The process of phosphating
Phosphating is a chemical process for treating the surface of steel, where barely soluble metal-phosphate layers are formed on the base material. The layers …
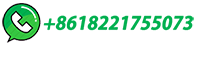
Phosphating Plant
A seven-tank phosphating pretreatment plant is a specialized industrial system used in metal finishing and surface treatment processes. It is designed to prepare metal surfaces for painting, coating, or other finishing processes by removing contaminants, promoting adhesion, and improving corrosion resistance.
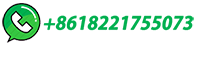
Phosphating of Steel for Cold Forming Processes
Phosphating is a conversion coating process that utilizes diluted phosphoric-acid or phosphate-salts aqueous solution in order to convert the surface of a metal in an …
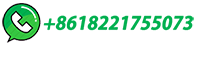
Rod wire pickling and phosphating | SIRIO
Rod wire pickling and phosphating. The steel material phosphating process has the purpose to produce a surface conversion layer, at thin and compact thickness strongly anchored on the surface, in order to facilitate the cold deformation or the further drawing operations. It exists different type of phosphate.
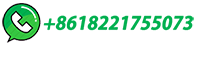
PHOSPHATING & POWDER COATING
PHOSPHATING • The conventional seven-tank Hot Zinc Phosphating system is used. • The following are the different steps involved in the process:-
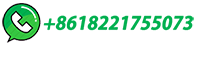
Hot dip galvanizing plant manufacturers & exporter
What is Hot Dip Galvanizing Plant. A hot dip galvanizing plant is a facility where the process of hot dip galvanizing is carried out. These plants are important for the durability and longevity of galvanized products. Compared to other coating methods, hot dip galvanizing is highly cost-effective, offering superior protection at a competitive ...
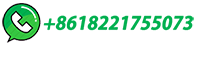
Hot vs. cold phosphating -- differences and advantages
I would like to know the difference between hot phosphating and cold phosphating. Basically we are using hot 7 tank process for our pre treatment of steel, both HR and CR before powder coating. I would like to switch over to cold process.
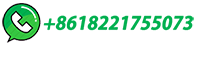
Phosphating Basics as a Pretreatment
Waste treatment is usually a simple neutralization process; however, it is best to discuss this with local authorities to be sure your disposal process is in compliance with associated restrictions. As noted above, the final stage after phosphating is often referred to as a seal.
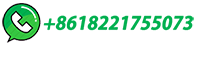
Materials | Free Full-Text | Manganese Phosphatizing …
The phosphating process could be applied to metal substrates such as steel, cast iron, or zinc. This type of treatment process is based on the reaction between the metal surface and liquid environment, which, as a result, forms the solution of orthophosphoric acid (H 3 PO 4) containing Mn, Zn, and Ni cations [27,31]. The …
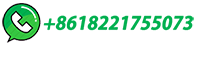
What is Phosphating | Application Of Phosphating
Phosphating is the process of converting a steel surface to iron phosphate. This is mostly used as a pretreatment method in conjunction with another method of corrosion protection. A layer of phosphate coating typically includes iron, zinc or manganese crystals.
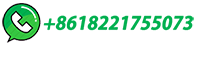
7 Tank Phosphating Process for Powder Coating on Metal
7 Tank Phosphating Process includes Degreasing, Rinsing Pickling, Rinsing, Phosphating, Rinsing and Passivating metal surface .
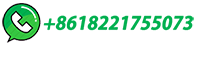
A flowchart of the operating sequence involved in the …
Context 1. ... general, the phosphating process includes six proce- dures as illustrated in the flow chart (Fig. 1). Some of their operations may be omitted or additional steps can …
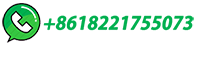
7 tank hot phosphating process
My plant has 7-step hot zinc based Phosphating Process basically done for precoating for metal parts for rubber bonding purpose. We don't have any standard for thickness of phosphate coat required for metal to rubber bonding -- can you guide me?
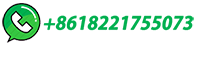
Monitoring the Phosphatizing Process of Metal Surfaces
Phosphatizing, which contributes to an estimated global revenue of more than 500 million dollars, is the most vital metal pretreatment procedure.
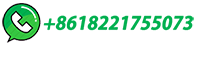
Phosphate Coatings
The article also describes the controlling procedures of coating weight and crystal size. It provides guidelines for choosing phosphate coatings based on application, coating weight requirements, and recommended process parameters. The article concludes with a discussion on safety precautions and the treatment of effluents from phosphating plants.
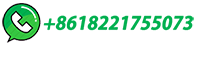
SURFACE TREATMENT PLANTS
Where degreasing is followed by a drying process, convection hot air or vacuum drying is used. Pickling. Pickling plants suitable for cleaning, de-scaling, phosphating and bonder lubrication of steel components, along with steam heating coils, transporting system, fresh air blower and fume exhaust system. ... Phosphating plants for the pre ...
