Advancing Iron Ore Beneficiation: Exploring Cutting-Edge
In the dynamic landscape of mining and metallurgy, the iron ore beneficiation process stands as a cornerstone, pivotal in transforming raw ore into high-grade iron products. This article delves ...
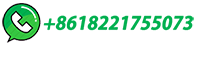
Iron Production
Introduction; Outside links; References; The production of iron from its ore involves an oxidation-reduction reaction carried out in a blast furnace. Iron ore is usually a mixture of iron and vast quantities of impurities such as sand and clay referred to as gangue.
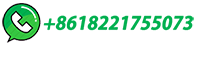
Iron processing
Iron ore sintering consists of heating a layer of fines until partial melting occurs and individual ore particles fuse together. For this purpose, a traveling-grate machine is …
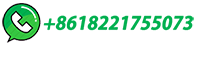
Sulphur removal in ironmaking and oxygen steelmaking
The SM ladle treatment processes are comparable for both BF-BOF and EAF steelmaking. However, sulphur removal is less of an issue in the EAF process, since its raw materials (scrap, direct reduced iron) contain less sulphur than the raw materials of the BF-BOF process (iron ore, coke and coal) Citation 1, Citation 4.
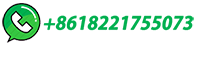
Ore Minerals | Formation, Genesis, Occurrence » Geology …
Ore minerals are naturally occurring minerals that contain valuable elements or minerals in sufficient quantities to be economically mined and processed for their desired metal or mineral content. These minerals are typically extracted from the Earth's crust and processed to obtain the valuable elements or minerals for various industrial, …
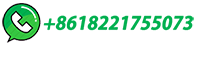
Recent Trends in the Technologies of the Direct Reduction …
In the direct reduction process of iron ore where solid carbon is the reductant, self-reducing pellets, briquettes or composites entails iron ore embedded in coal or carbonaceous materials are typically used in blast furnace and direct reduction processes to mitigate the effect of carbon consumption for better productivity and …
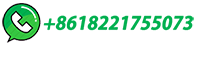
Arsenic Removal from Arsenopyrite-Bearing Iron Ore and …
In most cases, arsenic is an unfavorable element in metallurgical processes. The mechanism of arsenic removal was investigated through roasting experiments performed on arsenopyrite-bearing iron ore. Thermodynamic calculation of arsenic recovery was carried out by FactSage 7.0 software (Thermfact/CRCT, Montreal, …
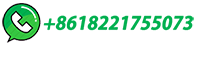
Iron Ore Agglomeration Technologies | IntechOpen
Until the 1950s of the last century, the oxidized iron ores that were loaded into the blast furnace had granulometries within 10 and 120 mm. However, the depletion of high-grade iron ore sources has made necessary the utilization of concentration processes with the purpose of enriching the iron ore. Because of these processes, a …
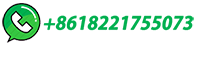
Exploring Steel Production: A Comprehensive Visual Process …
The Journey from Iron Ore to Steel: An Overview. The transformation of iron ore into steel is a remarkable process that involves a series of detailed steps. Beginning with the extraction of iron ore from the earth through mining operations, this raw material is then treated and prepared for the smelting phase. The extracted ore …
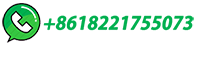
Iron Ore: Sedimentary Rock
Iron ore is a chemical sedimentary rock that people have used as an important source of metal.
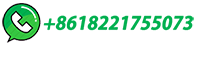
Iron Ore Pelletizing Process: An Overview | IntechOpen
The iron ore production has significantly expanded in recent years, owing to increasing steel demands in developing countries. However, the content of iron in ore deposits has deteriorated and low-grade iron ore has been processed. The fines resulting from the concentration process must be agglomerated for use in iron and steelmaking. …
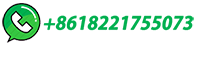
Ore
Ore is a deposit in Earth's crust of one or more valuable minerals. The most valuable ore deposits contain metals crucial to industry and trade, like copper, gold, and iron.
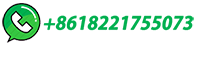
How iron is made
Iron ore is converted into various types of iron through several processes. The most common process is the use of a blast furnace to produce pig iron which is about 92-94% iron and 3-5% carbon with smaller amounts of other elements.
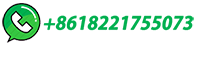
Iron ore | BHP
How is iron ore mined? From pit to port, our iron ore undergoes a series of processes before export. First, we explore the geology of the region to find the best iron ore prospects for our operations. Once the ideal site has …
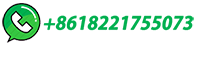
Iron Ore Processing, General
Making iron and steel from iron ore requires a long process of mining, crushing, separating, concentrating, mixing, agglomeration (sintering and pelletizing), and …
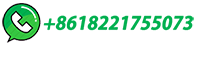
Iron Extraction and Purification / Steel | ChemKey
Iron ore isn't pure iron oxide – it also contains an assortment of rocky material. This wouldn't melt at the temperature of the furnace, and would eventually clog it up. ... This section deals with the types of iron and steel which are produced as a result of the steel-making process. Wrought iron.
