(Video) How Cement Is Made
Cement is one of the most popular building materials in the world and a key ingredient in concrete. Read our article to learn how it's produced.
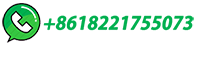
Cement Clinker Calcination in Cement Production Process | AGICO Cement
The cement clinker calcination is an important step in the cement production process. It mainly occurs in cement kiln and can be roughly divided into six reaction stages, namely drying, preheating, chemical decomposition, exothermic reaction, sintering and cooling.
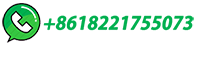
Energy Use – Cement
Energy Use. A cement manufacturing plant requires significant amounts of energy, mainly in the form of heat, to produce clinker. Significant amounts of electricity are then required during the milling (grinding) of clinker and other constituents to produce cement – the main binder in concrete.
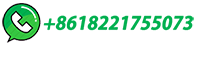
Comprehensive Guide to Cement Kilns: Processes, Types, …
A cement kiln is a type of industrial furnace used to heat raw materials such as limestone, clay, and other additives to high temperatures to produce clinker. The clinker is then ground to produce cement, a key binding material in construction.
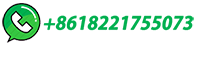
Here's How a Concrete Batch Plant Works | Concrete …
A concrete batch plant works by storing the various constituent elements of concrete (water, cement, aggregates, and additives) in suitable tanks and then manufacturing custom concrete at the request of each customer. Indeed, a concrete batch plant is an installation designed to produce concrete in large quantities.
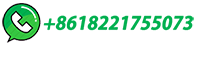
What Is Concrete Batching Plant? Work Procedure, Types, …
A concrete batching plant, also known as a concrete mixing plant, is a machine that combines various ingredients to form concrete. It plays a crucial role in modern construction projects, providing ready-mixed concrete for buildings, bridges, roads, and other infrastructure.
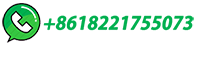
Everything you need to know about Automation …
Everything you need to know about Automation and Optimization in the Cement Plant . ... Using Expert Systems in cement process applications is, by now, a well-established procedure. The objective is to allow less …
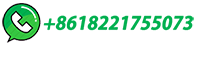
Stormwater Best Management Practices: Concrete …
produces glue that binds the aggregates together to make concrete. Concrete washout. After concrete is poured at a construction site, the chutes of ... mixed concrete plants x: Returned back to a surface water, ... procedure is used to perform the washout from the top down: (1) after the pour is completed, the driver attaches the extension ...
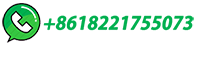
Inventory Management in Cement Industry: Best Practices …
Technology modernises cement inventory management through automation, data analytics, and real-time monitoring, enhancing efficiency, accuracy, and responsiveness to market dynamics. How can cement plants minimise the risk of supply chain disruptions affecting inventory levels?
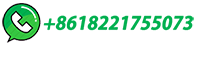
How Cement is Made
The cement manufacturing process is a complex one involving several steps. Each step in the process plays an important role in the overall quality of the finished product. In this …
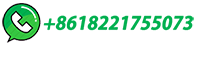
A review of low-carbon technologies and projects for the global cement
Most cement plants in India are located in dry and hot areas with large amounts of solar radiation and unshaded arid land. This situation provides the optimal conditions for solar power plants. Some cement plants have attempted to generate solar power, as one company has established its target of changing to renewable …
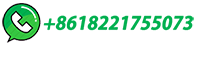
How Much Does It Cost To Start A Cement Plant?
Cement plant manufacturer. If you are ready to buy a cement plant, it is suggested to choose a cement plant manufacturer with a large scale and strong strength, which will provide full cement equipment and service, and also ensure quality and …
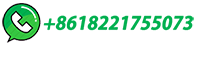
The Cement Plant Operations Handbook
Philip A. Alsop, PhD. perations Handbook SEVENTH EDITIONThe Cement Plant Operations Handbook is a concise, practical guide to cement manufacturing and is the standard reference used by. lant operations personnel worldwide.Providing a …
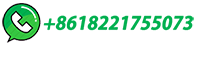
Cement
The webpage explores the challenges and opportunities for reducing CO2 emissions from cement production, a major source of global energy demand and emissions. It presents the latest data, analysis and policies from the IEA on cement.
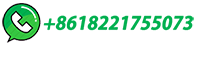
CEMENT PRODUCTION AND QUALITY CONTROL A. …
The whole process of cement manufacturing in Messebo Cement plant which consists of ... to produce PLC type of cement, (Special clinker + Gypsum) to produce LHHS type of cement. After grinding, the finished product ... This procedure is used for testing of raw materials, finished, and semi-finished ...
