Types of Rock Crushers | Quarry Crushing Equipment | Kemper
Do you need to process sand, gravel, minerals, rock, or other aggregate products and have not yet purchased or leased crushing equipment? There's no question—you need to work with a capable and professional material handling equipment design and engineering company dedicated to selling, renting, and installing the best new crushers for your needs.
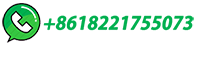
Crushing Plant Flowsheet & Design-Layout
As the need for finer crushing increases, consideration must be given to the achievement of maximum crushing and screening efficiency. The majority of crushing plants recently constructed have accomplished this desired efficiency by optimizing plant design, crusher design and automation.
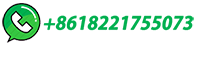
Crusher
A. Gupta, D.S. Yan, in Mineral Processing Design and Operation, 2006. ... Impact crushers are widely used in stone quarrying industry for making chips as road and building material. These crushers are normally employed …
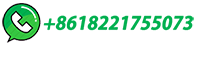
Equipment Used in Crushed Stone Processing
The stone that is too large to pass through the top deck of the scalping screen is processed in the secondary crusher. Cone crushers are commonly used for secondary crushing (although impact crushers are sometimes used), which typically reduces material to about 2.5 to 10 centimeters (1 to 4 inches).
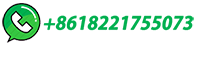
Crushing Plant Design and Layout Considerations
%PDF-1.2 %âãÏÓ 114 0 obj /Linearized 1 /O 116 /H [ 1107 524 ] /L 2121851 /E 29615 /N 29 /T 2119452 >> endobj xref 114 34 0000000016 00000 n 0000001031 00000 n 0000001631 00000 n 0000001849 00000 n 0000001991 00000 n 0000002645 00000 n 0000002863 00000 n 0000003081 00000 n 0000003294 00000 n 0000003946 00000 n 0000004487 …
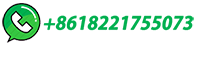
Design and Construction of Rock Crushing Machine …
The design and construction of a prototype rock crushing machine was performed this is with a view to ensuring that the designed crusher is capable of crushing rocks, lime stone and solid minerals for indigenous use. The research work was tailored mainly on the design and production of locally fabricated rock crushing machine for indigenous use.
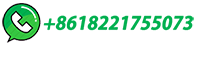
Rock Crushers & Pulverizers | Williams Crusher
With industry-best rock crushers, you can reduce rocks of all types and sizes to your desired product size. Learn more about Williams Patent Crusher rock crushers.
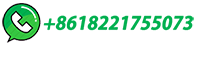
How it Works: Crushers, Grinding Mills and Pulverizers
Crushers, grinding mills and pulverizers are types of grinding equipment that transform or reduce a coarse material such as stone, coal, or slag into a smaller, finer material.
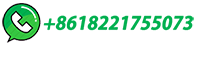
Jaw Crusher Explained
There are three common crushers used at mining and processing plants, these designs are: Gyratory Crusher; Jaw Crusher; Cone Crusher; Crusher Types (jaw, cone, gyratory) Typically, the initial crushing stage is completed using either gyratory crushers or …
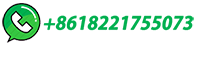
The Ultimate Guide To Crushed Stone And Gravel
How to process crushed stone and what is it used for? Crushed stone is a type of construction aggregate that is typically produced by mining a suitable rock deposit and breaking the removed rock down to the desired size using crushers. It is a popular material for use in construction projects, including roads, bridges, buildings, and …
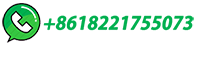
CRUSHING PLANT PROCESS OPTIMISATION
The purpose of the research presented in this paper is to explore the process design of crushing plants in order to gain further understanding on how the crushing plant …
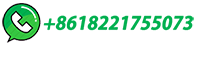
CRUSHING PLANT PROCESS OPTIMISATION
The purpose of the research presented in this paper is to explore the process design of crushing plants in order to gain further understanding on how the crushing plant process can be made more optimised. Earlier work by the author has focused on optimisation on existing plants (Svedensten, 2007).
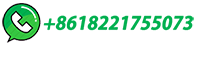
The Ultimate Guide to Designing an Efficient Aggregate …
Designing the layout of an aggregate crushing plant is crucial to ensuring that the plant operates efficiently and effectively. Here are some primary, secondary, …
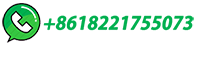
Crushing and Screening Handbook
crushing process. We are the world's leading supplier of both unit machines and complete aggregates processing systems. ... heavy duty design. Cone crushers – capacities available to suit all secondary, tertiary or quarternary crushing ap-plications. High performance technology.
