Construction Working and Maintenance of Crushers for …
The goal of a crusher is to crush the given material in to the material with certain size and shape. Information about crushing technology, construction, working and maintenance of crushers …
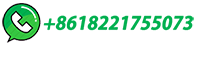
Understanding Jaw Crusher Parts and Their Functions
Introduction: Jaw crushers are powerful machines that are widely used in the mining, quarrying, and recycling industries. These machines are designed to crush large rocks and ores into smaller pieces for further processing. A jaw crusher consists of a fixed jaw and a movable jaw, with the latter being driven by an eccentric shaft that moves the jaw up and down.
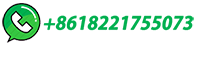
Understanding the Different Types of Crushers | Agg-Net
As a compression crusher, this type of machine generally produces the coarsest material because it breaks the rock along its natural lines of weakness. Jaw crushers are an excellent primary stage solution to prepare rock for subsequent processing stages, such as washing, classifying or secondary crushing. General efficiency tips:
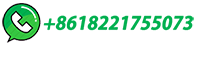
The Rock Cycle
Melting: Rocks beneath Earth's crust melt due to high pressure and temperature, forming magma.. Cooling and Solidification: Magma cools and solidifies either beneath the Earth's surface (intrusive) or upon reaching the surface as lava through volcanic activity (extrusive).Magma and lava form igneous rocks. Mechanical and Chemical Weathering: …
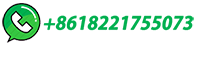
Jaw Crusher Explained
Size Reduction) A crusher is a machine designed to reduce the size of large rocks to smaller rocks, gravel, sand, or rock dust; this is essential for efficient transport of the product via …
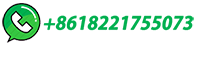
Understanding Jaw Crusher Parts and Their Functions
Introduction: Jaw crushers are powerful machines that are widely used in the mining, quarrying, and recycling industries. These machines are designed to crush large …
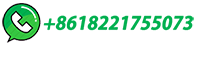
SAND, GRAVEL, AND CRUSHED STONE ON-THE-JOB …
In autogenous crushers, the rock to be crushed also provides the crushing force. Crushing is accomplished by the tumbling action of the rock. Flexible crushing circuits can be constructed so that hard ores, as well as soft ores, can be processed. Wet, sticky ores can be processed in autog enous m ills, w hile t he same ore would
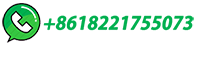
How Does a Jaw Crusher Work? A Simple Guide
In jaw crushers, the crushing force is generated by the movement of the movable jaw plate towards the fixed jaw plate. This force is a result of the mechanical pressure created …
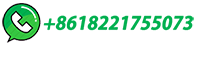
Cone Crusher Sizing & Selection To Maximize Production
The first step is determining the type of material you need to crush. This includes properties such as hardness, abrasiveness, and moisture content. Harder and more abrasive rocks, such as granite, require heavier-duty cone crushers compared to softer rocks, such as limestone. High moisture content material tends to clog cone crushers faster.
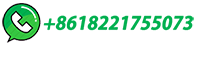
IROCK Crushers | OEM Crushing & Screening Parts
Jaw Crusher. Mobile. TJ-2440 – Mobile Jaw Crusher TJ-2745 – Mobile Jaw Crusher TJ-2950 – Mobile Jaw Crusher; Impact Crusher. Mobile. TC-15CC Mobile Impact Crusher (HSI) TC-20 Mobile Impact Crusher (HSI) Portable. RDS-15 Portable Impact Crusher (HSI) RDS-20 Portable Impact Crusher (HSI) Cone Crusher. Mobile. ITC-200 Mobile Cone Crusher ITC ...
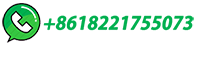
"Computer Aided Design of Jaw crusher"
1.4 Crusher Size and Power rating: The size of a jaw crusher is usually expressed as gape x width. The common crusher types, sizes and their performance is summarized in Table …
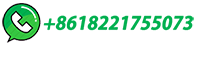
Below the surface: Setting up an underground primary jaw crusher
The required capacity defines the size and type of crushing equipment and also the number of parallel crushers or plants required to meet the mine?s production rate. ... without causing process risks. To achieve this top size, the crusher setting is 200mm or below, depending on the rock characteristics. If a belt is not used to transport the ...
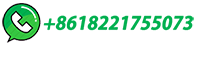
What Is The Rock Cycle: Definition, Diagram, And Examples
The rock cycle is a concept of geology that describes the transition of rocks between the three rock types: igneous, sedimentary, and metamorphic.The cycle outlines how each rock type can be converted to another rock type through geologic processes. What is the rock cycle? Most of us think of rocks as objects which don't change.
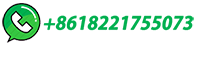
The Complete Guide to Primary Crushing, Secondary …
Learn everything you need to know about primary crushing, secondary crushing, and tertiary crushing in this comprehensive guide. Discover the types of crushers used in each stage, their working principles, and the advantages and disadvantages of each process. Get answers to frequently asked questions and improve your understanding of the comminution …
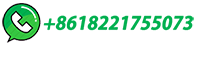
AMIT 135: Lesson 5 Crushing – Mining Mill Operator Training
Diagram of a jaw crusher [image: (135-5-4)] Diagram of a jaw crusher [image: (135-5-5)] Single Toggle Jaw Crusher. The maximum motion is at the top of the jaw. Light to medium duty …
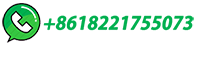
Primary Crusher Selection & Design
How you select your primary crusher will be based on factors like moisture content, maximum rock lump size, material density SG, abrasion index, degradability and it being prone to dusting or not. The crusher capacities given by manufacturers are typically in tons of 2,000 lbs. and are based on crushing limestone weighing loose about 2,700 lbs. per yard3 and …
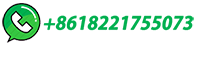
Construction Working and Maintenance of Crushers for …
For example, jaw crushers using this method of compression are suitable for reducing extremely hard and abrasive rock. As a mechanical reduction method, compression ... The gyratory crusher is mainly used in rock that is abrasive and/or has high compressive strength. The crusher is the workhorse of the hard
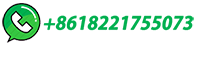
Jaw Crusher: Range, Working Principle, Application
Jaw crushers are used as primary crushers, or the first step in the process of reducing rock. They crush primarily by using compression. The rock is dropped between two rigid pieces of metal, one of which then moves inwards towards the rock, and the rock is crushed because it has a lower breaking point than the opposing metal piece.
