Blast Furnace Process
A blast furnace is a steel cylinder lined with refractory. It operates continuously until the lining wears out, which takes many years to occur. ... Limestone reacts with impurities in the furnace, forming slag, which floats to the top of the furnace vessel. 6. Every hour or so the molten iron is removed and sent on for further processing.
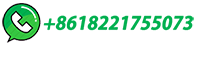
Limestone Processing Equipment
Limestone can be a challenging material to work with. From its varying composition, to its abrasive nature, limestone requires an engineered process solution, combined with heavy-duty equipment. That's why we not only offer …
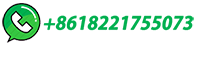
Pig iron
The blast furnace gas that leaves the top of the furnace is a mixture of carbon dioxide, carbon monoxide, hydrogen and nitrogen and has a calorific value between 3,200 and 4,000 kJ/m³. After cleaning, it is used for a …
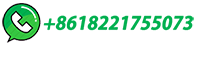
Solved 1 A copper ore has the following proximate analysis
Question: 1 A copper ore has the following proximate analysis: 20%Cu2S, 56% FeS2 and 24% SiO2. It is smelted in a reverberatory furnace using pure limestone as a flux.
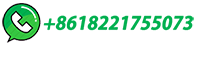
The Effects of Fly Ash, Blast Furnace Slag, and Limestone …
This study investigates the alterations in the ratios of components such as class C fly ash (FA), blast furnace slag (BFS), and waste stone powder (WSP) types of limestone powder (LP) used in the production of geopolymer concrete. These components are meticulously examined concerning the physical and mechanical attributes of …
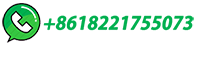
Describing the Use of Limestone in a Blast Furnace
What is the purpose of adding limestone to a blast furnace? (A) The limestone decomposes and the products of that reaction convert impurities into slag. (B) The limestone decomposes, an exothermic reaction, heating up the furnace. (C) The limestone reduces the iron ore to iron.
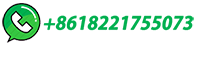
Lime Production Process and Required Equipment | Fote …
3 The practice has proved that a shaft furnace is best for limestone with a size of 40-80mm while a rotary kiln is ideal for limestone with 10-30mm. Fote Company manufactures various crushing and mining equipment over fourty years, if you need any machine to process limestone, ...
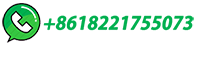
IGCSE CHEMISTRY BLAST FURNACE Flashcards | Quizlet
Study with Quizlet and memorize flashcards containing terms like Contains three things, Step 1, Step 2 and more.
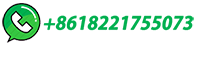
Ironmaking 101 – From Ore to Iron with Blast Furnaces
Ironmaking Blast Furnace. Iron is made by reacting iron ore (iron oxide and impurities), coke (a reductant) and limestone (CaCO 3) in a blast furnace.. Iron ores with lower iron content such as taconite are first processed to concentrate the iron level and drive off volatile impurities.
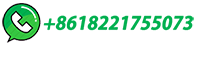
Hiking the Limestone Loop at Canoe Creek State Park in …
The limestone quarried here was an instrumental part of Pennsylvania's industrial history and was used in the iron and steel furnaces throughout the state. The limestone kilns in Canoe Creek State Park are beautiful and historic.
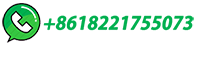
Chemistry of the Ironmaking by Blast Furnace Process
A considerable improvement in the furnace operations is achieved when 'self-fluxing' agglomerates of iron-ore concentrates are the principal iron-bearing charge to the furnace. Limestone and dolomite can be added to the feed of sintering machines and pelletizing furnaces.
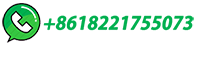
What is a cupola furnace and how does it work?
Cupola Furnace is a type of melting furnace commonly used in foundries to make cast iron from pig iron charge which consists of pig iron, coke, limestone (flux) and scrap iron. The word "Cupola" means "small dome". The name of …
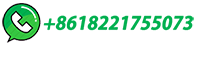
23.3: Metallurgy of Iron and Steel
Figure (PageIndex{1}): A Blast Furnace for Converting Iron Oxides to Iron Metal. (a) The furnace is charged with alternating layers of iron ore (largely Fe 2 O 3) and a mixture of coke (C) and limestone (CaCO 3). Blasting hot air into the mixture from the bottom causes it to ignite, producing CO and raising the temperature of the lower part ...
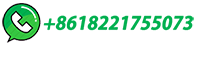
Furnace Charging
Electric Furnace Charging; Cupola Charging; Pusher Charging; Bucket Charging; Bin Tilter Charging; Coke and Limestone Hopper Charging; Foundry Projects Limited offer bespoke mechanical handling equipment for charging and feeding materials into furnaces.
