why coke is added to iron ore for pelletizing
why coke is added to iron ore for pelletizing. Iron ore - Wikipedia, the free encyclopedia . Iron ores are rocks and minerals from which metallic iron can be economically extracted.
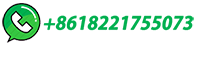
Why to Pelletizing or Briquetting iron bearing mineral?
Why iron bearing materials should be pelltized or briquetted before they are introduced to the blast furnace?
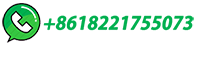
Reduction of Iron Ore Pellets, Sinter, and Lump Ore …
coke and iron-bearing materials separately, which leads to a lay-ered structure.The iron-bearing materials consist ofironorepel-lets, lump ore, and sinter. When the charge material descends, it ... ore, and iron ore pellet is presented as R ¼ ...
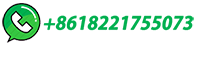
Coke addition in the iron-ore pelletizing process
Iron ore pellets with high coke addition can be achieved if sintering and coke combustion is optimized in terms of pellet particle size. Coarser particle size is …
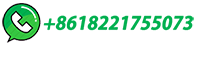
Assessment of iron ore pellets production using two …
Iron ore pelletizing plant consumes coal, pet coke, oil and natural gas to get the required chemistry, physical and metallurgical properties for iron ore pellets, …
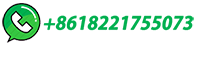
Method of Making Iron Ore Pellets with a Carbon Core …
The pellet making method was studied for production of iron ore pellets with a carbon core. The pellets are to be fired in a sintering machine to produce sintered ores containing carbonaceous ...
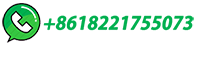
EVOLUTION AND GROWTH OF IRON ORE PELLETIZING
In the last years, pelletizing has been playing an important role for iron ore mining and ironmaking. Some factors have contributed to this fact like as: depletion of high-grade iron ore reserves ...
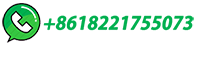
A comparative study of pellets, sinter and mixed ferrous …
The iron ore pellet bed and ferrous burden (pellet and sinter mixture) are quenched at 1480 and 1505°C, respectively. In order to investigate the internal state of the sinter bed at high temperature, it is quenched at 1550°C.
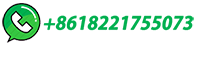
Utilization of Pellet Fines in the Iron Ore Sintering Process
An iron ore blend was prepared by mixing the iron ore fines with the required proportion of pellet fines. A small pile was prepared by layering the iron ore blend, coke breeze, flux and return fines on a weight basis, according to the proportions mentioned in Table 1. After proper mixing, these raw materials were transferred to the …
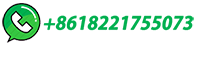
Direct Reduction of Iron Ore Pellets by Using CO/CO
Reduction of iron ore pellets by using CO/CO 2 and pure CO gases were conducted in a high temperature thermogravimetric (HTG) furnace. The schematic …
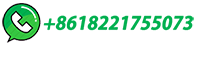
A comparative study of pellets, sinter and mixed ferrous …
ABSTRACT. Physicochemical behaviour of the pellets, sinters and its mixture (60% pellets: 40% sinter) is investigated by a series of smelting and quenching …
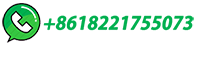
Iron Ore Pelletizing Process: An Overview
However, the content of iron in ore deposits has deteriorated and low-grade iron ore has been processed. The fines resulting from the concentration process must be …
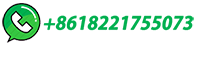
DR-Grade Iron Ore Pellets
The creativity of DR plant operators, ingenuity of process suppliers, and expertise of iron ore pellet producers assure DRI products keep pace with demand.
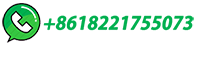
Comparison of Sinter and Pellet Usage in an Integrated …
Key words: Iron ore; Pellet feed; Sintering; Pelletizing; Blast furnace. 1 Technical contribution to the 43rd Ironmaking and Raw Materials Seminar, ... the ash content of coke, and the added fluxes it follows that utilizing a lower acid gangue material will produce less slag per ton of burden or hot
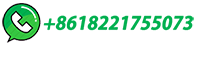
Reduction Behavior of Iron Ore Pellets with Simulated Coke …
In this study, iron ore pellets were isothermally reduced with simulated original and reformed coke oven gas (RCOG) at 700–980°C. The results were …
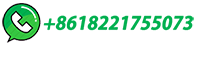
THE GROWING IMPORTANCE OF PELLETIZING FOR IRON ORE MINING AND IRON
The binder is an important additive widely applied in pelletizing iron ore concentrates, making iron ore pellets available as feedstocks for blast furnace ironmaking or direct reduction processes ...
