Reduction of Iron Ore Pellets, Sinter, and Lump Ore …
Sinter, lump ore, and iron ore pellets were used in experiments. The composition for all three materials is shown in Table 1. The total iron content (Fe tot) and the oxidation stage of the iron were measured with a titration method and the sulfur content with flame analysis. The contents of other components were mea-
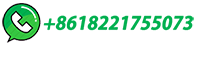
Influence of Biomass Absorptivity on the Process of Sinter …
Capillary water absorption of materials is a very important factor in the process of pre-treatment of fine-grained materials. Materials that are in a moisturized state capable of forming a firm, compact pellet are, thanks to this particular physical property, suitable for utilisation in sinter charge preparation within the process of sintering iron-ore raw materials. The pelletising ability of ...
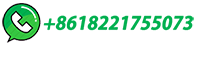
Unit Processes in Pyrometallurgy: Drying, …
Principle steps for sintering process- 1.The iron ore fines, limestone fines, dolomite fines, lime dust, metallurgical wastes and coke breeze are taken proportionately based on charge calculations. Then this mixture is mixed and …
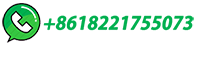
Pelletization
Similar to sintering, pelletizing is another widely used process to agglomerate the iron ore. Sinter plants are usually located near the blast furnace plant, but pelletizing plants …
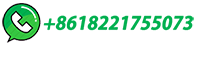
Iron Ore Pelletizing Process: An Overview
Evolution of binders for iron ore pelletizing Induration technologies Challenges and innovations in iron ore pelletizing 2. Pelletizing process and raw materials The iron ore is mined mostly from open pit deposits through mining operations and the raw product, run of mine, is subjected to mineral processing.
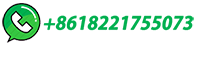
Sintering: A Step Between Mining Iron Ore and …
World resources are estimated to be greater than 800 billion tons of crude ore containing more than 230 billion tons of iron. The only source of primary iron is iron ore, but before all that iron ore can be turned into steel, it …
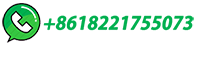
sintering and pelletisation of nignian iron ore
Contribute to lbsid/en development by creating an account on GitHub.
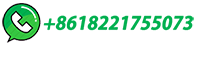
sbm/sbm difference sintering and pelletisation of iron ore…
You've already forked sbm 0 Code Issues Pull Requests Packages Projects Releases Wiki Activity
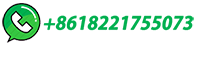
Utilization of Biomass Pellets in the Iron Ore Sintering …
3.1 Impact of Biopellet on Sintering Temperature Profiles. Figure 3 shows the temperature profile observed during iron ore sintering process at different proportions of biopellet. With an increase in biopellet the maximum temperature within the sinter bed reduces. In the presence of biomass, the water content required to granulate the sinter raw mix to a …
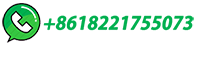
Iron Ore Pelletization: Part I. Fundamentals
ABSTRACT. The behavior of iron ore pellet binders is complex. Any pellet binder is subject to a handful of practical requirements: that it be readily dispersed through a pellet, that it effectively controls the movement of water within the pellet, and that it contributes to the inter-particle bonding within the pellet.
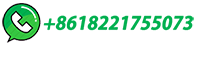
Iron Ore Pelletizing Process: An Overview | IntechOpen
The iron ore production has significantly expanded in recent years, owing to increasing steel demands in developing countries. However, the content of iron in ore deposits has deteriorated and low-grade iron ore has been processed. The fines resulting from the …
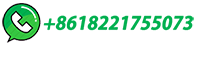
Study the effect of chromite ore properties on pelletisation process
Chrome ore properties play a critical role in various pelletisation subprocesses (grinding, filtering, pelletisation and sintering) and slight variation in ore properties significantly affect the whole pelletisation process. Three ore samples (sample-A, B and C) were collected from different working faces of a chromite ore mine.
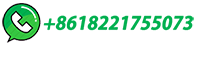
Iron Ore Pelletization
As there can be significant variation in process requirements and sources of iron ore fines, testing is often an essential part of the development of a successful iron ore pelletizing operation. Different sources of iron ore will respond …
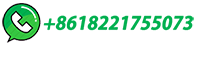
PMAI I Pellet Manufacturers Association of India
India's iron ore export basket used to comprise predominantly of iron ore fines (almost to the tune of 80% of total iron ore exports) largely because of the lucrative market it catered to globally and secondly as the domestic market for …
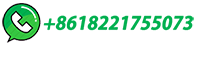
Iron Ore Agglomeration Technologies | IntechOpen
Until the 1950s of the last century, the oxidized iron ores that were loaded into the blast furnace had granulometries within 10 and 120 mm. However, the depletion of high-grade iron ore sources has made necessary the utilization of concentration processes with the purpose of enriching the iron ore. Because of these processes, a fine granulometry is produced, and …
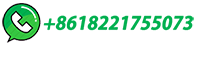
Iron Ore Pelletizing Process: An Overview
The iron ore pelletizing process consists of three main steps: Pelletizing feed preparation and mixing: the raw material (iron ore concentrate, additives —anthracite, dolomite—and binders …
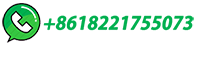
New Paradigms for Iron Ore Pelletization | SpringerLink
The iron ore concentrate used in the starch binder tests was a hematite concentrate rather than a magnetite concentrate . ... but with a few differences. First, the concentrate was dried, de-lumped, and then rehydrated to a known moisture content of 9.75% before binder addition.
