Gyratory Crusher & Cone Crusher Mantle Differences
In the Gyratory all the movement is in the bottom of the crusher mantle. This is due to the angle that the main shaft is on. The greater angle of the cone crusher puts the …
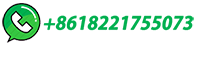
Gyratory and Cone Crusher
A primary gyratory crusher was required to crush iron ore at the rate of 3000 t/h. The largest size of the run-of-mine ore was 1000 mm. The required product size was less than …
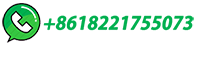
Types of Crushers: What You Need to Know
Gyratory crushers. Run of mine material is transferred into a gyratory crusher's upper-level hopper. The walls of the gyratory crusher's hopper are lined with "V-shaped" pieces, the mantle and the concave, like a jaw crusher but shaped like a cone. The ore is discharged through the smaller bottom output hole of the cone.
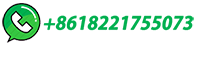
Minerals | Free Full-Text | Torque Analysis of a Gyratory Crusher …
Comminution by gyratory crusher is the first stage in the size reduction operation in mineral processing. In the copper industry, these machines are widely utilized, and their reliability has become a relevant aspect. To optimize the design and to improve the availability of gyratory crushers, it is necessary to calculate their power and torque accurately. The …
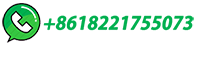
Impact, Cone & Jaw Crusher Equipment For Sale | Kobe
The excellent design of the Gyratory Crusher is only one of the reasons the team at Minprovise recommend this model when choosing crusher equipment. The GY's design is a combination of some of the world's most modern engineering techniques and applications. ... The Compound Crusher is a double-rotary, primary impact crusher, which functions ...
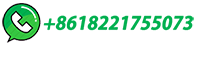
Compare Gyratory Crusher vs Jaw Crusher
To accomplish this reduction in size takes several steps or stages of crushing and grinding. Primary crushing is the first of these stages. Generally speaking there are two types of primary crushers, lets compare them: GYRATORY CRUSHER or a JAW CRUSHER. Although they don't look anything like they do have similarities that put them into ... title="Compare …
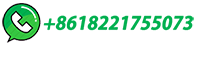
TECHNICAL NOTES 5 CRUSHERS
Figure 5.1 Schematic diagram of a crusher showingg the open- and closed-side settings. 5.1 Jaw and Gyratory Crushers. Jaw and gyratory crushers are used mostly for primary crushing. …
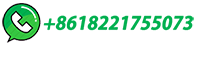
Heavy duty, maintenance-friendly Gyratory Crusher
The Gyratory Crusher "NT" incorporates all of the TC's heavy-duty design features (Heavy Cast-Steel Shell Sections, Forged Main Shaft and Countershaft, Robust Gearing, Generous Lubrication, Long-Life Bronze Components) and focuses on coupling these historical characteristics with updated maintenance-friendly features.
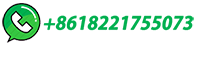
Gyratory Crusher
Gyratory Crusher - Mining Fundamentals. A gyratory crusher is an ore processing machine that crushes the ore between an eccentrically mounted cone and a crushing throat, that is fixed. In …
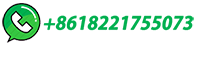
3.4 Gyratory crusher
A gyratory crusher consists of a concave surface and a conical head, both surfaces are typically lined with manganese steel liners. The inner cone has a slight circular movement, but does not …
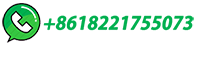
Gyratory Crusher
A gyratory crusher is an ore processing machine that crushes the ore between an eccentrically mounted cone and a crushing throat, that is fixed. In mining, the most important criteria for effective crushing of ores is to choose the type of crusher that suits the rock (ore) material, and to ensure uniform feed. ...
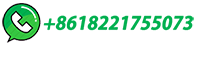
CG810 Primary Gyratory Crusher For Maximum …
CG800i Gyratory crusher brochure Capacity (by hour) 1,300 - 2,700 mtph (1,430 - 2,970 stph) Feed opening 1,067.0 mm (42.0 in.) ... (TIMS) provides real-time monitoring of the crusher lubrication system to ensure it functions optimally. Monitoring the Lubrication system, spider bearing grease system and overpressure system, it ensures ...
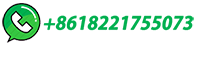
Gyratory Crusher vs. Cone Crusher: What's the Difference?
Primary Crusher vs. Secondary Crusher: Understanding Their …
The primary crusher's function is to reduce the size of the rock or stone for easier handling and transportation. The primary crusher is usually a jaw crusher or a …
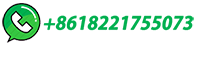
What is the function of crushing chamber in a gyratory crusher
The crushing chamber in a gyratory crusher plays a crucial role in the crushing process. Here are its primary functions: 1. Material Compression: The crushing chamber is where the actual crushing ...