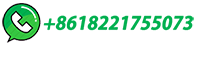
Safety in Cement Plant
Safety in Cement Plant. ... Health procedures require eye protection, breathing masks and full cover clothing. • Used Oils: Used oils will need to be checked for PCB content, which will determine precise precautions required. Requirements are generally similar to those for solvents, with similar health precautions. ...
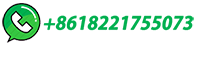
Cement Hazards and Controls Health Risks and Precautions …
But anyone who uses or supervises the use of portland cement should know its health hazards and the safe working procedures necessary to minimize exposure. This article outlines those hazards and makes recommendations on how to use cement safely.
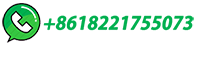
Manufacturing Process
How do we produce Cement? The manufacturing of cement at our Plant involves the selection of best quality raw materials and employing the Dry Process; major portion of ingredients consists of Limestone and Clay.
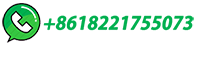
Manufacture of Cement- Materials and Manufacturing …
Manufacturing of cement involves various raw materials and processes. Each process is explained chemical reactions for manufacture of Portland Cement.
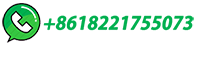
PPC Cement Manufacturing Process
Portland pozzolana cement is also known as PPC cement. What is the PPC cement manufacturing process? AGICO offers high-quality Portland pozzolana cement plants and different Portland pozzolana cement equipment.
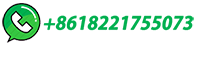
How Is Cement Produced in Cement Plants | Cement Making …
The dry process is the most popular industrial cement making process which is widely adopted by cement plants all over the world for its great advantages in energy saving …
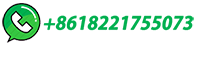
Everything To Know About Concrete Plants
Before learning how concrete plants functions, knowing the fundamentals of a batching plant"s construction is essential, you may put things like aggregates, sand, water, cement, ... Each step in the procedures above is performed meticulously and well-organised. There is a time limit attached to every action.
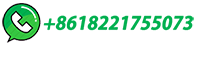
All Stages of Cement Manufacturing from The Cement …
As a result, they make good, perfect-quality cement that will gradually be utilized to manufacture concrete by contractors & "ready-mix" industries. A cement manufacturing facility is an extension of a cement mining process, as cement plants are usually central to the minerals needed to make the cement. This reduces transportation expenses and ...
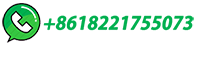
Cement Production Process | Cement Manufacturing
In general, a full cement production process includes the stone crushing, raw mill process, clinker process, and cement grinding process, cement packing …
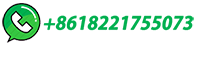
How To Make Cement – Step by Step Guide
Cement manufacturing is not as complex as it seems to be. To make cement, industrial plants follow step by step systematic process. Here is a brief guide on how to make …
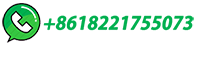
All about Cement
The raw materials needed to produce cement (calcium carbonate, silica, alumina and iron ore) are generally extracted from limestone rock, chalk, shale or clay. ... (as it is known) is transported to the plant where it is stored. Step 2: Raw Grinding and Burning. Grinding produces a fine powder, known as raw meal, which is preheated and then ...
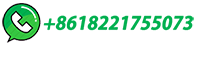
What is a Concrete Plant? (The Ultimate Guide)
Concrete is one of the most important building materials in the world, and concrete plants are the factories that produce it. In this article, we'll take a closer look at what a concrete plant is, how it works, and the different types of …
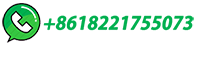
The cement kiln
This reduces the capital costs of a new cement plant. A dry process kiln might be only 70m long and 6m wide but produce a similar quantity of clinker (usually measured in tonnes per day) as a wet process kiln of the same diameter but 200m in length. For the same output, a dry process kiln without a precalciner would be shorter than a wet ...
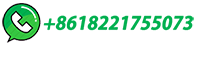
Cement Manufacturing Machine
Choose the right cement manufacturing machine is an important influence factor to produce high-quality cement. The cement making machine frequently used in cement plants includes cement rotary kiln, shaft kiln, cement vertical mill, cement ball mill, cement roller press, etc.
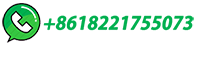
Cement Plant: The Manufacturing Process 4 5
Cement Plant: The Manufacturing Process. 4 The kiln feed is blasted in a 5 The clinker is mixed cement kiln at a temperature with additives, such of 1450oC, causing clinkering …
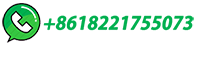