How Cement is Made
Cement Manufacturing Process. Joseph Aspadin (Great Scientist) first started manufacturing cement in England. First manufacturing name of cement is ordinary Portland cement (OPC) because when cement mixes with water it converts to a solid mass after some period and this solid mass (looks like solid stone) is rooted in the Portland (England). India is …
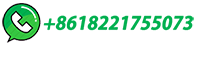
Cement Manufacturing Process: 6 StepsTo Make …
Before starting an excellent cement plant, it is necessary for a new beginner to learn cement manufacturing process first. So AGICO CEMENT who has plenty of experience in supplying cement plant and …
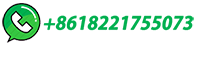
How Cement is Made
Stage of Cement Manufacture. There are six main stages of the cement manufacturing process. Stage 1: Raw Material Extraction/Quarry The raw cement ingredients needed for …
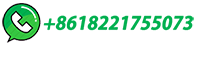
Explore Raw Material Used For Cement Production | JK Cement
From limestone to clay and supplementary additives, each ingredient contributes to the durability and strength of cement. Let us learn about the essential raw materials used for cement production. Composition of Cement. There are two primary cement manufacturing components that form the distinctive properties of cement.
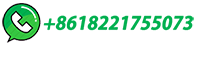
Cement Production
The dry process uses less water during the raw material grinding and crushing, requiring less heat input for the dehydration stage. ... The high level of CO 2 emission happens when burning fossil fuels to generate heat to initiate the cement manufacturing process and thermal decomposition of calcium carbonate in the progression of manufacturing ...
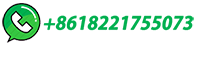
A practical guide to improving cement manufacturing …
The cement production process 1. The Quarry: The cement production process begins with the extraction of limestone and clay from the quarry. 2. Crusher and Pre-Blending: The material is …
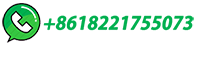
11.6 Portland Cement Manufacturing
11.6 Portland Cement Manufacturing 11.6.1 Process Description1-7 Portland cement is a fine powder, gray or white in color, that consists of a mixture of hydraulic ... E. Secondary crushing -10 F. Screening -11 G. Raw material transfer -12 H. Raw material grinding/drying …
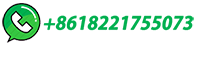
Manufacturing process
The cement manufacturing process starts from the mining of raw materials that are used in cement manufacturing, mainly limestone and clays. A limestone quarry is inside the plant area and a clays quarry is as far from the plant area as 25 km. The limestone is excavated from open cast mines after drilling and blasting and loaded onto dumpers ...
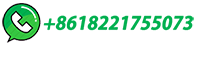
Portland Cement Manufacturing – Ordinary …
The Portland cement manufacturing process can be divided into 6 steps: raw material crushing, pre-homogenization, fine grinding, clinker production, cement grinding, cement packing, etc. In these processes, we need the assistance of …
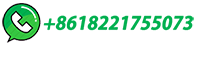
Cement: Materials and manufacturing process
Cement Manufacturing Process 1 Extraction. Materials are extracted / quarried / recovered and transported to the cement plant. 2 Crushing and milling. The raw materials, limestone, shale, silica and iron oxice are crushed and milled into fine powders. 3 Mixing and preheating.
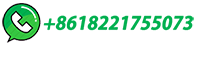
Cement Manufacturing—Technology, Practice, and …
The primary cement manufacturing process involves the mining of raw materials, mainly limestone and clay, which are used in cement manufacturing. In most of the cases, the limestone and clay are excavated from open cast mines by drilling and blasting and other appropriate processes in mines. ... Fossil fuels preparation consists of crushing ...
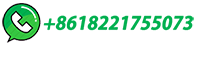
Limestone Crushing And Sand-Making Plant
As an essential building material with a long mining history, limestone is the raw material for manufacturing cement, aggregates, lime, and calcium carbide in modern industry. With the increasing demand for machine-made sand, limestone sand production also become popular. ... This equipment can replace the rough crushing process of the stone ...
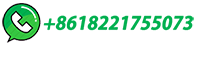
What Do You Know About Wet Process Of Cement Production
Therefore, the crushing of limestone plays an important role in the material crushing of cement manufacturing plants. Meanwhile, the prehomogenization technology is to use scientific stacking and retrieval technology to achieve preliminary homogenization of raw materials during the storage and retrieval process of raw materials, so that the raw ...
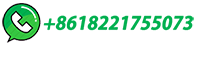
A life-cycle assessment of Portland cement manufacturing: …
Traditional Portland cement is composed primarily of calcium silicate minerals (Table 1).The raw materials are quarried or mined and transferred to the manufacturing facility to be crushed and milled into a fine powder before entering a preheater and eventually a large rotary kiln where materials reach temperatures greater than 1400 °C [7].The clinker or kiln product is …
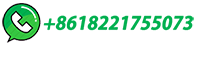
Cement Manufacturing
The preparation of cement involves mining; crushing, and grinding of raw materials (princi- ... mixing the clinker with gypsum; and milling, storing, and bagging the finished cement. The process generates a variety of wastes, including dust, which is captured and recycled to the pro- ... Cement Manufacturing. 277. Air Emissions. A maximum ...
