Solved suppose an industrial control chemist analyzes a
Scrap metal precipitates out,and pure copper mical reaction: Fe(s) + CuSO4(aq) ? Cu(s) + FeSO4(aq) processing plant in the following way. He adds powdered iron to a 400. ml. Suppose an industrial quality-control chemist analyzes a sample from a copper copper(I) sulfate sample from the plant until no more copper will precipitate.
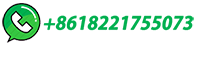
Metallurgical Accounting Formulas | Concentration and …
The ratios of concentration, Kcu and Kzn are those for the copper and zinc concentrates, respectively, with Rcu and Rzn the percentage recoveries of the metals in their corresponding concentrates. As follows:
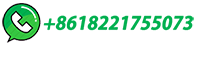
The Extraction of Copper
Most of the sulfur in the chalcopyrite turns into sulfur dioxide gas. This is used to make sulfuric acid via the Contact Process. An overall equation for this …
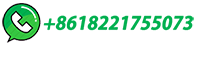
Gold processing
Gold processing - Mining, Concentrating, Refining: The nature of the ore deposit determines the mining and mineral processing techniques applied. Oxide ore deposits are frequently of such low grade (e.g., 3 to 10 parts per million) that extensive mineral processing cannot economically be justified. In this case they are merely shattered by …
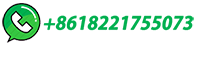
Key factors impacting treatment efficiency in actual copper …
The experimental conditions used were laboratory temperature 294.65 K, temperature of copper mineral processing wastewater 296.15 K, pH 7, the initial COD 138.4 mg/L, ... The substance can generate an ammonia-like substance in the ozone oxidation process, which makes the concentration of ammonia nitrogen rise . Since other nitrogenous organic ...
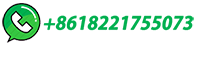
Copper processing
Copper processing - Roasting, Smelting, Converting: Once a concentrate has been produced containing copper and other metals of value (such as gold and silver), the next step is to remove impurity elements. In older …
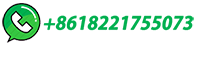
Copper Overview: From the Ore to the Applications – A Case …
Therefore, the process used to obtain the matte is a copper concentration process in this phase. There are several elements that accompany the copper that are …
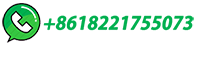
Sustainable copper production processes from mine to cathode copper
Sustainable copper production processes from mine to cathode copper: some process selection considerations. April 2011; ... Energy consumption and greenhouse gas emissions in copper concentration ...
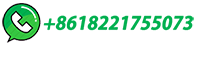
From Ore to Finished Product
From its original home buried underground in a mine to its use in a finished product such as wire or pipe, copper passes through a number of stages. When it is recycled it can pass through some over and over again.
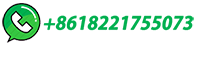
Novel Concentration Process for Platinum Group Metals in …
Finally, in the flotation process, the copper sulfide-coated PGMs are separated from the hydrophilic ceramic components of the autocatalyst and recovered in the froth. Cu was selected as the plating material because the flotation process for copper sulfide ores is well established in the mining industry.
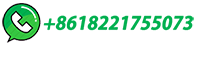
Copper Refining: From Ore to Market
Mined rock typically contains less than 1 percent copper. That means to become a market-ready copper product, it must undergo a variety of physical and chemical processing steps. After copper ...
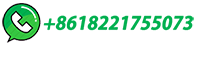
Copper Ore Processing Plants, Flow And Equipment
The main beneficiation process of copper ore is flotation, contact us to customize copper ore processing plants and equipment. get a quote now!
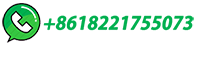
Designs of new operating copper processing plants: process …
The article describes the largest operating processing plants for lowgrade copper sulphide ores of our time: 10 plants using the semi-autogenous grinding (SAG) technology and 10 plants using high ...
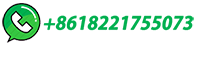
Solved One way in which the useful metal copper is …
One way in which the useful metal copper is produced is by dissolving the mineral azurite, which contains copper (II) carbonate, in concentrated sulfuric acid. The sulfuric acid reacts with the copper (II) carbonate to produce a blue solution of copper (II) sulfate. Scrap iron is then added to this solution, and pure copper metal ...
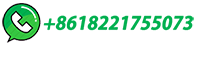
Achieving step change performance in copper ore …
Copper concentrate commands a price dependent on its grade, or copper content, which typically lies in the range 25 – 35%. However, penalties are imposed for impurities that …
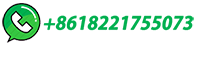
Solved One way in which the useful metal copper is …
Question: One way in which the useful metal copper is produced is by dissolving the mineral azurite, which contains copper(II) carbonate, in concentrated sulfuric acid.
