A promising physical method for recovery of LiCoO
Flotation is a physical separation method based on the wettability difference of particle surface [22]. Cathode material (LiCoO 2) belongs to the ionic crystal with strong polarity and good hydrophilicity. In the flotation process, LiCoO 2 is completely wetted by water and then sinks into the bottom of the flotation cell. Anode material ...
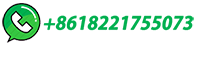
Characteristics of Spent Lithium Ion Batteries and Their …
The strive for more sustainability boosts the production of Lithium-ion batteries (LIBs) (Al-Thyabat et al. 2013). ... Since flotation is the most common processing method successfully applied to the physical separation of minerals in the mining industry, researchers have given a lot of attention to this area. The success of recycling by ...
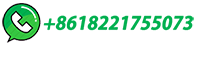
Processes | RYNACO
Our lithium ores undergo crushing processes adhering to European refining standards, facilitated by our state-of-the-art crushing equipment. Moreover, our on-site laboratory, certified ISO 9001:2015, empowers us to autonomously verify the entirety of our production, ensuring rigorous quality control throughout the process.
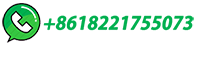
Lithium Mineral (spodumene, petalite and …
ZJH minerals supply the whole set of equipment for Lithium Mineral Flotation, most notably for spodumene. Spodumene theoretically contains 8.03% Li2O and therefore the production of this mineral is greatly increasing, especially …
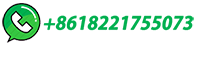
Goulamina Project Details – Leo Lithium Limited
The Goulamina Lithium Project located in southern Mali, approximately 150km south of the country's capital of Bamako, is one of the largest undeveloped hard rock lithium deposits globally. ... Primary jaw crusher and cone crusher circuit; Milling: ... Flotation: Multi-stage flotation circuit; Community Engagement. Leo Lithium has proposed a ...
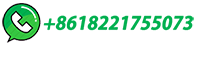
Improving your Lithium Flotation Process
the megatrends of the lithium market, the beneficiation of lithium minerals from hard rock ores, Clariant's capabilities for lithium processing? Speaker: M Suresh Raju. Global Tech Manager in IM, Clariant. Tim Walsh. Development Scientist, Clariant. Wagner Silva. Global Head of Technology, Clariant. Event on demand available: Register to get access
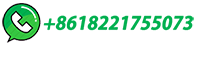
The Most Effective Lithium Ore Processing …
Lepidolite mostly uses positive flotation, while spodumene ore can be used for both positive and reverse flotation. 1.1 Lithium ore positive flotation method. Add strong alkali (such as sodium hydroxide or sodium carbonate) for …
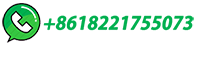
HARD ROCK LITHIUM PROCESSING
%PDF-1.4 %âãÏÓ 296 0 obj > endobj xref 296 37 0000000016 00000 n 0000001546 00000 n 0000001693 00000 n 0000002147 00000 n 0000002627 00000 n 0000003247 00000 n 0000003361 00000 n 0000003473 00000 n 0000003850 00000 n 0000004282 00000 n 0000004369 00000 n 0000004939 00000 n 0000005590 00000 n 0000007435 00000 n …
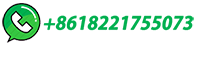
Nigeria's largest lithium processing plant unveiled in …
President Bola Tinubu has welcomed the unveiling of a lithium processing plant with an average capacity to produce about 4,000 metric tonnes daily. The plant, situated in Nasarawa State, was built ...
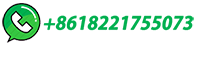
Processing Technology | Cornish Lithium Plc.
