration process, feed ore size is generally 75-6mm. 【 Working Principle 】 Under the action …
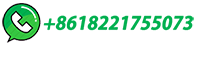
Iron Ore Processing: From Extraction to Manufacturing
The final stage in iron ore processing is ironmaking, where the iron ore is transformed into molten iron through a process called reduction. The most common method of ironmaking is the blast furnace route. In a blast furnace, iron ore, coke (carbon), and fluxes (limestone or dolomite) are loaded into the furnace from the top.
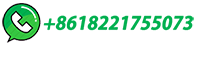
Eco-efficient and cost-effective process design for magnetite iron ore …
Assessment of different eco-efficient comminution process circuits to treat magnetite iron ore. ... There have been three expansions since and, in the 1990s, Empire Mines had a total of 24 individual concentration lines and a total plant capacity of 8 Mtpa of pellets. The target grind size of the circuit varies between the 90-95 percent minus ...
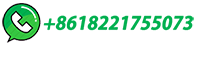
Magnetite
The magnetite ore which makes up a large percentage of the existing orebody is mined as part of the usual open cut mining process. Processing . Copper and gold are recovered from the ore using traditional grinding and flotation methods in the concentrator. Magnetite is liberated during this process and the magnetite
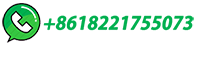
Iron Ore Processing, General | SpringerLink
CHAPTER-7. ON ORER. K. Rath and R. SinghINTRODUCTIONGravity concentration process is the o. dest beneficiation method known to mankind. This is a physical process and exploits …
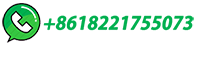
Knelson Concentrator
The Knelson Concentrator relies on an enhanced gravitational force together with fluidization process to recover even very micron sized particles.First water is injected into the rotating concentrating cone through series of fluidization holes. Then feed slurry is introduced through a stationary feed tube.
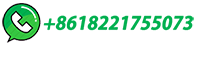
Iron Ore Beneficiation Process
The whole process of magnetic concentration as applied to the eastern Mesabi magnetites is a good illustration of the manner in which the various types of machines can be made to work together so as to produce a high-grade furnace product from an ore material containing only 25 per cent of iron in the form of magnetite.
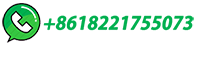
Iron Ore Pelletizing Process: An Overview
The iron ore production has significantly expanded in recent years, owing to increasing steel demands in developing countries. However, the content of iron in ore deposits has deteriorated and low-grade iron ore has been …
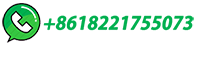
Coons-Pacific Iron Ore Concentrator
The first step in all beneficiation plants is converting crude ore into a medium that can be effectively fed into a concentrator. This generally involves some degree of primary crushing, as well as screening or classifying the ores into sizes - either oversized or minus-grade and undersized ores - which were amenable to concentration. At the Coons-Pacific plant, …
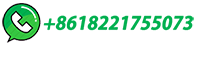
1 Froth Flotation – Fundamental Principles
the ore is not weighed and only assays will be available. However, it is possible to express the ratio of concentration in terms of ore assays. Starting with the mass balance equations, and the definition of the ratio of concentration: F = C + T, Ff = Cc + Tt, Ratio of Concentration = F/C
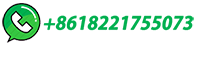
Iron Ore Company of Canada
We are a leading North American producer and exporter of premium iron ore pellets and high-grade concentrate. Our operations include a mine with five operational pits, a concentrator and a pelletizing plant located near Labrador City and the wholly-owned 418 km railroad, the Quebec North Shore and Labrador Railway (QNS&L), that links our Labrador operations to Company …
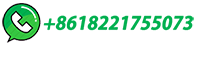
Ore Concentrate filtration – Dewater Filter Press
Ore Concentrate filtration. What is the filtration or dewatering of ore concentrates? After mine excavation, the mining process, forecasts to separate the valuable ore like iron ore, copper, zinc, molybdenum, coal concentrate etc.. from the undesired materials called tailings. This process is done in the ore concentrator plant or beneficiation ...
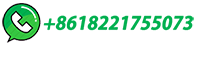
Understanding Iron Ores and Mining of Iron …
The process of mining of iron ore from discovery of an iron ore deposit body through extraction of iron ores and finally to returning the land to its natural state consists of several distinct steps. The first is discovery of the iron …
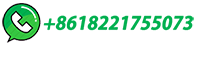
Iron Ore Concentration
Iron ore concentration is a mineral-specific concentration process within the mineral processing industry. Multotec has custom-developed mineral processing concentration equipment to suit all requirements pertinent to iron ore concentration.
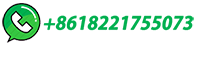
Nickel processing
Nickel processing - Extraction, Refining, Alloying: The extraction of nickel from ore follows much the same route as copper, and indeed, in a number of cases, similar processes and equipment are used. The major differences in equipment are the use of higher-temperature refractories and the increased cooling required to accommodate the higher operating temperatures in nickel …
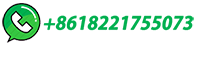
Samarco Iron Ore Mine, Alegria, Brazil
Iron ore mining. Itabiritic ore is excavated by bulldozers, loaded by front-end loaders into 177t-capacity trucks and taken to a crushing and screening plant in the blending yard. ... The concentrator is capable of an annual production of 24Mt of iron-ore concentrates a year. Its output in the 2008 financial year was 8.5Mt. ... The installation ...
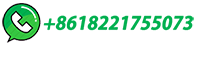