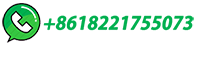
The Benefits of Lime Injection in the Electric Arc Furnace
Lime injection now provides a reliable technology for steelmakers to control y slag, reduce waste disposal, improve safety and save electrical energy. DENSE VS. DILUTE …
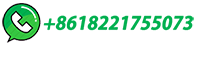
New PFR lime kiln process with blast furnace gas and …
MAERZ OFENBAU AG New PFR lime kiln process with blast furnace gas and oxygen. Production of high reactive lime is now possible with inexpensive blast furnace gas. . A …
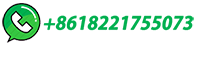
A Comprehensive Review on the Ground Granulated Blast …
The blast furnace is supplied with a carefully regulated combination of limestone, iron ore and coke. When limestone, iron ore and coke are melted together in …
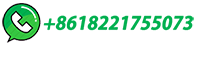
Improving the Heating System and Structure of Shaft …
In Russia, limestone is mainly roasted in rotary fur naces (around 30% of output), shaft furnaces with gas and fueloil heating (~35%), and shaft furnaces fueled by coke and coal (15–20%). The remaining lime is produced in fluidizedbed furnaces (3–4%), parallel flow/counterflow regenerative and annular furnaces
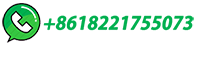
Burnout Furnace Supplier in Rajkot, Limestone Scrubber …
Seven Seas Enterprise as a Manufacturer and Supplier of Burnout Furnace, Limestone Scrubber at Best Prices. Our office is Based in Rajkot, Gujarat, India. Get contact detail in our website.
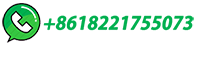
sbm/sbm furnace limestone machine méxico.md at main
Contribute to sili2023/sbm development by creating an account on GitHub.
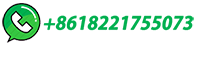
Blast Furnace Slag Cement Clinker Production Using Limestone …
The BFS is also solid, although in real-world applications, the BFS is molten. As a result, the goals of this study are to determine the best blast furnace slag to limestone powder ratio for producing cement clinker and to determine the minimum temperature required for processing limestone and blast furnace slag to make cement …
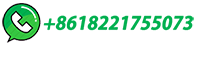
Blast Furnace: Introduction, Definition, Construction, Working
This article comprehensively discusses and elaborates the information regarding blast furnace, its construction details, including its main parts and their working phenomenon and function. This article also highlights the application of these furnaces for its practical use.
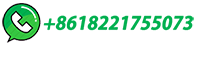
The Role of Limestone in the Blast Furnace Process
Limestone plays a crucial role in the blast furnace process by acting as a flux to remove impurities from the raw materials and form a slag that can be easily …
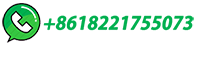
Cupola Furnace : Principle,Construction, Working, …
Cupola Furnace is a melting device used to melt cast iron, Ni-resist iron, and some bronzes and It is used in Foundries.The cupola can be made of any size and the size of the cupola is measured in diameters which range from 1.5 to 13 feet.
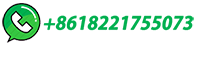
Limestone and Dolomite and their Use in Iron and Steel Plant
In ironmaking, limestone and dolomite are used in the production of sinter, pellets, and directly in blast furnace as fluxing materials. In case of steelmaking limestone and dolomite are used as lime or calcined dolomite both in the primary steelmaking (basic oxygen furnace, electric arc furnace), and in the secondary steel making processes.
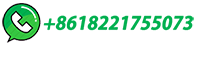
Limestone in Glassmaking: What You Need to Know.
Limestone is an essential ingredient in glassmaking. But why do you need it and what type is best for your process? In this article, we explain the fundamentals. ... Contemporary manufacturing technologies centered around energy efficient electrical furnaces, improved energy consumption, reduced emissions, and national energy security will ...
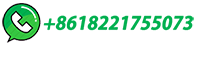
Solved Three aggregates are blended by weight in the
Question: Three aggregates are blended by weight in the following percentages:50% crushed limestone, bulk dry specific gravity: 2.70230% blast furnace slag, bulk dry specific gravity: 2.33120% natural sand, bulk dry specific gravity: 2.600Calculate the specific gravity of the blend.
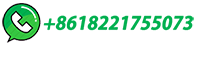
Solved What mass of limestone, in kilograms, should be …
What mass of limestone, in kilograms, should be added for 1.00 kilogram of iron ore processed in a blast furnace if the limestone is 95.5 % CaCO3 and the iron ore contains 8.24 % SiO2? The resulting product, calcium silicate, has the formula CaSiO3.
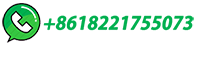
The Sintering Process of Iron Ore Fines – IspatGuru
The Sintering Process of Iron Ore Fines. satyendra; March 9, 2013; 8 Comments ; flux sinter, Iron ore fines, self fluxing sinter, sinter, sinter machines, Stright line machine. circular machine, super fluxed sinter,; The Sintering Process of Iron Ore Fines. Sintering plants are normally associated with the production of hot metal in blast furnaces in …
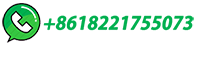
Pig Iron Manufacturing Process
An experiment was made, extending over several hours, to note the effect upon the pig steel of continuous charging and tapping rather than intermittent operation of the furnace. In addition to hematite, limestone, and coke a …
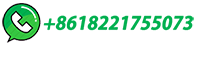