Selecting the right type of crushing equipment
Primary HSI crushers are considerably wider than primary breakers at comparable capacity ratings. Secondary HSI crushers – These crushers are characterised by a high 10:1 reduction ratio and by their suitability for generating a cubical product. They can also be used for a variety of applications.
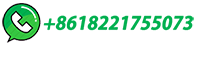
Checking Crusher Gap -Measuring Crusher …
To check the gap on a crusher a procedure called LEADING is done. A lump of lead, whose dimensions are greater than the gap of the crusher, is lowered through the crusher while the crusher is running.
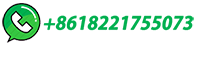
AMIT 135: Lesson 5 Crushing – Mining Mill Operator Training
Measurement of the crusher's closed side setting (CSS) varies depending on the jaw profile that is being used and has an impact on the crusher's capacity and product gradation. ... This expression is valid for primary crushers. For secondary cone crushers, the 0.75 value takes a value of unity. Advantages vs. Disadvantages of Gyratory ...
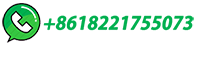
Crushing and Screening Handbook
Primary gyratory crushers – ideally suited to all high-capacity primary hard rock crushing applications. Jaw crushers – we have more installed jaw crushers than anyone in the world. The lead-ing choice due to their high reduction ratio and heavy duty design. Cone crushers – capacities available to suit all
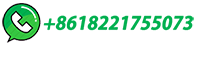
TECHNICAL NOTES 5 CRUSHERS
Jaw crushers are operated to produce a size reduction ratio between 4:1 and 9:1. Gyratory crushers can produce size reduction ratios over a somewhat larger range of 3:1 to 10:1. The primary operating variable available on a crusher is the set and on jaw and gyratory the open-side set (OSS) is specified. This reflects the fact that
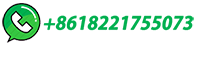
Liner wear and performance investigation of primary gyratory crushers
Wear measurements were taken for in-service crushers during the research period using a novel laser profile measurement device. Data from the wear measurements was correlated with crusher production information such as current draw and throughput. ... Related studies have been performed for primary crushers, both Jaw crushers Lindqvist (2005 ...
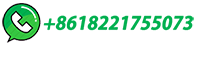
Primary Crusher vs. Secondary Crusher: Understanding Their …
While primary crushers are responsible for breaking down larger rocks and stones into smaller particles, secondary crushers are used to further refine these particles into the desired size and shape. The primary crusher is the first stage in the crushing process, while the secondary crusher is the second stage. ...
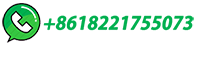
Jaw Crusher
Overview of size reduction of raw materials of the cement industry. Vipin Kant Singh, in The Science and Technology of Cement and Other Hydraulic Binders, 2023. 4.2.1 Jaw crushers. Jaw crushers are used for the primary reduction of hard and abrasive materials used for cement manufacture. Jaw crushers 3 are of either Blake-type or Dodge-type and operate by applying …
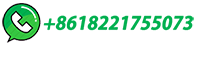
Primary Crusher Level Measurement
In the mining and minerals industry, the deployment of advanced sensor technologies is essential to smooth operations and safety. To detect a reversing truck (a) An Acoustic low-frequency 15 kHz transducer should be used for self …
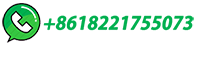
Understanding Effects of Crushing Mechanism on …
The study uses basaltic aggregate produced from two different crushing mechanisms (i) jaw, cone and VSI (vertical shaft impactor) as primary, secondary and tertiary crushers, respectively (Jaw-Cone-VSI, denoted as JCV); and (ii) jaw and HSI (horizontal shaft impactor) primary and secondary crushing units, respectively (Jaw-HSI denoted as JH).
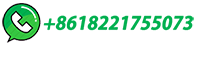
Types of Crushers: What You Need to Know
The demand for large-mouthed jaw crushers skyrocketed as the industry began to understand their potential as primary crushers in rock quarries. Through Thomas A. Edison's research and development, giant machines were innovated and placed around the United States. Smaller-sized jaw crushers were also developed as secondary and tertiary crushers.
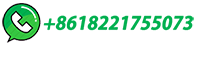
Cone Crushers (Parts of a Cone Crusher) Explained
Jaw Crushers; Cone Crushers; Typically, the initial crushing stage is completed using either gyratory crushers or jaw crushers. It is often the case that there will be only one crusher installed, and this will be referred to as the primary crusher. Cone crushers are more often used for 2nd, 3rd & 4th stage crushing steps (although not always).
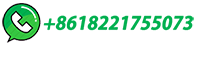
The Complete Guide to Primary Crushing, Secondary …
As the term 'primary' implies, these crushers are used in the first stage on any size reduction cycle. The primary crusher is the link between chemical comminution (blasting) and the …
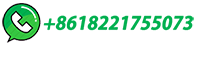
Gyratory Crusher
Gyratory crushers are principally used in surface-crushing plants. The gyratory crusher (Figure 6.5) consists essentially of a long spindle, carrying a hard steel conical grinding element, the head, seated in an eccentric sleeve.The spindle is suspended from a "spider" and, as it rotates, normally between 85 and 150 rpm, it sweeps out a conical path within the fixed crushing …
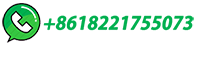
McLanahan | How To Size A Jaw Crusher
Jaw Crushers are primary crushers used in the first stage of the crushing process. They feature a V-shaped cavity (called the crushing chamber) that is formed by a moving piece of steel and a stationary piece of steel (called …
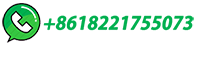
Closing the gap
After spending countless hours at numerous mine sites trying to optimise crusher performance and explaining the need to measure the CSS of primary crushers accurately to management, Brant said seeing the C-Gap …
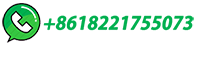
What is a Jaw Crusher and Selecting the Right One
Many factors make laboratory jaw crushers the optimum selection for effective and efficient primary crushing of hard, brittle, rock-like materials. Laboratory models are available with sample top sizes from 1in to 8in (25mm to 203mm). Jaw plates are available in a variety of material types to optimize performance with different materials.
