Primary Crusher
4.2.2 Jaw Crusher Circuits. Primary jaw crushers typically operate in open circuit under dry conditions. Depending on the size reduction required, the primary jaw crushers are followed by secondary and tertiary crushing. The last crusher in the line of …
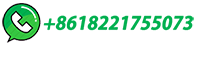
Stone Crusher Machines In Philippines
Stone crusher machines are equipment designed to crush or break down large stones, rocks, and minerals into smaller pieces, gravel, or dust for various applications. According to the customer's final particle size requirements for crushed aggregate, it has different crushing stages with various machines, including primary crushing equipment, medium crushing machine, …
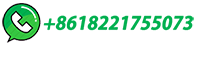
Jaw Crusher
Overview of size reduction of raw materials of the cement industry. Vipin Kant Singh, in The Science and Technology of Cement and Other Hydraulic Binders, 2023. 4.2.1 Jaw crushers. Jaw crushers are used for the primary reduction of hard and abrasive materials used for cement manufacture. Jaw crushers 3 are of either Blake-type or Dodge-type and operate by applying …
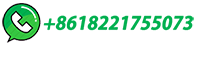
Primary Crushing | AllMinings
Here's a concise example of a list highlighting key aspects of the primary crushing process in a mining operation: Critical Commencement; ... Jaw Crusher: This stalwart machine exerts direct pressure on the material, effectively compressing it between two rigid surfaces. It is known for its simplicity, ruggedness, and versatility, making it ...
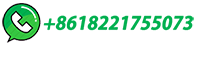
Crushing 101 – Different types of crushers for distinctive needs
In the single toggle jaw crusher, an eccentric shaft is on the top of the crusher. Shaft rotation, along with the toggle plate, causes a compressive action. ... Horizontal shaft impact crushers are used in primary, secondary or tertiary crushing stage. They reduce the feed material by highly intensive impacts originating in the quick rotational ...
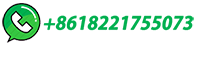
COMPARISON OF SECONDARY CRUSHING …
primary crushing operations are performed using jaw and gyratory type crushers. In contrast, the others such as cone, roll, vertical (VSI), and horizontal (HSI) shaft impact
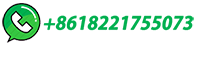
Crushing and Screening Handbook
the crusher and scalp out fi nes. Primary gyratory crushers – ideally suited to all high-capacity primary hard rock crushing applications. Jaw crushers – we have more installed jaw …
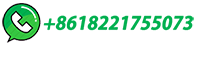
A Comprehensive Guide to Secondary Crusher Types
Learn about the different types of secondary crushers, including impact crushers, cone crushers, roll crushers, and jaw crushers, and their functions, advantages, disadvantages, applications, and factors to consider when selecting them. Discover case studies and examples of successful applications, as well as future developments in secondary crusher technology.
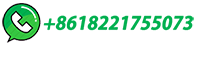
Understanding Jaw Crusher Parts and Their Functions
Introduction: Jaw crushers are powerful machines that are widely used in the mining, quarrying, and recycling industries. These machines are designed to crush large rocks and ores into smaller pieces for further processing. A jaw crusher consists of a fixed jaw and a movable jaw, with the latter being driven by an eccentric shaft that moves the jaw up and down.
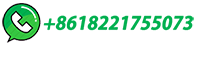
Crusher
Fault diagnosis of mechanical equipment in high energy consumption industries in China: A review. Yongjian Sun, ... Xiaohong Wang, in Mechanical Systems and Signal Processing, 2023. 2.1.1 Crusher. Crusher is a widely used gravel machine, which is mainly used in the crushing of granite, limestone, quartz and other stones. The crusher can crush the stone into fine …
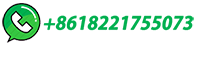
Concrete aggregates properties crushed by jaw and impact secondary crushing
The coarse aggregates obtained by different crushing mechanisms (jaw and impact crushers) show very similar characteristics in terms of binder content assessed by acid leaching (27.5 and 26.6 wt.%), water absorption (8.76 and 9.75 wt.%) and porosity (18.6 and 20.2 vol.%).Thus, it is not possible to conclude that any of these mechanisms are more efficient in …
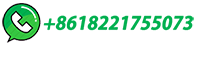
P&Q University Lesson 7: Crushing & Secondary …
Today, primary crushing is viewed as more important within the balance of production and proper sizing needs. The size and type of the primary crusher should be coordinated with the type of stone, drilling and blasting …
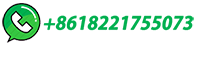
Crushing & Screening Plant
Methods used in Crushing & Screening Plants on ore range from a simple combination of a grizzly and one crusher to an elaborate arrangement in series of grizzly, jaw crusher, screens, and rolls or cone crushers.. Crushing is done underground at a few large mines. In general, the jaw crusher is the most suitable primary machine, yet many gyratories …
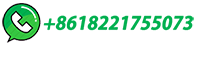
What is a Primary Crusher? | Machinery Partner
Primary jaw crusher and secondary impact crusher working together in a plant set-up. The most common primary crusher is a jaw crusher, but, there are many other types including gyratory and cone crushers. ... Secondary …
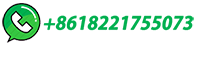
Primary Crushing Station | SpringerLink
The primary crusher is mainly divided into gyratory crusher, jaw crusher, hammer crusher, etc. In addition to its own buildings and equipment, the primary crushing station also needs supporting facilities, such as upper ore bin, lower ore bin, conveyor gallery, oversize component gallery air raise, dedusting chamber, measurement chamber, etc.
