Dynamics in double roll crushers
The load conditions in the roll crusher, however, are usually point to face or face to face load conditions, which cause a larger contact area and therefore a slightly higher breaking force to be considered by a conversion factor (Schmidt, 2011). The method shows good results, however, for single particle crushing and low comminution ratios.
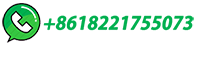
Factors to Consider When Selecting the Proper Roll Crusher …
A good rule of thumb for single-stage crushers is that a Single Roll Crusher provides up to a 6:1 ratio of reduction and a Double Roll Crusher provides up to a 4:1 …
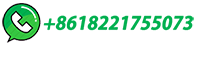
Single Roller Crushers
The single roll crusher reduces the feeding material in a wedge-shaped crushing area by means of pressure and shearing stress. The crushing body is formed by a rotating roll …
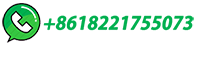
Roll Crushers
This chapter deals with the designs and operation of different types of roll crushers. Two main types are indicated. The first type where the rolls ar…
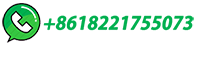
SINGLE ROLL CRUSHERS
The single roll crusher reduces large size particles in the feed to a medium size while producing a considerably lower percentage of fines than other crushers. The single roll …
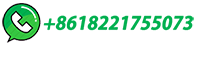
Single Roll Crushers
Products. Crushers. Single Roll Crushers are primary crushers that provide a crushing ratio. They reduce materials such as coal, mine refuse, shale, slate, gypsum, bauxite, …
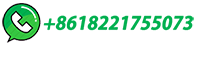
Jaw Crusher
However, et al. (1976) ... Figure 8.1 shows two basic types of jaw crushers: single toggle and double toggle. In the single toggle jaw crusher, an eccentric shaft is installed on the top of the crusher. ... The composition, working principle and fault mechanism of crusher, ball mill, rotary kiln and grate cooler are introduced above.
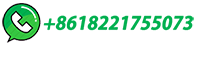
How Does a Jaw Crusher Work? A Simple Guide
Discover how does a jaw crusher work with our simple guide. Learn about the mechanics and operation of jaw crushers on our blog.
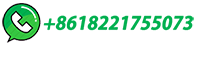
Dynamics in double roll crushers | Request PDF
A single particle crushing event inside a double roll crusher takes on the order of 20-35 ms (Lieberwirth et al., 2017), which translates to a relatively modest average strain rates in the ...
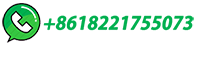
Crusher
Roll Crushers. A. Gupta, D.S. Yan, in Mineral Processing Design and ... crushers were originally designed and developed by around 1920 and therefore are often described as cone crushers. As the mechanism of crushing in these crushers are similar to gyratory crushers their designs are similar, but in this case the spindle is ...
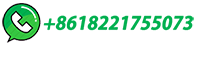
The Differences Between Double Roll Crushers and …
Double Roll Crushers and Sizers are two types of crushers used in mineral processing. While both can be used for material size reduction, here are the differences operators should consider when choosing between a Double Roll Crusher and Sizer to meet the needs of their site.
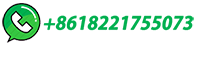
McLanahan | Quad Roll Crushers
How Quad Roll Crushers Work. Quad Roll crushers are designed for larger feed sizes and high ratios of reduction at high capacities. The top stage of the Quad Roll crusher is essentially made up of a double roll crusher, which is designed with the appropriate diameter rolls and tooth configuration to readily grab the incoming feed material.
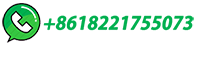
Roll Crushers
Lancaster Products Roll Crushers reduce – in a single pass- material previously requiring primary and secondary crushing.
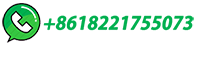
Single Roll Crushers & Shredders for Scrap Materials
Our Single Roll Crushers are ideal for heavy-duty primary and secondary reduction of ROM Coal, middlings, screenings, and re-crushing. With high tonnage capacities in each …
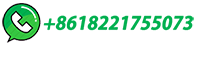
(PDF) Design of Impact stone crusher machine
Based on the mechanism used crushers are basically of three types; namely, Cone crusher, Jaw crusher, and Impact Crusher. ... • Single-Roll Crusher ... 4 M AT H E M AT I C AL M ODELING .
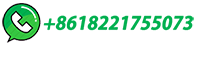
Modeling of coal breakage in a double-roll crusher
To represent the particle behaviors and to predict the product size distributions of coal breakage products by a double-roll crusher, a new combined breakage–agglomeration model has been ...