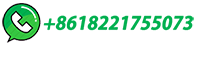
Compression mining crushers | Primary crushers | FL
Compression mining crushers for your mining aggregate/cement needs field By using high intensity compressive forces, your materials can be broken down into much smaller particles. However, the process is incredibly wear intensive, and can easily take its toll on your equipment and your operation.
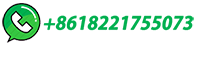
Jaw Crusher Explained
Blake type crushers come in various sizes and are commonly used for primary and secondary crushing roles. How Jaw Crushers Are Sized. Jaw crushers are sized based upon the dimensions of the top feed inlet (gape) or the dimensions of the jaws. For example, a 32 x 54 sized jaw crusher will measure 32 inches from the movable to stationary jaw ...
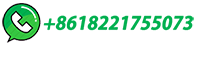
What Is Primary, Secondary, and Tertiary Crushing?
The degree to which material is reduced through stages of primary, secondary, and tertiary crushing can depend on the type of material, like aggregate, concrete, and asphalt, and can also depend on the variety of output sizes needing produced. ... jaw crushers, and cone crushers that are critical for any stage of crushing. When you speak with a ...
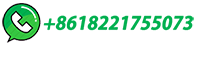
Superior™ MKIII Series primary gyratory crushers
Superior™ MKIII primary gyratory crushers provide high throughput and less downtime to bring maximum efficiency to your operation. Menu Close ... Detailed reports and intelligent measurement of crushing operations. Easy and safe …
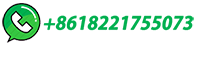
Primary Crusher Selection & Design
How you select your primary crusher will be based on factors like moisture content, maximum rock lump size, material density SG, abrasion index, degradability and it being prone to dusting or not. The crusher capacities …
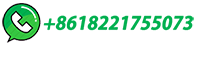
iCrusher
iCRUSHER KEY BENEFITS FOR PRIMARY CRUSHERS. increase Crusher Availability by up to 29 % ... The solution monitors the material in the dump pocket to provide the automation system with high-speed level measurements and detects unusual changes in the 3D surface profile and material volume flow in the different segments to provide highly reliable ...
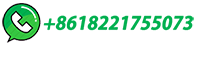
The Importance of Primary Crushing in Mill Feed Size …
The application of image analysis to measure the feed and product size on-line has provided detailed insights into crusher operating conditions. Figure 5, page I-195, shows the fluctuation …
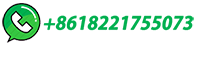
Mining crushers SuperiorTM MKIII Primary Gyratory
Outotec's line of Superior™ Primary Gyratory crushers are designed to meet the demand for high efficiency and high capacity mining installations. Superior™ MKIII is the first high speed Gyratory. The new features allow significant CAPEX reduction of a primary crushing stage from the retaining wall to the primary stock pile.
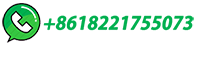
Primary Crusher Selection & Design
How you select your primary crusher will be based on factors like moisture content, maximum rock lump size, material density SG, abrasion index, degradability and it being prone to dusting or not. The crusher capacities given by manufacturers are typically in tons of 2,000 lbs. and are based on crushing limestone weighing loose about 2,700 lbs. per yard3 and …
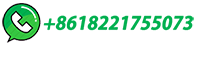
Superior™ MKIII 50-65 primary gyratory crusher
The latest Superior™ MKIII primary gyratory crushers generation is again better, more efficient, safer, and simpler than the previous one. ... improving the profitability of primary crushing. Intelligent measurement and analytics of crushing operations by control systems such as **VisioRock® and VisioTruck® provide detailed reporting and ...
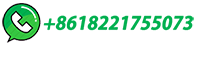
Compare Gyratory Crusher vs Jaw Crusher
To accomplish this reduction in size takes several steps or stages of crushing and grinding. Primary crushing is the first of these stages. Generally speaking there are two types of primary crushers, lets compare them: GYRATORY CRUSHER or a JAW CRUSHER. Although they don't look anything like they do have similarities that put them into ... title="Compare …
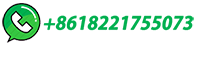
Choosing the right primary crusher for your …
The first step in choosing a primary crusher takes place at a high level. It's necessary to identify the purpose the crusher will be used for. This purpose is a given that precedes the entire decision-making process. Sometimes, a …
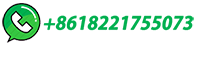
How to Select the Right Primary Crusher | Mellott
1. Identify The Purpose Of The Crusher. The first step in selecting a primary crusher takes place at a high level. It's necessary to identify the purpose the crusher will be used for. This purpose is a given that precedes …
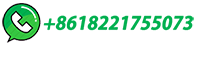