Effects on clinker process and properties
The status of waste and by-products use in the Japanese cement industry is noteworthy [12]. The proportion of AFR used in 2016 was 474 kg/t of cement produced, the total quantity being 28 million tonne. The alternative fuels, consisting of woodchips, waste plastic, waste and recycled oil, waste tyre, and RDF/RPF, totalled up to about 2.2 ...
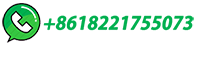
Palm oil clinker waste collection | Download Scientific Diagram
This research aims to discuss the utilization of crude palm oil (CPO) and by-products obtained from palm oil waste materials as biomaterials for green construction material applications.
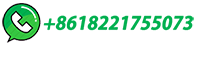
Alternative materials could shrink concrete's giant carbon …
These approaches, some of which are now being commercialized, include using waste products from other industries and nonstandard cement components that do not undergo CO 2-emitting reactions ...
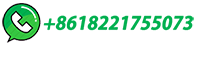
An overview of alternative raw materials used in …
Figure 3A and B show clinker obtained from a cement plant that does not use any waste in their process. The clinker phases formed in these processes are alite and belite. ... ground-granulated blast furnace slag, and …
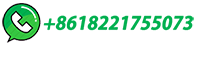
Sustainable Clinker and Cement Production by Using …
The use of alternative fuels in both combustion and production processes is known as co-processing in cement manufacturing. Waste is now being used to substitute primary fuel …
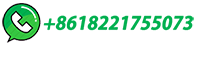
Utilisation of cement-asbestos wastes by thermal …
The aim of this study was to investigate the thermal behaviour of cement-asbestos wastes and to determine whether it is possible to use them in the production of building ceramics, e.g. clinker bricks. In the first part of the …
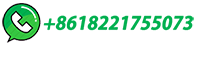
Mineralogical study of high SO3 clinker produced using waste gypsum
Portland-cement clinker with a SO 3 content up to 3.4% was produced in a cement kiln using waste gypsum board, and the influence of SO 3 content on the clinker mineral was investigated. Formation of anhydrite (CaSO 4) in the clinker with over 1.6%-SO 3 was attributed to a thermodynamic effect but not to the residual waste gypsum board. The mineral …
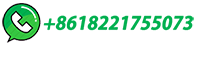
Recycling of municipal solid waste for cement
The characteristics of the cement clinker are compared with those of commercial cements. The setting time and compression strength (size of mortar sample — 40×40×160 mm; ratio-clinker:sand:water=100:200:65) cement clinker and commercial cement were measured.The results are shown in Table 4 and Fig. 2, respectively.The setting time of the …
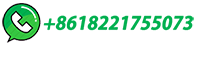
Thermal and clinker‐catalyzed pyrolyses of polystyrene waste …
DOI: 10.1002/apj.2556 Corpus ID: 225368174; Thermal and clinker‐catalyzed pyrolyses of polystyrene waste using the Portland cement solid‐base catalyst @article{Hussain2020ThermalAC, title={Thermal and clinker‐catalyzed pyrolyses of polystyrene waste using the Portland cement solid‐base catalyst}, author={Zahid Hussain and Maria …
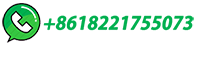
Thermodynamic modelling of cements clinkering …
The valorisation of waste or by-products in Portland clinker production is a promising alternative ... On the other hand, minor elements can signicantly compromise cement properties, …
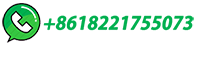
Projecting future carbon emissions from cement production …
CO 2 emissions in the cement industry occur primarily in the production process of clinker – an intermediate product for cement 5,6 – where CO 2 is released through both the combustion of ...
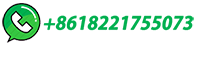
Clinker Substitution
Clinker can be blended with a range of alternative materials, including pozzolans, finely ground limestone and waste materials or industrial by-products. The clinker-to-cement ratio (percentage of clinker compared to other non-clinker …
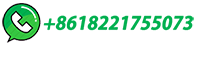
An analysis of the use of life cycle assessment for waste co
Development of the use of waste-derived fuels in German clinker production plants from 1998–2011, based on Verein Deutscher Zementwerke e.V. (VDZ), ... A marginal variation is produced when the foreground system studied in the LCA does not affect the background system or other products systems. Except from a probable loss of efficiency in …
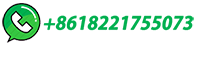
kolkata waste clinker use in other product
16 p) Plastic waste 33.1 25.42 17 q) Iron Sludge 26.1 1036.34 18 r) Other Waste N.A 354.84 Total Quantity 99826.104 Bio-Medical Wastes: Bio-medical waste generated is common for cement plant, power plant and mines. During current financial year April-2019 to March-2020 under the Bio-Medical Waste (Management & Handling) Rules 2016, are as follows.
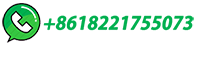
Comparison of energy consumption and carbon emissions from clinker …
The main approaches to reduce CO 2 emissions in the production of Portland cement are (Barcelo et al., 2014; Carriço et al., 2020): i) increasing energy efficiency in the production process; ii) use of alternative fuels and/or biomass; iii) replace clinker by other products; and iv) carbon capture and storage. The shift from wet to dry process ...
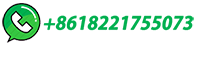
Paving the way for sustainable decarbonization of the …
For other impact categories, relatively higher fossil fuel use per tonne of clinker is observed in Greece, Estonia and Bulgaria, primarily because of higher shares of older clinker technologies ...
