Foundry Sand: Life of a Casting | Reliance Foundry
Molding sand is at the heart of the sand casting process. It must hold a shape well and capture the fine details of a casting, yet be permeable enough to allow gases to escape. …
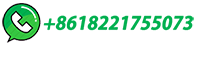
Moulding Core Making and Types of Moulding Sands
The moulding is a process of making a cavity (or mould) out of sand by means of a pattern. The molten metal is poured to produce castings.
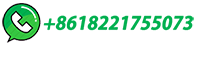
The 6-Step Process of Sand Casting | Molding | OneMonroe
The six steps of the sand casting process are; placing the mold in patern in sand, setting up the gating system, removing the mold pattern, pour molten metal into mold cavity, wait for the metal to cool, the final step is …
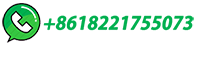
What is Sand casting & How does it work? Pros & Cons casting
During the sand casting process, the material is heated to the correct temperature to melt and sometimes treated to modify the chemical composition to achieve the required material properties. ... Undercuts in sand casts are features that prevent and stop the pattern from being removed during the mould making stage. Usage of core …
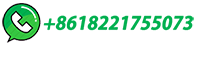
Foundry processes: the recovery of green moulding sands for core
The dry mechanical process is economical and effective, but, due to the high gathered acid request value (∼10 ml), requires a change in the cold-box core making foundry operations if this recovered foundry sand is to be used, and an individual study of the organic additives mixture is necessary for each plant in order to comply with the core ...
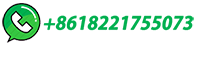
Learn Sand Casting: Types, Steps, Animation, Diagram, …
Sand casting is a cost-effective manufacturing process carried out in a foundry to produce casting in a mould using various types of sand material.
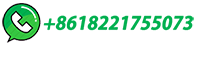
Core-Making: Fundamental Concepts and Processes
Core-making is an essential process in the production of metal castings, primarily for iron and steel foundries. It involves the creation of a solid object called a core, which is placed inside ...
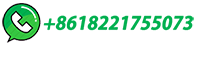
The 6-Step Process of Sand Casting: A Step-by-Step Guide …
Step1:Pattern & Core Making. Wooden, plastic, or metal patterns create the mold cavity. Sand cores form internal features like holes. Care in Pattern Making: …
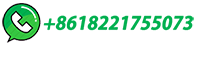
A Revolutionary Inorganic Core and Mold Making Process
With the elimination of a post-production treatment for the core or mold using ethanol as a carrier, the resulting new development makes the Cadic Convert Process considerably simpler, because the nano silica compounds can be added to the sand mix prior to the production of the core or mold in any organic resin-bonded …
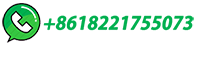
USE OF COLD BOX PROCESS
With this process, for the first time, a core or mould could be stripped from the core box and cast immediately. Cores could be produced in seconds with good strength, excellent ... core making V. The prepared sand should be quickly delivered to the core making machine with minimum of variation. 4. CORES I. During high humidity period, the ...
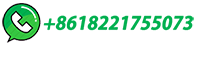
Molding Sand: Constituents, Types and Properties
Build an understanding of the uses of molding sand, its components, and properties. Explore natural and synthetic molding sands.
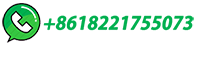
STEPS FOR MAKING SAND CASTINGS – Bajrang Engineering
The process cycle for sand casting consists of six main stages, which are explained below. They Are (1) Mould Making (2) Core Making (3) Clamping (4) Melting & Pouring (5) Cooling (6) Removal (7) Trimming. (1) Mould Making-The first step in the sand casting process is to create the mold for the casting.
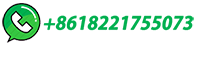
(PDF) Parameter Optimization of No Bake Core Making Process …
Inherent drawback of CO 2 moulding i.e Poor knockout property made the subject of moulding sand reclamation more prominent. In the present paper it is attempted for optimization of the process parameters of CO 2 moulding process made of reclaimed sand for better knockout property.
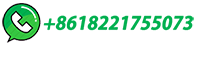
An overview of sand core making in casting
An overview of sand core making in casting. Published - 11th Jun 2019. Cores are used in our foundry casting process to create cavities as well as internal and external features which cannot be generated by our patterns.
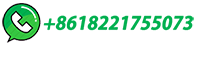
Sand Casting Process, Defects, Design
The sand casting process involves the use of a furnace, metal, pattern, and sand mold. The metal is melted in the furnace and then ladled and poured into the cavity of the sand mold, which is formed by the pattern. ... The production cost includes a variety of operations used to cast the part, including core-making, mold-making, pouring, and ...