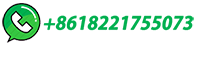
Phosphating Technique: A Reliable Approach for Corrosion
Controlling or preventing metal corrosion through phosphating involves the following steps: the removal of impurities from the surface, water-rinsing of the metal …
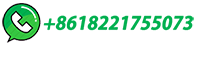
Phosphate Conversion Coatings | SpringerLink
Phosphating is a conversion coating process in which metal dissolution is the starting point. Hence, an increase in electrochemical activity of the material would be beneficial for the formation of PCC. Earlier the author's research group has shown that the use of surface mechanical attrition treatment ...
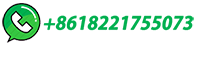
Phosphating Technique: A Reliable Approach for Corrosion …
The phosphating technique is mostly suitable to control metal corrosion either in the form of lubrication, decoration, spraying or painting. Phosphating as a chemical coating process is cost-effective and has a natural bonding effect (Liu et al., 2021). Phosphating also gives high anti-corrosion ability.
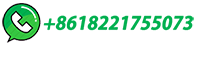
Zinc Phosphate Coating
In case of spray phosphating, major differences are found in the process sequences for zinc phosphating and alkali metal phosphating systems. Zinc phosphating lines are normally based on 5-stage to 6-stage plants.
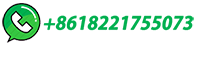
Phosphating
Phosphating is a surface technology process that modifies the surface layer of a metallic surface with an aqueous phosphate solution. Despite its high environmental incompatibility, the treatment is still frequently used to improve corrosion properties, electrical insulation and wear resistance.. During phosphating, the workpieces are immersed in an aqueous …
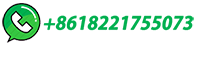
Zinc Phosphating Coatings Chemicals in UAE | Al Taher …
Phosphating is a treatment of steel, galvanized steel at elevated temperatures. Most frequently steel is exposed to the zinc phosphating process. The treatment of the items with phosphate produces fine phosphate crystals on the surface. The fine layer of phosphate crystals boosts the protective capacities of the metallic surface and enhances ...
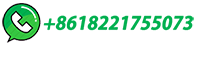
The Process Of Phosphating – Some FAQs
Phosphating is a chemical process for treating the surface of steel, where barely soluble metal-phosphate layers are formed on the base material. The layers created are porous, …
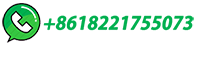
7 Tank Phosphating: A Surface Treatment Process for Metal …
Phosphating is a surface treatment process that is used to improve the corrosion resistance and paint adhesion of metal components. One of the most …
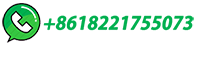
A flowchart of the operating sequence involved in the phosphating process.
Download scientific diagram | A flowchart of the operating sequence involved in the phosphating process. from publication: Zinc phosphate conversion coatings on magnesium alloys: A review ...
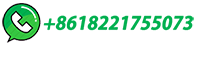
Phosphating
What Does Phosphating Mean? Phosphating is a conversion coating that is applied to steel or iron components, and is mostly used as a pretreatment method in conjunction with another method of corrosion protection. The process involves immersing a component in a dilute solution, which then converts the surface of the metal into a layer …
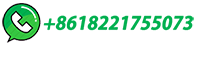
Manganese Phosphate Coating
The coating weight and crystal size of the manganese phosphate coatings are influenced to an even greater extent than in zinc phosphating by the mechanical, thermal, and chemical pretreatment of the workpiece surface prior to phosphating. For example, cleaning in alkaline aqueous cleaning agents or pickling in acids produces coatings with …
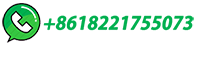
Phospating
Phospating . Phosphating (also phosphatization) is a chemical process in which coatings are generated on a pure metal (normally steel) surface. Coatings generated by phosphating are electrically non-conductive and therefore reduce …
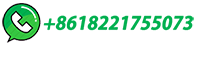
Pretreatment Plants,Phosphating Plant,Pretreatment System
In general, there are two alternative pretreatment systems or Phosphating plant as they are called, viz. the dip system (cold or hot process) and the spray system. Meanwhile, ask for details of our complete painting plants consisting of pretreatment and stoving equipment, conveyor, spray booths and spray painting equipment.
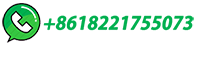
Phosphating Explained: How It Works and Why It Matters
The phosphating process improves paint adhesion by creating a porous, rough surface on the metal. This allows the paint to bond mechanically with the substrate. The porous layer created by the phosphate flakes provides a surface ideal for anchoring paint particles, …
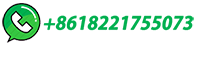