Crushing plant optimisation by means of a genetic …
Crushing plants are used both by aggregate producers and the mining industry. ... low plant performance or unexpected fluctuations due to plant instability (Asbjörnsson, 2013). Moreover, when economic optimization is of interest, simply choosing to maximize one product fraction may lead to the undesirable production of fines (Svedensten and ...
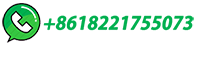
Trade-Off Curves for Performance Optimization in a Crushing Plant …
This potentially leads to a problem of performance optimization based on the desired target product, available feed material and capability of the crusher. The paper presents an application of a multi-objective optimization method to generate multiple operational settings for the dynamic change in the operation condition in a crushing plant.
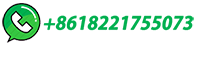
CRUSHING PLANT PROCESS OPTIMISATION
the crushing plant a modelling and simulation system is used, this is briefl y described followed by a description on the combined optimisation routine and expert system. It is the combined …
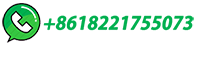
(PDF) Applied Calibration and Validation Method of
Process optimization and improvement strategies applied in a crushing plant are coupled with the measurement of such improvements, and one of the indicators for improvements is the mass flow at ...
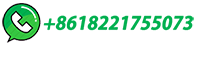
An illustration of a crushing plant circuit in …
Figure 1 shows a modular framework consisting of multiple layers of development needed for the implementation of optimization capability for crushing plants [5]. Developing a reliable and suitable ...
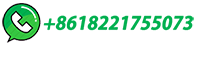
Crushing plant optimization | LUP Student Papers
The goals with the PlantDesigner optimization tool are best reached by separating the purposes by creating a new program that is focused on sales only and maintain the PD optimization tool for plant product optimization.}}, author = {{Lindberg, Mikael}}, language = {{eng}}, note = {{Student Paper}}, title = {{Crushing plant optimization}}, year ...
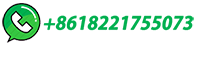
ref #5 PM10 Emission Factors for Two Transfer Points at …
a set of emission tests at a granite crushing plant to determine the PM10 emission factors. The specific sources tested were two conveyor transfer points. The plant selected by the EPA Task Manager was the Wake Stone Corporation, Knightdale, North Carolina Plant. The primary objective of the test was to determine the PM10 emissions ...
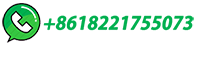
Artificial Intelligence for Monitoring and Optimization of an
Recovery of the mineral and grade of the product in an integrated mineral processing plant are two key performance indicators that define plant profitability. Online monitoring and optimization of these parameters helps improve process performance in real-time. However, achieving high product grade and high mineral recovery simultaneously is …
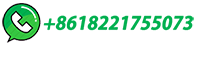
Trade-Off Curves for Performance Optimization in a Crushing Plant
The optimization capabilities for crushing plants comprise a system solution with the two-fold application of 1) Utilizing the simulation platform for identification and exploration of operational ...
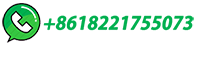
Quality-Driven Production of Aggregates in Crushing Plants
Aggregate quality is of great importance, and in this context it is essential to understand how various process parameters influence the product quality characteristics. Thus, there is a need for aggregate producers to improve their process knowledge. Research has led to an improved understanding of how different process parameters affect the outcomes of specific …
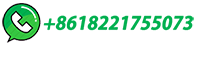
Crushing
Per Svedensten Manager Crushing Chamber and Materials Development Product Development Center Crushing (R&D) Master of Science in Mechanics, specialized in mechatronics Ph.D 2007, Chalmers University Partly funded by Modeling, simulation and optimization of crushing plants Technical-Economic Optimization
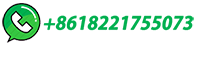
Simulation software for mineral processing plants
NIAflow ® excels across diverse operations, from managing sand washing plants to optimizing coal screening facilities and aiding iron ore agglomeration. As a versatile partner for industries like mining, fertilizer, and recycling, NIAflow ® supports both new ventures and upgrades in various mineral processing phases, from crushing and sorting to pelletizing.
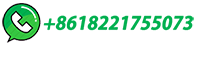
Minerals | Free Full-Text | Applied Calibration and Validation …
This paper presents a methodological routine to calibrate and validate process simulations for industrial aggregate crushing plants (see Figure 1, red box).The application of an optimization method is presented to calibrate and tune equipment models based on the controlled data obtained from experimental design and survey.
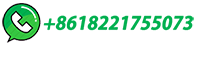
Optimization Capabilities for Crushing Plants | Guide books
The optimization capabilities for crushing plants comprise a system solution with the two-fold application of 1) Utilizing the simulation platform for identification and exploration of operational settings based on the stakeholder's need to generate knowledge about the process operation, 2) Assuring the reliability of the equipment model and ...
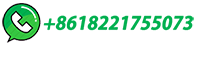
Maintenance and Optimization of Crushing Plants: …
The importance of effective maintenance and optimization practices for crushing plants in the mining and construction industries. Learn how Puzzolana's expertise can help minimize downtime, reduce costs, and improve overall efficiency, ensuring reliable operation and maximizing productivity.
