New understanding on the separation of tin from magnetite …
Calcium stannates were non-magnetic materials and Fe 3 O 4 was ferromagnetic, then tin-bearing compounds could be separated from iron oxides during a magnetic separation process. However, Ca 2 Fe 2 O 5 was found in the roasted products when roasting temperature was higher than 900 °C, which was adverse to the separation of iron and tin [28].
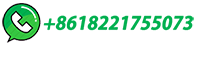
Types of magnetic separators: classification, application
Types of magnetic separators. ERGA produces more than 40 models of magnetic separators, which can be classified using the following parameters: >> Depending on the design >> Depending on the character of the medium for separation >> Depending on the type of magnetic system >> Depending on magnetic field intensity >> Depending on the type of …
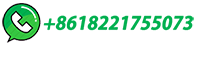
Minerals | Free Full-Text | Dry Permanent …
Dry permanent magnetic separators have been widely used in the mineral and coal processing industries due to their simple operation and high separation efficiency. These tools not only discard some amount of bulk …
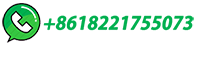
Three-Disc Magnetic Separator
Introduction: The three-disc magnetic separator is suitable for precisely separating various magnetic mineral mixed ores. It is mainly used to separate fine-grained weakly magnetic materials from non-magnetic materials, such as ilmenite, monazite, tungsten and tin, tantalum-niobium ore, and other dry separation operations. The induction distance between the …
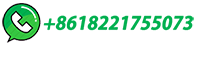
DRY MAGNETIC SEPARATION OF MAGNETITE ORES
The separation of chromite ore with lowest particle size fraction was done using Mozley mineral separator followed by the magnetic separation of the sink product by magnetic separator. The results obtained revealed about 77% of the total material containing 300 μm particle size, 52% ˂ 212 μm and 17% below 75 μm.
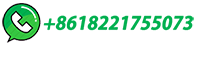
Assessing the performance of a novel pneumatic magnetic separator for
In another study, Ezhov and Shvaljov (2015) used a laboratory-scale EVS-10/5 magnetic separator for dry beneficiation of iron ore of the Backer deposit. This was done by analysing the influence of the current strength in the electromagnet winding of the magnetic separator on concentrate yield and recovery.
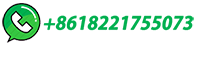
Magnetic Separators
Magnetic Separators Application in Mineral Industry. One of the oldest tools used in mineral concentrating is the magnetic separator. Virtually every mineral handling system has need for some type of magnetic equipment in two types of basic usage. ... Magnetite ore concentration; Removal of grinding iron from ball and rod mill pulps. Recovery ...
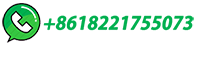
Magnetic Separator
Concentrators, which are used for the separation of magnetic ores from the accompanying mineral matter. These may operate with dry or wet feeds and an example of the latter is the Mastermag wet drum separator, the principle of operation of which is shown in Figure 1.43.An industrial machine is shown in operation in Figure 1.44.A slurry containing the magnetic …
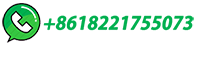
Developments in the physical separation of iron ore: Magnetic …
This chapter introduces the principle of how low-grade iron ores are upgraded to high-quality iron ore concentrates by magnetic separation. Magnetite is the most magnetic of all the naturally ...
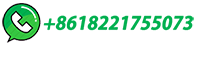
Developments in the physical separation of iron ore: magnetic …
Advancing iron ore slimes magnetic separation with functionalized Nanoparticles: Molecular insights from free energy simulations. 2024, Applied Surface Science. Show abstract. Magnetic nanoparticles have diverse scientific and technological applications, as their properties can be tuned accordingly. An example is the selective magnetic coating ...
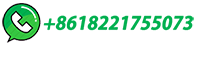
Iron ore magnetite processing
Iron ore magnetite processing (LIMS, MIMS, WHIMS, Davis Tubes) ... Wet LIMS (Low Intensity Magnetic Separation) Eriez L8 Electromagnetic Drum Separators (multiple units): The L8 has an adjustable electromagnet to deliver low intensity gauss field strengths between 500 to 1150G. The L8s can treat small 2-10 kg batches of slurry or be run in ...
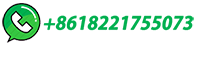
Magnetic Separator Basic Introduction & How To …
Magnetic separator is mainly suitable for the following purposes: The lean iron ore magnetic separator performs rough separation after coarse or medium crushing to remove waste rocks such as surrounding rocks, …
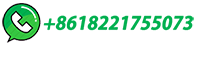
Recovery and separation of iron from iron ore …
Finally, the magnetic component of the roasted ore can be recovered by magnetic separation after being liberated from gangue minerals. Many pilot-scale suspension magnetizing roasting and magnetic ...
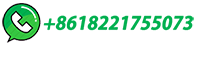
Wet High Intensity Magnetic Separators | Multotec
Wet High Intensity Magnetic Separators (WHIMS) from Multotec apply magnetism, matrix rotation and gravity to achieve para-magnetic materials separation. Applications include heavy minerals, ilmenite, manganese and iron ore (haematite) beneficiation; PGM upgrading as well as manganese recovery from slimes dams.