The process is undertaken at atmospheric pressure and modest temperature, followed by a series of impurity removal steps at progressively higher pH levels and the subsequent precipitation of lithium carbonate. The process contrasts …
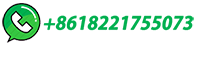
Grade-recovery modelling and optimization of the froth flotation …
Section snippets Material. About 50 kg sample of lepidolite run-of-mine ore (80% passing 14.3 mm), kindly supplied by Felmica Minerais Industriais, S.A. (MOTA® Ceramic Solutions), was employed in this study.For the flotation tests, the run-of-mine ore was finely ground to a particle size < 500 μm (77% passing 350 μm), through successive stages of …
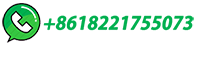
Silver Ore Flotation Process, Equipment
Silver is often associated with lead-zinc ore, copper ore, gold ore, and limonite, and is mainly produced by flotation.The silver intercalation in its silver-bearing minerals is fine and complex in size, and combined beneficiation methods such as flotation-cyanidation and gravity separation-flotation are often used.. JXSC will customize complete silver ore processing plant and …
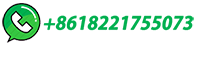
Characteristics of Spent Lithium Ion Batteries and Their …
The method is widely used for treating metallic and non-metallic ores, and it is adaptable to a broad range of mineral separations [39,40]. Although froth flotation is a relatively nascent ...
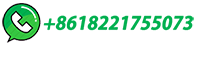
Lithium ore flotation process
The beneficiation method of lithium ore is based on the mineral properties of lithium ore, mainly the physical, chemical or physicochemical properties of different minerals, using different methods to separate lithium …
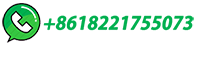
Lithium Spodumene Flotation Process and Reagents
The flotation process of lithium spodumene involves separating it from other impurities to increase the lithium grade and recovery. ... A hydraulic cone crusher is a common type of ore-crushing ...
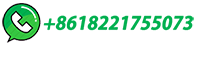
Recovery of LiCoO2 and graphite from spent lithium-ion …
In this paper, a Fenton reagent assisted flotation process is developed to recover valuable electrode materials LiCoO 2 and graphite from spent lithium-ion batteries (LiBs). At room temperature, effect of key parameters for Fenton reaction such as the ratios of H 2 O 2 /Fe 2+ (40–280) and liquid-solid (25–100) are investigated to determine the most efficient …
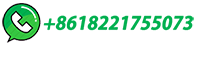
Recovery of lithium from spodumene-bearing pegmatites
The entire requirement of lithium and its compounds in India is exclusively fulfilled through imports. Nevertheless, the possibility of exploring the Amareshwar-based spodumene-bearing pegmatites for commercial implications was enumerated for the first time by Sadashivaiah et al. [30].The Amareshwar area is about 14 km west of the Hutti Gold Mines in Raichur …
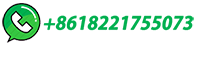
Bubbles to batteries: A review of froth flotation for …
Lithium-ion batteries (LiBs) have been consumed exponentially due to the rapid growth of electric vehicles and electronics. Efficient recycling of spent LiBs is crucial for sustainability; however, major current technologies have disregarded froth flotation which has been recently introduced as an effective separation method and drawn extensive attention in …
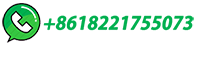
Lithium Processing Plant
Add sodium hydroxide and calcium ions to the ore for activation, and then use fatty acid soap to mix flotation spodumene-beryl, and use sodium carbonate, sodium hydroxide and acid, alkaline water glass to heat the mixed …
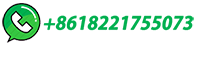
Small Scale LITHIUM Mining Flotation Plants From …
With the addition of a simple crusher and impactor to obtain the granular start mineral size, the plant is virtually ready to go. Available in variants of 1.5, 5, 10 and 20tph, the APT Lithium recovery plant is highly simple, cost …
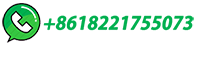
Lithium Mineral (spodumene, petalite and lepidolite) Flotation
ZJH minerals supply the whole set of equipment for Lithium Mineral Flotation, most notably for spodumene. Spodumene theoretically contains 8.03% Li2O and therefore the production of this mineral is greatly increasing, especially demand for electric vehicle batteries. The raw lithium ore is crushed by 3 stage of crushing process.