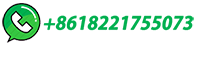
(PDF) Optimization Capabilities for Crushing …
aimed at achieving process optimization and process improvements. The optimization capabilities for. crushing plants comprise a system solution with the two-fold application of 1) Utilizing the ...
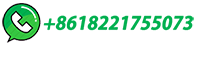
Full Scale Systematic Optimization Steps for a Heap …
Full scale systematic optimization steps for a heap leach crushing plant 445 conditions, blinding of the screens, and overflowing of the silos due to unsteady state of operating conditions, the plant was used to work at: 30-40 Mg/h or 700 Mg/d (under wet-though conditions) and 80-100 Mg/h or 1500 Mg/d (under dry-easy
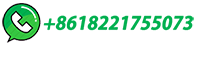
Modeling and Improving the Efficiency of Crushing Equipment
Abuhasel, K.A. Optimization and Simulation of Operation Performance in Crushing Plants Using Fuzzy Modelling. J. Syst. Sci. Syst. Eng. 2019, 28, 766–780. [Google Scholar] Abuhasel, K.A. Machine learning approach to handle data driven model for simulation and forecasting of the cone crusher output in the stone crushing plant. Comput.
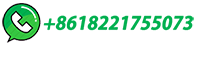
Crushing plant optimisation by means of a genetic …
Crushing plants are used both by aggregate producers and the mining industry. The overall crushed rock product production process can be improved by means of computer simulation and optimisation. ... Parameter optimization of multimachine power system stabilizers using genetic local search. Electrical Power and Energy Systems, 23 (2001), pp ...
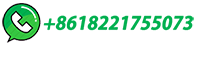
Stone Crusher Plant Design: Best Practices for Efficient Crushing …
Discover the best practices for designing a successful stone crusher plant, including factors to consider, equipment selection and configuration, environmental management, and safety and maintenance priorities. Learn how to optimize crushing operations and minimize environmental impact for efficient and effective production.
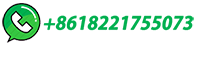
Optimization Capabilities for Crushing Plants
The optimization capabilities for crushing plants comprise a system solution with the two-fold application of 1) Utilizing the simulation platform for identification and exploration of …
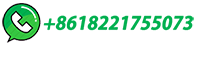
3 Steps for Optimizing Your Processing Plant to Increase…
When making changes to your crushing and screening circuit, keep these two things in mind: ... Plant optimization. Plant optimization is an ongoing process that is part of the circuit; it is not simply a task to be performed. You must have a system in place to achieve the lowest cost per ton. The system is the process of measurement and ...
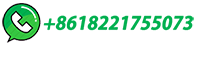
Setvaco Holding – Think Different, Think Solution
We are experts in Crushing and Screening solutions. We supply crusher spare and wear parts and screening media for a wide range of Original Equipment Manufacturers (OEM's). We also supply a wider range of products for mining …
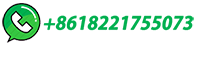
Crushing Technologies
Whether it's the optimization of operating conditions, adaptation to changed operating states, state-of-the-art automation or geographical relocation, we always offer you a complete solution. ... An extensive modernization of the EPC-based mobile crushing plant was exactly what the cement manufacturer Lafarge was looking for – and with the ...
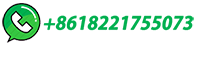
A review of modeling and control strategies for cone crushers …
The approach provides interesting insights into the effects of liner wear and mean time to failure on the capacity, quality and financial profit of the crushing plant. Bhadani et al. (2018) used the crusher model reported in Asbjörnsson et al. (2012) to propose a multidisciplinary optimization platform for crushing plants. An example ...
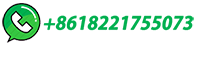
[PDF] The Simulation of Crushing Plants with Models …
A research group now known as the Julius Kruttschnitt Mineral Research Centre at the University of Queensland has been working since 1962 on the simulation, optimization and control of mineral treatment processes. The initial work was on the grinding and classification processes. This work has been very successful in the optimization (Lynch, et al, 1967) and control …
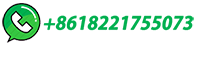
Crushing it: A Comprehensive Guide to Stone Crusher Plants
Introduction: A stone crusher plant is a machine designed to reduce the size of large rocks, eliminate gravel, or rock dust to smaller sizes for various applications. These plants find application in quarrying, mining, construction, and recycling operations. Stone crusher plants consist of several components, including a primary crusher, secondary crusher, and vibrating …
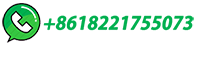
Applied Calibration and Validation Method of Dynamic …
performing process planning and process optimization activities for the crushing plant's operation. Keywords: optimization; comminution; classification; digitalization; dynamic process; data-driven modeling; aggregate production . 1. IntroductionPublished: Crushing and screening processes in aggregate production are intended to produce
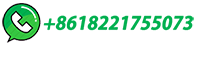
Trade-Off Curves for Performance Optimization in a …
The paper presents an application of a multi-objective optimization method to generate multiple operational settings for the dynamic change in the operation condition in a …
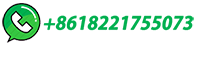
A review of modeling and control strategies for cone …
The approach provides interesting insights into the effects of liner wear and mean time to failure on the capacity, quality and financial profit of the crushing plant. Bhadani et al. …
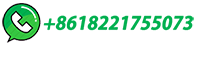