FLOW CHART FOR MINERAL BENEFICIATION PROCESS …
Process Flow Chart A process flow chart is a graphical representation of the successive steps involved in a process using symbols interconnected with lines. In case of mineral beneficiation, it is the diagrammatic illustration of various steps involved in the up-gradation of ores/minerals starting from their transportation till their final production to be used as raw materials in …
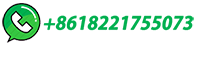
Coal Beneficiation Process Diagram
The Problem with Coarse and Fine Coal Beneficiation Economic and operating conditions make it important to provide a simple, low cost, efficient method for recovering fine coal from washery waste. Not only is the water …
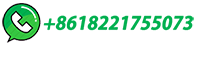
Beneficiation
Mineral Processing. Swapan Kumar Haldar, in Mineral Exploration (Second Edition), 2018. 13.2.4.3 In-Stream Analyzer and Process Control. Mineral beneficiation, particularly base and noble metals, is sensitive to optimum use of reagents, recovery of metals, and clean concentrate.High fluctuation of feed grade at flotation cells yields loss of metals to tailing.
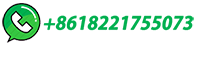
Iron Ore Beneficiation Process
Iron Ore Beneficiation Process. Previous. ... The Brunt Ore Drying Plant. In 1910, M. A. Hanna & Co. built an experimental drying plant at the Hollister mine, Crystal Falls, Mich. ... (Fig. 100) will help to an understanding of the process. Flow Sheet of Trout Lake Concentrator. One crude ore bin and one bar-grizzly. One 20-foot conical ...
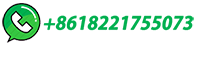
Iron Ore Processing: From Extraction to Manufacturing
The final stage in iron ore processing is ironmaking, where the iron ore is transformed into molten iron through a process called reduction. The most common method of ironmaking is the blast furnace route. In a blast furnace, iron ore, coke (carbon), and fluxes (limestone or dolomite) are loaded into the furnace from the top.
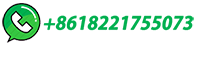
Manganese Ore Processing
The problem involved in Manganese Ore Processing deals with the production of acceptable specification grades of manganese concentrates at a maximum recovery of the total manganese from ores having variable characteristics. The flowsheet provides for both gravity and flotation with a maximum recovery of the manganese values in a coarse size in the most …
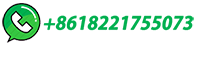
Integration of the Beneficiation Process into Iron Ore …
ore. The resulting plant was designed to process 6.8 Mtpa of feed at 55 per cent Fe, 4.3 per cent Al2O3 to produce 5.2 Mtpa of 63.6 per cent Fe products for a weight recovery of 76.5 per cent. …
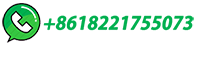
Understanding Pellets and Pellet Plant Operations – …
The process of enriching taconite ore involved grinding the ore to remove gangues and upgrading the iron ore (i.e., an ore beneficiation process). The resultant high grade ore is in the form of fine particles, as small as 0.1 mm or less, which are not suitable for sintering. ... These plants receive iron ore mostly by rails. some plant may ...
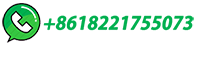
Iron Ore Beneficiation Process Flowsheet PDF
Iron ore beneficiation process flowsheet.pdf - Free download as PDF File (.pdf), Text File (.txt) or view presentation slides online. This document provides a flow diagram of a mineral processing plant. It shows the process flow from …
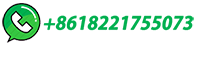
Iron Ore Beneficiation Process Flowsheet PDF | PDF
Iron ore beneficiation process flowsheet.pdf - Free download as PDF File (.pdf), Text File (.txt) or view presentation slides online. This document provides a flow diagram of a mineral processing plant. It shows the process flow from receiving the raw ore feed hopper through various crushing, grinding, and flotation circuits to produce concentrate products.
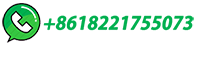
a Circular Journey from the Ground to the Recycling Line
The production of LFP requires lithium source, iron source, and phosphorous source. The high-level block flow diagram outlining the process is depicted in Fig. 15 below. Depending on the LFP production technologies applied, some of the popular feed material sources can be varied and listed in Table 1.
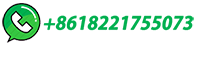
Mining and Beneficiation of Phosphate Ore
The first commercial production of phosphate rock began in England in 1847. A wide variety of techniques and equipment is used to mine and process phosphate rocks in order to beneficiate low-grade ores and remove …
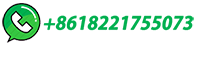
Driving investments in ore beneficiation and …
The pressure on the steel industry to reduce its carbon footprint has led to discussions to replace coke as the main reductant for iron ore and turn to natural gas, bio-syngas or hydrogen. Such a major transition from the blast …
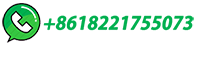
Advances in Low Grade Iron Ore Beneficiation
10 Mt/yr low grade beneficiation plant in its integrated steel plant and has further expanded it to 20 Mt/yr capacity recently. The Kudremukh plant in Karnataka was the first big iron ore beneficiation plant in India. It mainly processes complex haematite and magnetite ore. It got pelletisation facility for
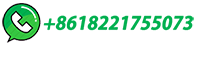
Phosphate Beneficiation Process
Laboratory and pilot plant work is very valuable in establishing the final treatment which will give the maximum net economic return. Phosphate Beneficiation The Phosphate Beneficiation Flowsheet Phosphate Ore Mining. Electrically operated drag lines strip off the overburden from the mining area and deposit the phosphate matrix around a pump pit.