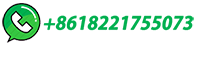
Extraction of Copper: Detailed Process
The process of extraction of copper from its ores and preparing copper metal or chemical compounds for use in various goods is known as copper processing.
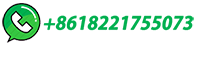
(PDF) Processing of Complex Materials in the Copper …
With the gradual decrease in the grade of copper ores being processed, copper concentrates have become more complex with higher impurity and gangue content.
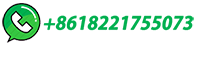
Current Status of Copper-Ore Processing: A Review
INTRODUCTION. According to the International Wrought Copper Council, copper is chiefly used in building construction, equipment manufacturing, and …
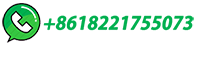
17.3: Concentration Effects and the Nernst Equation
17.3: Concentration Effects and the Nernst Equation ... [Cu 2 +] in the cathode compartment decreases as metallic copper is deposited on the electrode. During this process, the ratio Q = [Zn 2 +]/[Cu 2 +] steadily increases, and the cell voltage therefore steadily decreases.
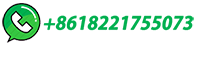
Copper Processing | Multotec
Copper processing uses physical, mechanical and / or chemical methods to convert run-of-mine (ROM) copper ore to high-quality, ... Due to the decreasing concentration of copper in ores, this is an important step to decrease the volume of material and to increase the grade of copper in the ore.
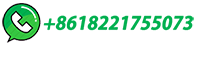
Recent Advances in Copper Ore Processing and Extraction
In this Special Issue, recent advances in copper ore processing and extraction are discussed, focusing on: innovations in hydrometallurgical, pyrometallurgical, electrometallurgical, and pre-concentration technologies; improving copper ore resource efficiency through application of integrated approaches.
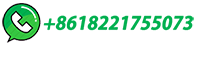
Acid Leaching
The process proceeds from tank to tank with a continual decrease in acid strength and increase in copper concentration until it is finally withdrawn as pregnant solution from the charge which has had its first leach cycle.
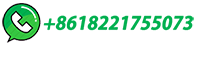
Froth Flotation Process
The Froth Flotation Process is about taking advantage of the natural hydrophobicity of liberated (well ground) minerals/metals and making/playing on making them hydrophobic (water-repel) individually to carefully separate them from one another and the slurry they are in. For this purpose we use chemicals/reagents: Frothers (MIBC) is …
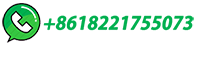
Recent Advances in Copper Ore Processing and Extraction
In this Special Issue, recent advances in copper ore processing and extraction are discussed, focusing on: innovations in hydrometallurgical, …
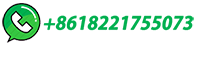
Copper Mining and Processing: Processing Copper Ores
Copper processing is a complicated process that begins with mining of the ore (less than 1% copper) and ends with sheets of 99.99% pure copper called cathodes, which will ultimately be made into products for everyday use.The most common types of ore, copper oxide and copper sulfide, undergo two different processes, hydrometallurgy and …
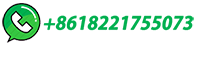
Optimizing the Rougher Flotation Process of Copper Ore
We searched for the variables that affect the copper law and metallurgical recovery. However, only relationships between these variables and the fine copper law were found at the end of the copper concentration process.
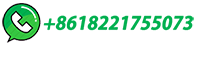
Extraction Of Copper | Mining, Concentration, Smelting
Understand The Extraction Of Copper, steps involved like mining, smelting copper, Concentration of Ore Chalcopyrite by Froth Flotation method, Reactions Involved and more with BYJU'S.
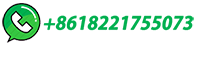
A Comprehensive Guide to Copper Ore Processing Lines …
However, the journey from raw copper ore to refined copper metal involves a series of intricate processes, necessitating specialized equipment and efficient processing lines.
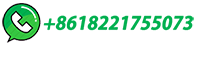
Flotation | Mineral Processing, Separation & Beneficiation
The flotation process was developed on a commercial scale early in the 20th century to remove very fine mineral particles that formerly had gone to waste in gravity concentration plants. Flotation has now become the most widely used process for extracting many minerals from their ores.
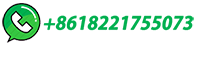