(PDF) An overview of the beneficiation of iron ores via …
Flotation is the most effective solution, both technologically and economically, when upgrading iron concentrates. Research regarding iron ore flotation began in 1931, demonstrating that reverse ...
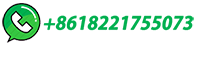
Residual amine in iron ore flotation
The possibility of recovering residual amine present in the water phase of tailings pulps of the reverse cationic flotation of iron ore was investigated. The samples collected in the tailings from mechanical and tank cells and also from flotation columns were kept under rest to promote the separation between the water and the solid particles.
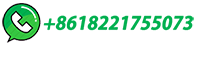
Akzo Nobel presentation on optimising reverse flotation of iron ore …
AkzoNobel will present a paper at the X CIS Congress of the Mineral Processing Engineers on optimising reverse flotation of iron ore, especially magnetite ores. ... AkzoNobel will discuss the effects of ore type, water quality and type of collector on froth properties. The Congress will take place February 17 through 19, 2105 at the World Trade ...
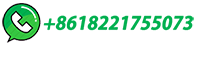
The Life Cycle of Water Used in Flotation: a Review
As flotation is an intensive water consumption process, e.g., 3~7 t water is used to process 1 t ore, water saving is always a key attempt in most of plants, not only to reduce the water cost paid to the authorities but also to reduce the wastewater treating cost required prior to discharging or reusing.
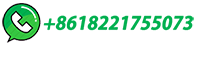
Sulfur reduction in Sangan iron ore by flotation
Magnetic skarn ore (MSO) is one of the major copper bearing ore extracted by the Ok Tedi Copper Mine in Papua New Guinea (PNG). Copper minerals are recovered by flotation while the iron not ...
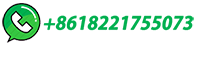
An overview of treatment techniques to remove ore flotation …
1. Introduction. Mining activities consume billions of m 3 of water annually. The water withdrawn by mining industries could achieve 17 m 3 per ton of processed ore while the water consumption required in processing varies between 0.34–6.27 m 3, according to data from 359 industries reports [1].Seeing that the world iron ore production was 2537 million tons in …
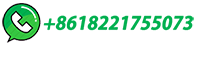
Use of process water in reverse cationic flotation of iron …
The reverse cationic flotation of iron ores using starch as depressant and ether amine as collector may be performed using the process (recycled) water with no impact on the iron …
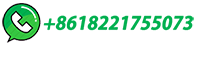
Buffering of pulp pH and its influence on process water …
Fig. 3. The flowsheet of the reverse cationic flotation of the iron ores in Yunnan, China 2.3. Methods 2.3.1. pH buffering test/Bench flotation experiments To prepare the sample to do the pH buffering/bench flotation experiments, 500 g of the iron ore sample was mixed with distilled water at room temperature.
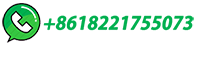
Collecting Agent–Mineral Interactions in the Reverse Flotation of Iron
Froth flotation has been widely used in upgrading iron ores. Iron ore flotation can be performed in two technical routes: direct flotation of iron oxides and reverse flotation of gangue minerals with depression of iron oxides. Nowadays, reverse flotation is the most commonly used route in iron ore flotation. This review is focused on the reverse flotation of …
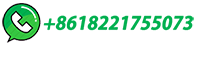
New Etheramine Based Collector for the Reverse Flotation of Iron Ore …
Froth flotation is dependent on a number of physico-chemical phenomena. Chemical factors include tensions of the air-water, air-solid and solid-liquid interfaces, bubble attachment processes, and ...
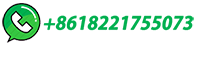
Treatment and Recycling of the Process Water in Iron Ore Flotation …
Coagulating sedimentation and oxidation treatment of process water in iron ore flotation of Yuanjiacun iron mine had been studied. The process water of this mine carried residual polyacrylamide ...