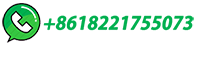
Research Status of Spodumene Flotation: A Review: Mineral Processing …
Spodumene is one of the important lithium resources, so it is of great significance to concentrate it. Beneficiation methods of spodumene include magnetic separation, gravity separation, and flotation. Since the major gangue minerals of spodumene are quartz and feldspar, flotation becomes the most important way to concentrate spodumene.
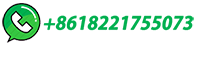
Hard Rock Spodumene Lithium Processing | Saltworks …
In step 1, to convert spodumene into lithium sulfate (Li 2 SO 4), the raw ore is crushed and separated both mechanically and via floatation.Next, the concentrate undergoes energy- and chemically intensive hot acid-roasting. This process (as shown in Figure 1 below) sees concentrated spodumene powder roasted at 1050°C, cooled, mixed with sulfuric acid, …
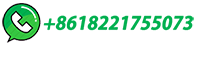
A contribution to understanding the flotation behavior of lithium …
The battery active powder sample (0.5 g) was suspended in a 100 ml cuvette by stirring at 600 min-1 for 30 s. To avoid the bursting of the bubble during stirring stress the needle was silanized beforehand by using the method developed by Ditscherlein et al. [9].After 30 s stirring and sedimentation, an image of the bubble was taken with a high-resolution camera …
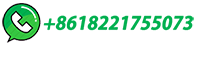
Froth flotation of lithium micas – A review
Main processing routes to treat such deposits are flotation and magnetic separation due to both medium magnetic susceptibility and surface properties of these minerals. Lithium-micas cleavage plan exhibits a negative charge over almost all the pH range. Therefore, the most usual processing route is flotation using cationic collectors.
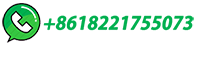
Lithium Hydroxide Process
Lithium Hydroxide Process 's proprietary technology offers a short-cut process concept for spodumene concentrates: direct alkaline leach process for lithium extraction and solubilization, followed by crystallization of the lithium product. Furthermore, the leach process is environmentally sustainable: acid &
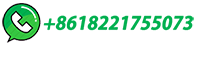
A contribution to understanding the flotation behavior of lithium …
The recycling of spent lithium-ion batteries (LIBs) can not only reduce the potential harm caused by solid waste piles to the local environment but also provide raw materials for manufacturing new batteries. Flotation is an alternative approach to achieve the selective separation of cathode and anode active materials from spent LIBs.
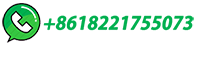
Sustainable Lithium Extraction: How is Lithium Mined and …
The process of extracting lithium from mines primarily revolves around extracting lithium-bearing minerals, notably spodumene, through an intricate interplay of mining and processing methodologies. Initially, ore containing lithium is excavated from subterranean depths and subjected to rigorous physical separation techniques to eliminate ...
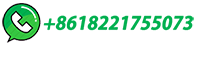
LESSONS LEARNED FROM NEW HARDROCK LITHIUM …
lithium ion battery, Mica, Reflux classifier, Spodumene. INTRODUCTION Lithium is a soft, white and lustrous metal and it is the first element in alkali-metal group (Group 1) of the periodic …
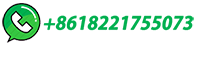
IJMMME
Figure 7. Grade-recovery curve of the Gonçalo lepidolite froth flotation. Similarly to what occurred with spodumene, it was not possible to obtain concentrates with Li 2 O grades close to the Gonçalo lepidolite Li 2 O content (5.58 % Li 2 O [31]), even after the cleaning stage, having been 4.50 % Li 2 O the maximum value achieved. The shape of the grade-recovery curve indicates …
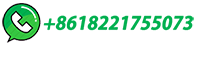