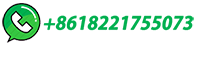
The Manufacturing Process
The Manufacturing Process; ... Co-processing. Crushing. Raw meal grinding. Preheating. Precalcining. Clinker production in the rotary kiln. Cooling and storing. Cement grinding. Storing in cement silos To download the cement manufacturing process fact sheet, please click here. Information; Policies;
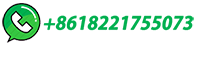
Everything you need to know about Crushers in Cement …
The roller crushers are used for moist and sticky materials. Generally the machines have to be rigid enough to crush also hard inclusions. As the reduction ratio is only about 5:1 …
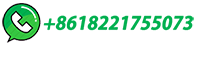
Know All About Cement Manufacturing Process in India | mycem cement
After crushing, the crushed limestone is piled longitudinally by an equipment called stacker / reclaimer. The stacker deposits limestone longitudinally in the form of a pile. ... Discover the detailed steps of the cement manufacturing process in India. Heidelberg Cement offers insights into modern techniques and industry-leading practices.
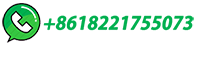
Inside the Cement Manufacturing Process
The Cement Manufacturing Process. The production of cement involves a series of steps that transform raw materials into the final product. The process begins with the crushing and grinding of raw materials, followed by …
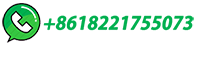
Cement Manufacturing—Technology, Practice, and …
The primary cement manufacturing process involves the mining of raw materials, mainly limestone and clay, which are used in cement manufacturing. In most of …
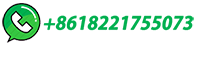
Cement Manufacturing and Process Control | SpringerLink
The major raw materials used as a source of CaO for cement manufacturing are limestone, chalk, marl, etc. These raw materials by virtue of their natural occurrence contains other mineral impurities e.g, MgO, SiO 2, Al 2 O 3, Fe 2 O 3, alkali compounds, and sulfides.These impurities play an important role to influence the cement manufacturing …
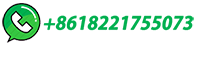
Cement Clinker Manufacturing Process with Reactions
Cement Clinker Manufacturing Process with Reactions Syeda Tahsin Hasan. Extraction and Preparation of Raw Materials. The main raw materials (limestone, clay chalk or basalt) are quarried from natural rocks. They are crushed and transferred to pre-blending storage where other substances (such as sand, iron ore, bauxite, shale, slag, fly ash) are ...
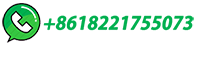
A critical review on energy use and savings in the cement industries
Details of cement manufacturing process for few selected countries around the world can be found in [18], [38], [42], [45], [46]. ... A final product is formed with the crushing action of the balls and mixing the clinker with additives. Then the final output product cement is ground in a cement mill. 3.1.9.
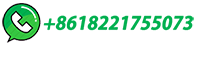
Cement
A first approximation of the chemical composition required for a particular cement is obtained by selective quarrying and control of the raw material fed to the crushing and …
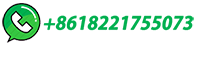
Cement manufacturing process: Step-by-step …
P ortland cement is by far the most common type of cement in general use around the world. This articles looks at the cement manufacturing process in 4 steps. Step 1: Mining. The first step of Cement manufacturing …
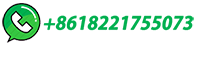
How To Choose Cement Crusher? | Jaw Crusher, Cone Crusher
Cement is a kind of hydraulic cementitious material, as for the cement manufacturing process, limestone and clay are used as the main raw materials, which is made into raw material by crushing, mixing, grinding, calcined into the cement kiln to make cement clinker, adding an appropriate amount of gypsum (sometimes also add mixed materials or ...
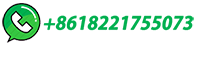
The Cement Plant Operations Handbook
testing – 11. Process control analysis – 12. Chromate passivation – 13. Cement quality – 14. Setting time – 15. ASTM cement types and specifications – 16. European EN 197 cement specification – 17. Composite cements (intergrinds and blends) – 18. Supersulphated cement – 19. Calcium aluminate cement (CAC) – 20. Shrinkage-
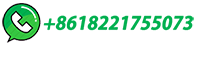
Chapter 4 Cement Manufacturing and Process Control
First, crushing reduces the rocks to a maximum size of about 6 inches. The rocks ... Fig. 4.1 Flow sheet of cement manufacturing process 4 Cement Manufacturing andfiProcess Control. 63 4.3 Fuel Different fuels like coal, oil, petcoke, gas, etc. are used as the source of heat energy
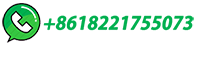
Types of Cement Crusher Machines
A cement crusher machine is a specialized equipment used in the crushing and grinding of raw materials. These include limestone, clay, shale, and other materials. The crusher grinds these materials into smaller pieces to be used in the cement manufacturing process.
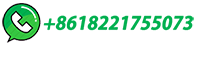
PPC Cement Manufacturing Process
Portland Pozzolana Cement Manufacturing Process. Portland pozzolana cement shall be manufactured by mixing and inter-grinding Portland cement clinker, pozzolanic materials, and gypsum. The manufacturing process is approximately the same as ordinary Portland cement, which can be divided into four processes: raw material crushing, raw material ...
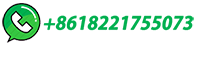