Flotation Cell
The use of power ultrasound in mining. L. Gaete-Garretón, in Power Ultrasonics, 2015 35.5.1 The flotation process. One of the most used processes to concentrate mineral from a mine is flotation. To perform a flotation process the mineral is finely ground (particle sizes between 50 and 150 μm), then the ground mineral is mixed with water in a container called a flotation cell.
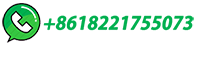
GTEK Laboratory Single Flotation Cell Brochure
lab@mineral-technology +86-159 5822 9409 +86-186 0211 1147 GTEK MINERAL TECHOLOGIES Great Thoughts Embrace Knowledge Description XFD Series Single Flotation Cell can be used for mixing, separation, cleaning, mineral sample concentration in the laboratory room of mineral processing plant, universities and research institutions, and also in ...
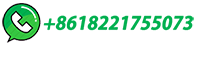
Flotation Processes: A Review
a froth ßotation cell is shown in Figure 1, and a real photo from the Flotation cell. Figure 2. ßotation cells from the processing plant (photo taken by the authors). culties and Challenges in Flotation Processes Flotation is a separation mechanism enga Figure 2. Photo of real flotation cells from the processing plant (photo taken by the ...
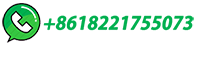
Flotation Cells | Centre for Minerals Research
.text-formatted h1 { margin-top: 1rem; margin-bottom: 1rem; font-size: 26px; } Background Flotation takes place within flotation cells which broadly include mechanical, column, jet, film and novel flotation cells. Research in flotation cells is 'themed' into research into conventional mechanical flotation cells and novel flotation cells.
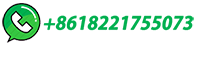
Flotation Cells Design & Operating Characteristics
However, several other concepts for impeller less cells are discussed below. Two other processes contributory to flotation take place in cells: a) all or part of mineral/reagent interactions; and b) particle/bubble contacting. For the first, no special design features are required since the available turbulence levels are usually adequate.
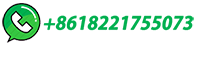
Optimizing Flotation Cells
Optimizing Flotation Cells. H ow a flotation cell works . Flotation Cells (Froth Flotation) were developed to separate and recover high value Sulphide ores from low grade ore bodies. The ore is crushed and milled at the concentrator in a …
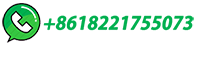
Flotation Techniques: Trends and best practice for …
In the mineral processing field, flotation techniques have witnessed significant trends and best practices that are shaping the industry. One prominent trend is the increasing reliance on digitalization and data analytics. …
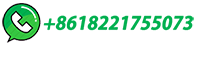
Flotation technologies
grades and the demand for improved flotation selectivity, all bring new challenges to minerals processing flowsheets. The Outotec Concorde Cell technology helps flotation circuits overcome these challenges and achieve improved efficiency in fine and ultra-fine particle recovery. Concorde Cell™ is an ideal flotation solution due to:
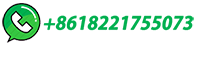
Comprehensive Guide to Flotation Machines: Principles, …
They consist of a series of cells arranged in a row, with each cell containing an impeller-driven rotor that rotates to create turbulence and disperse air bubbles into the slurry. Mechanical flotation machines are further divided into three subcategories: ... Mineral processing: Flotation is a key process in the recovery of minerals such as ...
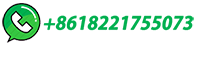
Digital twin of minerals processing operations for an …
The froth flotation process typically involves a series of multiple flotation cells arranged in a sequential manner. This configuration allows for a step-wise separation of valuable minerals from the ore, with each cell playing a specific role in the overall process [].The use of multiple cells in series enhances the efficiency of the flotation process by optimizing the …
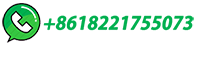
Fine, Coarse and Fine-Coarse Particle Flotation in Mineral Processing
Furthermore, two devices developed at the University of Newcastle, Australia i.e. Concorde cell TM [23, 43] and the Reflux Flotation Cell (RFC) [44] together with StackCell TM typically used for ...
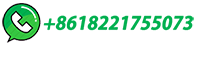
Flotation Processes: A Review
Flotation cell. Minerals2024, 14, 331 froth. Throughout the ß frothers, and activators are utilized to enhanc The e ßotation relies on the interaction of multiple factors, …
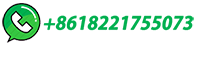
XFD Single Flotation Cell | GTEK
Description. GTEK XFD Series Single Flotation Cell can be used for mixing, separation, cleaning, mineral sample concentration in the laboratory room of mineral processing plant, universities and research institutions, and also in geology, metallurgy, construction, chemistry, and coal industry.
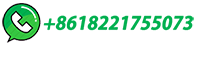
Fluid Flow and Kinetic Modelling in Flotation Related …
In the last decade, flotation equipment related to mineral processing industry has shown a dramatic increase in size, reaching values of 250 m 3 in unitary mechanical flotation cells (Weber et al., 2005) and more than 250 m 3 in pneumatic columns (De Aquino et al., 1998). The general feeling, however, is that despite the great advances observed ...