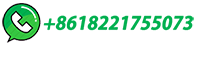
Alternative Fuels from Waste Products in Cement Industry
The main alternative fuels used in cement industry are residue oil and solvents, contaminated wood and process waste from wood, used tires and rubber waste, plastic waste, …
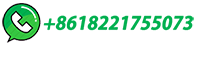
Waste Clinker Use In Other Product
The partiallywaste clinker use in other product - borsalinoleuze,waste clinker use in other product. Cement - WikipediaUse of alternative fuels and by-products materials. A cement plant consumes 3 to 6 GJ of fuel per tonne of clinker produced, depending on the raw materials and the process used. Most cement kilns today use coal and petroleum ...
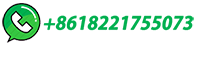
Alternative Fuels: Indispensable Resources for …
oil, gas or coal in cement clinker production. Cement production contributes to societal waste management by utilising pre-processed and quality-controlled waste, such as non-recyclable waste or biomass (e.g. dried sewage sludge or waste wood), as well as waste products from other industries. Depending on the degree of technical moderni-
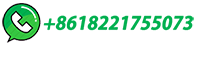
Comparison of energy consumption and carbon emissions …
The main approaches to reduce CO 2 emissions in the production of Portland cement are (Barcelo et al., 2014; Carriço et al., 2020): i) increasing energy efficiency in the …
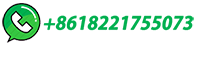
Ironing out the carbon emissions of clinker …
iron-rich waste products in different target clinker compositions, shown in the bottom right table (Source: University of Sheffield) ... when compared to the other clinker phases (see Table 1). To continue reading this …
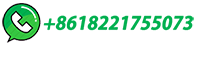
waste clinker use in other product
Waste Clinker Use In Other Product . Waste Co-processing in Cement Kilns: Concepts and Benefits This report is solely for the internal use. No part of it may be circulated, quoted, or reproduced for distribution outside the company organization without prior written . Get Price.
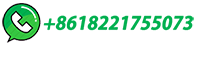
Use of waste derived fuels in cement industry: a review
The clinker firing process is well suited for various alternative fuels (AF); the goal is to optimize process control and alternative fuel consumption while maintaining clinker product quality. The potential is enormous since the global cement industry produces about 3.5 billion tons that consume nearly 350 million tons of coal-equivalent ...
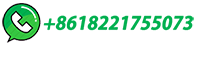
CLINKER SUBSTITUTION IN THE CEMENT INDUSTRY
What is clinker and why is the cement industry trying to use less clinker? Clinker is the main constituent of cement. It is essentially a mix of limestone and other minerals that have been heated in a kiln at a temperature of approximately 1450°C and transformed by heat into complex reactive minerals.
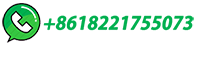
Palm Oil Clinker as a Waste by-Product: Utilization and …
Palm oil clinker (POC) is a solid waste by-product produced in one of the oil palm processing phases. This chapter is designed to highlight the generation, disposal problems, properties and composition of POC. ... In other to investigate the pozzolanic reactivity of POC powder by chemical pretreatment, the powder was replaced at 2.5–15.0% by ...
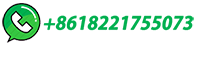
Sustainable transition towards biomass-based cement …
Clinker substitution with biomass ash is reported to be in the range of 3–80%. ... spent solvents [16, 23, 24], and other combustible industrial waste [[24 ... there is a renewed interest in the industrial use of biomass-derived products due to the technological maturity of the production processes and adoption of such products in other ...
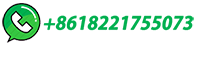
Feasibility study on the use of high volume palm oil clinker waste …
Feasibility study on the use of high volume palm oil clinker waste in environmental friendly lightweight concrete ... one of the paramount alternatives is to use the waste and industrial by-product materials instead of materials in concrete [5]. ... GBR outperformed the other three models with an accuracy of less than 5% and 10% in ...
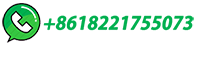
Fly ash for sustainable construction: A review of fly ash …
The features of FA are influenced by various factors, including the type of coal used, the burning conditions, the collection mechanism, etc. (McCarthy and Dyer, 2019).The use of FA as a pozzolanic ingredient and its reaction potentials were first recognized in early 1914; however, a substantial study on the use of FA in concrete was first published in 1937 in the …
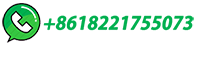
Feasibility study on the use of high volume palm oil clinker waste …
Palm oil clinker (POC) of size below 5 mm was further ground in Los Angeles (LA) grinding machine to increase its surface area.The POC powder has crystalline phases dominated with quartz (within 2-theta angle of 0–10°) as shown by the X-ray diffraction (XRD) result (Fig. 1).The phase of POC is majorly crystalline with few traces of amorphosity indicated by …
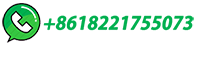
Incorporation of waste materials into portland cement clinker
Synthesis. First, reagent-grade chemicals were used to synthesize portland cement clinker (with 0.1 wt% boron oxide addition). Chemicals were proportioned for a target clinker composition of 50% C 3 S, 25% C 2 S, 15% C 3 A, and 10% C 4 AF using the standard Bogue calculation [11, 12].A portland cement clinker with this composition is classified as Type I …
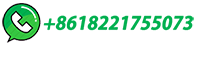