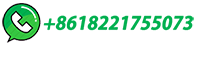
What Is Primary, Secondary, and Tertiary …
The degree to which material is reduced through stages of primary, secondary, and tertiary crushing can depend on the type of material, like aggregate, concrete, and asphalt, and can also depend on the variety of …
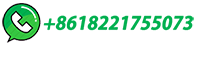
McLanahan | Jaw Crushers
McLanahan's Universal Jaw Crusher produces more spec material at a lower cost per ton and ensures continuous crushing action with less abrasive wear. ... They are used for primary and sometimes secondary size reduction. …
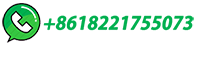
The Ultimate Guide to Jaw Crushing Machines: …
The crushing process in a jaw crusher begins with the feeding of the material into the crushing chamber. The material is crushed between a fixed jaw and a moving jaw, which moves back and forth against the fixed …
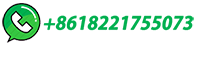
Secondary Crushing 101: Everything You Need to Know
The process of turning raw materials into usable forms involves a carefully structured operation, essential for a wide range of uses. This process unfolds in three key phases: initially, primary crushing takes the lead by breaking down large chunks into smaller, more manageable pieces. Next, the journey continues with the second stage of material …
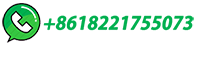
Stone Crushers: A Technical Review on Significant Part of
Stone Crusher is a sort of pulverizer which is utilized to compress or break out assortment of enormous stones. It normally highlights a huge crushing rate and high return and is utilized as an essential equipment in primary, secondary, and tertiary stages of crushing.
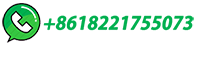
Jaw Crushers
A jaw crusher is a crucial component in mining and ore processing plants, performing the primary crushing of rock and mineral ore to reduce and control the size of materials for …
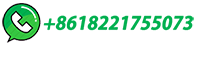
Jaw Crushers – MEKA
Jaw crushers are used as the primary crushers in the first stage of the crushing process. Jaw crushers are preferred for when breaking large rocks is the priority rather than achieving high capacity. Jaw crushers can be used as first-stage crushers in small- and medium-sized plants, as well as for secondary crushing when necessary.
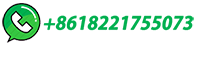
Analisis Kinerja Crushing Plant pada Tambang Andesit
The andesite processing unit consist of several equipment including hopper, primary crushing, secondary crushing, screening and belt conveyor. Each equipment in a processing unit has continuity with each other equipment. Initial stages of the process of andesite is crushing and then the process of separation of size.
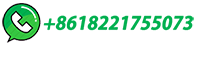
SIZE REDUCTION BY CRUSHING METHODS By
5 5.2 Gyratory crusher : A gyratory crusher is similar in basic concept to a jaw crusher, consisting of a concave surface and a conical head; both surfaces are typically lined with manganese steel ...
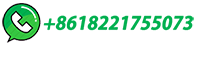
Primary Jaw Crusher – Everything You Need to …
A primary jaw crusher is a machine designed to reduce large rocks into smaller rocks, gravel, or rock dust. It is used in many industries, including mining, construction, and demolition, to crush materials such as …
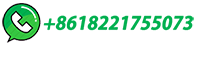
How does an impact crusher work? | RUBBLE MASTER
4 high bars: this mode is for processing small materials (e.g. asphalt millings or gravel) or in a secondary crushing application (e.g. after a jaw crusher) 2 high & 2 low bars: this mode is a multi-purpose setup which is ideal for primary crushing and recycling applications.
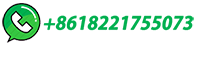
Primary Jaw Crusher – Everything You Need to Know
In the context of a jaw crusher, the term "primary" refers to the first stage of the crushing process. A primary jaw crusher is the first machine in a series of crushers that are used to reduce the size of rocks and minerals. It is designed to handle large pieces of material and break them down into smaller, more manageable pieces.
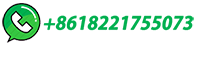
Jaw Crusher Explained
Size Reduction) A crusher is a machine designed to reduce the size of large rocks to smaller rocks, gravel, sand, or rock dust; this is essential for efficient transport of the product via conveyors etc. Crushing is the first of many stages that lead to separation of the mineral(s) from the waste (gangue) material.Waste material can be discarded or recycled allowing the mineral …
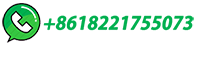
Perfecting the Performance of Secondary Crushers | E & MJ
Cone crushers are fed with pre-screened material from the primary crusher (usually a jaw crusher or primary gyratory), and the secondary crusher should always, if possible, have a scalped feed. Ideally, the deck on the scalping screen should have a cut point equal to the closed side setting (CSS) of the crusher.
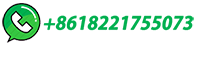
Limestone Crushing Process
Primary Crushing. The extracted limestone is transported to the primary crusher, usually a jaw crusher. This crusher reduces the large chunks of limestone into smaller particles. Secondary Crushing. After primary …
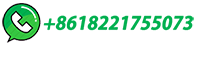