ITP Mining: Energy and Environmental Profile of the …
Table 4-4 shows the energy requirements for the beneficiation of iron ore. The ball mill requires the most energy and is the most energy intensive equipment in beneficiation. This is due to the ratio of ball-ball hits in the mill versus ball-ore hits.
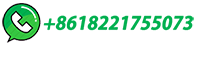
Introduction: Overview of the global iron ore industry
This chapter first provides an overview of world iron ore production and trade, as well as reserves and resources, followed by a summary of the key mining operations in the top ten iron ore producing countries.
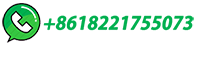
Iron Ore Supply Chain: From Mining to Steel Production
The iron ore supply chain begins with the mining of iron ore, which is then transported to processing plants for beneficiation and further refinement. The refined iron ore is then transported to steel mills for use in the production of steel products.
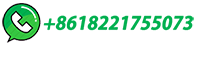
Iron processing | Definition, History, Steps, Uses, & Facts
Iron processing, use of a smelting process to turn the ore into a form from which products can be fashioned. Included in this article also is a discussion of the mining of iron and of its preparation for smelting.
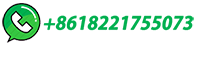
Why Is Iron Ore Valuable? Behind the Scenes of Production …
Learn about the extraction and production process of crude iron ore, along with which countries mine and store the most. See what experts say.
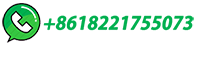
Iron Ore Processing: From Extraction to Manufacturing | Mining …
Learn about the key stages in iron ore processing, including crushing, screening, and beneficiation techniques for optimal resource utilization.
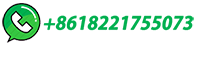
Iron Ore Mining Process: From Extraction to Export
Iron ore mining is relatively simple compared to other minerals and metals that require underground tunnels and complex chemical-drive processes, like gold. Iron ore is generally sourced from open pits on the planet's surface and typically requires only crushing before it is ready for the smelter.
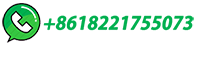
Iron processing
As-mined iron ore contains lumps of varying size, the biggest being more than 1 metre (40 inches) across and the smallest about 1 millimetre (0.04 inch). The blast furnace, however, requires lumps between 7 and 25 millimetres, so the ore must be crushed to reduce the maximum particle size.
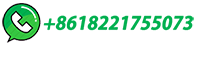
Iron Ore Processing, General
Making iron and steel from iron ore requires a long process of mining, crushing, separating, concentrating, mixing, agglomeration (sintering and pelletizing), and shipping to steel mills. Iron ore processing is characterized by a constant adaptation to changing raw materials and market conditions.
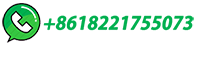
Iron ore | BHP
Iron ores are rocks and minerals from which metallic iron can be extracted. There are four main types of iron ore deposit: massive hematite, which is the most commonly mined, magnetite, titanomagnetite, and pisolitic ironstone.
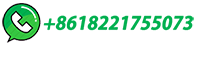