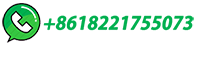
DENVER STYLE FLOTATION CELLS
These banks of larger industrial froth flotation cells are modern reconstructions of the classic DENVER Flotation machine designs.Made to order to any size/volume and cell per bank you need. Specifications. Sizes: 100 cu.ft./cell – 600 cu.ft./cell (open flow) = …
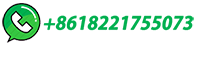
StackCell® Flotation
StackCell ® High-Intensity Flotation Superior metallurgical performance contributing to a more profitable and sustainable mining operation. StackCell flotation reduces conventional flotation residence time requirement by 75 to 85% and increases selective recovery of fine particles and slow floating minerals, which increases profitability and improves environmental sustainability …
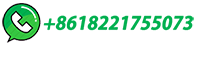
Challenges in processing nickel laterite ores by flotation
It should be added that segregation of laterite ores prior the flotation process has shown some improvement in upgrading nickel. The segregation process relies on the addition of calcium chloride or sodium chloride and carbon allowing the formation of nickel and iron chlorides at temperatures between 900 and 1150 °C. Iwasaki et al., (1961) and Nagano et al., (1970) …
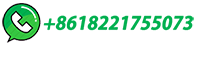
Digital twin of minerals processing operations for an …
The froth flotation process typically involves a series of multiple flotation cells arranged in a sequential manner. This configuration allows for a step-wise separation of …
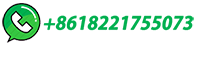
Flotation
Research and application of fluidized flotation units: A review. Jikang Han, ... Yanfeng Li, in Journal of Industrial and Engineering Chemistry, 2023. Introduction. Flotation is a separation process of particles using bubbles which are commonly used in mineral processing, plastic recycling, wastepaper deinking, and wastewater treatment [1–6].Froth flotation techniques …
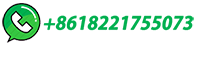
Flotation
How the data is used to determine flotation kinetics is a subject of a separate video. The key aspects are: the types and setup of the laboratory cell; sample to be tested, test conditions and; how the test is conducted. The standard laboratory cell and cell size for many decades has been the Denver D12 with 2.5 litre stainless steel cell.
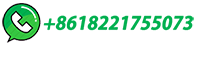
Design, Modeling, Optimization and Control of Flotation …
Design, Modeling, Optimization and Control of Flotation Process. A special issue of Minerals (ISSN 2075-163X). This special issue belongs to the section "Mineral Processing …
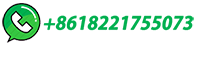
What Are Column Flotation Cells?
Flotation is a science that brings together many complicated variables. Factors include knowledge of mineral structure, chemicals, temperature, technical skills of the operator and dependability of the flotation cell. Read on to learn more about flotation cells, its uses and the different types of flotation cells. What are Flotation Cells?
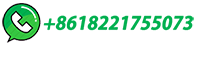
Minerals | Free Full-Text | ImhoflotTM Flotation Cell …
The present work investigates a comparative study between mechanical and ImhoflotTM cells on a mini-pilot scale and the applicability of one self-aspirated H-16 cell …
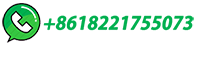
Optimization of Flotation Recovery with Integrated …
Flotation use in mineral processing as a critical separation and selective recovery process was first documented in 1905, and the process and equipment have undergone significant changes since then to improve efficacy [].Today, froth flotation technology is widely used in the recovery of many minerals, including (but not limited to) coal, copper, gold, …
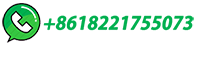
Minerals | Free Full-Text | The Challenges and Prospects of …
Flotation is a common mineral processing method used to upgrade copper sulfide ores; in this method, copper sulfide mineral particles are concentrated in froth, and associated gangue minerals are separated as tailings. However, a significant amount of copper is lost into tailings during the processing; therefore, tailings can be considered secondary …
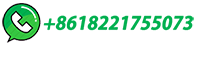
(PDF) A Brief Review of Fine Particle Flotation
Flotation is a common mineral processing method used to upgrade copper sulfide ores; in this method, copper sulfide mineral particles are concentrated in froth, and associated gangue minerals are ...
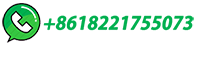
Flotation
Eriez Flotation provides game-changing innovations in process technology for the mining and mineral processing industries such as HydroFloat® for coarse particle recovery and the StackCell® mechanical flotation cell, as well as advanced testing and engineering services, column flotation and sparging equipment.. Applications for Eriez Flotation equipment and …
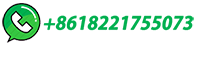
1 Froth Flotation – Fundamental Principles
1 Froth Flotation – Fundamental Principles Froth flotation is a highly versatile method for physically separating particles based on differences in the ability of air bubbles to selectively adhere to specific mineral surfaces in a mineral/water slurry. The particles with attached air bubbles are then carried to the surface and
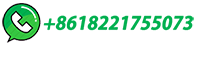
Fluid Flow and Kinetic Modelling in Flotation Related …
In the last decade, flotation equipment related to mineral processing industry has shown a dramatic increase in size, reaching values of 250 m 3 in unitary mechanical flotation …
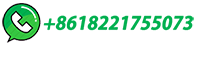
Flotation: The Past, Present and Future of …
E&MJ explores the sustainability of a time-honored beneficiation technique . By Carly Leonida, European Editor. As we look to the future, the mining industry faces a myriad of challenges. While demand for metals like copper, cobalt, …
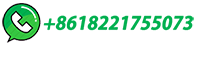