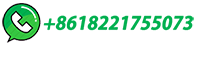
Heavy-duty single roll crusher | Magaldi
Working concept. Magaldi Single-Roll Crusher features a toothed roll assembly, which crushes the incoming feed material against anvil plates. When the material enters …
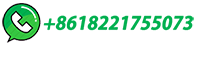
(PDF) DESIGN AND OPERATIONS CHALLENGES OF A SINGLE TOGGLE JAW CRUSHER
A review on the design and operations challenges of a single toggle jaw crusher is presented. Strength and fracture toughness of the material to be crushed are intrinsic properties that determine ...
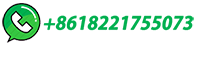
SRC | Single roll Crusher
SRC | Single roll crusher: Single roller crusher redefined. The newly developed SRC series is characterized by a high crushing ratio.
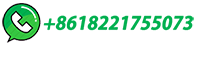
Optimisation of the swinging jaw design for a single toggle jaw crusher
The comminution mechanism largely depends on the rock material properties (abrasive, hard, sticky or brittle) . These machines are designed to achieve primary, secondary, and successive (tertiary and quaternary) crushing . The most common crushers in crushing sites and industries are gyratory, jaw, roll, and cone crushers .
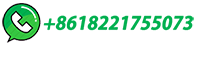
A fundamental model of an industrial-scale jaw crusher
Jaw crushers have been modelled previously; in 1953, Gauldie conducted a performance study of the jaw crusher, including a capacity model that handles varying speeds and closed side setting (CSS) (Gauldie, 1953). The kinematics of the single-toggle crusher has been modelled by Oduori et al. (2015).
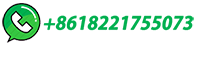
One-stop Turnkey ROLL CRUSHER
This improved roll crusher with mightiness and high efficiency is devel-oped by Fote's senior mining research technicians through improving the roll pressure, rotation, and materials. ... are single-row tapered roller bearings on both sides of roll milling. The main crushing part is roll milling, which undertakes the major crushing work ...
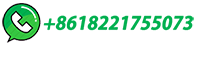
Construction Working and Maintenance of Crushers …
For example, a single-roll crusher, employ shear together with impact and compression. Shear crushing is normally used under following conditions. When material is somewhat friable and has relatively low silica content. ... actuating mechanism (eccentric and driving gears), and in its upper part a cone shaped
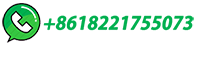
Roll Crusher | HRC
Roll Crusher operation is based on the principle of continuous pressure generated between two counter-rotating rolls; allowing uninterrupted crushing, in contrast to the intermittent action of jaw crushers.
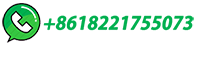
McLanahan | Double Roll Crushers
How Double Roll Crushers Work. Operating Double Roll Crushers is quite simple. Whether it is a single or dual drive arrangement, the rolls are powered by electric motors and V-belt drive configurations, resulting in reliable and quiet operation.
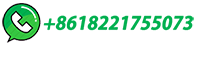
Laboratory-scale validation of a DEM model of a toothed double-roll
Besides these empirical models and experimental studies, the particle flows and breakage in both single-roll and double-roll crushers were numerically studied based on DEM using a breakage model [1]. DEM is becoming a popular method for the study of crushing processes.
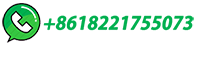
Optimization of roller teeth based on the analysis of the …
Sintered ore; single roll crusher; crushing mechanism; JH-2 constitutivemodel;roll tooth optimization Introduction ... Zhao et al. [13] established the crushing process model of the impact crusher and established the function of crushing product size with the crusher rotor radius, rotor rotating ...
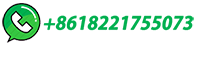
SSINGLEINGLE RROLLOLL CCRUSHERSRUSHERS
Single roll crushers utilize machine cut teeth on the gear set between the roll shaft and countershaft. Gear teeth are ... Where used, the automatic toggle relief mechanism is completely guarded by hinged access doors. Operation of these doors is controlled by a hazardous-location limit switch, which when wired (by others) in series with the ...
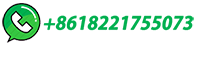
Single Roller Crushers
Automatic toggle mechanism allows the crushing plate to hinge open, pass uncrushable tramp material and return to the previous position for continued operation; Operation. The single roll crusher reduces the feeding material in a wedge-shaped crushing area by means of pressure and shearing stress.
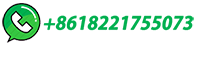
Roll Crushers
By reason of the reduced strains, single side- frame castings, bolted together, can be used to support the roll-bearings in place of the usual massive continuous bed-plate casting. ... A few years ago we had a mill consisting of a 10 by 20 roll crusher, two 6 by 20 breakers in parallel, and a pair of 20 by 28 Krom rolls. ... No feed …
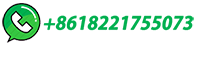