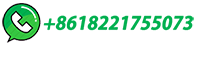
Step-by-Step Guide: Chrome Plant Process Flow Explained
Beneficiation is a crucial step in the chrome plant process flow, as it involves the separation of chromite from other minerals present in the ore. Various techniques, such as gravity separation, magnetic separation, and flotation, are used to achieve this separation.
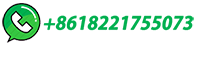
Typical Tin Processing Flowsheet
Typical Tin Beneficiation Flow Sheet. Multotec specialises in tin beneficiation equipment with over 50 years of global experience and leading technology. Our team of metallurgists and engineers will partner with you to customise your …
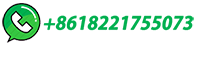
A review of cassiterite beneficiation fundamentals and plant practices
2.1. Production. The strategic metal tin production was almost stable at about 200 tonnes per annum during the post-war period and finds many ups and downs in 1960–1990 due to fluctuations in the international market price.The world production of tin reached as high as 325,000 tonnes in 2005 due to increased demand.Around 244,000 tonnes of tin production …
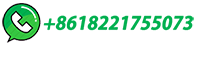
How to Extract Iron from Hematite: Methods and Plants
The process flow of the extraction of iron from hematite is as follows: crushing, grinding, extracting (flotation separation, magnetic separation, gravity separation, etc.) and drying. ... The hematite ore processed by a beneficiation plant in India has an uneven grain size and gangue minerals as quartz. It adopted a combined process of stage ...
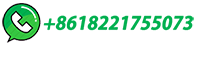
Characterization and Beneficiation of Dry Iron Ore …
Current industrial practice of processing of iron ore fines in India does not involve much beneficiation. However, few plants in India are treating fines during washing, classification, and jigging process [4]. In other parts of the world, iron ore fines are beneficiated for magnetite- and hematite-rich iron ore in * P. Dixit prashant.dixit ...
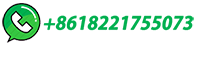
A Study on High-Grade Iron ore Beneficiation to Reduce
Iron ore pellets are largely characterized by inherent physical and chemical properties of the ore. Alumina and silica play important roles in determining the productivity of a Blast Furnace. On average, one percent increase in iron content improves productivity by 2% and reduces coke consumption by 1%. Therefore higher iron ore feed content to blast furnace is …
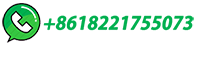
Iron Ore Pellets and Pelletization Process – IspatGuru
Slurry tank for storage of concentrated iron ore slurry from beneficiation plant. The particle size of iron ore in the ore slurry is less than 45 micro meter for around 80 % of the particles. Additive materials (such as dolomite, limestone, lime or olivine etc. depending on the quality of the pellet to be produced) is added to the slurry.
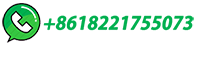
Iron Ore Beneficiation Process
By beneficiation is meant all methods of removing impurities, and raising the iron content to a point where it can be sold in open market, the principal impurities being silica and moisture. The general processes to which …
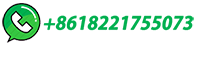
The six main steps of iron ore processing
When iron ore is extracted from a mine, it must undergo several processing stages. Six steps to process iron ore. 1. Screening We recommend that you begin by screening the iron ore to separate fine particles below the crusher's CSS before the crushing stage. A static screen is used to divert the fine particles for crushing.
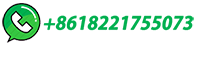
Iron Ore Processing, General | SpringerLink
The earliest attempts to float iron oxide minerals involved the use of anionic collectors such as oleic acid or sodium oleate. Such a process was used at the Cuyuna Range plant which processed manganiferous iron ore in 1931. One of the successful applications of anionic flotation process was the iron ore flotation plant at Marquette county ...
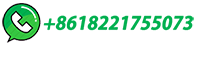
Iron Ore production in the Pilbara
Iron Ore production in the Pilbara Activities involved in finding, mining and processing iron ore at our Pilbara operations have been simplified in the following diagram. Rio Tinto operates 11 iron ore mines in the Pilbara and the specific sequence of activities varies from mine to mine. Excellence in planning, scheduling and quality control
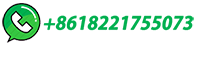
Lithium Processing Plant, Equipment
Crushing & screening: In the crushing and screening stage of lithium ore, a three-stage and one closed-circuit crushing and screening process, or a two-stage and one closed-circuit crushing and screening process can be adopted.Specifically, it is necessary to refer to the particle size of the raw ore and equip a reasonable lithium ore crushing process.
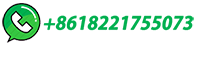
World leader in fine iron ore beneficiation
cost effective fine iron ore beneficiation for the highly variable low‑grade ore. Innovative plant design Extending beyond traditional spiral plants our designs for fine iron ore beneficiation …
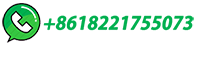
EXECUTIVE SUMMARY
grade iron ore from the captive mines at Rajnandgaon. The above upgardation will also result in enhancing the throughput capacity from 0.7 MTPA Iron Ore Grinding Unit to 1.0 MTPA Iron Ore Grinding and Beneficiation Plant. The process flow chart for Iron Ore Grinding& Beneficiation Plant is given in Figure below .
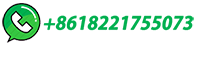