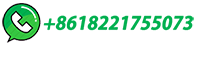
Mathematical model of thermal processes in an iron ore …
An unsteady one-dimensional model of an iron ore sintering bed with multiple solid phases was proposed. The proposed model confers a phase on each solid material. The present model was established with a series of conservation equations in the form of a partial differential equation for each solid phase and gas phase. Coke combustion, limestone …
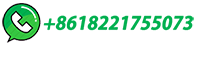
Iron Ore Processing, General
Making iron and steel from iron ore requires a long process of mining, crushing, separating, concentrating, mixing, agglomeration (sintering and …
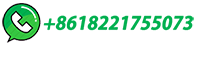
Hematite: A primary ore of iron and a pigment mineral
Hematite is the most important ore of iron.Although it was once mined at thousands of locations around the world, today almost all of the production comes from a few dozen large deposits where significant equipment investments allow companies to efficiently mine and process the ore.
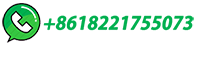
Iron Mining Process
Iron Mining Process. From blasting to crushing to separation – more than 85% of the iron mined in the United States is mined in northeastern Minnesota to make our nation's steel. Blasting Taconite is a very hard rock. Using explosives, the taconite is blasted into small pieces. ... The iron ore is separated from the taconite using magnetism ...
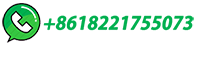
Introduction to Iron ore Pellets and Pelletizing processes
Process technology. There are four stages involved in the production of iron ore pellets. These stages consist of (i) raw material preparation, (ii) formation of green balls or pellets, (iii) induration of the pellets, and (iv) cooling, storage and transport of …
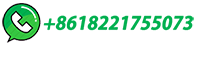
Steel Manufacturing: Process, Types, and Standards
The steel production process is a multi-faceted journey that begins with extracting and processing iron ore, a primary raw material essential to steel making. Iron ore undergoes a series of refining steps to extract the iron content, culminating in the creation of molten iron.
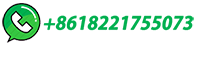
Iron ore beneficiation: an overview
Special focus has been given on the selection of beneficiation processes routes based on mineralogy for processing of low-grade iron ore, various steps involved in the test work along with the commonly used equipment in a commercial set up. A final recommended and operating process flowsheet for an iron ore deposit is also …
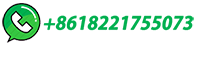
From Ore to Alloy: Navigating Ironmaking in Modern Steel …
At the heart of steel production lies the intricate process of ironmaking, where iron ore is transformed into molten iron and eventually alloyed to create various grades of steel. This article delves into the journey from ore to alloy, exploring the technologies, challenges, and innovations that shape modern ironmaking. 1.
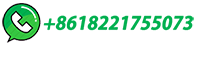
Iron processing | Definition, History, Steps, Uses, & Facts
Learn about the steps involved in iron ore processing, from crushing and grinding to separation. Contact Multotec experts for guidance on iron processing.
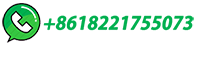
Iron Ore production in the Pilbara
Iron Ore production in the Pilbara Activities involved in finding, mining and processing iron ore at our Pilbara operations have been simplified in the following diagram.
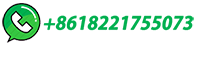
Iron Ore Processing: From Extraction to Manufacturing
Iron ore processing is a complex and vital process that transforms raw iron ore into usable steel. From exploration and extraction to grinding, beneficiation, and …
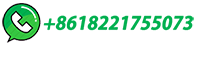
Processes for phosphorus removal from iron ore
Phosphorus can be removed from iron ore by very different routes of treatment. The genesis of the reserve, the mineralogy, the cost and sustainability define the technol ogy to be applied. The articles surveyed cite removal by physical processes (flotation and selective agglomeration), chemical (leaching), thermal and bioleaching processes.
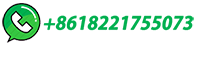
A review of ironmaking by direct reduction processes: …
DR processes reduce iron ore in its s lid state by the use of either natural gas o coal as reducing agents, and they have a comparative advantage of low capital costs, low emissions and production flexibility over the BF process. © 2019 The Autho s. Publ shed by Elsevier B.V. Peer-review under responsibility of the organizing committee of ...
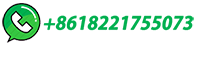
Drying and preheating processes of iron ore pellets in a …
A mathematical model of drying and preheating processes in a traveling grate was presented based on the laws of mass, momentum, heat transfer, and drying semiempirical relations. A field test was systematically carried out in a traveling grate. The effects of pellet diameter, moisture, grate velocity, and inlet gas temperature on the …
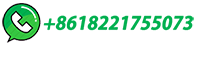