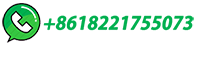
Gyratory Crusher & Cone Crusher Mantle Differences
Difference between jaw crusher and gyratory crusher. Any of you that are at all familiar with the Gyratory crushers and Cone Crushers that the former are used as Primary crushers will probably note many similarities between the types. Each use a cone shaped crushing surface, and the same principal in the eccentric is employed to develop the crushing …
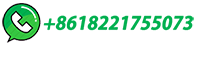
Sensors | Free Full-Text | Modelling of Gyratory Crusher …
A gyratory crusher is a key mineral processing asset in a comminution circuit. Monitoring and predicting the crusher liner wear is essential to ensure the throughput and product quality are maintained during production. This study developed a digital sensor and a discrete element modelling (DEM)-coupled methodology to monitor and reconstruct the gyratory …
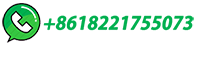
Gyratory and Cone Crusher
Primary crushers are solidly built to receive large lumps of rock directly from the mines and designed for large tonnage throughputs. Basically, gyratory crushers consist of a fixed solid conical shell or bowl (also called concaves) and a solid cone within the bowl called a breaking head (Figure 5.1).The breaking head is fixed to a central spindle, which is …
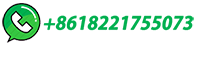
Application guide SUPERIOR® primary gyratory crusher …
Gyratory crushers are one of the main primary crusher types used in mines and quarries. The size designation of gyratory crushers is based on the size of the feed opening and the mantle diameter. Main features • Steep crushing chamber and long crushing surfaces for exception-
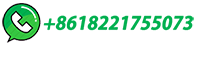
Working Principle of Crushers
Working Principle of Crushers. On left is a showing of the "standard gyratory with straight concaves" is a section through any vertical, radial plane in the crushing chamber of one of the intermediate sizes of the crusher. In order to understand the crushing action in such a chamber it is helpful to consider the process as though each step took place in an orderly, and …
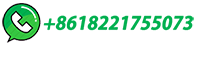
Mathematical Modeling and Multi-Criteria Optimization of …
A differential equation was derived. As a result of its solution, the rational shape of the working chamber cheek of the single-roll gyratory crusher was established, representing a logarithmic spiral arc. Analytical expressions were derived to determine the rational rotation speed and productivity of the crusher under consideration.
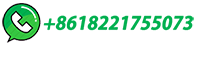
Gyratory Crusher vs. Cone Crusher: What's the Difference?
Understanding the differences between gyratory crushers and cone crushers can help you make an informed decision about which type of crusher is best suited for your needs. Ultimately, the choice between a gyratory crusher and a cone crusher will depend on a variety of factors, including the materials you are working with, the desired product ...
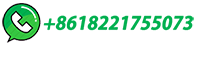
Types of Crushers Explained: Everything You Need to Know
Nevertheless, gyratory crushers are usually more expensive, need more intricate foundation and have higher operating and maintenance costs as compared to jaw crushers. The decision of a jaw crusher or a gyratory crusher is based on, for instance, the required output size, production capacity, and the available budget.
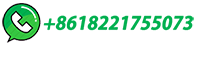
Crushing 101 – Different types of crushers for distinctive needs
The gyratory crushers are equipped with a hydraulic setting adjustment system, which makes it possible to regulate the gradation of the crushed material. Secondary crushing for fine and optimized results. Cone crushers resemble gyratory crushers from the technological standpoint, but unlike gyratory crushers, cone crushers are popular in ...
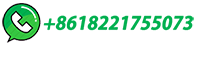
Unveiling the Advantages and Applications of Gyratory Cone Crushers …
Gyratory cone crushers are powerful machines that have revolutionized the crushing industry. Their unique design and superior performance make them a popular choice for a wide range of applications, from mining and construction to recycling and chemical processing. In this article, we explore the many advantages of gyratory cone crushers, including their …
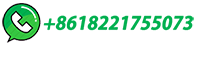
Simulation and optimization of gyratory crusher
The gyratory crusher is widely used in primary crushing of metal ore such as iron ore and copper ore due to its high productivity and large feed inlet [[1], [2], [3]]. ... To describe breakage as a function of the loads on the individual rocks, Minerals developed a breakage model that incorporates elements of PBRM techniques. ...
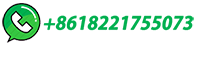
Understanding the Different Types of Crushers
Cone and gyratory crushers. Cone crushers and gyratory crushers are also compression-type machines that crush material between a moving piece of steel and a stationary piece. The output is controlled by the …
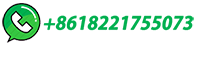
How it Works: Crushers, Grinding Mills and Pulverizers
Table Source: Wikipedia (Crushers) Cone crushers use a spinning cone that gyrates in the bowl in an eccentric motion to crush the rock between the cone surface, referred to as the mantle, and the crusher bowl liner.Gyratory crushers are very similar to cone crushers, but have a steeper cone slope and a concave bowl surface. As the gap between the bowl liner …
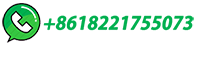
Construction Working and Maintenance of Crushers for …
A gyratory crusher uses a mantle that gyrates (rotates) within a cone shaped inner surface lined with wear resisting plates often called concaves. As the mantle gyrates within the crushing chamber, progressively approaching, and receding from, each element of the cone shaped inner surface, it creates compressive force, which fractures the ...
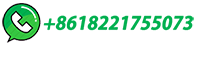
DEM simulation and optimization of crushing chamber shape of gyratory …
The gyratory crusher is essential in the primary crushing process of the ore (Pothina et al., 2007); ... The mantle rotates around the centreline of the gyratory crusher with the gyration point as a fixed point under the function of the eccentric sleeve. The ore particles are fed into the crushing chamber from the inlet, the mantle shaft is ...
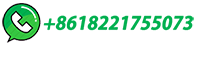
CG800i GYRATORY CRUSHER SERIES
you to get the most out of your crusher. It can also automatically adjust your crusher settings to compensate for crush-ing chamber wear – ensuring consistent product size. The Tank Instrument Monitoring System (TIMS) provides real-time monitoring of the crusher lubrication system to ensure it functions optimally.
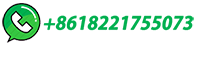