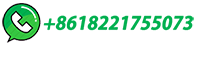
Types of Crushers Explained: Everything You Need to Know
The crushing process is commonly conducted in several stages. Each stage of the crushing process implements a different type of crusher to gradually reduce the size of the material. The first step is crushing the material by using larger crushers that can reduce the material into smaller sizes that will be used in the next stage. Following …
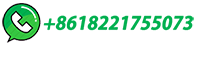
Forces in a Cone Crusher | Steel in Translation
Abstract The literature on the design of cone crushers and analysis of the corresponding crushing processes is mainly based on empirical observations. As a result, it is generally accepted that the crushing action is due solely to compressive forces. Crushers are designed on that basis. Accordingly, many cone crushers today are …
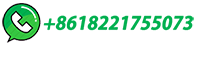
Measurement-Control for Crushing and Screening Process
It mainly includes crushing process control, crushing appliance fault diagnosis, and automatic distributing control. Crushing Process Control. To ensure the continuous, stable, and safe operation of the ore crushing production process, it is necessary to monitor the running state and parameters of key equipment (such as …
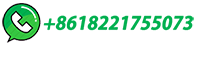
crusher stone processing used design
Jaw crushers, Impact crushers, and Cone crushers for rock, concrete, stone, glass and more. Various used crushers plus NEW Beyer and Red Rhino models. National Agro Foundation - stone crusher machine 25 … PF Impact Crusher. By absorbing the advanced technology from the world, we researched and designed PF series impact …
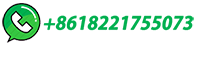
The Ultimate Guide to Stone Crusher Plant Design
Discover the best practices for designing a successful stone crusher plant, including factors to consider, equipment selection and configuration, environmental …
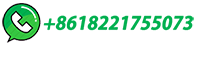
Primary and Secondary Crushing: Understanding the Basics
The jaw crusher is the most common type of primary crusher used in mining and quarrying operations. It has a simple design, reliable performance, and high crushing ratio. The jaw crusher uses a compressive force to crush the materials between two jaws. The gyratory crusher, on the other hand, is used for large primary crushing …
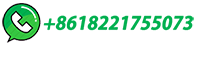
Stone Crusher Professional Manufacturer And Exporter- AIMIX
Aimix, a reliable stone crushing machine supplier, tells us the detailed stone crusher process here. stone-crushing-process. The First Stage: Primary Crushing. In this stage, we generally use a jaw crusher to crush the stone materials coarsely. The stone crusher plant design is excellent: the machine has a high processing capacity and a large ...
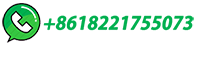
What Machines Do Stone Crushing Plants Need? | Fote …
A gyratory crusher is one of the most in-demand primary crushers for stone crushing plants. It can process rocks, metal ores, granite, and other solid minerals of medium to high hardness. ... Cone crushers have a cone-shaped design that breaks larger rocks into smaller pieces. They can produce a well-graded and cubical end product. …
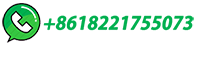
The Ultimate Guide on How to Crush Stone: Techniques and …
Their design allows them to crush materials by compressing them between an eccentrically gyrating spindle and a concave hopper. ... Beyond the primary stone crusher and secondary crushers, screeners play a vital role in the stone-crushing process by grading the crushed material by size. Screeners, or screening equipment, are integral to this ...
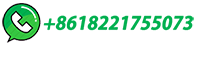
4 Types of Stone Crushers' Maintenance and Efficient …
The article shows the most common crushers used in mining, and the useful solutions for damages of important crushers' parts such as jaw plate, concave, mantle, hammer, and rotor.
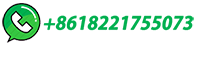
11.19.2 Crushed Stone Processing and Pulverized …
Crushed Stone Processing. Major rock types processed by the crushed stone industry include limestone, granite, dolomite, traprock, sandstone, quartz, and quartzite. Minor …
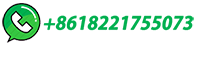
Diamond Processing | Equipment, Process Flow, Cases
Diamond processing description from its geology mineral property to how to extract mineral from rock and placer deposit, related processing plant flow chart and layout design.
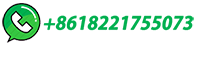
Primary Crusher Selection & Design
Primary crushers with crush run-of-mine rock from blast product size to what can be carried by the discharge conveyor or fit/math the downstream process. A …
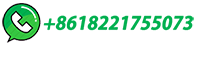
11.19.2 Crushed Stone Processing and Pulverized …
11.19.2 Crushed Stone Processing and Pulverized Mineral Processing 11.19.2.1 Process Description 24, 25 ... Jaw, impactor, or gyratory crushers are usually used for initial reduction. The crusher product, normally 7.5 to 30 centimeters (3 to 12 inches) in diameter, and the grizzly
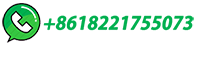
(PDF) Crushing and Screening Handbook
Since the crushing plants operate under harsh conditions and involve very abrasive material, multiple factors can influence their performance. This paper assesses a number of factors affecting the performance of the crushing plant by addressing the critical design parameters and consideration of ore characteristics, operability and maintainability.
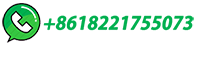
Primary Crusher Selection & Design
How you select your primary crusher will be based on factors like moisture content, maximum rock lump size, material density SG, abrasion index, degradability and it being prone to dusting or not. The crusher capacities given by manufacturers are typically in tons of 2,000 lbs. and are based on crushing limestone weighing loose about 2,700 …
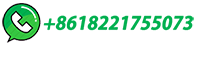