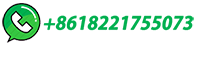
Green Sand Moulding: Process, Methods, Diagram, and …
Green sand moulding is a traditional and widely used foundry process that forms the backbone of metal casting operations. It involves the creation of moulds using a mixture of silica sand, water, and a clay binder, giving …
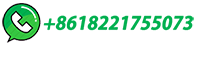
Foundry Sand Casting Process: Step by Step
Learn all about the sand casting manufacturing process from start to finish with this simple step-by-step explanation.
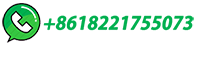
Foundry Sand: Life of a Casting | Reliance Foundry
Ferrous foundries (those dealing with iron and steel) usually use silica sand, sometimes known as quartz sand. Silica sand has long been used in core making, so switching to using the same aggregate throughout the casting process has made the process of managing foundry supplies easier. Silica sand is the most commonly used type of …
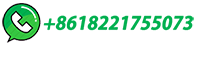
Sand Casting Process, Defects, Design
Mold-making - The first step in the sand casting process is to create the mold for the casting. In an expendable mold process, this step must be performed for each casting. A …
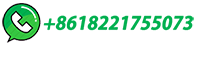
The Cold-Box process in the production of foundry cores
Cold-Box technology is a series casting sand core production process based on a reaction between sand and resins at room temperature, accelerated by a catalyst. It has been used for over 50 years and continues to be the main method of producing sand cores due to its wide range of applications, efficiency and economic convenience.
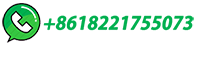
Moulding Sand, Types, Composition and its Properties
Moulding sand and core sand depend on the size, shape composition and distribution of the sand grain, clay content, moisture, and additives. Increased demand for good surface finish and high precision in casting requires certainty in the quality of the mould and the sand of the core.
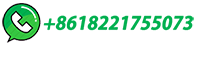
Core Making In Casting Process | Coke Making in Foundry | Sand Core …
Core making in foundry method/steps are: 1) Preparing core sand. 2) Core moulding using a core box. 3) Baking core in oven. 4) Core finishing.
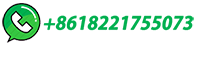
Coremaking: Life of a Casting | Reliance Foundry
Cores are made by many of the same methods employed for sand molds. In addition, core blowers and screw feed machinesare used. Core blowers force sand into the core box by compressed air at about 100 lb/in2. They can be used for making all types of small- and medium-sized cores. …
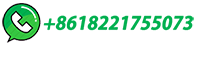
What Are Cores in the Sand Casting Process
Cores will be made from the same resin sand used in the sand casting process. The sand is placed into a core box that has the desired interior pattern for the part
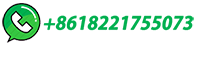
The effect of sand quality on the bending strength and …
The hot-box process is another widely used core-making technology that is suitable for the production of high-strength cores with high dimensional accuracy under relatively short cycle times. During this process, the sand mixture, which contains a phenolic and/or furfuryl-alcohol-based resin, is blown into a preheated core box.
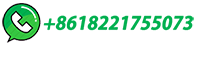
MOULDING SAND PROPERTIES FOR SAND CASTING
During Sand casting, we uses sand for the preparation of mould. It is the moulding sand properties which improves the quality of the casting. If a sand of suitable property is chosen, than it greatly minimises the casting defects that may be produced during the mould preparation and casting.
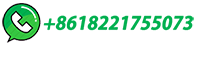
Sand Cast Molding & Core Making | Sivyer Steel Castings
Using the sand cast molding method, we make cores and molds using no bake resin for the production of steel castings.
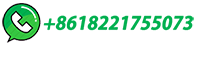
The Cold-Box process in the production of foundry cores
Cold-Box technology is a series casting sand core production process based on a reaction between sand and resins at room temperature, accelerated by a catalyst. It has been …
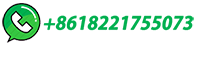
Sand Casting
Sand casting is a process where molten metal is cast in a mould made from a sand mixture. ... But nowadays it is also suitable for high volume production thanks to automated equipment for making sand moulds. ... (singly or in combination: sulfur, boric acid, potassium fluoborate, and ammonium fluosilicate) in the molding and core sand …
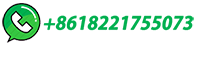
What is Sand Casting | Process | Application | JC casting
The basic process of the traditional sand casting process has the following steps: sand preparation- mold making- core making, modeling-pouring-sand falling- grinding processing- inspection, etc. Sand mixing. Preparation of molding sand and core sand. For modeling. Generally, a sand mixer is used to mix the old soil and the …
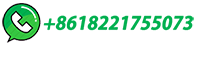