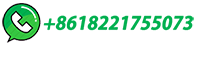
What Are the Differences Between The 7 Types of Crushers?
7 Types of rock crushers have different advantages in many aspects like crushing ability, suitable material, lifespan, etc. Once you know what are the differences, you know to choose an optimal crusher. ... For example, good classification according to the required ratio, no organic and soluble compounds that affect the setting time and ...
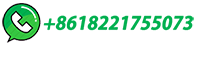
In- depth – Components of a Jaw Crusher | PROPEL …
The jaw crusher is one of the most admired and most sought after equipment from the house of Propel Industries. For the benefit of newcomers in the industry, here is an explainer of the various components of the Jaw crusher. A jaw crusher consists of Crusher Body Pitman Jaw plate Rear end frame Eccentric shaft
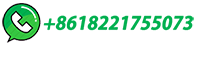
Jaw Crusher Components & Parts
These are bolts that have a known shear strength. If something that the crusher cannot crush accidentally gets into the crushing chamber these bolts will shear off when the Jaw hits the unbreakable object. This will prevent damage to the rest of the crusher. Unlike the gyratory crusher the main lubrication used on Jaw crushers is grease instead ...
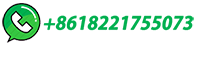
Sample Space Diagram
The sample space diagram shows all the possible outcomes for this game. We can use sample space diagrams to find probabilities. Jon plays the game and wants to know the probability of getting a score of more than 6. We can see from the table that there are 4 scores more than 6. There are a total of 12 possible outcomes from this game.
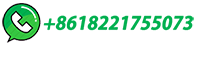
Types of Crushers Explained: Everything You Need to Know
They break large rocks, ore, or other materials into smaller, more usable pieces. This equipment reduces the material by means of compressive force, impact, attrition or shear that are specific for the type of crusher being used. The main function of a rock crusher is to generate particles of similar sizes.
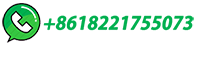
Cone crusher basics in 4 minutes
Feed moving towards a crusher in the -designed Deer Park quarry in Melbourne, Australia. A quick spin. Are you aware of how fast the mantle in your cone crusher spins? It can make between four and seven revolutions per second, so crushing material is compressed multiple times as it descends through the crusher
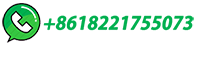
Factors Controlling the Capacity of Rock Crushers
Of this space, a certain restricted part DFIH ' governs the quantity of rock discharged at each cycle of the machine! .and may be. regarded as the displacement volume of. the crusher. The rock, which occupies the space DFIH while the jaws are closed, descends between the jaws and falls from the opening HJ as this becomes wider by movement of ...
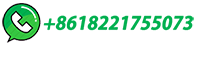
Crushing in Mineral Processing
Typical hard-rock crushers like jaw, gyratory and cones break rock by nipping the ore between a fixed/stationary and a moveable wear-resistant surface/liner. How much reduction each crushing stage is capable of infliction of rocks (reduction ratio) is driven by the angles between the 2 surfaces on each side and holding the rocks-to-be-crushed ...
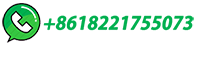
Roll Crushers
Roll crushers consist of two or more adjacent rolls placed parallel to each other and rotated in opposite directions. Single roll crushers are also available which rotate a single roll against a fixed breaker plate. Mineral or rock particles placed between the rolls are nipped and then crushed as they pass between the rolls.
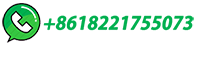
Small Portable Rock Crushers
Types: Small portable jaw crusher with vibrating screen; Small portable jaw crusher with belt conveyor; Small portable hammer crusher; Application: The small portable rock crushers widely used to crush and screen various rocks, stone, aggregates, construction materials and ores, including limestone, granite, marble, gypsum, basalt, iron ore, copper ore, etc crushing and …
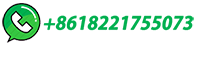
Hammer Mill Crusher & Grinder
The hammer mill is the best known and by far the most widely used crushing device employing the impact principle of breaking and grinding stone. Thus far we have described machines which do a portion of their work by impact, but the only machine described in which this action plays an important role was the sledging roll type and particularly the Edison roll …
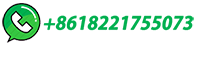
Mini Rock Crusher
The 1" X 2" 911MPEJAC12 Small Rock Crusher is designed to finely crush rock and stone like aggregates or your favorite ore type (gold, silver, copper, etc.) from 3/4" (20mm) feed size down to a D50 - 50% passing 25 Mesh (700um). This also corresponds to a crushed product P80 size of 80% passing 1.5mm or 14 mesh. This small jaw crusher and its miniature opening gape of 25 …
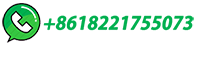