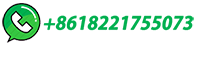
A review of the effect of water quality on flotation
Water quality for flotation on a mine site can vary significantly over time (Levay and Schumann, 2006, Luukkanen et al., 2003, Stén et al., 2003). The composition of flotation …
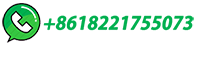
Flotation of Iron Ores: A Review
The impact of the zeta potential and surface chemistry on flotation and deslime is also discussed. The aim of this paper is to provide a well-detailed, well-referenced source for the current status of iron ore flotation, …
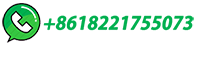
Froth Flotation Process
The Froth Flotation Process is about taking advantage of the natural hydrophobicity of liberated (well ground) minerals/metals and making/playing on making them hydrophobic (water-repel) individually to carefully separate them from one another and the slurry they are in. For this purpose we use chemicals/reagents: Frothers (MIBC) is what allows the …
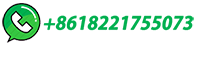
Effects of Cations/Anions in Recycled Tailing Water on …
It is well known that reverse flotation performance of iron oxides is affected by water quality. Since many potential variations among water sources recycling in a mineral processing plant bring unpredictable effects on the flotation system of iron oxides: disturbing ions/compounds, pH, hardness, residual reagents, etc. In this study, the recycled tailing water …
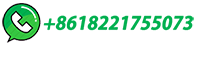
Use of process water in reverse cationic flotation of …
The reverse cationic flotation of iron ores using starch as depressant and ether amine as collector may be performed using the process (recycled) water with no impact on the iron recovery and the quality of iron concentrate (silica and iron contents). The use of recycled water allows to reduce the collector consumption up to 50 % while a
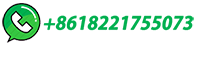
An Overview of Calcite Recovery by Flotation
In general, precipitated calcium carbonate (PCC) is used as a mineral filler in paper industries; while natural calcite (CaCO3) ore is also suitable for industrial use if it is a finely ground high-grade material. Naturally, calcite is found in the form of high- or low-grade ores and it is one of the most widely distributed industrial minerals on the earth's crust. However, it is …
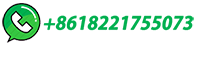
Existing and New Processes for Beneficiation of Indian Iron …
The iron ore industries of India are expected to bring new technologies to cater to the need of the tremendous increase in demand for quality ores for steel making. With the high-grade ores depleting very fast, the focus is on the beneficiation of low-grade resources. However, most of these ores do not respond well to the conventional beneficiation techniques used to …
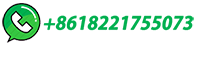
Temperature and climate-induced fluctuations in froth …
Seasonality in flotation performance has been reported on numerous plants processing different ore types. Since flotation is a physicochemical process, there are physical and chemical …
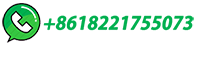
Flotation Techniques: Trends and best practice for Mineral …
- **Role**: Water quality, including its chemical composition and purity, can affect the performance of reagents and the stability of the froth. ... - **Operation**: In iron ore flotation, selective attachment is used to separate iron ore minerals from gangue minerals. Different types of collectors and depressants are employed.
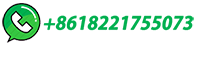
Optimal Control of Iron Ore Flotation with Soft Sensors for …
For Brazilian iron ore producers, reverse cationic flotation is preferred to obtain high quality concentrates from silicate ores. The SiO2 (silica) particles are rendered …
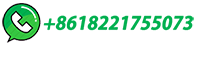
Anionic flotation of high-iron phosphate ores—Control of process water
The fatty acid flotation of a difficult-to-float igneous phosphate ore (26.2% P2O5, 15.4% Fe2O3) was investigated through batch flotation tests in the presence of soda ash.
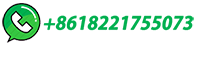
Minerals | Special Issue : Iron Ore Flotation
Iron ore flotation is a key technique to concentrate intermediate-low-grade ore, in order to reach the market requirements for higher-grade concentrates of iron. ... The biosurfactant reduced the air/water surface …
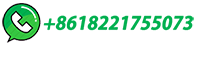
Fundamentals of froth flotation
Under discussion is the particle and bubble interaction in froth flotation. Water flow from an interlayer between a particle and a gas bubble under effect of hydrophobic component of wedging ...
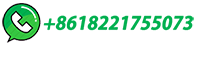
SciELO
Most research has focused on understanding the issues associated with water quality in flotation, where studies focus on three main aspects: (1) ... v. 65, n. 4, pp. 549–552, 2012.] demonstrated the feasibility of process water reuse in iron ore flotation after treatment by DAF for the removal of Ca 2+ and Mg 2+ cations.
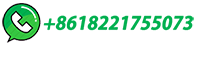
Treatment and Recycling of the Process Water in Iron Ore …
1. Introduction. Iron ore resources are extremely rich in China, but most of them belong to complex ultrafine iron ore with high content of impurities [].Reverse flotation has …
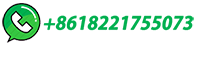
Anionic flotation of high-iron phosphate ores—Control of process water
The fatty acid flotation of a difficult-to-float igneous phosphate ore (26.2% P 2 O 5, 15.4% Fe 2 O 3) was investigated through batch flotation tests in the presence of soda ash.The poor flotation of this otherwise high quality ore was attributed to very high concentrations of calcium and sulfate ions (about 1000 and 2000 mg/L, respectively) found in process water, …
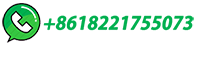
Temperature and climate-induced fluctuations in froth flotation…
Seasonal changes in flotation water quality could be derived from pH variations (impacting flotation kinetics), ... Work by Cooke et al. on iron ore flotation showed that at pH 6, haematite recovery improves with temperature, while calcium-activated quartz recovery drops. Moreover, out of fatty acids such as linolenic, linoleic, oleic, elaidic ...
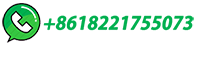
Digital twin of minerals processing operations for an …
2.1 Froth flotation process. Froth flotation is extensively used to enrich sulfide minerals (galena, chalcopyrite, sphalerite, molybdenite, and pentlandite) as well as non-sulfides such as phosphate minerals, iron ores, and fine coal [1, 2].The mineral ore is ground to fine particles of typically 10 to 100µm in diameter and mixed with water to create a slurry.
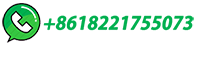
Froth Flotation: Factors affecting, Advantages, Disadvantage
Froth flotation is a commonly utilized metallurgical technology that is employed in a variety of sectors such as mineral processing and wastewater treatment. During the flotation process, air is bubbled through a suspension of fine iron ore in water with a tiny amount of flotation reagent added.
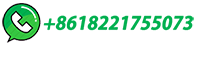