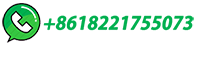
A comparison of the shrinking core model and the grain …
In that context, the current study is specifically to reassess the single particle combustion models in the iron ore pellet indurator simulation. As the feed of blast furnace, the typical iron ore pellet is made of mostly iron oxide mixed with coke, and limestone with water.
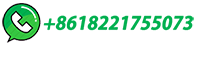
Applications of Iron Ore Pellets
Iron ore is the most critical mineral resource for any Iron and Steel Industry. Know about the Applications of Iron Ore Pellets & Iron ore Pelletization Process.
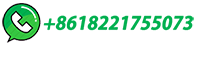
Effect of adding limestone on the metallurgical properties of iron ore …
In this study, the focus was placed on limestone as an additive in the production of iron ore pellets and its effect on pellet properties. Some researchers have already studied the effect of basicity on the properties of iron ore pellets.
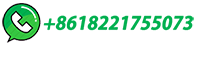
Iron processing
Iron processing - Ores, Smelting, Refining: Iron ores occur in igneous, metamorphic (transformed), or sedimentary rocks in a variety of geologic environments. Most are sedimentary, but many have been changed by weathering, and so their precise origin is difficult to determine. The most widely distributed iron-bearing minerals are oxides, and …
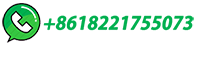
Use of Iron Ore Pellets in Blast Furnace Burden – IspatGuru
Use of Iron Ore Pellets in Blast Furnace Burden. satyendra; June 13, 2014; 0 Comments ; BF burden, blast furnace, Hot metal, Iron ore, iron ore pellets, sinter,; Use of Iron Ore Pellets in Blast Furnace Burden Pelletizing is a process that involves mixing very finely ground particles of iron ore fines of size less than 200 mesh with additives like …
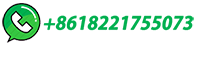
Iron Ore Pelletizing Process: An Overview
Iron ore pellet making process involves balling of green mix (containing iron ore fines, binder, limestone and coke) using rotating disk or drum to produce green …
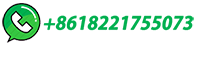
Effectiveness of Organic Binders for Iron Ore …
the major concerns of the iron ore pelletizing industry (19). Standardized quality acceptance tests and specifications for organic binders are currently nonexistent. Quality-control tests with the binder ingredient alone, as well as when mixed with iron ore, are needed. The tests must be relatively simple, fast, reproducible, and
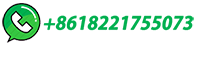
Iron Ore Agglomeration Technologies | IntechOpen
Until the 1950s of the last century, the oxidized iron ores that were loaded into the blast furnace had granulometries within 10 and 120 mm. However, the depletion of high-grade iron ore sources has made necessary the utilization of concentration processes with the purpose of enriching the iron ore. Because of these processes, a fine …
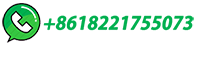
Iron Ore Pelletizing
If the ore is a Hematite ore, coke or anthracite coal can be added to the mix to work as an internal fuel to help fire the pellets. This mixture is blended together in a mixer and fed to balling discs or drums to produce green pellets of size typically about 9-16mm.
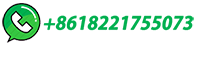
What Are Iron Ore Pellets and How to Make Them? | Fote …
How to Pelletize Iron Ore? (The Complete Guide) 1. Preprocessing Before pelletizing, iron ore has to go through a pretreatment stage. Generally, the low-grade iron ore raw ore needs a beneficiation process to upgrade into iron fines that suit pelletization.
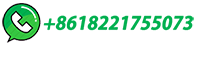
Preparation of Iron Ore Micro-pellets and Their Effect on …
2.2 Preparation of Micro-pellets. In the pelletizing phase, the preparation and characterization of green micro-pellets was attempted before sintering process. After homogenization of the sample (iron ore concentrate), the first step was to determine chemistry, size analysis, and specific surface area.
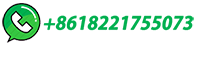
Pelletization
The main disadvantage of clays and other binders based on silicate minerals is that they add silica to the finished pellet. Since the purpose of iron ore processing is to remove silicate minerals from the ore, adding silicates back in the form of a binder is counterproductive.
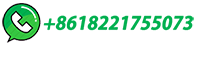
Iron Ore Pelletizing Process: An Overview
The iron ore pelletizing process consists of three main steps: Pelletizing feed preparation and mixing: the raw material (iron ore concentrate, …
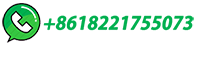
Reduction of Iron Ore Pellets, Sinter, and Lump Ore under …
A – (BF) is the dominant process for making iron in the world. Herein, the reducibility of the iron ore pellet, sinter, and lump ore in the BF shaft is focused on. The simulated BF atmosphere in four...
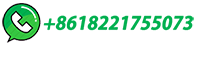