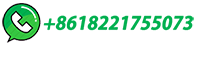
(PDF) Iron Ore Pelletizing Process: An Overview
The iron ore pelletizing process consists of three main steps: 1. Pelletizing feed preparation and mixing: the raw material (iron ore concentrate, additives. — anthracite, dolomite — and ...
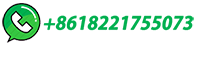
THE GROWING IMPORTANCE OF PELLETIZING FOR IRON ORE MINING AND IRON
The concentration of low-grade iron ores is vital to the continued availability of iron and steel in our everyday lives (Eisele and Kawatra, 2003;Kawatra and Claremboux, 2021a;Zhang et al., 2021).
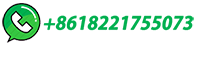
Iron Ore Pelletization: A Critical Review of Processes and
Iron ore pelletization is a critical aspect of the steel manufacturing process, providing a method to utilize fine iron ore particles and beneficiate lower grade ores, which …
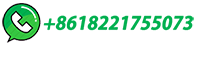
A review of binders in iron ore pelletization
This article reviews the numerous types of binders (both organic and inorganic) that have been considered for iron ore pelletization, including discussion of the binding mechanisms, advantages and limitations of each type, and presentation of actual pelletization results, so that the performance of the various types of binders can be compared ...
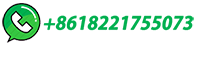
Iron ore pelletization
Iron ore lump, sinter, and pellets comprise the main burden of modern blast furnaces. However, sinter and pellets are now the dominant blast furnace burden, because the natural lump supply has declined dramatically due to depletion of the world's high-grade competent iron ore resources. ... Due to the differences in mineralogy, different ...
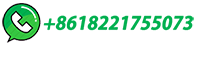
Recycling of steel plant mill scale via iron ore pelletisation process
Abstract. Mill scale is an iron oxide waste generated during steelmaking, casting and rolling. Total generation of mill scale at JSWSL is around 150 t/day and contains 60–70%FeO and 30–35%Fe 2 O 3.To recover the iron, the mill scale must be smelted in a blast furnace or other reduction furnace; however, it is usually too fine to use without previous agglomeration …
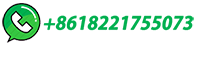
STUDY OF TRANSPORTATION OF IRON ORE OVER …
11. Destination of Iron Ore Transportation for Domestic Use 9.0 11 12. Destination of Iron Ore Transportation for Exports 9.1 12 13. Major Iron Ore exporting ports in India 9.2 12 14. Types of Wagons being used loading of Iron Ore 10.0 12 15. Capabilities & Weaknesses 11.0 13 16. Challenges from new modes of Transport 12.0 15 17.
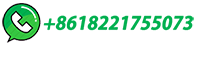
Iron Ore Agglomeration Processes and their Historical
In 1902, W. Job invented the sintering of pyrite cinder and dusty iron ores with addition of coal and air blowing through the bed from bottom upwards (German patent number 137438). In 1905, EJ Savelsberg developed the process of iron ore sintering with the sintering mixture containing coal and coke breeze (German patent number 210742).
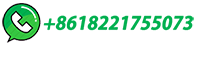
Advances in Sintering and Pellet Technology
Amongst various processes used in agglomeration, sintering and pelletization are widely used in the iron ore industries. About 70% of the blast furnace feed is reporting from the sintering processes. The objective of iron …
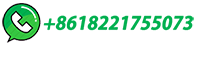
Sintering & Pelletisation – Carbon steel materials
Dr Lu is the Team Leader for Sintering & Pelletisation guiding CSIRO's R&D into iron ore agglomeration and high temperature behaviour of iron ore agglomerates in blast furnaces and alternative ironmaking processes. With …
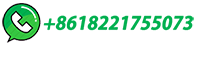
(PDF) COMPARISON OF SINTER AND PELLET USAGE IN AN …
Global iron ore production has grown dramatically in recent years to meet increasing world steel demand, especially in Asia. High grade lump ore resources are being depleted and a greater amount ...
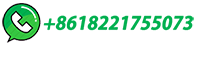
Iron Ore Pelletization: Part I. Fundamentals | Request PDF
This is because various types of iron ore fines have distinct pelletisation ... This work presented an experimental study on the iron ore granulation and sintering using a novel horizontal high ...
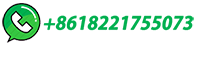
091102 Iron ore
ore) roasting or sintering, including pelletisation' is to be included in the ETS. Table 1 gives an overview of the NACE classification of this Annex I activity. Table 1 Classification of the iron ore industry according to the Annex I of the amended Directive and corresponding activity in NACE Rev. 1.1 classification
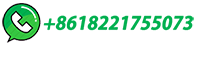