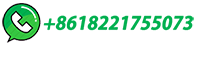
Wet drum magnetic separator for separating fine-grained …
Our STEINERT wet drum magnetic separators are used in the fine grain range from 1 µm up to 3000 µm (0.001 mm – 3 mm) to separate magnetic particles from process liquids, sludges or emulsions. ... The applications range from processing heavy solutions from flotation or sink/float separation, iron ore beneficiation through to the cleaning of ...
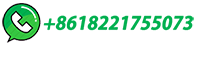
Eriez Magnetic Separation
Eriez is world authority in magnetic separation technologies. Since 1942, Eriez provides a range of permanent and electromagnetic separators for many industries.
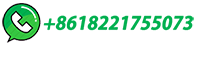
Magnetite
regrind magnetic separators. The concentrate produced will be directed onto the cleaner magnetic separator circuit, mixing once more with the liberated magnetite from the primary cyclone cluster, while the tailings will be discarded as final tails. Cleaner magnetic separator circuit . The cleaner magnetic separator circuit works in the same way as
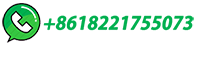
Edison and Ore Refining
The plant had three magnetic separators that could produce a total of 530 tons of refined ore. There was other equipment to re-refine what was left over to extract even more ore. ... The iron ore business was nearly a complete economic failure for Edison, and he lost a great deal of money. To finance the operation he had sold his stock in ...
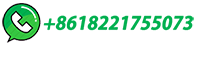
Beneficiation of Low-Grade Hematite Iron Ore …
Present investigation includes the magnetizing roasting of low-grade iron ore fines followed by grinding and beneficiation using magnetic separation. The hematite iron ore used in the investigation contains 53.17% …
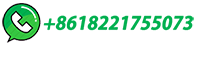
Magnetic separators: Magnetic sorting technology with …
Magnetic & non-ferrous metal separators for sorting scrap / waste & for the mining industry – select from a wide range of magnetic head pulleys, drum, extraction & overhead suspension magnet separators ... Ore sorting; Low-grade stockpile treatment; Industrials minerals; Gemstones: diamond sorting; ... High iron extraction using rotary ...
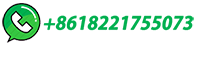
Magnetic Separators For Mineral Processing
A magnetic separator separates the iron impurities in the minerals. It can improve the purity of minerals and is an essential production link. Mineral Magnetic Separation Process. Among them, the most magnetic is …
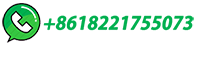
(PDF) Laboratory test and analysis of recovery from separation of iron
The widely used method is using a magnetic separator since the iron ore is a material that is strongly attracted by magnetic force. In contrast, the impurity material is repelled by magnetic ...
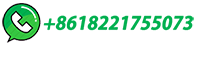
Process and Principle of Magnetic Separation of …
Magnetic separation is a beneficiation method that uses the magnetic difference between minerals in a non-uniform magnetic field to separate different minerals. Magnetic separation is the most commonly used …
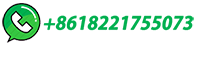
Developments in the physical separation of iron ore: magnetic …
Because the crystal water in limonitic ores will report to the iron ore concentrate in magnetic separation, the iron ore concentrate grade is limited to about 52% Fe. Figure 9.17 shows an example of a flow sheet to upgrade a limonitic ore. The ore is mainly composed of limonite and quartz with a grade of about 40% Fe.
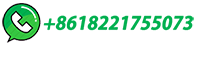
Understanding Magnetic Separation: Explained with Examples
It is used to separate ferrous materials, such as iron and steel, from non-ferrous materials, like aluminium and copper. This separation ensures that valuable metals can be reclaimed and reused. ... Magnetic separators can efficiently remove magnetic minerals from ore, enhancing the purity and quality of the final product. ...
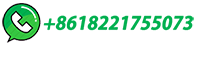
SGM MAGNETICS
The SGM MIMS separator features an innovative proprietary magnetic circuit that results in a unique substantially homogeneous (both axially and radially) high magnetic field and high gradient along its whole magnetic arc which makes it extremely performing on low magnetic susceptibility iron ore both in terms of recovery and purity.
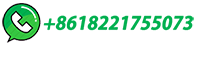
Physical separation of iron ore: magnetic separation
Low-grade iron ore mined from the earth is usually composed of several minerals, desirable and undesirable. Magnetic separation means applying a magnetic field of …
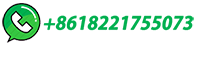
Developments in the physical separation of iron ore: …
Abstract. This chapter introduces the principle of how low-grade iron ores are upgraded to high-quality iron ore concentrates by magnetic separation. Magnetite is the …
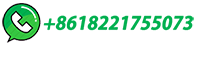
Advancing iron ore slimes magnetic separation with …
Magnetic separation experiments of iron ore ultrafines validated the molecular-level analyses meeting experiment–theory nexus. Abstract. Magnetic nanoparticles have diverse scientific and technological applications, as their properties can be tuned accordingly. An example is the selective magnetic coating technique for the selective ...
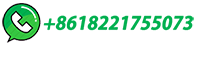
Magnetic Separation
The suspended magnetic separator absorbs iron metal on the conveyor belt's surface, whereas the roller magnetic separator absorbs iron metal near the bottom of the belt. As a result, they are frequently connected in series to improve the efficiency of ferrous metal recovery in practical applications. ... The separation is between economic ore ...
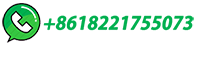